Porsche erforscht aktiv die 3D-Drucktechnologie und wendet sie nun erstmals auf hochbelastete bewegliche Bauteile wie Kolben an. Noch sind sie ein Prototyp, aber die ersten Ergebnisse von Tests an gedruckten Kolben sind vielversprechend.
Ergebnis einer Entwicklungspartnerschaft zwischen Porsche, Mahle und Trumpf (die die Produktions- und Druckverfahren entwickeln), um diese Technologie zu testen, montierte der deutsche Hersteller diese Kolben im Sechszylinder des „Monsters“ 911 GT2 RS.
Sie fragen sich vielleicht, warum Kolben drucken?
Bereits die Schmiedekolben im Motor des 911 GT2 RS verwenden eine Fertigungstechnologie, die Leichtigkeit, Stärke und Langlebigkeit vereint. Wesentliche Merkmale, um den Strapazen der versprochenen Höchstleistung standzuhalten.
Es ist jedoch möglich, weiter zu gehen. 3D-Druck oder additive Fertigung (durch Schichten) ermöglicht es Ihnen, das Kolbendesign insbesondere auf struktureller Ebene zu optimieren, indem nur Material aufgetragen wird und nur dort, wo Kräfte auf den Kolben wirken. Eine Optimierung, die mit herkömmlichen Herstellungsverfahren nicht zu erreichen ist, nur möglich, weil der 3D-Druck das Objekt Schicht für Schicht „erzeugt“ und es ermöglicht, neue Formen zu erforschen.
Abonniere unseren Newsletter
Durch die Designoptimierung entstehen eher organische als geometrische Formen, die direkt aus der Natur zu kommen scheinen, daher die Bezeichnung bionisches Design.
Am Ende haben wir ein Bauteil mit der notwendigen strukturellen Integrität – Porsche sagt, dass seine gedruckten Kolben noch stärker sind als geschmiedete – aber weniger Material benötigt wird, um dies zu erreichen, was zu einem leichteren Bauteil führt.
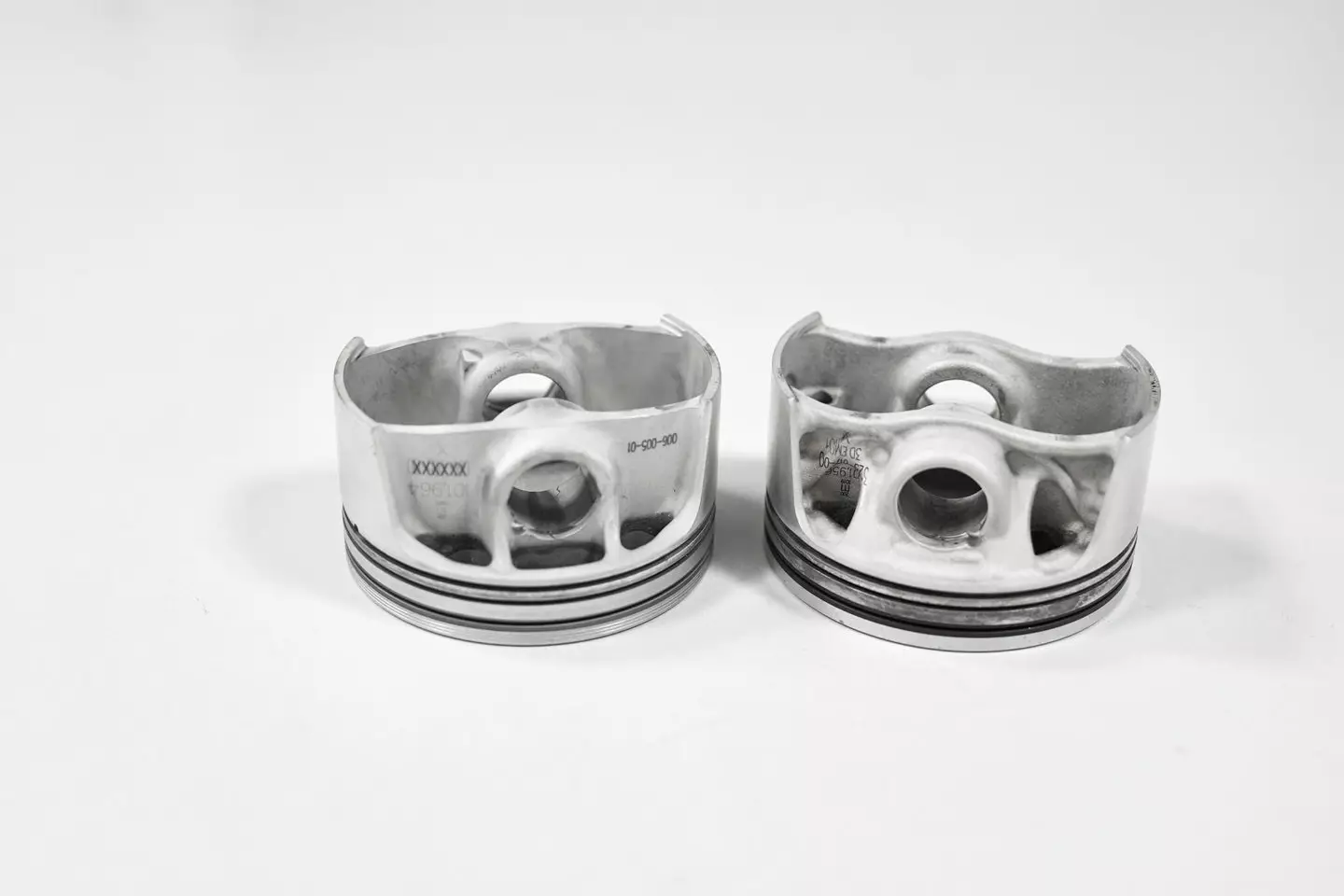
Vergleich Schmiedekolben (links) mit Druckkolben (rechts).
10 % leichter, mehr 300 U/min, mehr 30 PS
Bei gedruckten Porsche-Kolben konnte durch diese Technologie ihre Masse im Vergleich zu den Schmiedekolben des serienmäßigen 911 GT2 RS um 10 % reduziert werden, aber laut Frank Ickinger von der Porsche-Vorentwicklungsabteilung „zeigen unsere Simulationen, ein Potenzial von bis zu 20 % Gewichtseinsparung“.
