Vergangenes Jahr SEAT hat seinen Umsatz- und Gewinnrekord in seiner 70-jährigen Geschichte gebrochen und die spanische Marke scheint nach Jahren der Verluste ihre Zukunft erobert zu haben.
Wenn 2019 mit einem Höchststand endete – mit einem Umsatz von über 11 Mrd.
Nicht nur der CEO von SEAT, Luca De Meo, hat sich dem Wettbewerb gestellt (Renault), sondern - hauptsächlich - die Pandemie hat die aufeinander folgenden Jahre der Verbesserung aller Arten von Wirtschaftsindikatoren gebremst, wie dies in den meisten Wirtschaftssektoren der Fall war Unternehmen auf der ganzen Welt.
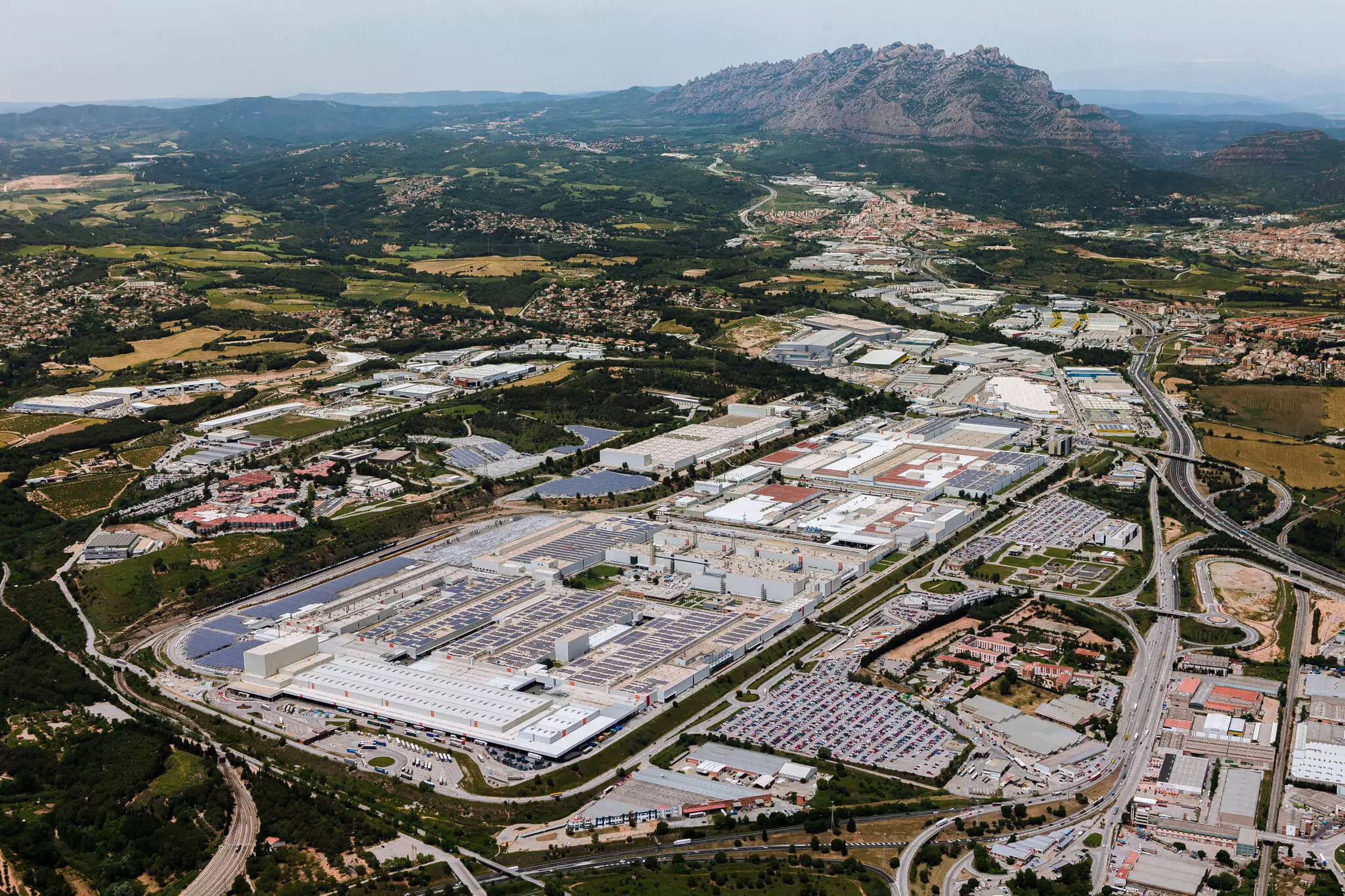
Die jüngste Serie des Umsatzwachstums der spanischen Marke gegenüber dem Vorjahr (von 400.000 im Jahr 2015 auf 574.000 im Jahr 2019, 43% mehr in nur vier Jahren) wird daher in diesem Jahr gestoppt.
11 Millionen Autos hergestellt
Das Werk in Martorell wurde 1993 nach nur 34 Monaten Bauzeit (damals eine Investition von 244,5 Millionen Peseten, umgerechnet 1470 Millionen Euro) eingeweiht und in 27 Jahren wurden rund 11 Millionen Fahrzeuge produziert, aufgeteilt in 40 Modelle oder Derivate.
Seitdem hat sich viel verändert, die Fläche des gesamten Industriekomplexes hat sich versiebenfacht auf aktuell 2,8 Millionen Quadratmeter, auf die (nur zur Veranschaulichung) 400 Fußballfelder passen würden.
Abonniere unseren Newsletter
Und es ist bei weitem nicht das einzige Produktionszentrum der spanischen Marke in diesem Bereich. In der Freizone am Fuße der Stadt (wo 1953 und bis 1993 die Automobilproduktion des Unternehmens begann) werden diverse Teile (Türen, Dächer, Kotflügel, insgesamt über 55 Millionen für 20 Fabriken) nur von mehreren Marken des Volkswagen Konzerns gepresst im Jahr 2019); am Rande des Flughafens, in Prat de Llobregat, befindet sich ein weiteres Komponentenfertigungszentrum (von dem letztes Jahr 560.000 Getriebe produziert wurden); sowie ein Technical Center (seit 1975 und in dem heute mehr als 1100 Ingenieure arbeiten).
