Audi ตัดสินใจก้าวไปอีกขั้นในแง่ของนวัตกรรมยานยนต์ ด้วยแนวคิดที่ไม่มีอะไรใหม่ในอุตสาหกรรมยานยนต์แต่ให้ประโยชน์มหาศาล ค้นพบสปริงไฟเบอร์กลาสรุ่นใหม่ของ Audi
ควบคู่ไปกับการลงทุนในการพัฒนาเครื่องยนต์และวัสดุคอมโพสิตที่มีประสิทธิภาพมากขึ้นซึ่งช่วยให้ลดน้ำหนักได้ ในขณะที่เพิ่มความแข็งแกร่งของโครงสร้างของแชสซีและตัวถัง Audi ได้เปลี่ยนมาใช้วัสดุคอมโพสิตอีกครั้งเพื่อนำไปใช้กับส่วนประกอบอื่นๆ
ดูเพิ่มเติม: โตโยต้านำเสนอแนวคิดนวัตกรรมสำหรับรถยนต์ไฮบริด
Audi มุ่งมั่นที่จะพัฒนาและขยายเทคโนโลยีนี้ให้มากขึ้น ทั้งหมดนี้มีจุดประสงค์เดียว: เพื่อลดน้ำหนัก ซึ่งจะเป็นการปรับปรุงความคล่องตัวและการจัดการของรุ่นในอนาคต
นี่คือแฟชั่นใหม่ของแผนกวิจัยและพัฒนาของ Audi: the ไฟเบอร์กลาสแบบเกลียวและสปริงอัดเสริมโพลีเมอร์ . แนวคิดที่เชฟโรเลตได้นำไปใช้แล้วในคอร์เวทท์ ซี4 ในปี 1984
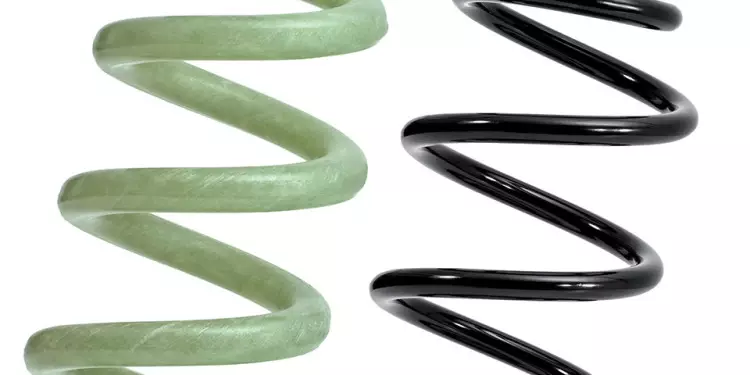
ความกังวลที่เพิ่มขึ้นเกี่ยวกับน้ำหนักของระบบกันสะเทือน และด้วยอิทธิพลของน้ำหนักที่มากเกินไปขององค์ประกอบระบบกันสะเทือนที่มีต่อประสิทธิภาพและการบริโภค ทำให้ Audi ให้ความสำคัญกับการพัฒนารูปแบบระบบกันสะเทือนที่เบากว่า สิ่งเหล่านี้ควรนำมาซึ่งน้ำหนักที่เพิ่มขึ้นอย่างชัดเจน การบริโภคที่ดีขึ้น และการตอบสนองแบบไดนามิกที่ดีขึ้นจากรุ่นต่างๆ
ห้ามพลาด: Wankel Engine การหมุนในสถานะบริสุทธิ์
ความพยายามด้านวิศวกรรมของ Audi ที่มี Joachim Schmitt เป็นหัวหน้าโครงการ ได้พบหุ้นส่วนในอุดมคติในบริษัท SOGEFI ของอิตาลี ซึ่งถือสิทธิบัตรร่วมสำหรับเทคโนโลยีนี้กับแบรนด์ Ingolstadt
สปริงเหล็กทั่วไปต่างกันอย่างไร?