Bei einem Automobil ist das Gewicht oder besser die Masse der Feind – das gleiche gilt für einen Motor. Der Kolben ist ein bewegliches Bauteil, daher bringt das Entfernen von Masse Vorteile. Da es leichter ist, gibt es weniger Trägheit, so dass im Prinzip weniger Kraftaufwand erforderlich ist, um es zu bewegen.
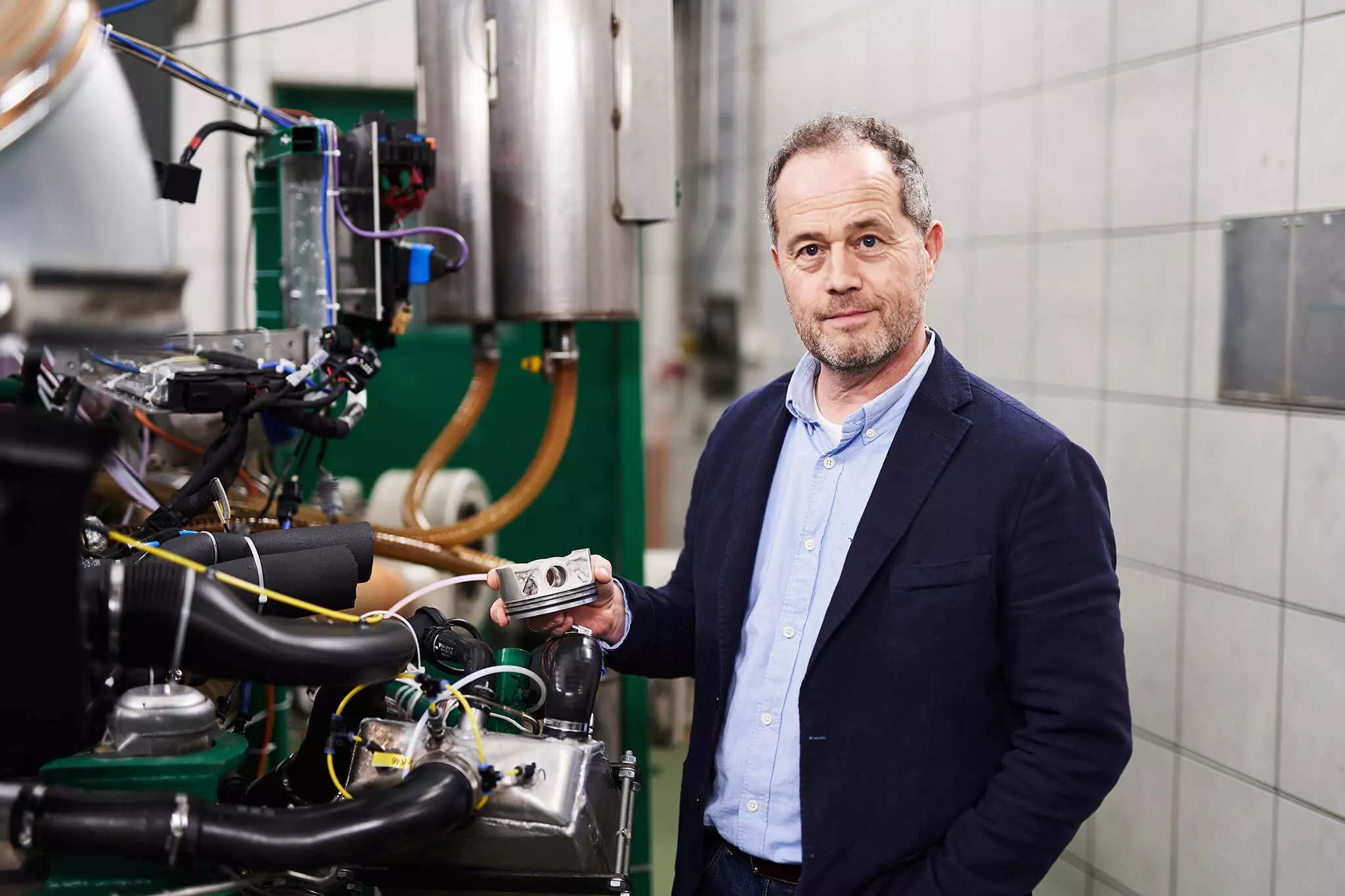
Das Ergebnis ist, dass die gedruckten Kolben von Porsche es dem 3.8 Biturbo-Sechszylinder des 911 GT2 RS ermöglichen, mit 300 U / min über dem Serienmotor zu laufen, was zu einer zusätzlichen Höchstleistung von 30 PS oder 730 PS anstelle von 700 PS führt.
Die Vorteile enden jedoch nicht mit der größeren Leichtigkeit des Kolbens. Wie bereits erwähnt, ermöglicht der 3D-Druck Wege, die mit herkömmlichen Herstellungsverfahren nicht zu erreichen sind. Bei diesen gedruckten Kolben konnte durch die Schichtfertigung ein Kühlkanal hinter den Kolbenringen angebracht werden. Es ist wie ein geschlossenes Rohr im Kolben, mit nur zwei Einlass- und Auslassöffnungen für den Ölkreislauf.