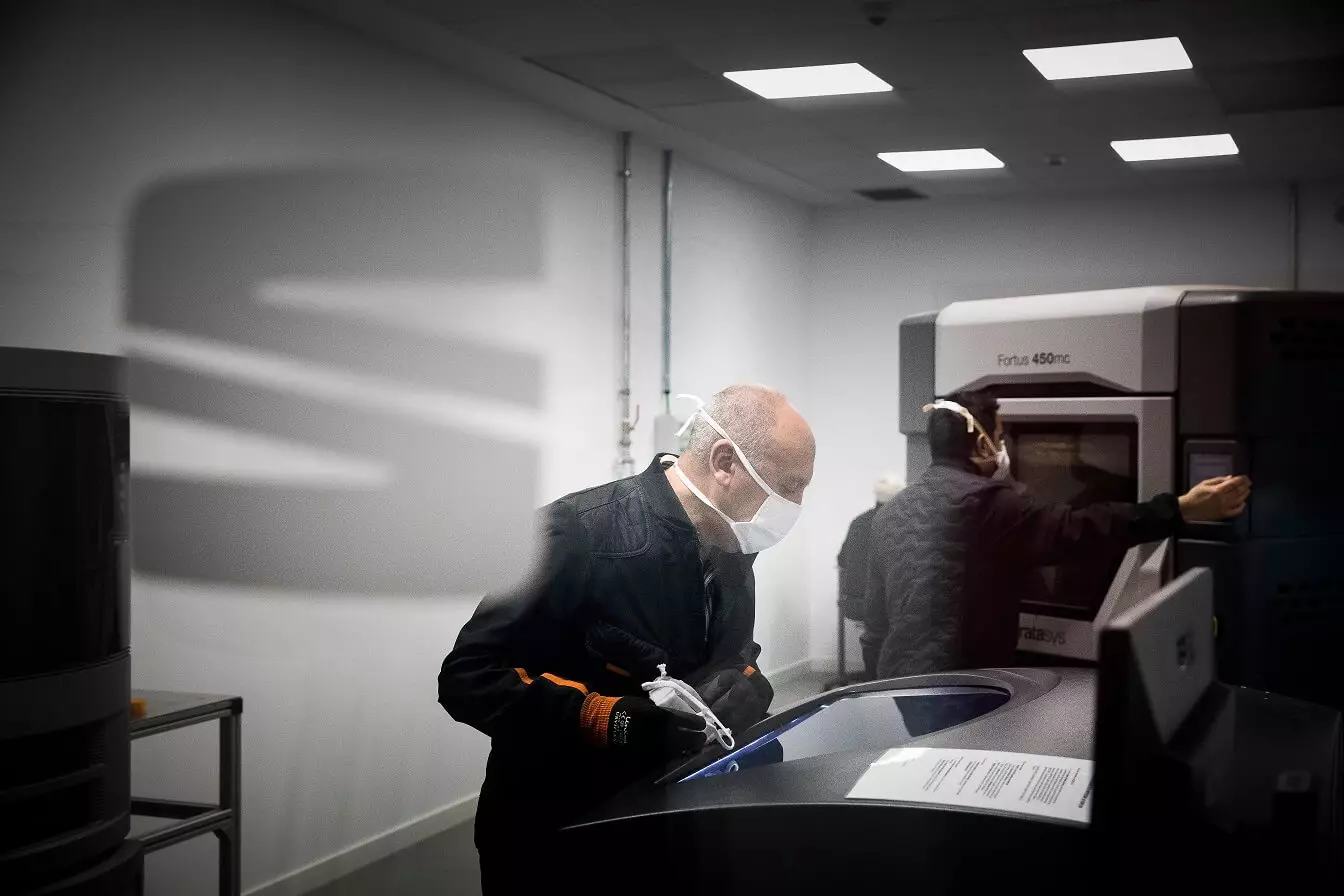
3D-Druckzentrum
Damit ist SEAT eines der wenigen Unternehmen des Landes, das seine Produkte in Spanien entwirft, technisch entwickelt und fertigt. Und in der Region und verbunden mit SEAT gibt es auch ein riesiges Logistikzentrum, ein 3D-Druckzentrum (seit kurzem neu und in der Fabrik selbst) und ein Digital Lab (in Barcelona), in dem über die Zukunft der menschlichen Mobilität nachgedacht wird (mit wichtigen Integration von Universitätsstudenten, die auch im Werk eine ständige Ausbildung absolvieren, im Rahmen eines Protokolls mit der Polytechnischen Universität von Katalonien).
