El año pasado SEAT batió su récord de ventas y beneficios en 70 años de historia y la marca española parece haber conquistado su futuro tras años de pérdidas.
Si 2019 terminó en un alto, con una facturación superior a 11 mil millones de euros y ganancias de más de 340 millones de euros (17,5% por encima de 2018), el mejor resultado de la historia, el año 2020 comenzó con menos motivos para las festividades.
No solo salió a competir el consejero delegado de SEAT, Luca De Meo (Renault), sino que -principalmente- la pandemia frenó los años sucesivos de mejora en todo tipo de indicadores económicos, como ocurrió en la gran mayoría de sectores de actividad y empresas de todo el mundo.
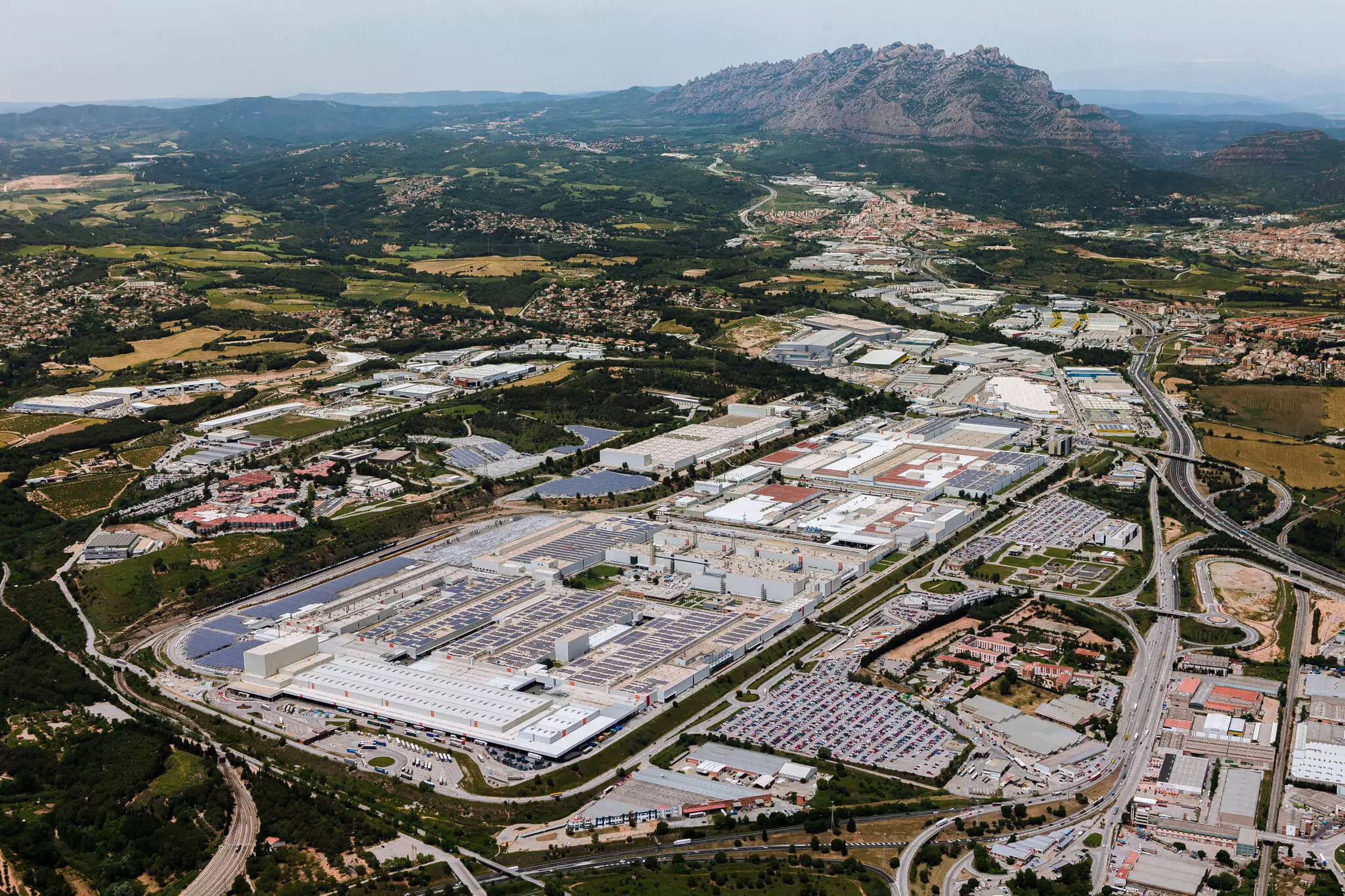
La reciente serie de crecimiento interanual de las ventas de la marca española (de 400.000 en 2015 a 574.000 en 2019, un 43% más en tan solo cuatro años) se detendrá este año.
11 millones de coches fabricados
La fábrica de Martorell se inauguró en 1993, tras haber sido construida en tan solo 34 meses (y haber requerido, en ese momento, una inversión de 244,5 millones de pesetas, equivalente a 1470 millones de euros) y en 27 años produjo alrededor de 11 millones de vehículos, divididos en 40 modelos o derivados.
Desde entonces, mucho ha cambiado, con la superficie de todo el complejo industrial aumentando siete veces hasta los 2.8 millones de metros cuadrados actuales, donde (solo para ayudarlo a visualizar) cabrían 400 campos de fútbol.
Suscríbete a nuestro boletín
Y está lejos de ser el único centro de producción de la marca española en esta zona. En la Zona Franca a pie de la ciudad (donde se inició la fabricación de automóviles de la empresa en 1953 y hasta 1993) se prensan diversas partes (puertas, techos, guardabarros, por un total de más de 55 millones para 20 fábricas). De varias marcas del Grupo Volkswagen únicamente. en 2019); hay otro centro de producción de componentes (del que salieron el año pasado 560.000 cajas de cambio) en las afueras del aeropuerto, en el Prat de Llobregat; además de un Centro Técnico (desde 1975 y donde trabajan hoy más de 1100 ingenieros).
