Vi har redan nämnt vinstpotentialen hos Tesla modell 3 . Det var en av slutsatserna av den uttömmande analysen av modellen - demonterad till "sista skruven" - som utfördes av ingenjörskonsultföretaget Munro & Associates.
Dess VD, Sandy Munro, var imponerad av modellens teknologi, förknippad med batterier och elektronik, som han anser är den mest avancerade i branschen idag.
Munro framförde dock flera kritik som, enligt honom, hindrar Model 3 från att nå sin potential, nämligen den dåliga designen (inte en kritik av estetiken, utan mot designen); och produktion, som trots växande antal kräver mycket mer resurser än andra produktionslinjer.
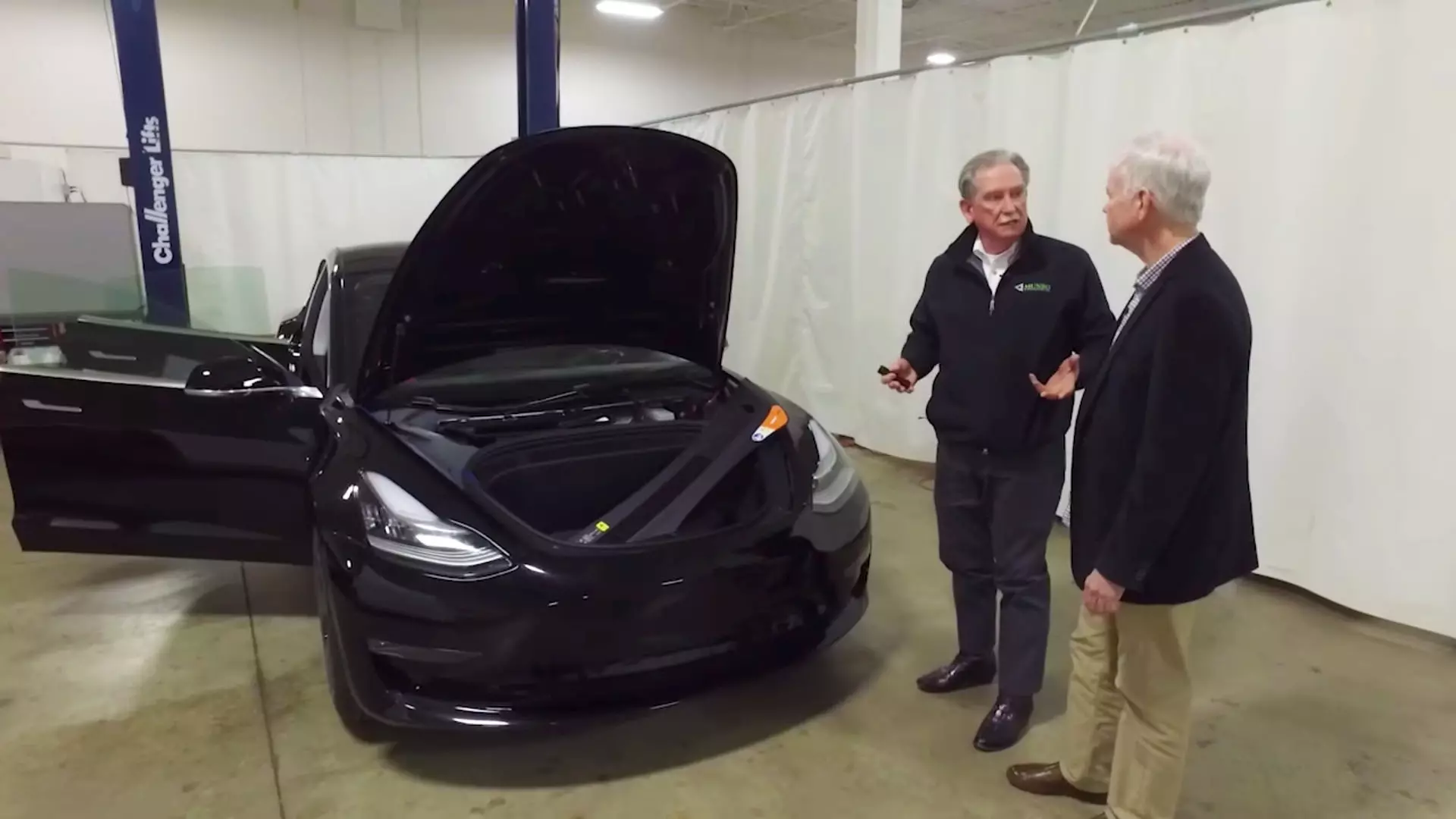
Munro drog slutsatsen att betongenheten i den demonterade Tesla Model 3 kostar 2000 dollar mer (1750 euro) att bygga än en BMW i3 (en annan av modellerna som redan har passerat genom hans såll), detta utan att räkna de extra kostnader som kommer från monteringen linje .