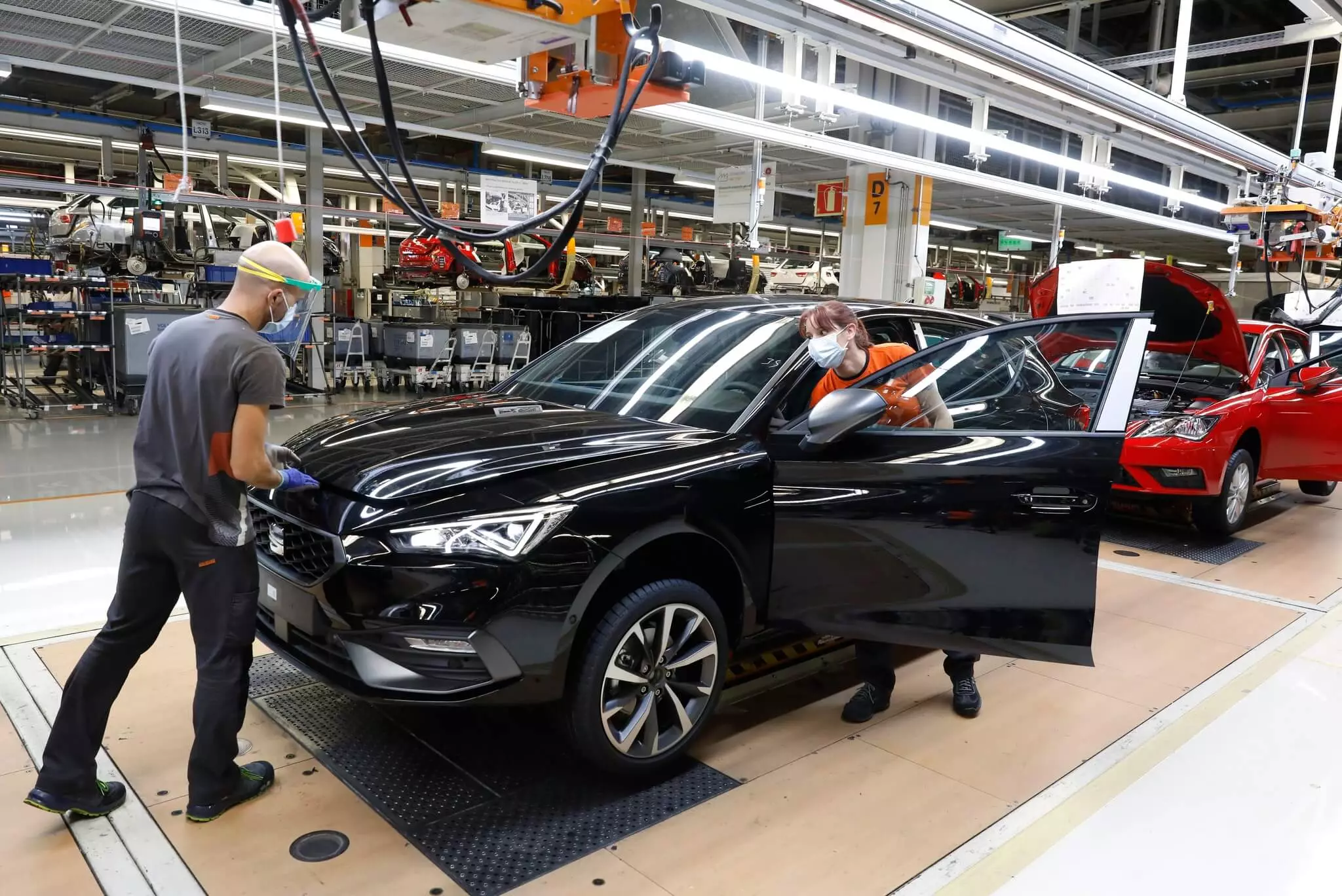
27 Jahre verändern alles
Zu Beginn, 1993, fertigte Martorell 1500 Autos pro Tag, heute rollen 2300 „auf eigene Faust“, das heißt alle 30 Sekunden ein neues Auto, das bereit ist, an einen eifrigen Kunden zu versenden.
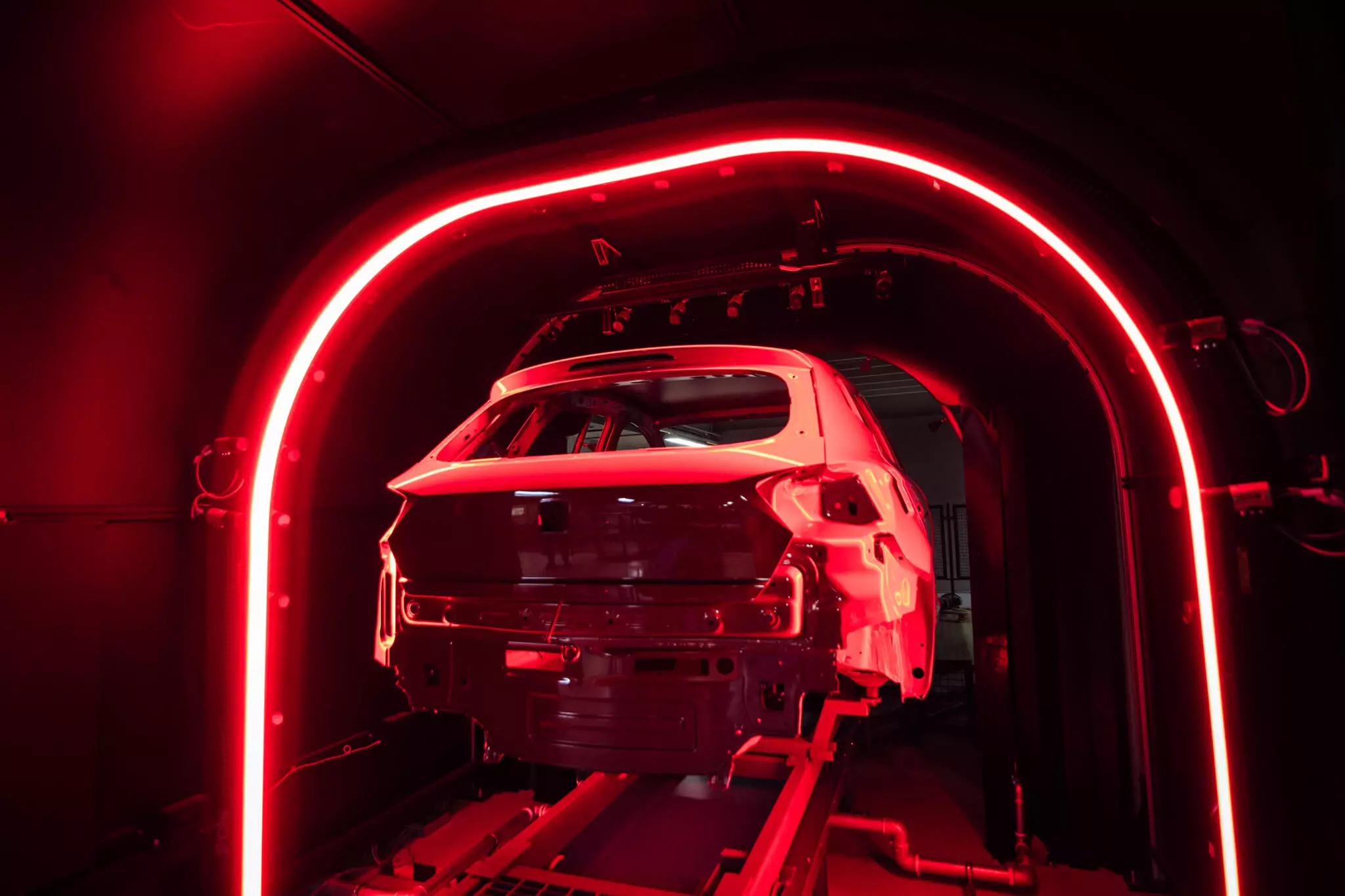
Von 60 Stunden auf 22 Stunden, um ein neues Auto zu bauen: Heute tragen 84 Roboter dünne Lackschichten in einer Lackierkabine auf und ein hochmoderner Scanner prüft die Glätte der Oberfläche in nur 43 Sekunden. Virtual Reality, 3D-Druck und Augmented Reality sind weitere Innovationen, die mit dem Aufkommen von Industrie 4.0 entstanden sind.
