If there is a way to increase the efficiency of an engine, it is through its supercharging and we have done it essentially in two ways: through a compressor or a turbocharger (turbo for friends).
Both systems work differently, and have their advantages and disadvantages, but the goal is the same: increase the pressure of the air that reaches the combustion chamber, compressing it, allowing for more efficiency, in other words, more horsepower and torque.
However, in this battle for power, turbos have clearly been preferred, with superchargers almost oblivious. But why? Let's investigate…
how they work
Let's start with the compressors , also identified by superchargers or blowers — and who doesn't remember the Mercedes-Benz Kompressors? — which in the past have even had their (few) moments, thanks to explosive machines like the Hellcat or the small but vibrant Yaris GRMN.
These work essentially like an air pump, and are generally driven by a belt, connected directly to the engine, which creates pressure at idle and increases torque and power at low rpm.
However, it's not all rosy as we climb toward higher engine revs — the compressor ends up stealing more power from the engine than it adds.
already the turbocharger it works by taking advantage of exhaust gases from combustion, using them to turn a turbine that creates pressure. They are capable of turning at much higher speeds than compressors — more than 100,000 rpm, against 10 to 15,000 rpm — but for that to happen, they also need the engine to run at higher revs to run at full capacity.
The low speed simply doesn't get enough gases or they don't travel fast enough for the turbine to rotate at the speed necessary to create pressure. It is the main reason for phenomena such as turbo lag, that is, the delay in the response between the throttle opening and the moment when the turbo starts to provide boost or pressure.

Subscribe to our newsletter here
the common problem