Prenumerera på vårt nyhetsbrev här
Roten till problemen? Elon Musks oerfarenhet
Elon Musk, Teslas VD, har utan tvekan visionen, men det gör honom inte till en expert på att tillverka bilar. Problemen som rapporterats av Sandy Munro avslöjar Musks oerfarenhet inom bilindustrin:
Om den här bilen tillverkades någon annanstans, och Elon (Musk) inte var en del av produktionsprocessen, skulle de (Tesla) tjäna mycket pengar. De lär sig alla gamla misstag som alla andra gjorde för år sedan.
Men Munro är en själverkänd beundrare av den teknik som den amerikanska tillverkaren har utarbetat och använt - som visar sina "Sillicon Valley"-rötter - så, med hänsyn till analysen som utförts av hans företag, utarbetade han en lista med 227 förbättringsåtgärder för att "räta ut" Model 3 en gång för alla.
Lista som han skickade till Tesla själv... kostnadsfritt.
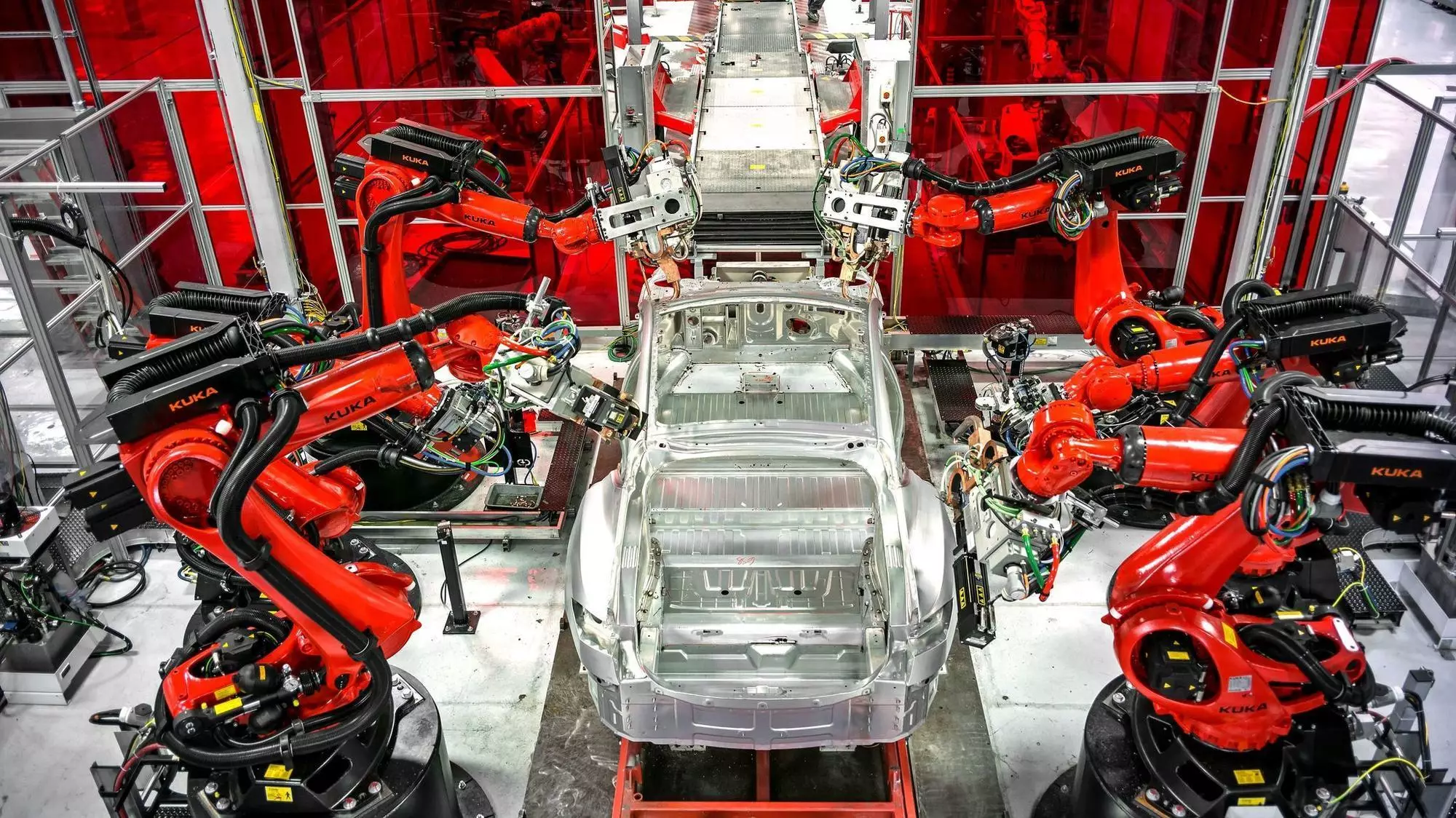
Vad kan förbättras
De flesta av lösningarna relaterar till Model 3:s karossdesign, det vill säga unibody-struktur och karosspaneler, vilket Munro anser vara huvudproblemet, vilket ger onödig vikt, kostnad och komplexitet.