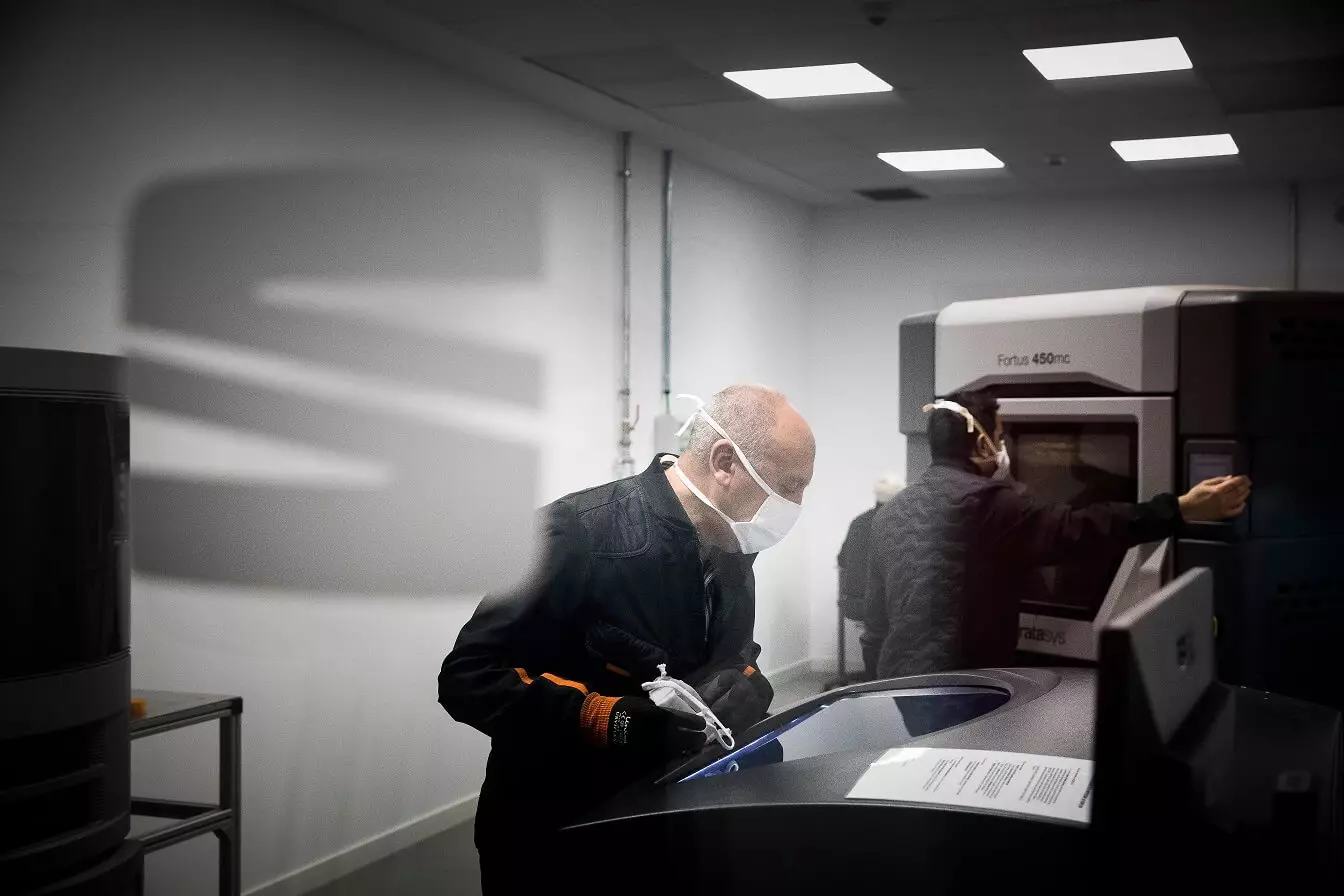
Centro de impresión 3D
Esto hace que SEAT sea una de las pocas empresas del país que diseña, desarrolla técnicamente y fabrica sus productos en España. Y, en la comarca y asociado a SEAT, también hay un enorme centro logístico, un centro de impresión 3D (recientemente nuevo y en la propia fábrica) y un Laboratorio Digital (en Barcelona) donde se piensa el futuro de la movilidad humana (con importantes integración de estudiantes universitarios que también reciben formación constante en la fábrica, bajo protocolo con la Universidad Politécnica de Cataluña).