Juan Pérez, Verantwortlicher für DruckprozesseIch war gerade 18 Jahre alt, als ich zum ersten Mal die Fabrik in Martorell betrat und erinnere mich an die euphorische Atmosphäre in der Stadt, in der gerade die Olympischen Spiele stattfanden. Er war Lehrling und meine Kollegen und ich hatten große Hoffnungen in die Zukunft – alles war neu und uns wurde gesagt, es sei die modernste Fabrik Europas.
So erinnert sich Juan Pérez, derzeit Leiter der Druckprozesse, an die ersten Tage vor 27 Jahren im Werk Martorell, wo die Mitarbeiter täglich 10 km zu Fuß gelaufen sind: „Als ich nach Hause ging, konnte ich nicht einmal das Schließfach finden Zimmer. Es war sehr leicht, sich zu verirren.“
Heute gibt es autonome Fahrzeuge, die den Mitarbeitern helfen, täglich rund 25.000 Teile auf die Strecke zu bringen, dazu kommen 10,5 km Eisenbahn und 51 Buslinien.
Ein Portugiese führt Qualität
Ebenso oder wichtiger ist der stetige qualitative Fortschritt auch in jüngster Zeit, wie die neuesten Indikatoren zeigen: Zwischen 2014 und 2018 sank die Zahl der Reklamationen von Besitzern spanischer Markenmodelle um 48 % und Martorell liegt praktisch auf dem Niveau der Qualitätsrekorde / Zuverlässigkeit des Volkswagen-Stammwerks in Wolfsburg.
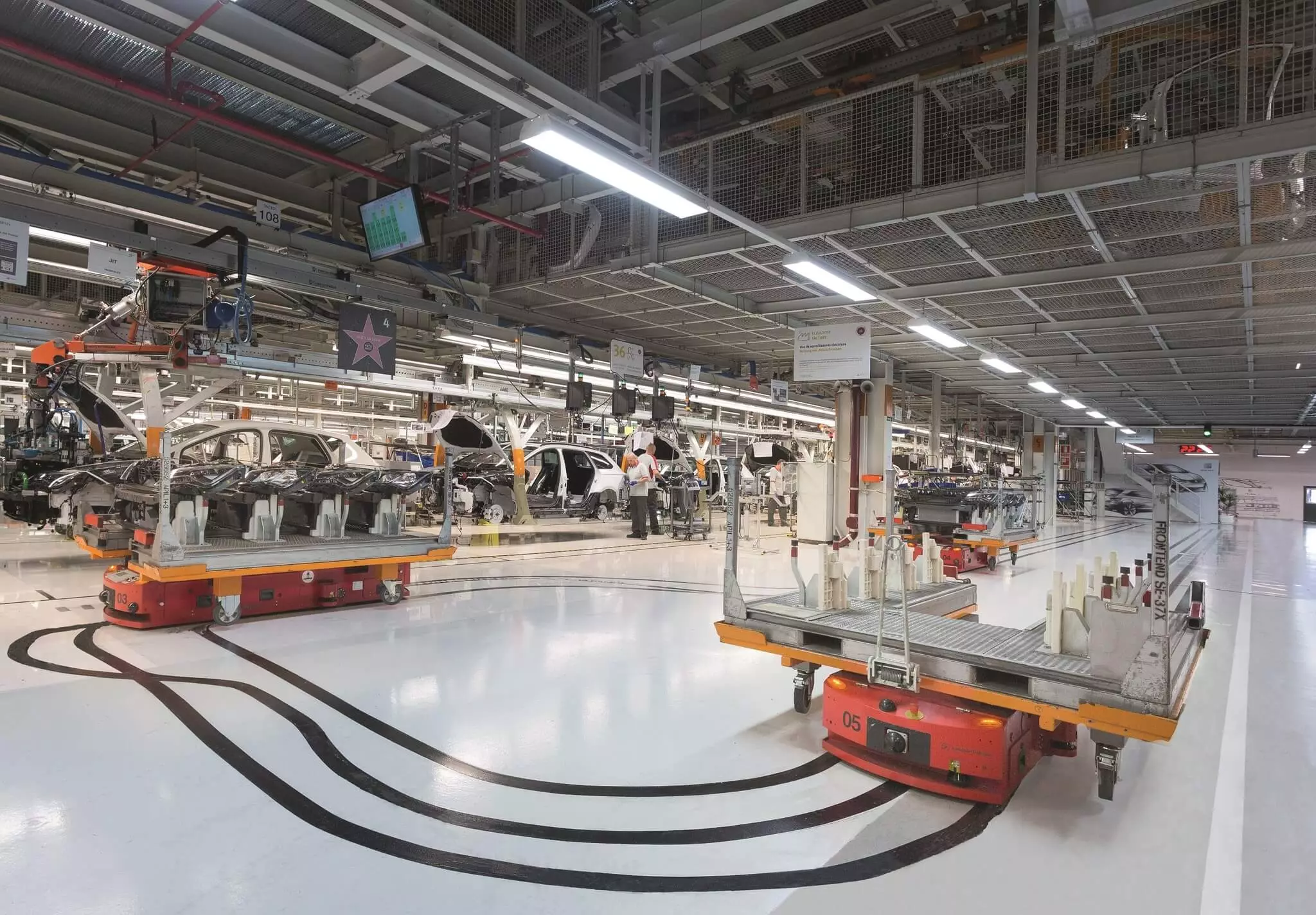
Dies sollte nicht überraschen, wenn man bedenkt, dass die gleichen industriellen Prozesse von A bis Z verfolgt werden, wie José Machado bestätigt hat, der Portugiese, der jetzt die Qualitätskontrolle in Martorell leitet, nachdem er bei Autoeuropa (in Palmela) angefangen hat, von wo aus er nach Puebla ( Mexiko), um diese wichtige Position in der Wiege fast aller SEAT einzunehmen:
José Machado, Direktor der QualitätskontrolleWir folgen alle dem gleichen Leitbild und das zählt, denn am Ende zählen zu unseren 11.000 Mitarbeitern – direkt und indirekt – 67 Nationalitäten und 26 verschiedene Sprachen.
