Because the subject is complex, let's first briefly explain the compression ratio concept to understand why Nissan's VC-T variable compression engine is so extraordinary? So I'm going to try to simplify, at the risk of committing some inaccuracy – if that happens you can always go through our Facebook and leave us a comment.
Rate what?
The compression ratio is the amount of times a given volume is compressed inside the cylinder. Practical example: a 1.0 liter four-cylinder engine with a 10:1 ratio has 250 cm³ cylinders which, at their top dead center, compress the mixture to a volume of just 25 cm³ — that is, to one-tenth of its volume (10 :1). The complex version of the compression ratio explanation can be seen here.And why is this so important?
Because the greater the compression ratio of the engine, the greater its efficiency. The greater the compression of the engine, the faster the expansion of the gases resulting from the explosion and consequently the faster the descent of the piston and connecting rod, and therefore faster the displacement of the crankshaft - ultimately resulting in more movement transmitted to the vehicle wheels. That's why sports cars have higher compression ratios – for example, the Audi R8's V10 engine compresses 12.7 times its volume.
So why don't all cars have high compression ratios?
For two reasons: the first reason is that the mixture pre-detonates and the second reason is that it is expensive to make an engine with a high compression ratio. But let's go to the first reason first. As the compression ratio increases, so does the temperature of the air-fuel mixture inside the combustion chamber and this increase in temperature can lead to ignition before the piston reaches top dead center. The name of this phenomenon is pre-detonation and it is because of this effect that car brands are forced to produce engines with conservative compression ratios, with ignition and injection maps designed to protect the engine from this phenomenon at the expense of maximum efficiency.On the other hand, producing engines with high compression ratios is also expensive (for brands and therefore for customers…). Because to avoid pre-detonation in engines with high compression ratios, brands have to resort to nobler and more resistant materials that dissipate the heat generated in the engine more efficiently.
Nissan finds (finally!) the solution
Over the last 25 years several brands have tried unsuccessfully to overcome the limitations of engines to this level. Saab was one of the brands that came closer, even presenting a revolutionary engine that, thanks to the lateral movement of the engine head, managed to increase or decrease the cubic capacity of the combustion chamber. and hence the compression ratio. Problem? The system had reliability flaws and never made it into production. Happily…
The first brand to find a solution was, as we said, Nissan. A brand that will present the world's first variable compression engine in September at the Paris Motor Show. It is a 2.0 Turbo engine with 274 hp and 390 Nm of maximum torque. This engine will initially only be launched in the U.S.A, replacing the 3.5 V6 engine that currently equips Infiniti models (Nissan's premium model division).