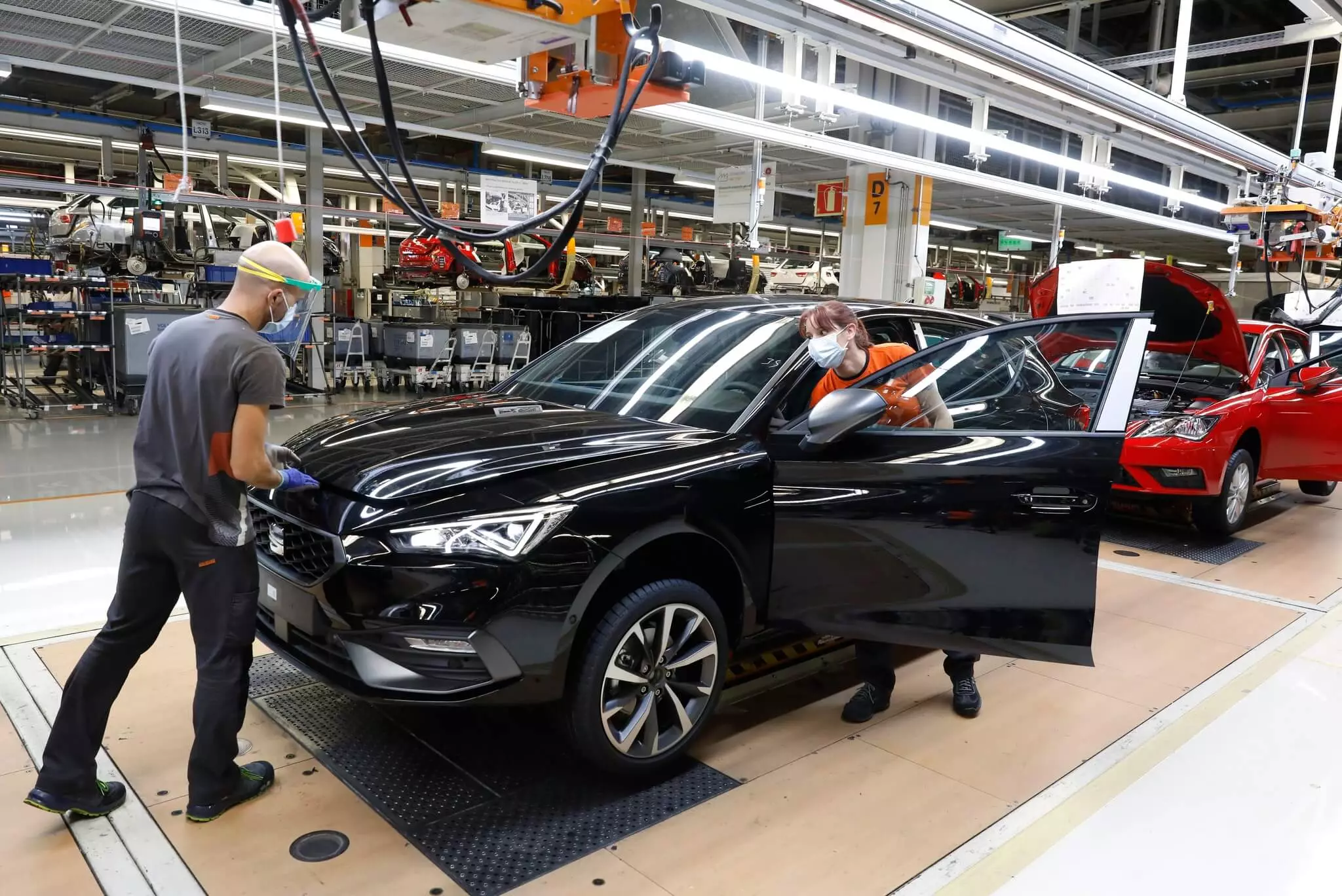
27 años lo cambian todo
En sus inicios, en 1993, Martorell terminaba 1500 coches por día, hoy hay 2300 rodando “por su propio pie”, lo que significa un auto nuevo listo para enviar a algún cliente ansioso cada 30 segundos.
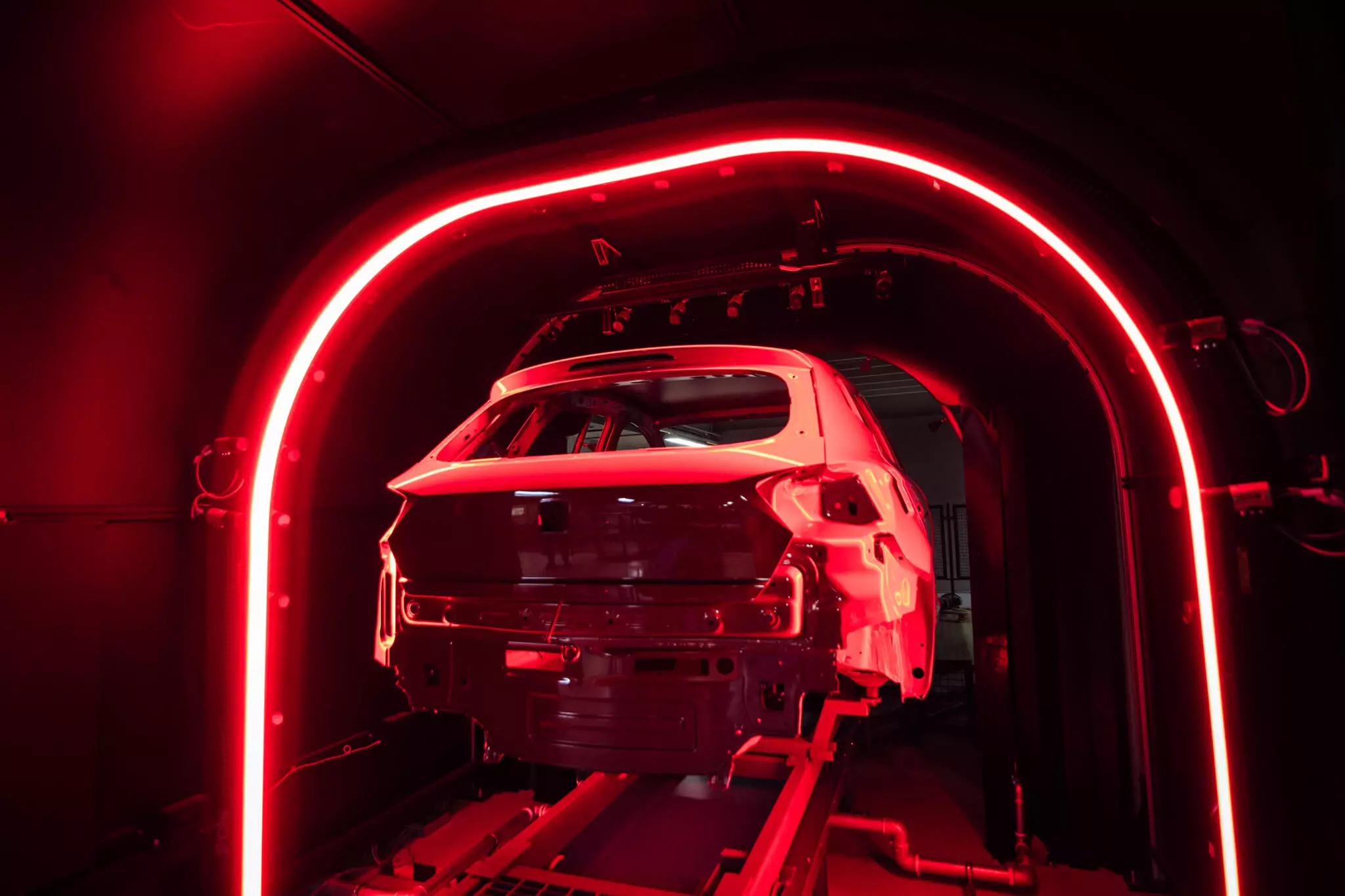
De 60 horas a 22 horas para crear un nuevo automóvil: hoy 84 robots aplican capas delgadas de pintura en una cabina de pintura y un escáner de última generación inspecciona la suavidad de la superficie en solo 43 segundos. La realidad virtual, la impresión 3D y la realidad aumentada son otras de las innovaciones que surgieron con la llegada de la Industria 4.0.