But if both systems have problems of their own, there is one that is common to both. The fact that compressed air is hot, affecting the efficiency of the entire system. A problem that would eventually be solved by our engineers friends, who developed something we know as an intercooler, that is, an air-to-air heat exchanger, famous in models like the Subaru Impreza STI and in several models that had this word inscribed in giant letters in the bodywork.These allow you to cool the air between 40% and 60%, benefiting the achievement of power and torque, but as you may be guessing, this solution also has its problems. The first is space, or rather the lack of it to install them; the second is that they add complexity to the air duct in the engine.
how did they evolve
Both technologies have evolved, in the case of compressors being more “friendly” to high speeds, with solutions such as clutches that disengage them at high speeds — however, the increase in complexity, affecting reliability, makes this solution rare —; and in the case of turbos, we've seen lighter turbine blades, smaller variable geometry turbos, or engines with two sequentially operating turbos (a smaller turbo for low revs and a larger turbo for high revs).
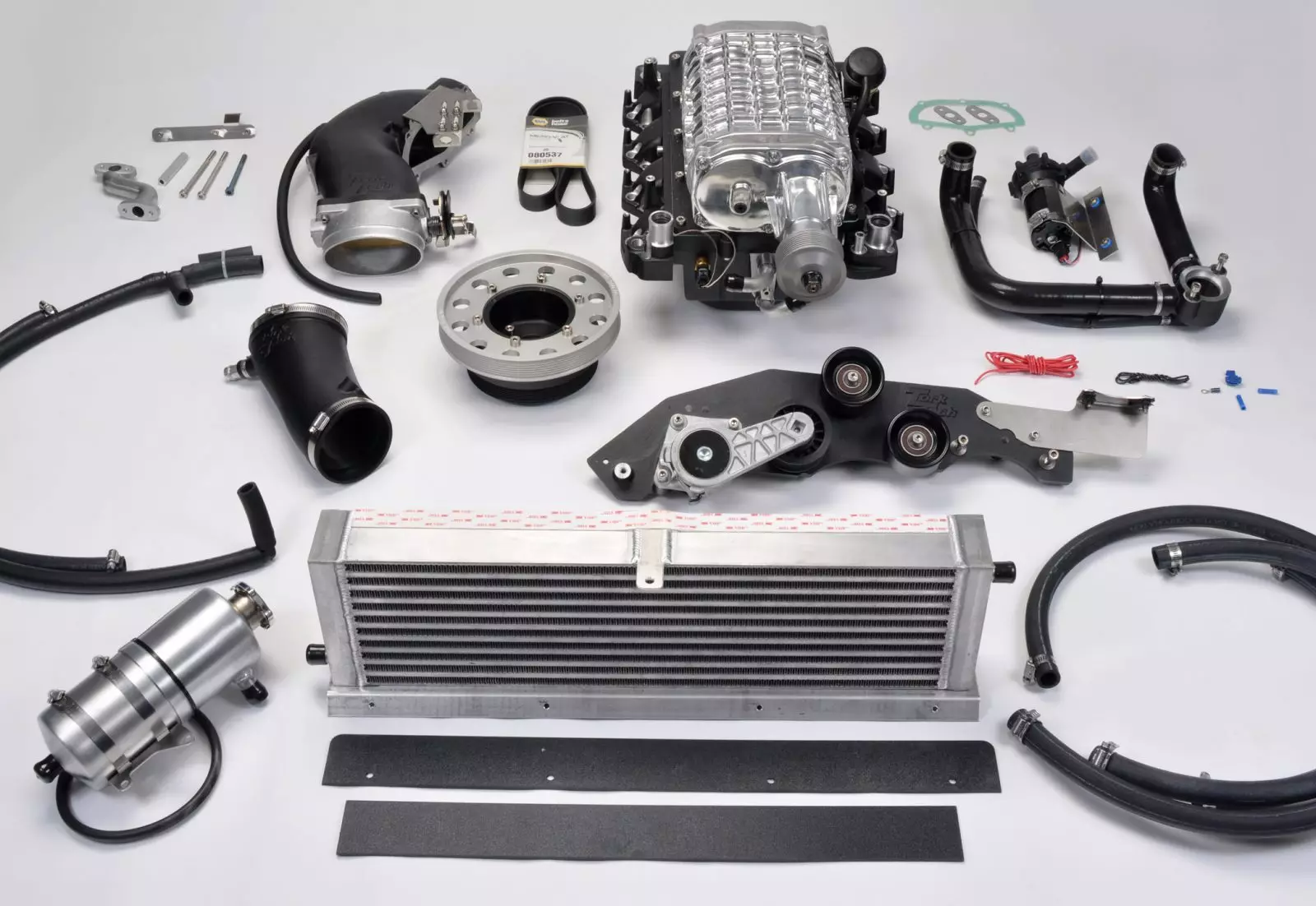
The goal? Achieve superior response at low revs. There have been cases, rarer, in which they combined the two technologies in the same engine, compressor and turbocharger, as we've seen in machines like the Lancia Delta S4, the more modest 1.4 TSI from Volkswagen or some of the versions of the 2.0 from Volvo.
Turbos pass forward
Currently, turbos are clearly preferred by manufacturers due essentially to their superior efficiency, achieving a better performance/economy binomial.
Using a waste to work, as are the exhaust gases, knocks any compressor. The latter end up having a parasitic effect, where to generate more efficiency, they also have to steal it from the engine — in large V8s where it is more common to find them, they can easily need more than 150 hp to work.
Furthermore, it is easier to extract greater power from a turbocharger than from a compressor, starting from the same engine.
Nowadays, with engines adopting small or low-pressure turbos, turbo lag is almost imperceptible, and in high-performance engines, new configurations like the Hot V also allow important gains in the response of the turbos. There is no lag of any kind in the compressors, whose final effect turns out to be similar to having an atmospheric engine with more cubic centimeters, maintaining the linearity of a good atmospheric.