80 % sind Männer, 80 % sind unter 50 Jahre alt, sind durchschnittlich 16,2 Jahre im Unternehmen und 98 % haben einen unbefristeten Arbeitsvertrag, was dazu beiträgt, Stabilität in den Menschen zu schaffen, die sich dann in der Qualität ihrer Arbeit. Arbeit.
Leon ist derjenige, der am meisten produziert und verkauft
Ebenso stolz oder noch stolzer auf das, was hier getan wird, ist Ramón Casas – Direktor der Abteilung Montage und Innenausbau – der Hauptleiter dieses Besuchs, der sich auf diesen Bereich konzentriert, für den er hauptsächlich verantwortlich ist: „Wir haben drei Montagen“ Linien insgesamt, 1 von Ibiza/Arona (die 750 Autos/Tag fertigstellt), 2 von Leon und Formentor (900) und 3 von einem exklusiven Audi A1 (500)“.
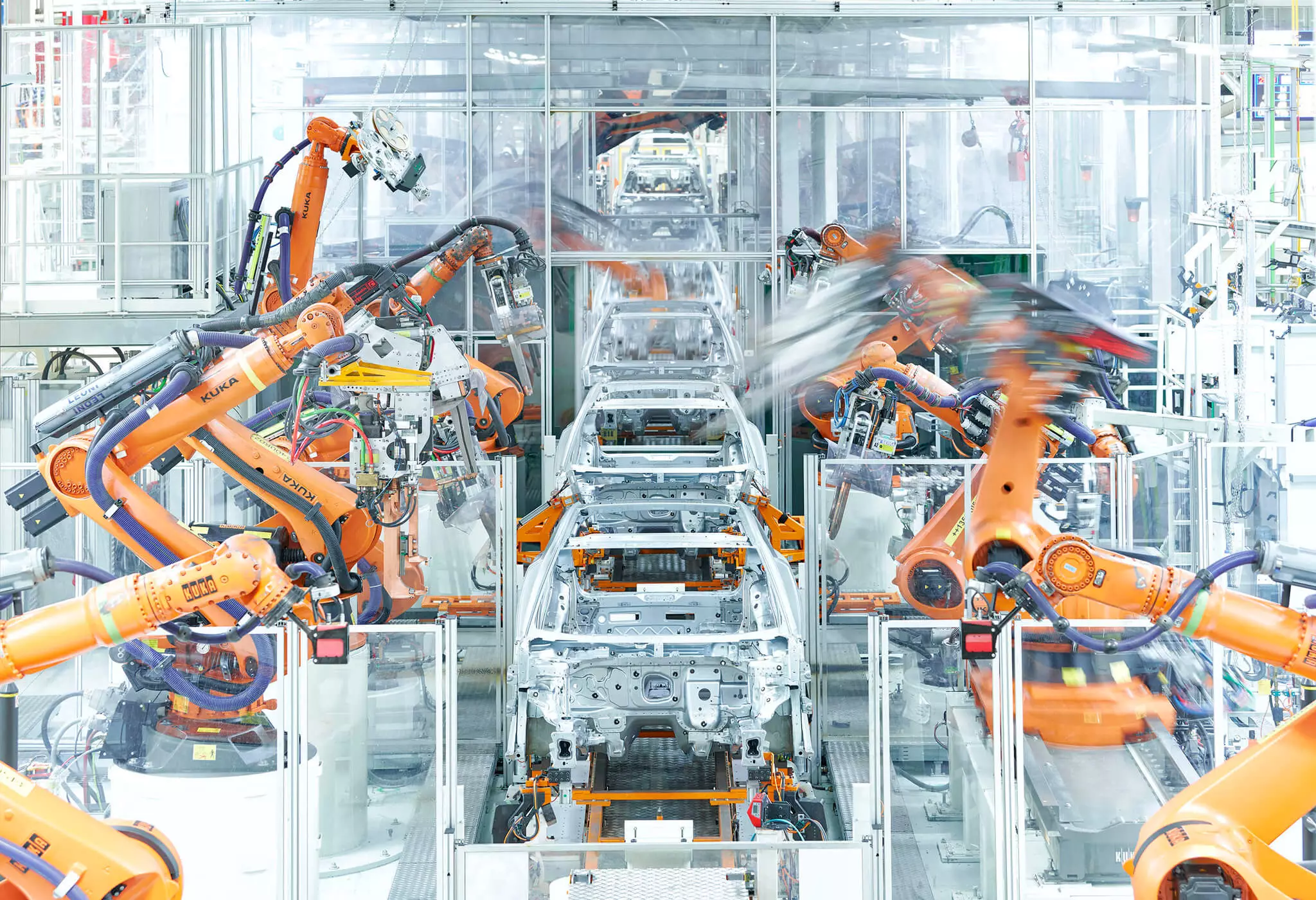
In diesem Fall befinden wir uns in der Wiege von Leon und Derivaten, da dieser Besuch zusätzlich zu einer Werksfahrt erfolgte, um den Leon Sportstourer-Van abzuholen, bevor er über die üblichen Kanäle auf dem portugiesischen Markt ankam.