Juan Pérez, Responsable de Procesos de ImpresiónTenía apenas 18 años cuando entré por primera vez en la fábrica de Martorell y recuerdo el ambiente eufórico de la ciudad que acababa de albergar los Juegos Olímpicos. Él era un aprendiz y mis colegas y yo tenía grandes esperanzas para el futuro: todo era nuevo y nos dijeron que era la fábrica más moderna de Europa.
Así recuerda Juan Pérez, que actualmente dirige los Procesos de Impresión, aquellos primeros días, hace 27 años, en la fábrica de Martorell, donde los empleados caminaban 10 km al día: “Cuando volvía a casa, no encontraba ni la taquilla. habitación. Era muy fácil perderse ”.
Hoy en día existen vehículos autónomos, que ayudan a los empleados a transportar alrededor de 25.000 piezas diarias a la línea, además de 10,5 km de vías férreas y 51 líneas de autobuses.
Un portugués lidera la calidad
Igual o más importante es el constante avance cualitativo incluso en los últimos tiempos, como muestran los últimos indicadores: entre 2014 y 2018 el número de quejas de los propietarios de modelos de la marca española descendió un 48% y Martorell se sitúa prácticamente en el nivel de récords de calidad / fiabilidad de la planta matriz de Volkswagen en Wolfsburg.
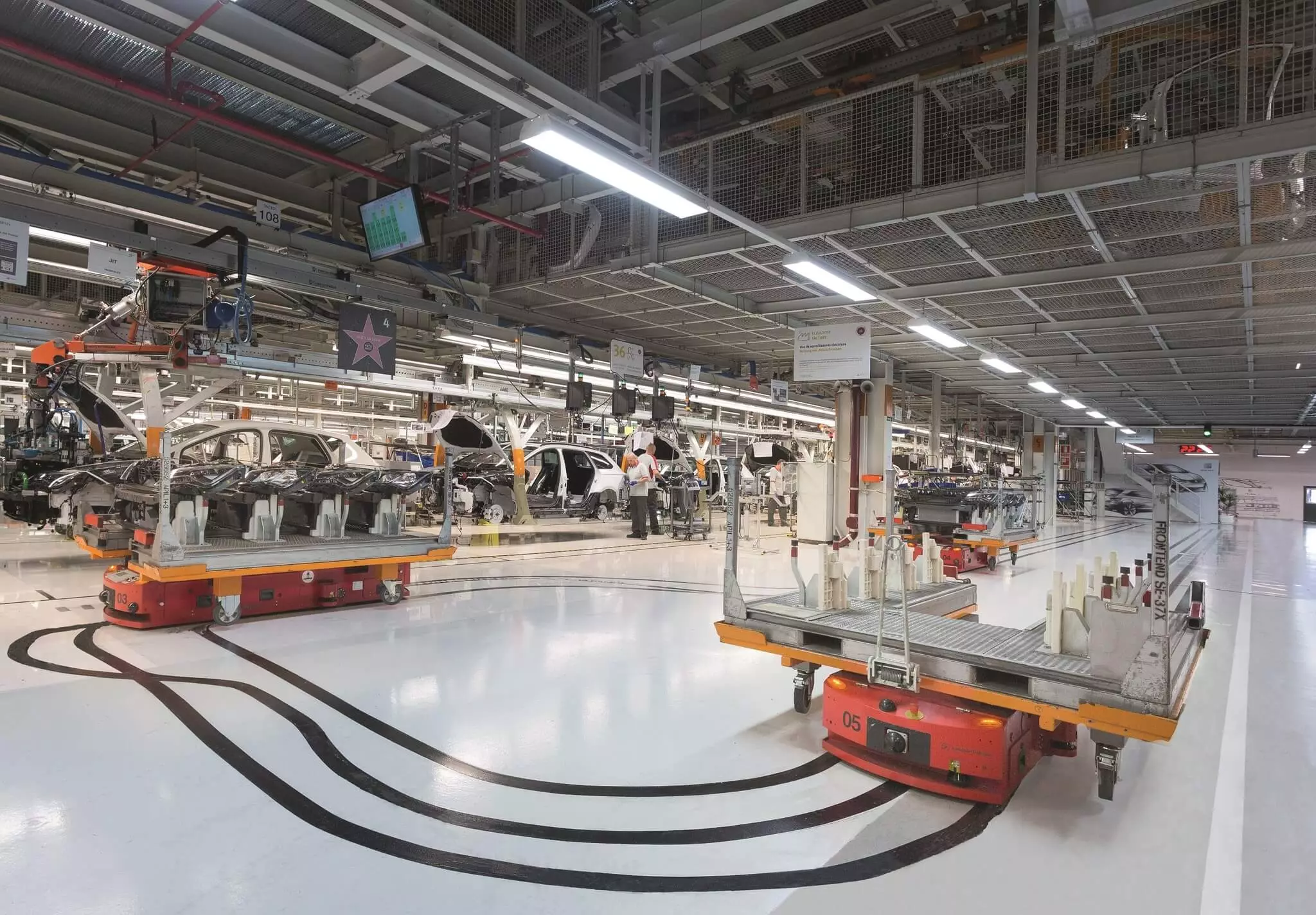
Esto no debe sorprender si se tiene en cuenta que se siguen los mismos procesos industriales de la A a la Z, como confirma José Machado, el portugués que ahora lidera el control de calidad en Martorell, después de comenzar en Autoeuropa (en Palmela), desde donde pasó a Puebla ( México), para asumir este importante puesto en la cuna de casi todos los SEAT:
José Machado, Director de Control de CalidadTodos seguimos la misma guía y eso es lo que cuenta, porque al final nuestros 11.000 empleados, directos e indirectos, incluyen 67 nacionalidades y 26 idiomas diferentes.