Han lyfter fram några exempel - tyvärr har vi inte tillgång till alla 227 åtgärder - och mer effektiva lösningar för att lösa samma problem som finns i konkurrensen:
- Stål- och aluminiumram vid basen av bilen - designad för att öka säkerheten, Munro säger att det inte är nödvändigt, eftersom batteripaketet, som ligger på plattformens golv, ger all nödvändig styvhet. Resultat: ökad vikt och kostnader utan att medföra stora fördelar.
- Baklucka i aluminium — bestående av nio delar sammanfogade av svetspunkter och nitar. Munro föreslår att du byter ut den mot en enda bit i glasfiber som sett hos andra byggare.
- Bakre hjulhus — även uppbyggt av nio metallbitar nitade, svetsade och sammanlimmade. På Chevrolet Bolt är det bara en stämplad bit i till exempel stål.
Tesla har själv nämnt vid tidigare tillfällen att de fortsätter att göra ständiga förbättringar av produktionslinjen och bilen. Vi hade redan nämnt t.ex. undertryckandet av 300 svetspunkter som har visat sig onödiga och ständiga optimeringar i produktionslinjen har rapporterats.
Även om Model 3 som Munro demonterade fortfarande är en av de första som produceras, utan att integrera många av de förbättringar som har skett under tiden, gick han så långt som att säga att Tesla borde sparka ingenjörschefen som designade strukturen /body av Model 3, förstärkande med "de borde inte ha anställt honom", eftersom det är här som de flesta "huvudvärk" finns på produktionslinjen.
Även om inga namn faktiskt nämndes, sparkade Tesla Doug Field, chef för fordonsteknik i juni förra året. Det är nu känt att Tesla Model 3 var den första bilen som utvecklades av honom.
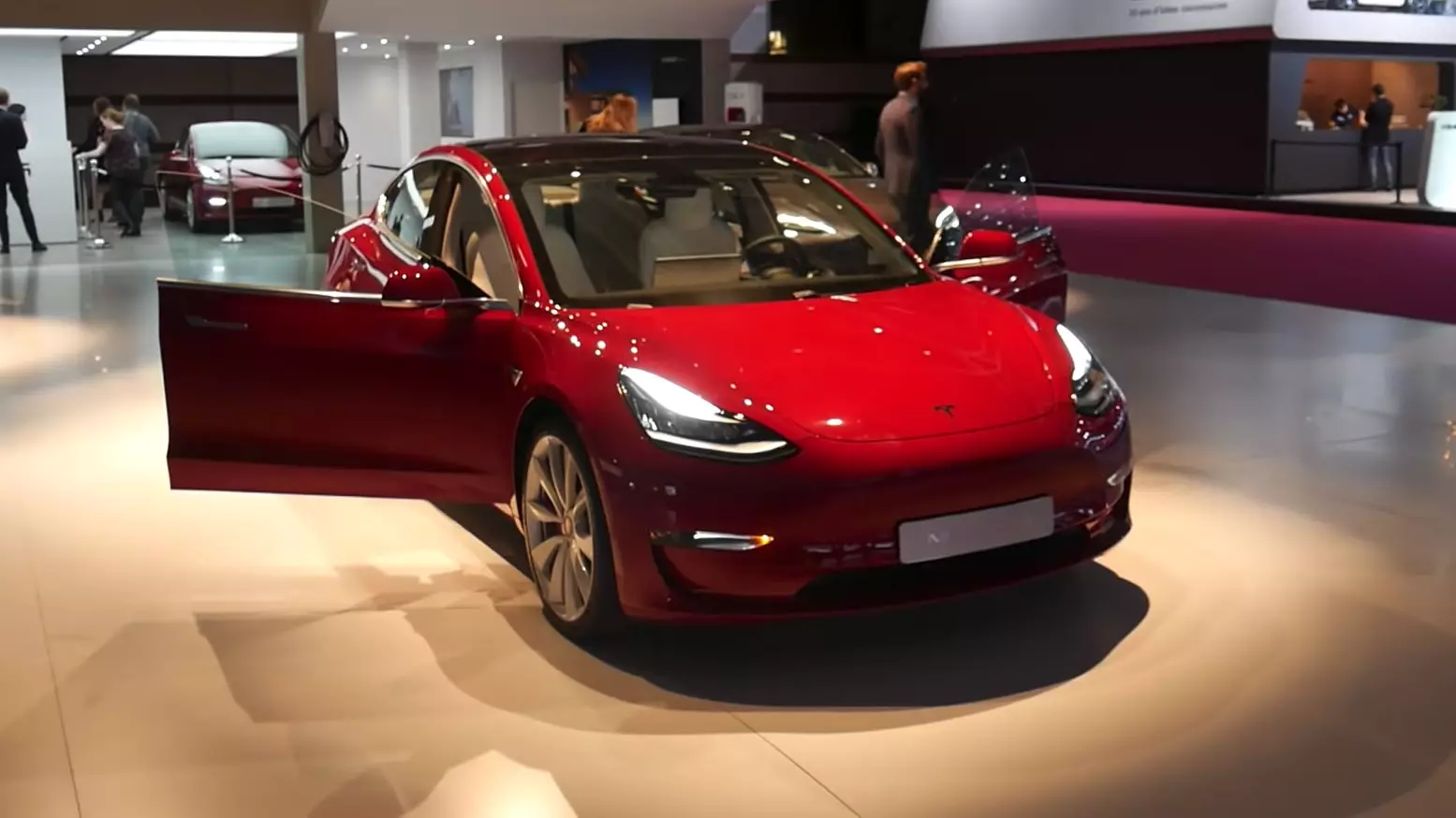
"Den överdrivna automatiseringen hos Tesla var ett misstag"