Casas erklärt, dass „diese Linie 2 diejenige ist, die die meisten Autos produziert, weil der Leon der meistverkaufte SEAT weltweit ist (ca. 150.000/Jahr), etwas höher als der Ibiza und der Arona (jeweils ca. 130.000) dieser Montagelinie beigetreten ist, wird die Produktionskapazität fast erschöpft sein.“
Die 500 005 Autos, die 2019 in Martorell hergestellt wurden (81 000 davon Audi A1), 5,4% mehr als 2018, nutzten 90% der installierten Kapazität des Werks, eine der höchsten Quoten in ganz Europa und ein sehr positiver Indikator von die finanzielle Gesundheit des Unternehmens.
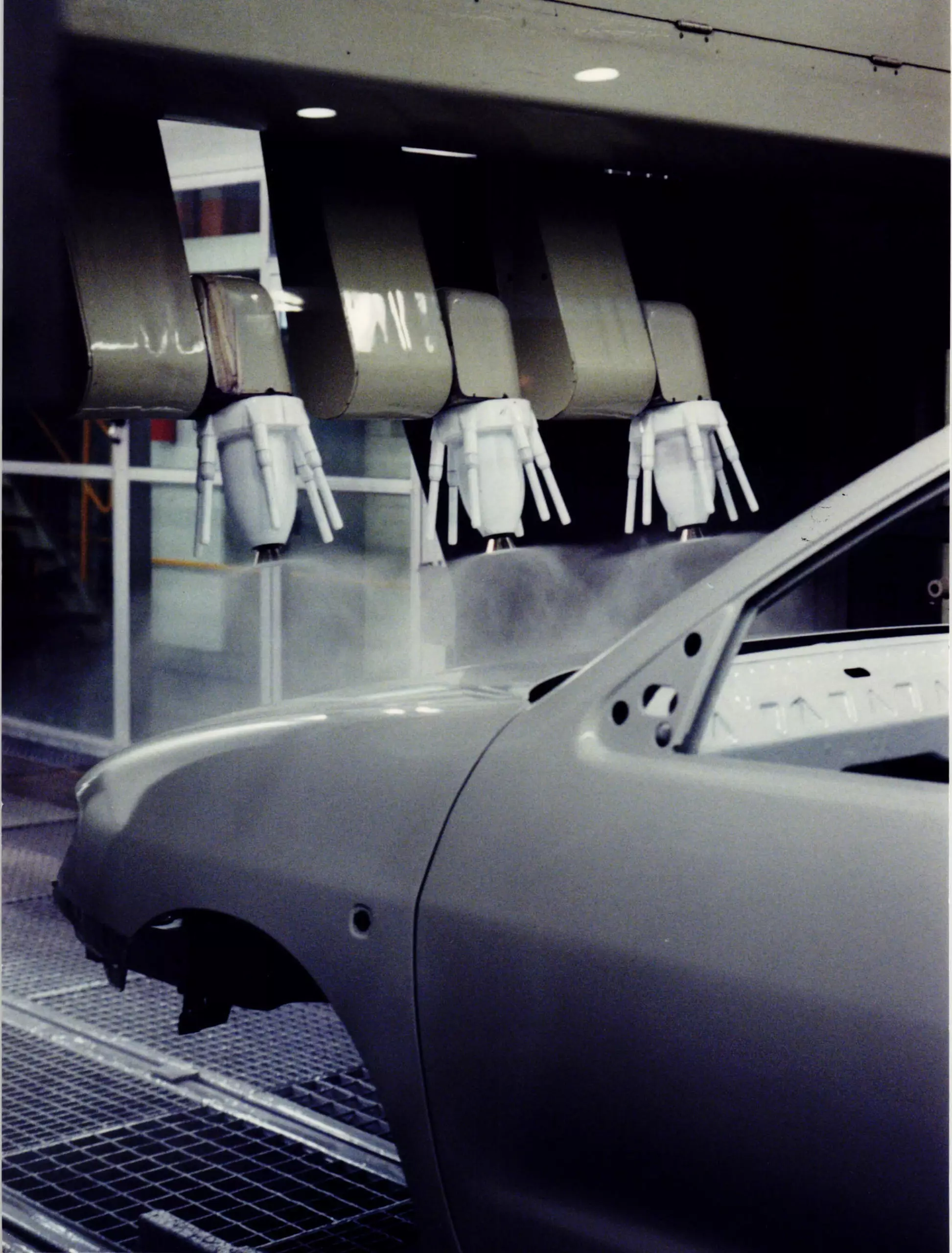
Die spanische Marke hatte jedoch einen höheren Absatz als die 420.000 in Martorell im letzten Jahr produzierten SEAT, da einige ihrer Modelle außerhalb Spaniens hergestellt werden: der Ateca in Tschechien (Kvasiny), der Tarraco in Deutschland (Wolfsburg), der Mii in der Slowakei (Bratislava) und der Alhambra in Portugal (Palmela).
Insgesamt hat SEAT im Jahr 2019 592.000 Autos produziert, wobei Deutschland, Spanien und Großbritannien die Hauptmärkte sind, in dieser Reihenfolge (80% der Produktion sollen in rund 80 verschiedene Länder exportiert werden).
22 Stunden, um einen SEAT Leon zu bauen
Ich setze meine Tour auf einem Teil der 17 km langen Gleise mit elektrifizierten Schienen, dann hängenden Wagenkästen und rollenden Untergestellen mit bereits montierten Motoren/Boxen (die später in dem, was die Fabriken "Hochzeit" nennen) zu finden, fort, während die beiden Führer weiterhelfen Details: Es gibt drei Hauptbereiche in jeder der Montagelinien, Karosserie, Lackierung und Montage, "aber der letzte ist, wo die Autos mehr Zeit verbringen", beeilte er sich, Ramón Casas hinzuzufügen, oder wenn das nicht wäre auch die einer unter seiner direkten Verantwortung.