Joachim Schmitt นำเสนอความแตกต่างในมุมมอง: ใน Audi A4 ซึ่งสปริงระงับบนเพลาหน้ามีน้ำหนักมากถึง 2.66 กก. แต่ละตัว สปริงโพลีเมอร์เสริมแรงด้วยไฟเบอร์กลาส (GFRP) ใหม่มีน้ำหนักเพียง 1.53 กก. ต่อชุดสำหรับชุดเดียวกัน ความแตกต่างของน้ำหนักมากกว่า 40% ด้วยประสิทธิภาพในระดับเดียวกันและประโยชน์เพิ่มเติมที่เราจะอธิบายให้คุณทราบในทันที
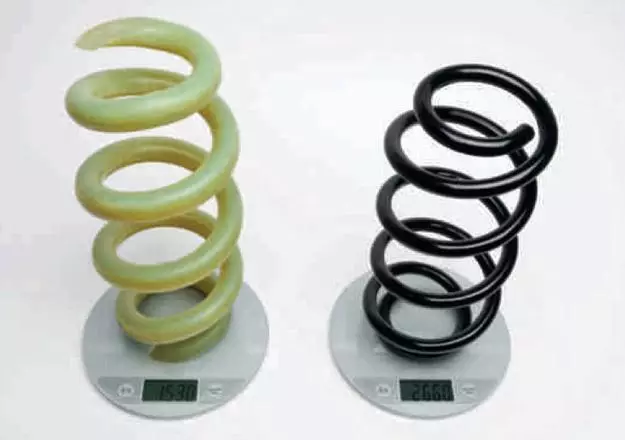
สปริง GFRP ใหม่เหล่านี้ผลิตขึ้นอย่างไร?
ย้อนกลับไปเล็กน้อยกับสปริงอัดของคอยล์ พวกมันถูกออกแบบมาเพื่อสะสมแรงในระหว่างการอัดและออกแรงไปในทิศทางของการขยายตัว มักผลิตจากลวดเหล็กที่มีรูปทรงกระบอก เมื่อจำเป็นต้องใช้แรงบิดที่สูงขึ้นในพื้นที่ขนาดเล็ก ลวดจะถูกหล่อด้วยรูปทรงอื่นๆ รวมถึงเกลียวคู่ขนาน ทำให้เกิดเป็นเกลียวที่ปลายแต่ละด้าน
โครงสร้างของสปริง
โครงสร้างของสปริงใหม่เหล่านี้มีแกนที่พัฒนาจากไฟเบอร์กลาสม้วนยาว พันกันและเคลือบด้วยอีพอกซีเรซิน ซึ่งต่อมาเครื่องจักรมีหน้าที่ในการพันเกลียวด้วยเส้นใยคอมโพสิตเพิ่มเติม โดยทำมุมสลับกันที่ ±45° สัมพันธ์กับ แกนตามยาว
ข้อควรจำ: นี่คือวิธีการผลิตเครื่องยนต์ Nissan GT-R
การรักษานี้มีความสำคัญเป็นพิเศษ เนื่องจากเป็นการผ่านการทำงานร่วมกันระหว่างชั้นที่รองรับร่วมกันเหล่านี้ ซึ่งจะทำให้สปริงมีคุณสมบัติการบีบอัดและแรงบิดเพิ่มเติม ด้วยวิธีนี้ แรงบิดผ่านสปริงจะถูกแปลงโดยเส้นใยให้มีความยืดหยุ่นและแรงอัด
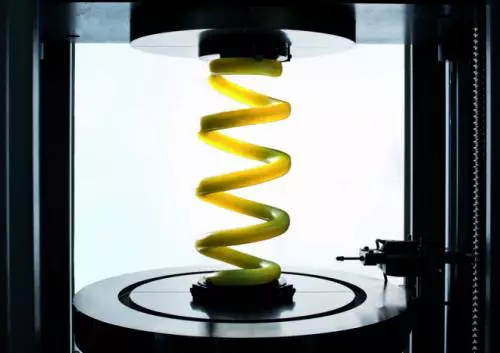
ขั้นตอนการผลิตขั้นสุดท้าย
ในขั้นตอนการผลิตขั้นสุดท้าย สปริงยังคงเปียกและอ่อนนุ่ม ณ จุดนี้เองที่มีการนำโลหะผสมที่มีอุณหภูมิหลอมเหลวต่ำมาใช้ จากนั้นสปริงใน GFRP จะถูกอบในเตาอบที่อุณหภูมิสูงกว่า 100° เพื่อให้โลหะผสมสามารถหลอมรวมกันได้อย่างกลมกลืนกับการชุบแข็งของไฟเบอร์กลาส .