El 80% son hombres, el 80% son menores de 50 años, llevan en la empresa una media de 16,2 años y el 98% tienen un contrato de trabajo indefinido, lo que ayuda a generar estabilidad en las personas, que luego se refleja en la calidad de su trabajo. trabajar, trabajar.
León es el que más fabrica y vende
Tan orgulloso o incluso más orgulloso de lo que se está haciendo aquí, Ramón Casas -director de la sección de Montaje y Revestimientos Interiores- es el guía principal de esta visita, que se centra en esta área de la que es el principal responsable: “tenemos tres montajes líneas en total, 1 es de Ibiza / Arona (que completa 750 coches / día), 2 de León y Formentor (900) y 3 de un exclusivo Audi A1 (500) ”.
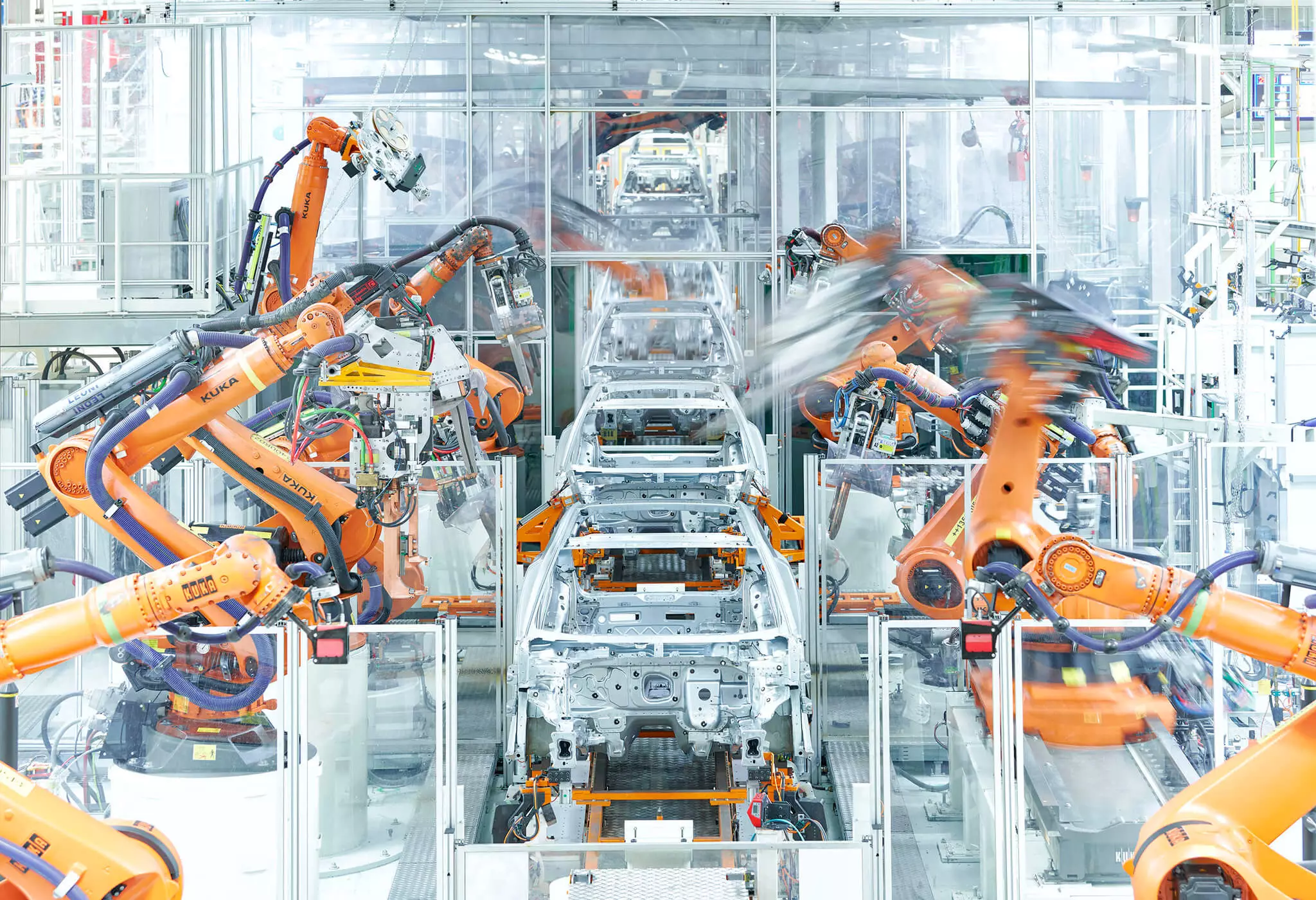
En este caso, estamos en la cuna de León y derivados porque esta visita se realizó además de un viaje a la fábrica para recoger la furgoneta León Sportstourer antes de que llegara, a través de los canales habituales, al mercado portugués.