Det andra stora problemet, enligt Munro, är överskottet av anställda på produktionslinjen. Om satsningen på automatisering till en början försvarades av Elon Musk, visade sig detta vara fel – till stor del på grund av bilens designproblem, såsom överskottet av lödpunkter, som nämndes av Munro – ett fel som Musk själv medgav för några år sedan månader.Först nu har vi gått från "8 till 80", med Fremont-fabriken, där alla Tesla tillverkas - en tidigare enhet som tillhör Toyota och GM - sysselsätter cirka 10 tusen anställda , som i år kommer att producera ungefär 350 000 Tesla (S, X och 3).
Jämför siffrorna på den tiden då Toyota och GM tillverkade bilar där. på sin topp 4400 anställda producerade 450 000 fordon per år.
Berättigandet för ett så stort antal anställda kan delvis förklaras av den ”interna” produktionen av delar som vanligtvis produceras externt av leverantörer som banker; motivering som avfärdats av Munro: "Även med tre skift och mycket arbete hemma, finns det ingen motivering för att behöva 10 000 personer."
Prenumerera på vår Youtube-kanal.
Kostnader och vinstpotential
Den demonterade Tesla Model 3 var prissatt till 50 000 $, med produktionskostnaden beräknad av Munro till 34 700 $ (30 430 euro) — ingenjörs-, forsknings- och utvecklingskostnader ingår inte i denna beräkning. Även om man lägger till logistikkostnader och en generös kalkyl för arbetskraft, förväntas bruttovinstmarginalen överstiga 30 %, en anmärkningsvärd siffra i bilindustrin.
Han uppskattar att även i en nybörjarversion kan Model 3 uppnå en marginal på 10 %, med en produktionskostnad på mindre än 30 000 $ (26 300 €) - tack vare ett mindre (och billigare) batteri och mindre installerad utrustning. Något bättre siffror än drygt 30 000 dollar för en Chevrolet Bolt och ungefär 33 000 dollar för en BMW i3 (båda också tidigare granskade av Munro & Associates).
Enligt Sandy Munro, nu handlar det om att Tesla ska göra sin tekniska fördel lönsam. . För detta måste varumärket inte bara hålla en viss produktionsnivå, det rekommenderar också att Elon Musk anställer chefer med erfarenhet av uppdraget att bygga och montera bilar. Om han lyckas säger Munro att Elon "inte är långt ifrån att tjäna pengar".
Källa: Bloomberg