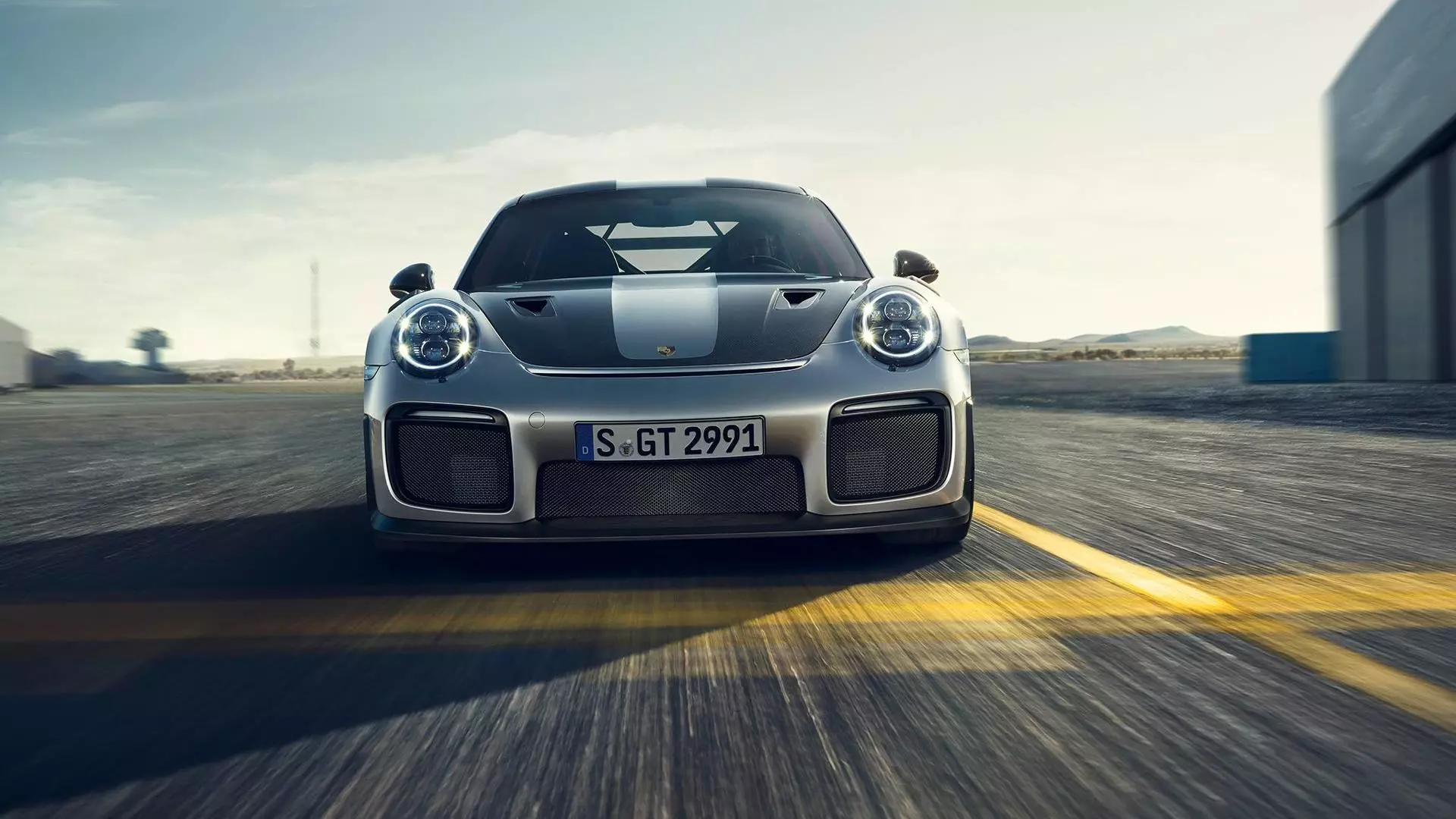
Durch diese zusätzliche Kühlung ist die Temperatur des Kolbens im Betrieb genau dort um mehr als 20°C gesunken, wo er thermisch am höchsten belastet wird. Durch eine niedrigere Betriebstemperatur des Kolbens ist es Porsche auch gelungen, die Verbrennung zu optimieren, Druck und Temperatur zu erhöhen, was zu mehr Effizienz führt. Wie Frank Ickinger es ausdrückt:
„Das ist ein gutes Beispiel dafür, dass der Verbrennungsmotor noch Zukunftspotenzial hat.“
Wie werden gedruckte Porsche-Kolben hergestellt
In Zusammenarbeit mit Mahle, das die Schmiedekolben für den 911 GT2 RS entwickelt und produziert hat, konnten sie das Metallpulver entwickeln, das als „Tinte“ zum Bedrucken der Kolben dient. Als Pulver kommt Mahles M174+ Aluminiumlegierung zum Einsatz, genauso wie die Schmiedekolben des 911 GT2 RS. Damit sind die Eigenschaften gedruckter Kolben mit denen von Schmiedekolben vergleichbar.