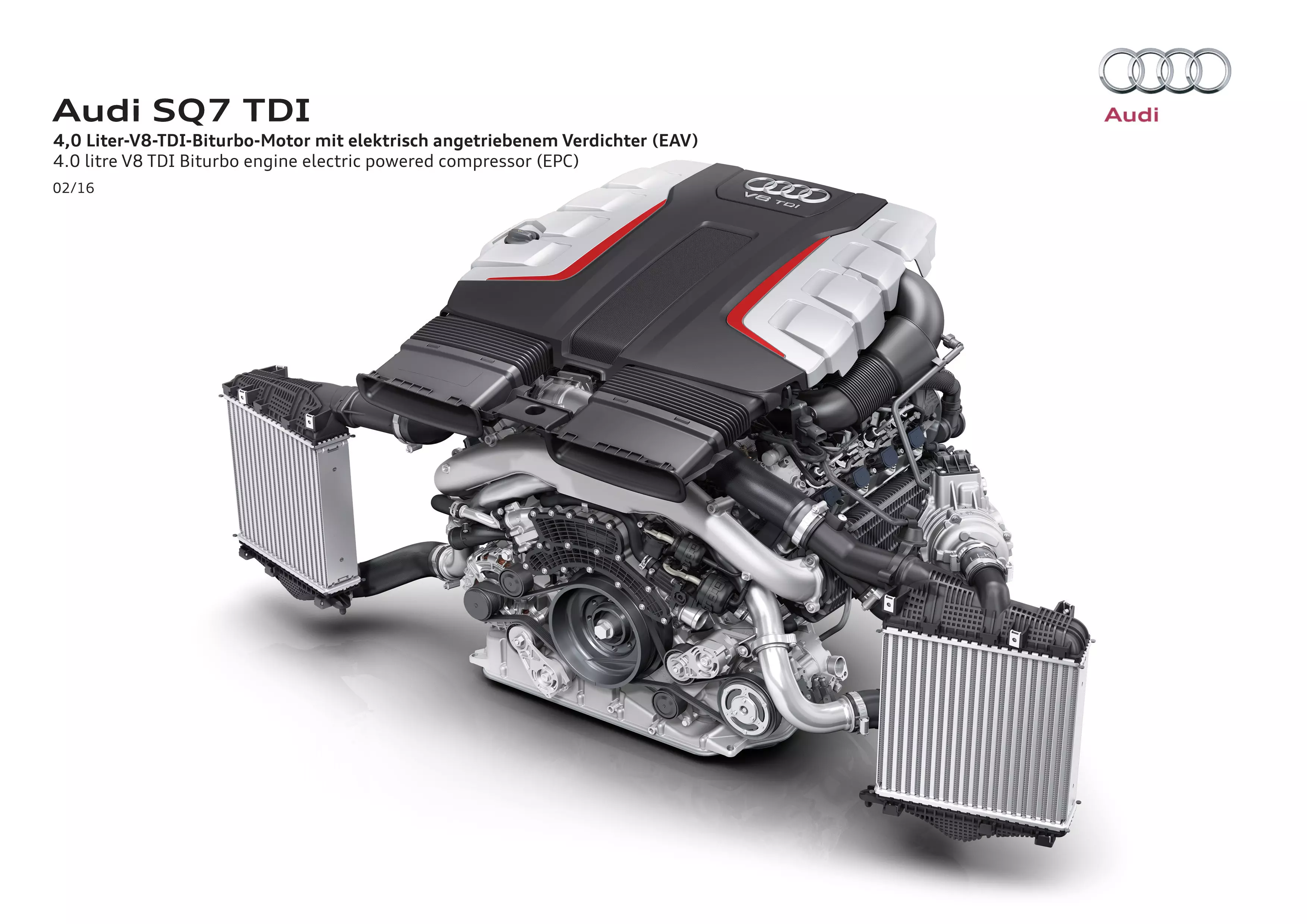
The future
Truth be told, despite the technology used in turbos being more advanced, compressors have not yet "gone down into history". Electric motors came to his aid, which could mean his return to the limelight.
Like? It is no longer necessary to have the compressor physically connected to the engine to start it, using an electric motor. This solution can be used in hybrid systems, joining the turbocharger to the electric drive compressor, a solution seen, for example, in the Audi SQ7.
So, if you really want to know who will win this “war”, the answer is: it's us, users, that we are taking advantage of more and more solutions that allow us not only to have greater performance, but also greater efficiency.