Casas explica que “esta línea 2 es la que más coches fabrica porque el León es el SEAT más vendido a nivel mundial (unas 150.000 / año) un poco más que los Ibiza y Arona (unas 130.000 cada uno) y ahora que el SUV Formentor se ha incorporado a esta línea de montaje la capacidad de producción estará muy cerca de agotarse ”.
Los 500005 coches fabricados en Martorell en 2019 (81000 de los cuales Audi A1), un 5,4% más que en 2018, utilizaron el 90% de la capacidad instalada de la fábrica, una de las tasas más altas de toda Europa y un indicador muy positivo de la salud financiera de la empresa.
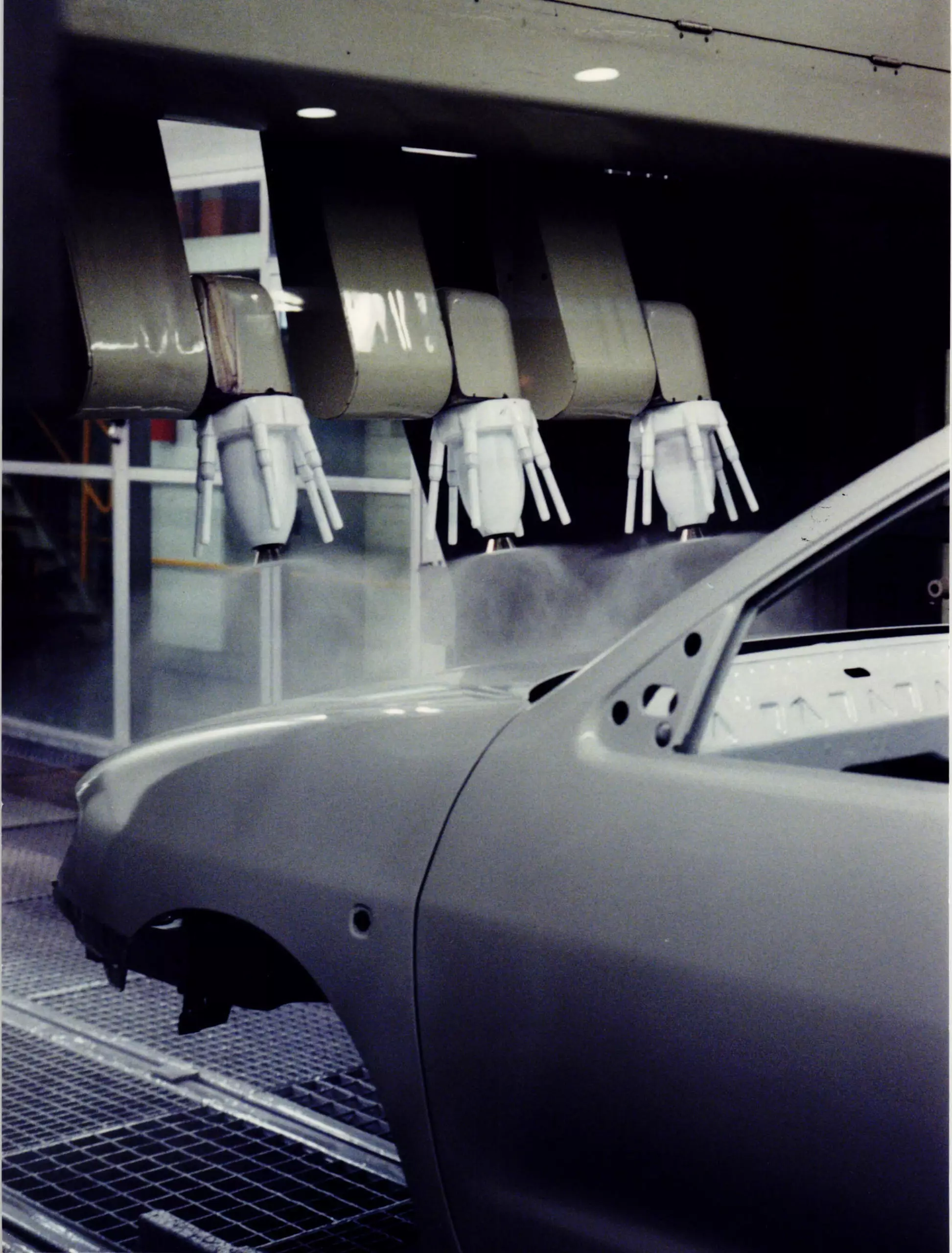
La marca española, sin embargo, tuvo unas ventas superiores a los 420.000 SEAT producidos en Martorell el año pasado, ya que algunos de sus modelos se fabrican fuera de España: el Ateca en la República Checa (Kvasiny), el Tarraco en Alemania (Wolfsburg), el Mii en Eslovaquia (Bratislava) y la Alhambra en Portugal (Palmela).
En total, SEAT produjo 592.000 coches en 2019, siendo Alemania, España y Reino Unido los principales mercados, en ese orden (el 80% de la producción está destinada a exportarse a unos 80 países diferentes).