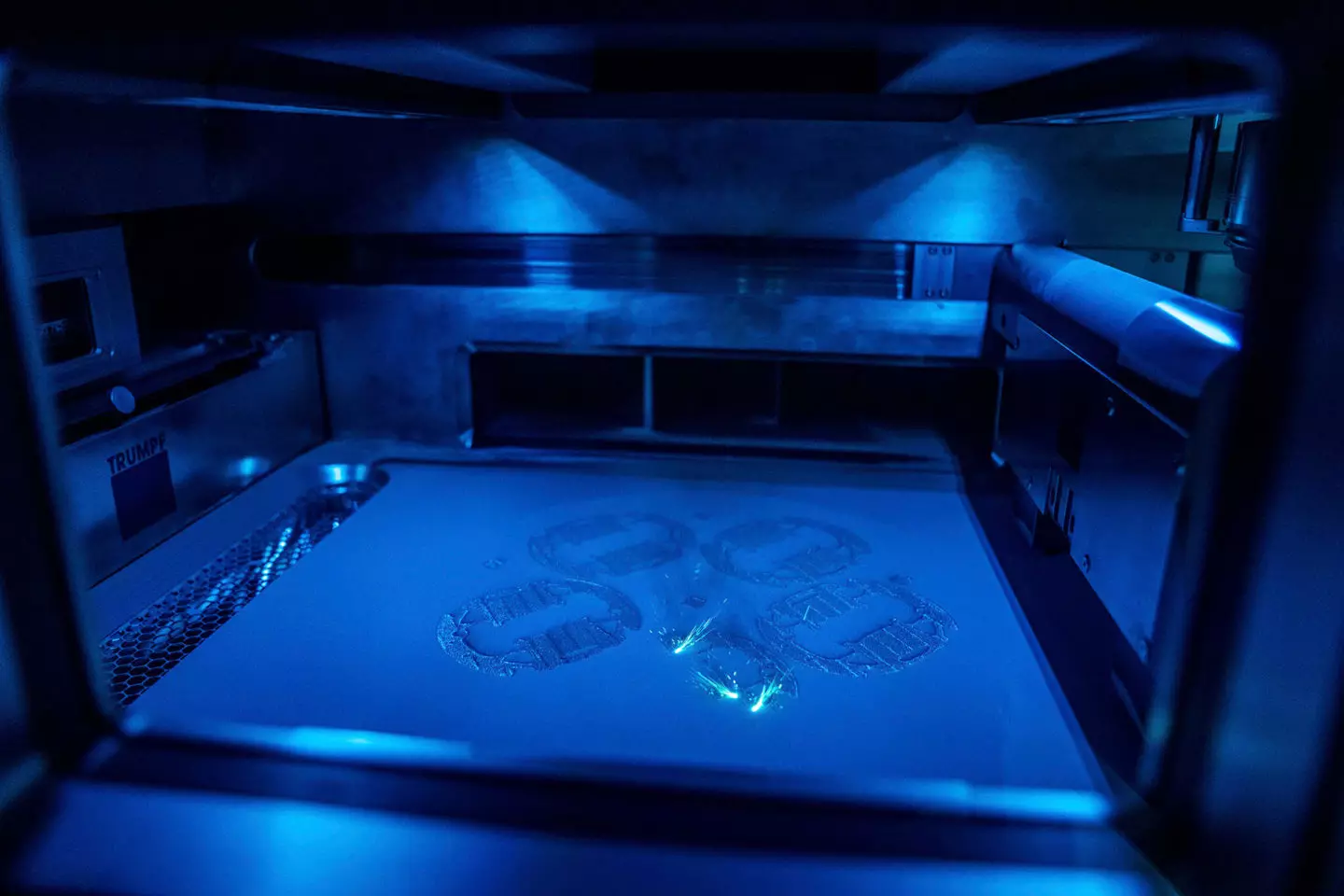
Der Laser schmilzt das Metallpulver und Schicht für Schicht nehmen die Kolben Gestalt an.
Betreten Sie Trumpf, der den Produktions- und Druckprozess entwickelt hat. Der hochpräzise 3D-Drucker Trumpf TruPrint 3000 verschmilzt das Pulver Schicht für Schicht durch einen Prozess namens LMF oder Laser Metal Fusion. Dabei wird das Pulver von einem Laserstrahl mit einer Dicke von 0,02 mm bis 0,1 mm Schicht für Schicht aufgeschmolzen.
In diesem Fall werden etwa 1200 Schichten benötigt, deren Druck etwa 12 Stunden dauert.
Die Druckmaschine von Trumpf ermöglicht das gleichzeitige Drucken von fünf Kolben und nach sorgfältiger Analyse der gedruckten Kolben in Zusammenarbeit mit Zeiss wurde bestätigt, dass sie sich nicht von geschmiedeten Kolben unterscheiden.