อะไรคือข้อดีของสปริง GFRP เหล่านี้ เมื่อเทียบกับสปริงเหล็กทั่วไป?
นอกเหนือจากข้อได้เปรียบด้านน้ำหนักที่เห็นได้ชัดประมาณ 40% ต่อสปริง สปริง GFRP ยังไม่ได้รับผลกระทบจากการกัดกร่อน แม้หลังจากผ่านไปหลายกิโลเมตรจะมีรอยขีดข่วนและรอยแตกที่เห็นได้ชัดในโครงสร้าง นอกจากนี้ยังกันน้ำได้อย่างสมบูรณ์ กล่าวคือ ทนต่อปฏิกิริยากับสารเคมีที่มีฤทธิ์กัดกร่อนอื่นๆ เช่น ผลิตภัณฑ์ทำความสะอาดสำหรับล้อ
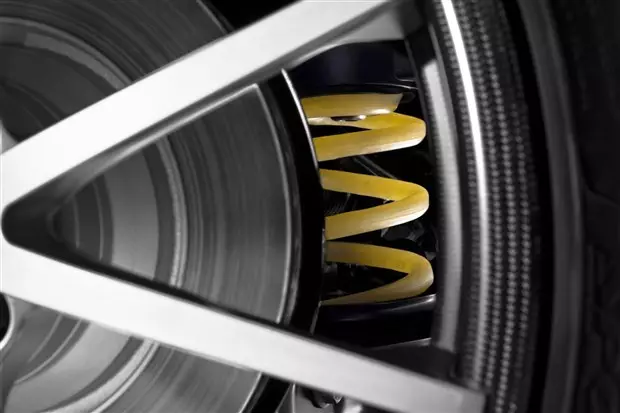
ข้อดีอีกประการของสปริง GFRP เหล่านี้สัมพันธ์กับความน่าเชื่อถือและความทนทาน ซึ่งได้แสดงให้เห็นในการทดสอบแล้วว่าสามารถวิ่งได้ 300,000 กม. โดยไม่สูญเสียคุณสมบัติการยืดหยุ่น ซึ่งมากเกินอายุการใช้งานของโช้คอัพคู่หูของพวกเขา .
MOT TO SPEAK: รายละเอียดทั้งหมดของเครื่องยนต์ 1.5 Skyactiv D ใหม่ของ Mazda
นี่เป็นกระบวนการเริ่มต้นที่ Audi ได้ผลิตต้นแบบสำหรับทดสอบ ก่อนที่จะเริ่มผลิตส่วนประกอบเหล่านี้นับพันชิ้นต่อปี
ตามแบรนด์ของแหวน การผลิตสปริงเหล่านี้ในวัสดุคอมโพสิตต้องการพลังงานน้อยกว่าสปริงเหล็กแบบดั้งเดิม อย่างไรก็ตาม ต้นทุนสุดท้ายจะสูงขึ้นเล็กน้อย ซึ่งเป็นปัจจัยที่อาจขัดขวางการเพิ่มมวลของสปริงอีกสองสามปี ภายในสิ้นปีนี้ Audi คาดว่าจะประกาศสปริงเหล่านี้สำหรับรุ่นระดับไฮเอนด์