In insgesamt 22 Stunden, die jeder Leon für die Produktion benötigt, verbleiben 11:45min in der Montage, 6:10min in der Karosserie, 2:45min in der Lackierung und 1:20min in der Endbearbeitung und Endkontrolle.

Werksleiter sind sehr stolz darauf, dass sie die Modellgeneration wechseln können, ohne die Montagekette unterbrechen zu müssen. „Auch mit breiteren Fahrspuren und einem anderen Radstand konnten wir die Produktion des neuen Leon integrieren, ohne die Produktion der Vorgängergeneration einstellen zu müssen“, betont Casas, für den es andere heiklere Herausforderungen gibt:
Ramón Casas, Direktor der Sektion Montage und Innenausbauder vorherige Leon hatte 40 elektronische Recheneinheiten, der neue hat mindestens doppelt so viel und wenn wir den Plug-in-Hybrid betrachten, sprechen wir von 140! Und sie alle müssen vor der Installation getestet werden.
Kompliziert ist auch die Reihenfolge der Teile, damit die Konfiguration des Autos genau der Bestellung entspricht. Allein bei der Front des Leon kann es 500 Variationen geben, was eine Vorstellung von der Schwierigkeit der Aufgabe gibt.
José Machado erklärt auch, dass „es keinen Zeitunterschied zwischen der Produktion eines Leon-Fünftürers oder eines Sportstourer-Vans und der Tatsache gibt, dass letzterer in den letzten Jahren an Popularität gewonnen hat – 40 % der Verkäufe gegenüber 60 % des Fünftürers – hat das Fließband nicht beeinflusst“.

Drohnen und Roboter helfen...
In Martorell gibt es mehr als einen Robotertyp. Es gibt solche, die zwischen verschiedenen Bereichen des riesigen Industriekomplexes liefern (wie Drohnen und automatisierte Landfahrzeuge, insgesamt 170 innerhalb und außerhalb der Fabrik) und dann Roboter, die helfen, die Autos selbst zusammenzubauen.
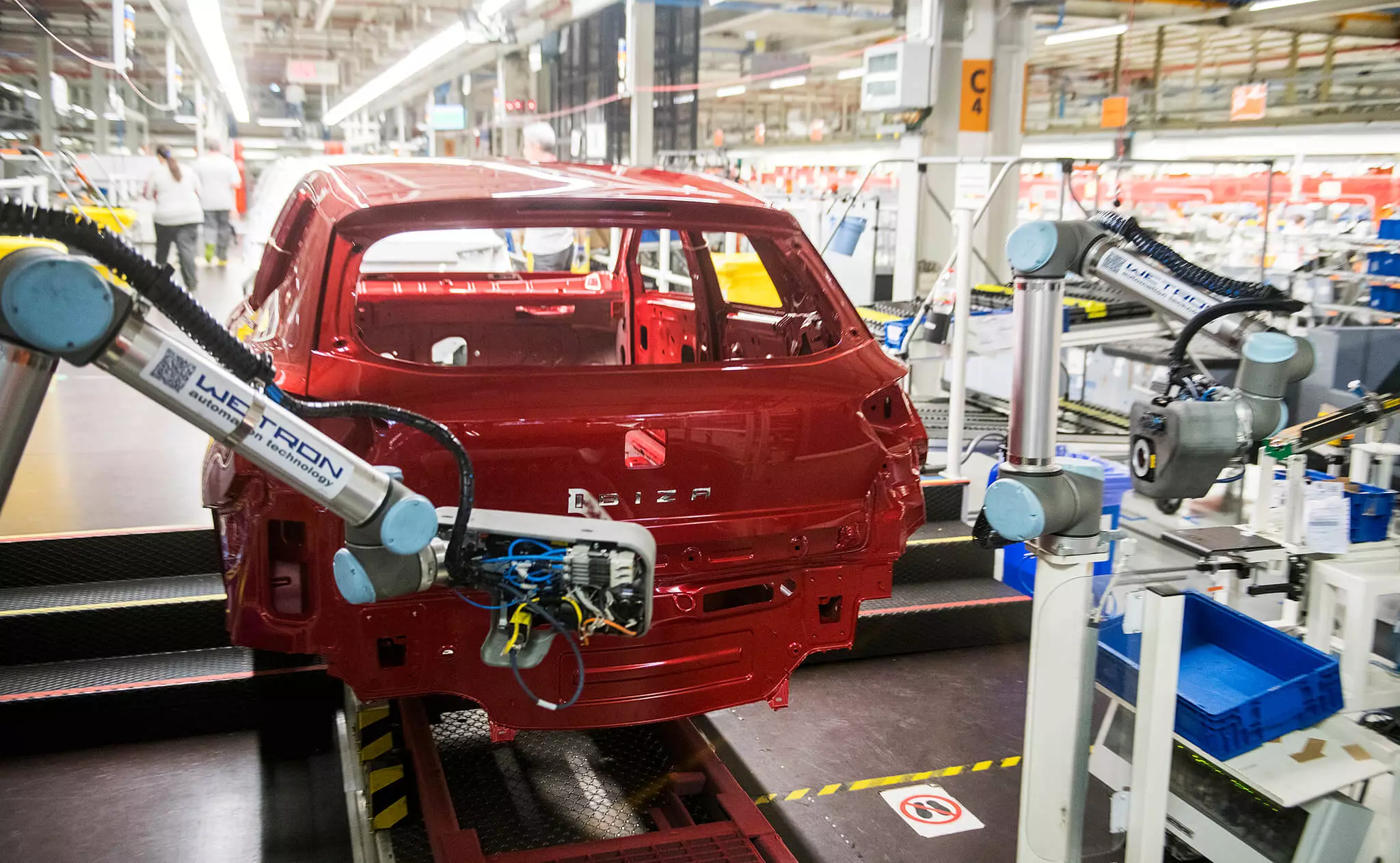
Machado sagt, dass „je nach Bereich der Montagelinie unterschiedliche Robotisierungsraten bestehen, mit etwa 15 % im Montagebereich, 92 % in der Beschichtung und 95 % in der Lackierung“. Im Montagebereich helfen viele der Roboter den Mitarbeitern, schwerere Teile wie die Türen (kann bis zu 35 kg erreichen) zu nehmen und zu drehen, bevor sie in die Karosserie eingebaut werden.