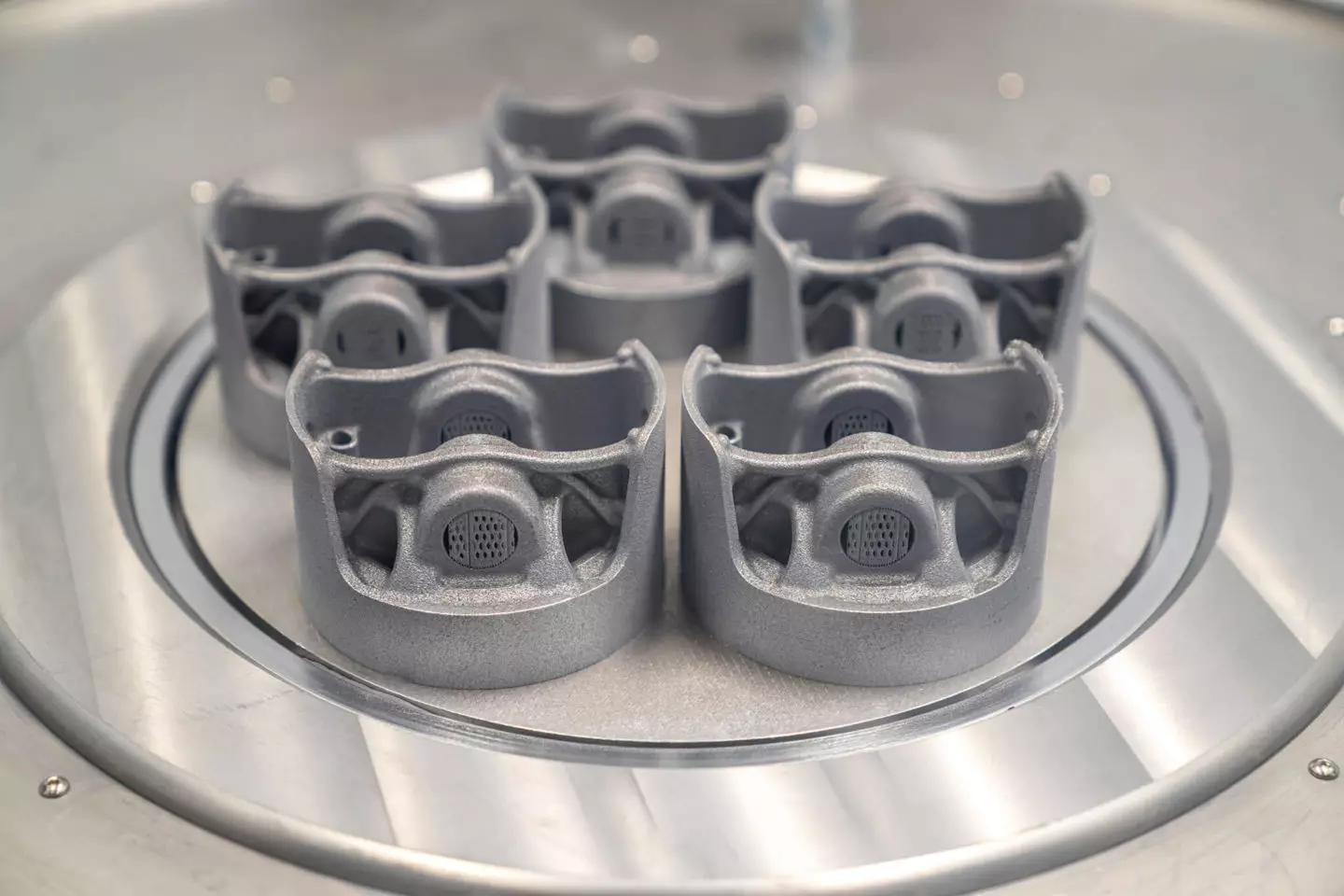
Der Drucker von Trumpf kann fünf Kolben gleichzeitig drucken.
testen, testen und testen
Nachdem sie auf den Sechszylinder-Boxer des 911 GT2 RS montiert sind, ist es an der Zeit, sie auszuprobieren. Auf einem Prüfstand wurde der Motor 200 Stunden lang einem Dauertest unterzogen.
Unter den verschiedenen durchgeführten Tests simulierte einer davon ein 24-Stunden-Rennen auf einem Hochgeschwindigkeitskurs: Er „reiste“ mit einer Durchschnittsgeschwindigkeit von 250 km/h rund 6000 km Strecke und simulierte sogar Tankstopps. Ein weiterer Test umfasste 135 Stunden bei Volllast und 25 Stunden bei unterschiedlichen Raten.