How did Nissan achieve this?
It was witchcraft. I'm kidding… it was pure engineering. In conventional engines the connecting rods (that arm that “grabs” the piston) are directly attached to the crankshaft, in Nissan's VC-T engine this does not happen. As you can see in the image below:
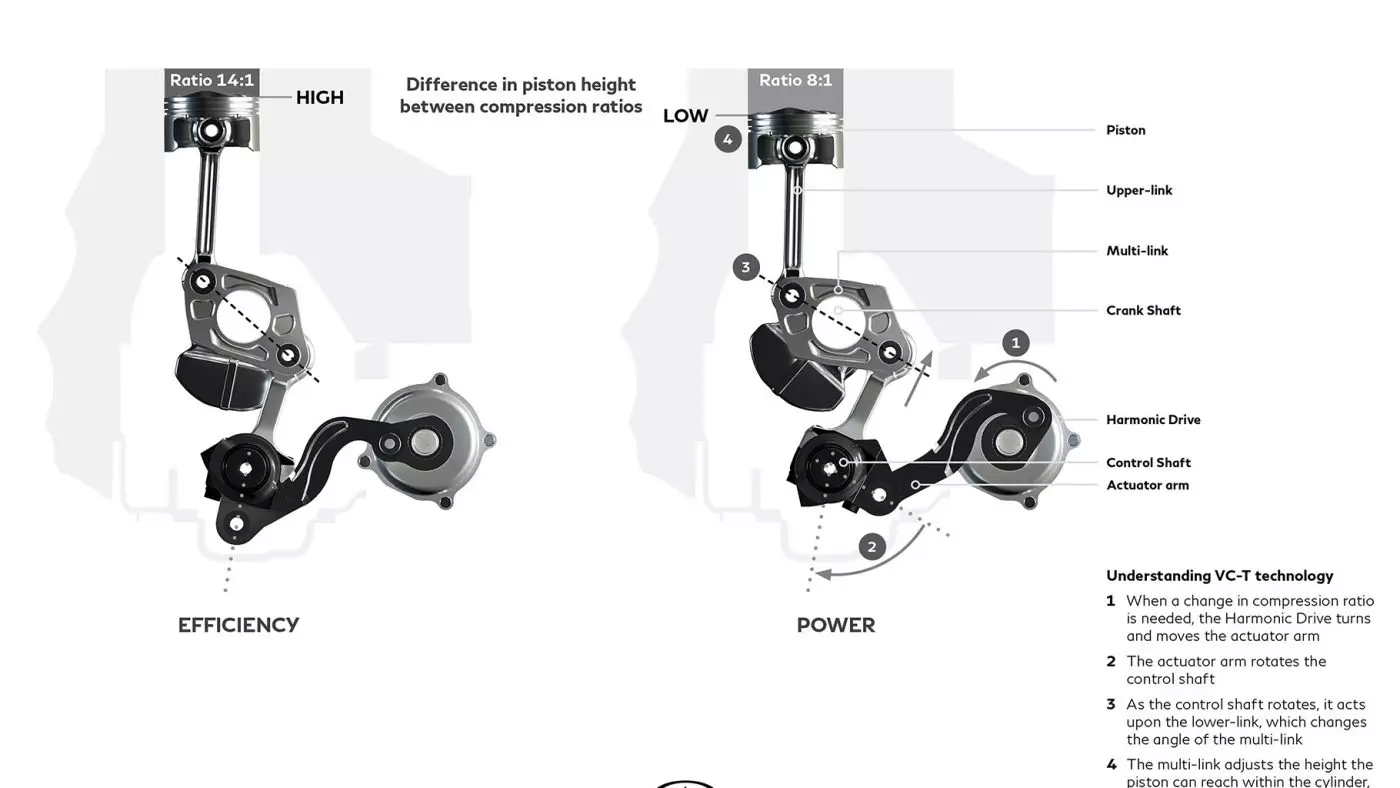
In this revolutionary Nissan engine the length of the main connecting rod was reduced and connected to an intermediate lever pivoted to the crankshaft and connected to a second movable connecting rod opposite the connecting rod which varies the extent of piston movement. When the engine control unit determines that it is necessary to increase or reduce the compression ratio, the actuator changes the angle of the intermediate lever, raising or lowering the connecting rod and therefore varying the compression between 8:1 and 14:1. Thus, the Nissan engine manages to combine the best of both worlds: maximum efficiency at low rpm and more power at high rpm, avoiding the pre-detonation effect.
This variation in the engine's compression ratio is only possible efficiently and in any rpm range, thanks to a myriad of sensors spread throughout the engine. These send hundreds of thousands of information per second to the ECU in real time (temperature of the air, combustion chamber, intake, turbo, amount of oxygen in the mixture, etc.), allowing the compression ratio to be changed accordingly. the needs of the vehicle. This engine is also equipped with a variable valve timing system to simulate the Atkinson cycle, in which the intake valves stay open longer to allow air to escape through them, thus reducing the engine's aerodynamic resistance in the compression phase.
Those who repeatedly announce the end of the internal combustion engine must go back to “keep the guitar in the bag” . The “old” internal combustion engines are already over 120 years old and seem to be here to stay. It remains to be seen whether this solution will be reliable.
A little more history?
The first studies on the effects of compression ratio on the duty cycle efficiency of internal combustion engines date back to 1920, when the British engineer Harry Ricardo headed the Aeronautical Development Department of the Royal Air Force (RAF). One of his most important missions was to find a solution for the high fuel consumption of the RAF aircraft and consequently for their short flight range. To study the causes and solutions to this problem, Harry Ricardo developed an experimental engine with variable compression where he found (among other things) that some fuels were more resistant to detonation. This study culminated in the creation of the first fuel octane rating system.
It was thanks to these studies that, for the first time, it was concluded that higher compression ratios are more efficient and require less fuel to produce the same mechanical energy. It was from this time that the gigantic engines with 25 liters of cubic capacity – which we know from World War I planes – began to give way to smaller and more efficient units. Transatlantic travel became a reality and tactical limitations during the war (due to the range of engines) were alleviated.
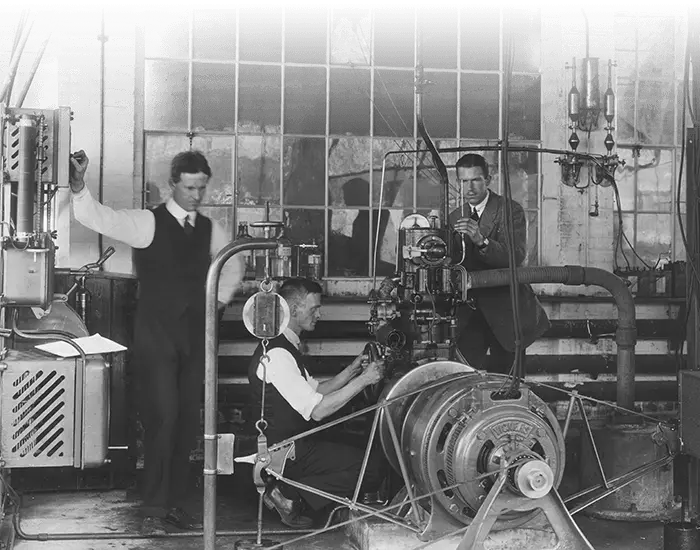