…aber der Mensch macht den Unterschied
Der Qualitätsleiter bei Martorell unterstreicht auch die Bedeutung des menschlichen Teams in dieser Industrieeinheit:
José Machado, Direktor der Qualitätskontrolle.Sie sind diejenigen, die das Signal geben, falls es ein Problem in der Montagekette gibt, den Vorgesetzten anrufen, der versucht, das Problem während der laufenden Linie zu lösen, und alles tun, damit es nicht aufhört. Sie wechseln alle zwei Stunden die Rollen, um übermäßige Routine zu vermeiden und sie auch mehr zu motivieren, und geben sogar Ideen, um den gesamten Prozess produktiver zu gestalten. Und wenn einer der Vorschläge angewendet wird, erhalten sie am Ende einen Prozentsatz dessen, was die Fabrik mit dieser Änderung eingespart hat.
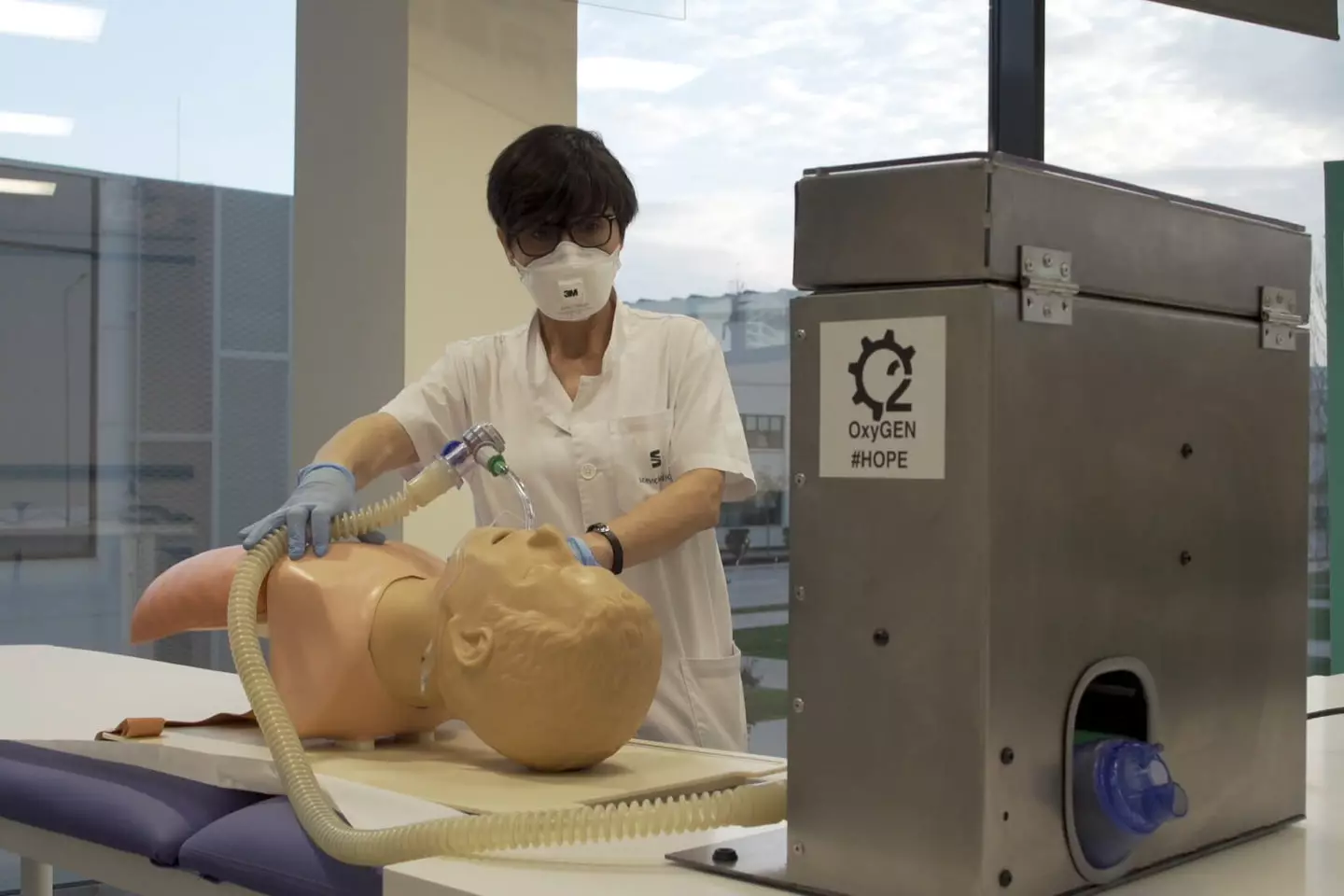
SEAT begann schnell damit, Fans im Kampf gegen Covid-19 zu produzieren.
Martorell wurde während der schwersten Phase der Ausbreitung von Covid-19 geschlossen, wie mir Ramón Casas erklärt:
Ramón Casas, Direktor der Sektion Montage und InnenausbauEnde Februar sind wir alle nach Hause gefahren, am 3. April haben wir mit der Fan-Produktion begonnen und sind am 27. April wieder an die Arbeit gegangen, um nach und nach alle Mitarbeiter auf Viren zu testen. Während des gesamten Aufenthalts in der Fabrik ist das Tragen einer Maske obligatorisch, überall gibt es Gel und viele Acrylschutzvorrichtungen in den Ruheräumen, der Cafeteria usw.