22 horas para hacer un SEAT León
Continúo mi recorrido por parte de los 17 km de pistas con raíles electrificados, luego carrocerías suspendidas y bases rodantes con motores / cajas ya montados (que luego se encuentran en lo que las fábricas llaman “Wedding”), mientras los dos guías brindan más Detalles: hay tres áreas principales en cada una de las líneas de montaje, Carrocería, Pintura y Montaje, "pero la última es donde más tiempo pasan los autos", se apresuró a agregar Ramón Casas, o si no fuera así también el uno bajo su responsabilidad directa.
En un total de 22 horas que tarda cada León en producirse, quedan 11:45min en Montaje, 6:10min en Carrocería, 2:45min en Pintura y 1:20min en Acabado y Comprobación Final.

Los directores de fábrica están muy orgullosos de poder cambiar la generación del modelo sin tener que interrumpir la cadena de montaje. “Incluso con carriles más anchos y una distancia entre ejes diferente, pudimos integrar la producción del nuevo León sin tener que detener la producción de la generación anterior”, destaca Casas, para quien existen otros desafíos más delicados:
Ramón Casas, Director de la Sección de Montaje y Revestimiento Interiorel León anterior tenía 40 unidades de procesamiento electrónico, el nuevo tiene al menos el doble y si consideramos el híbrido enchufable estamos hablando de ¡140! Y todos deben probarse antes de ser instalados.
También es complicada la secuenciación de las piezas para que la configuración del coche siga exactamente lo que se ordenó. Solo en el caso del frontal del León puede haber 500 variaciones, lo que da una idea de la dificultad de la tarea.
José Machado también explica que “no hay diferencia horaria entre la producción de una furgoneta León de cinco puertas o una Sportstourer y el hecho de que esta última haya ganado popularidad en los últimos años -40% de las ventas frente al 60% de la de cinco puertas- no ha afectado a la línea de montaje ”.

Drones y robots para ayudar ...
En Martorell hay más de un tipo de robot. Hay quienes realizan entregas entre diferentes áreas del gigantesco complejo industrial (como drones y vehículos terrestres automatizados, que suman 170 dentro y fuera de la fábrica) y luego robots que ayudan a ensamblar los autos ellos mismos.
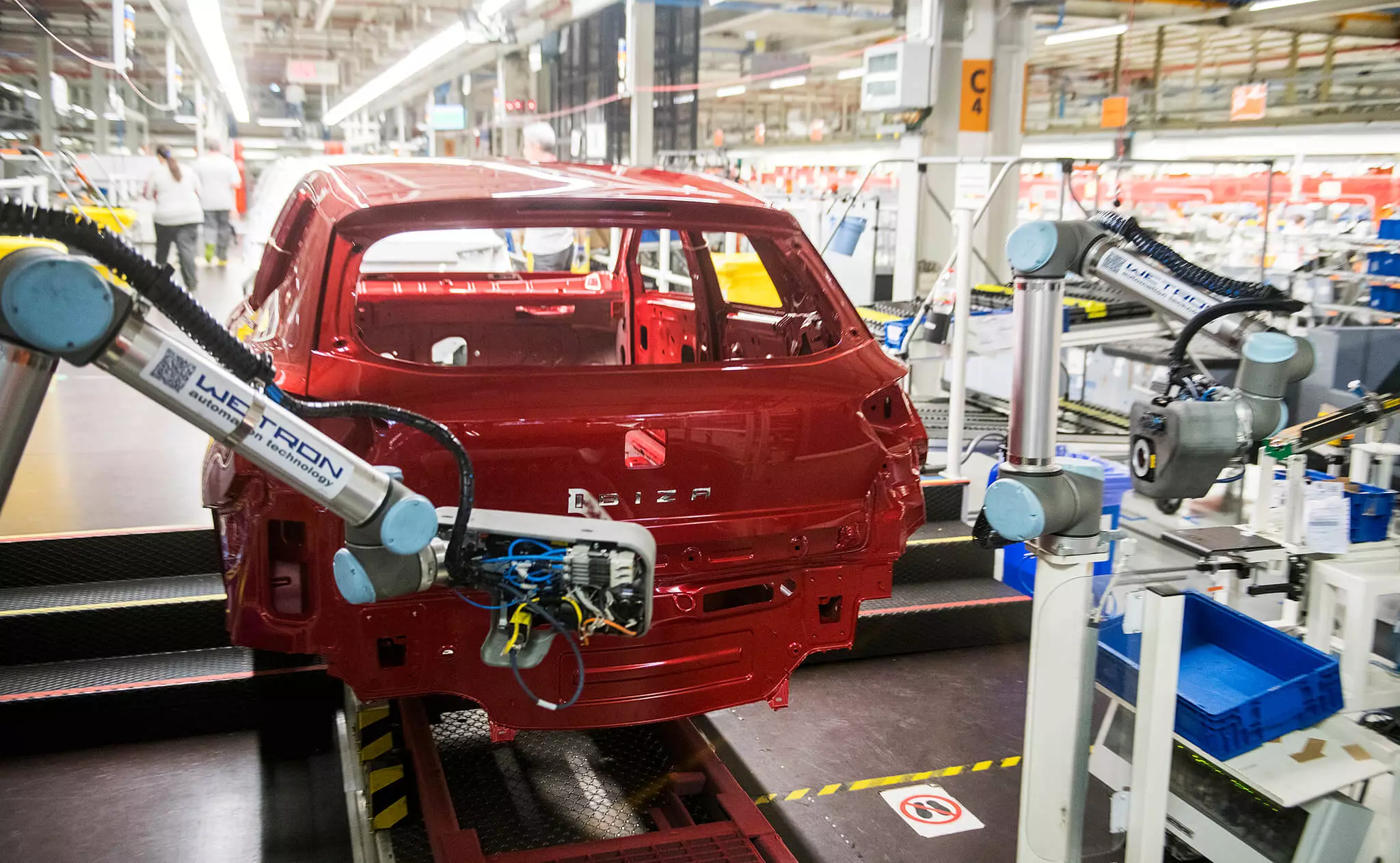
Machado dice que "existen diferentes tasas de robotización según el área de la línea de montaje, con alrededor del 15% en el área de montaje, el 92% en el enchapado y el 95% en la pintura". En la zona de montaje, muchos de los robots ayudan a los empleados a coger piezas más pesadas, como las puertas (pueden llegar a alcanzar los 35 kg) y rotarlas antes de encajarlas en la carrocería.