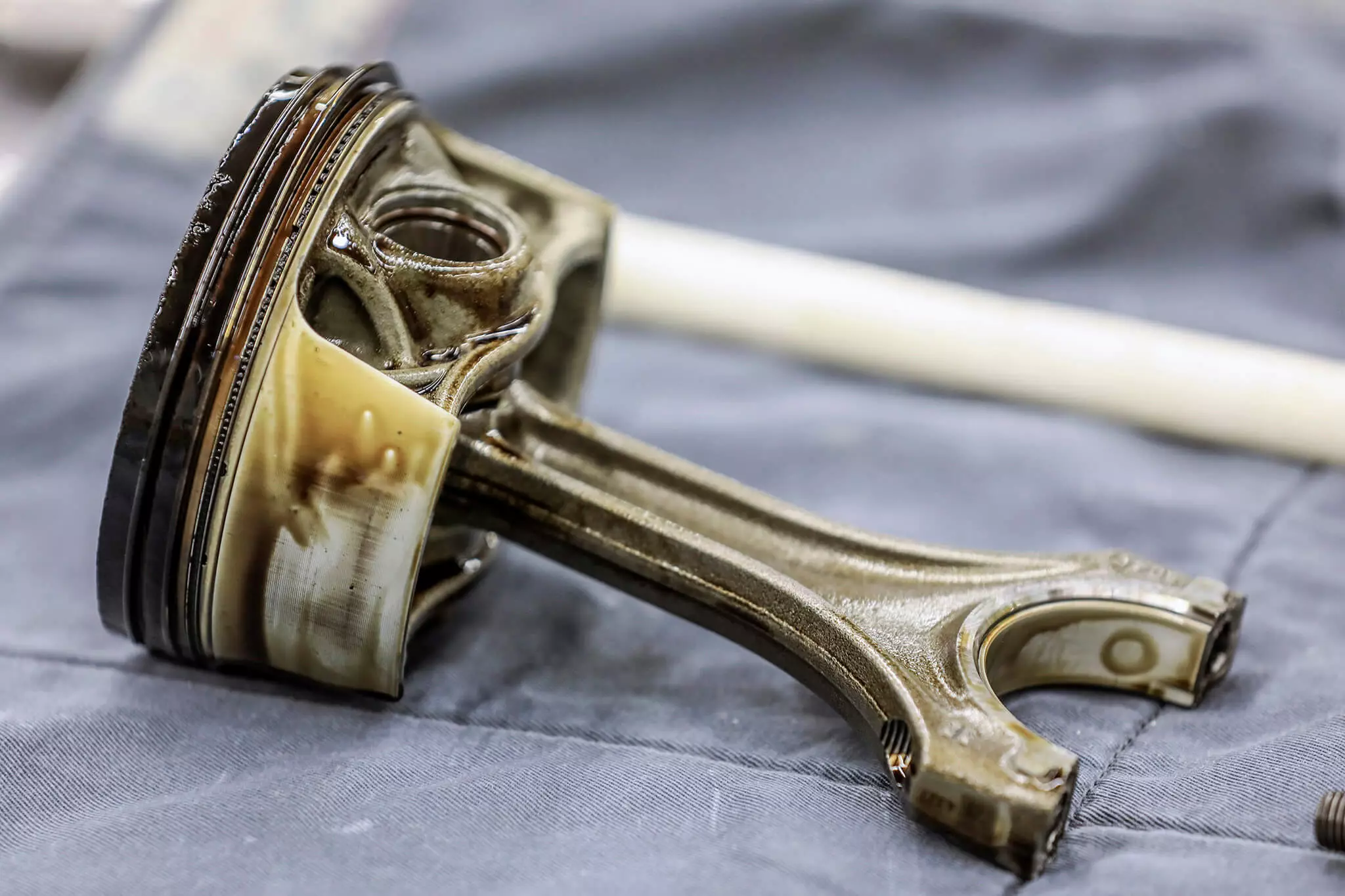
Das Ergebnis dieser harten Prüfung? Test bestanden, wobei alle gedruckten Kolben den Test bestanden haben, ohne irgendwelche Probleme zu registrieren.
Werden diese gedruckten Kolben auf den Markt kommen?
Ja, wir werden sehen, aber es gibt keinen konkreten Zeitplan. Die 3D-Drucktechnologie gibt es schon seit einigen Jahrzehnten und wird bereits in großem Umfang in der Automobilindustrie eingesetzt, aber in Wahrheit kratzt sie nur an der Oberfläche ihres Potenzials.