... pero es el ser humano el que marca la diferencia
El responsable de Calidad de Martorell también destaca la importancia del equipo humano en esta unidad industrial:
José Machado, Director de Control de Calidad.Ellos son los que dan la señal en caso de que haya algún problema en la cadena de montaje, llamando al supervisor que está tratando de solucionar el problema con la línea en curso, haciendo todo lo posible para que no se detenga. Cambian de roles cada dos horas para evitar una rutina excesiva y también para motivarlos más, incluso dando ideas para hacer más productivo todo el proceso. Y si se aplica alguna de las sugerencias, terminan recibiendo un porcentaje de lo que la fábrica ahorró con ese cambio.
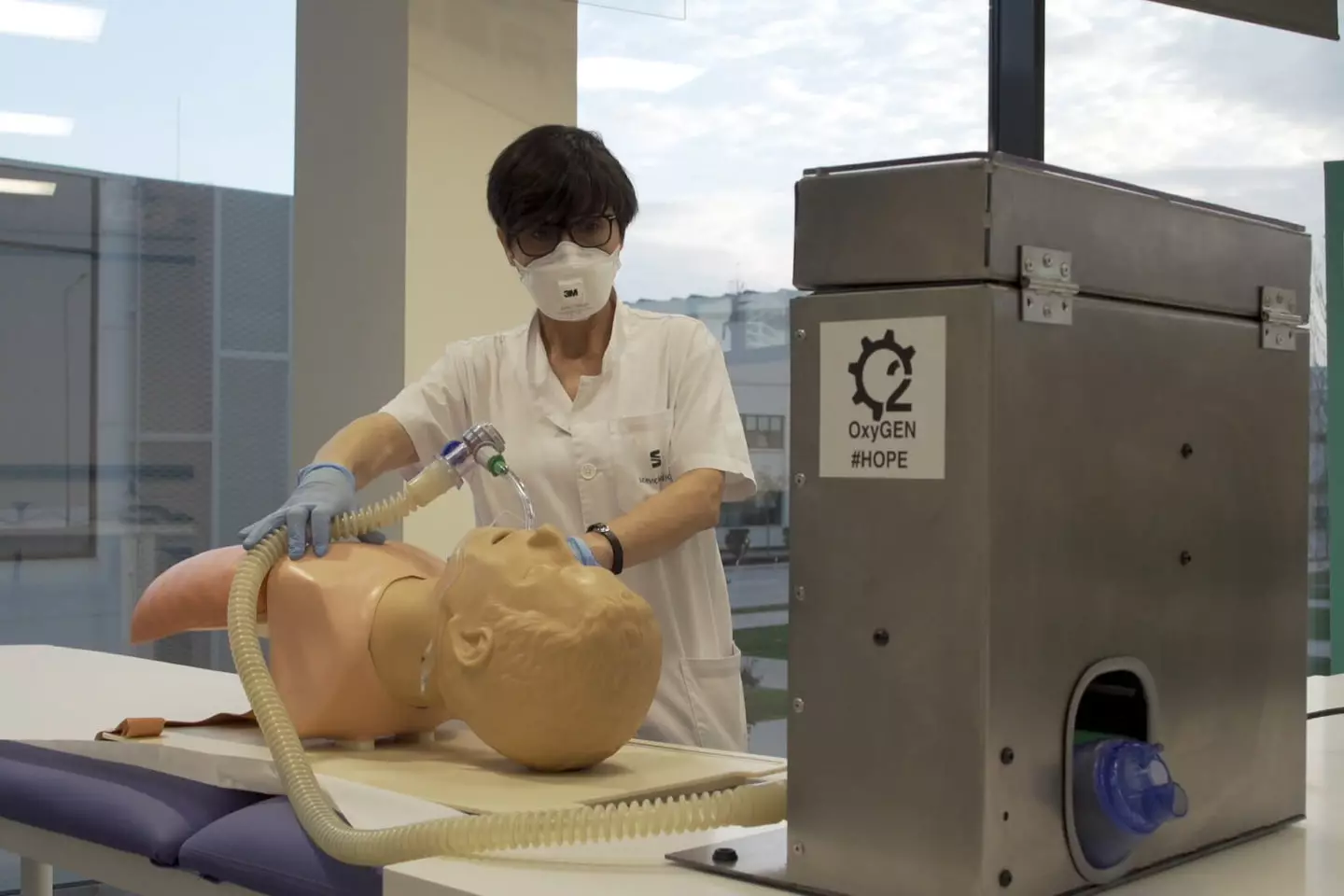
SEAT rápidamente comenzó a producir fanáticos en la lucha contra Covid-19.
Martorell se cerró durante la fase más grave de la propagación del covid-19, como me explica Ramón Casas:
Ramón Casas, Director de la Sección de Montaje y Revestimiento InteriorTodos nos fuimos a casa a fines de febrero, el 3 de abril comenzamos la producción de fans y volvimos a trabajar el 27 de abril, haciendo pruebas de virus gradualmente a todos los empleados. Es obligatorio el uso de mascarilla durante todo el período de estadía en la fábrica, hay gel por todas partes y muchas protecciones acrílicas en los espacios de descanso, cafetería, etc.