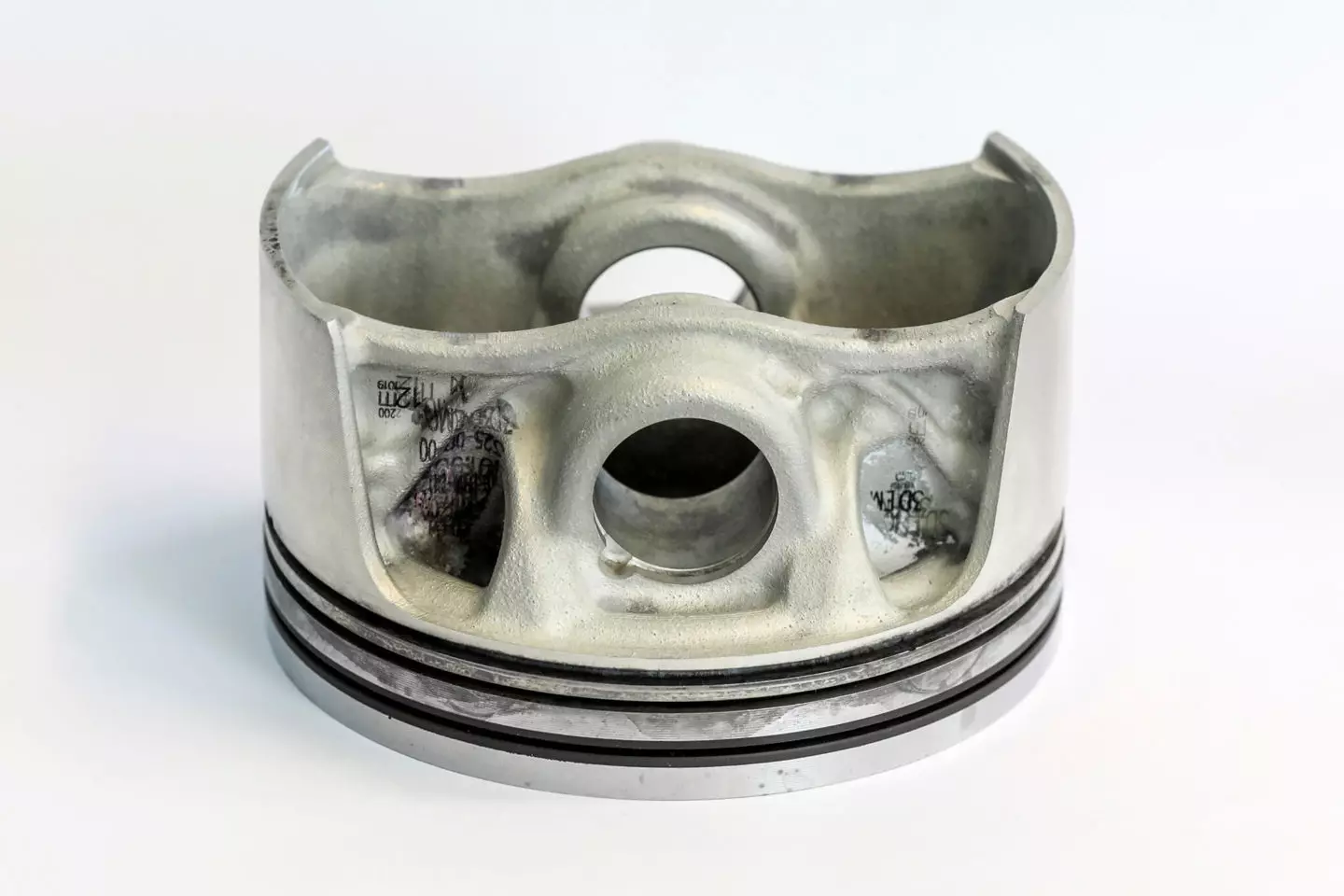
Werden wir aufgedruckte Kolben auf einem zukünftigen Porsche-Modell sehen? Sehr wahrscheinlich.
Es ist heute eine gängige Technologie im Prototyping. Es ermöglicht Ihnen, spezifische Komponenten zu erstellen und sogar verschiedene Varianten in der Komponentenkonstruktion schnell zu erkunden, ohne die Maschinen dafür entwickeln zu müssen, was eine ganze Welt von Möglichkeiten eröffnet.
Auch in anderen Bereichen setzt Porsche diese Technologie bereits ein, etwa im Wettbewerb und bei seinen Klassikern. Porsche Classic fertigt bereits 20 Teile (in Kunststoff, Stahl und anderen metallischen Legierungen) für klassische Modelle im 3D-Druck, die nicht mehr produziert wurden und sonst nicht mehr herstellbar wären.
Wir werden diese Technologie auch in Sonder- oder Kleinserienmodellen oder sogar in Form von Optionen oder Individualisierungen zum Einsatz kommen sehen – zum Beispiel ist in diesem Jahr ein Sitz im Baquet-Stil im 3D-Druck optional für den 718 und 911 erhältlich —, da sich diese Art der Fertigung als wirtschaftlich und technisch interessanter herausstellt.
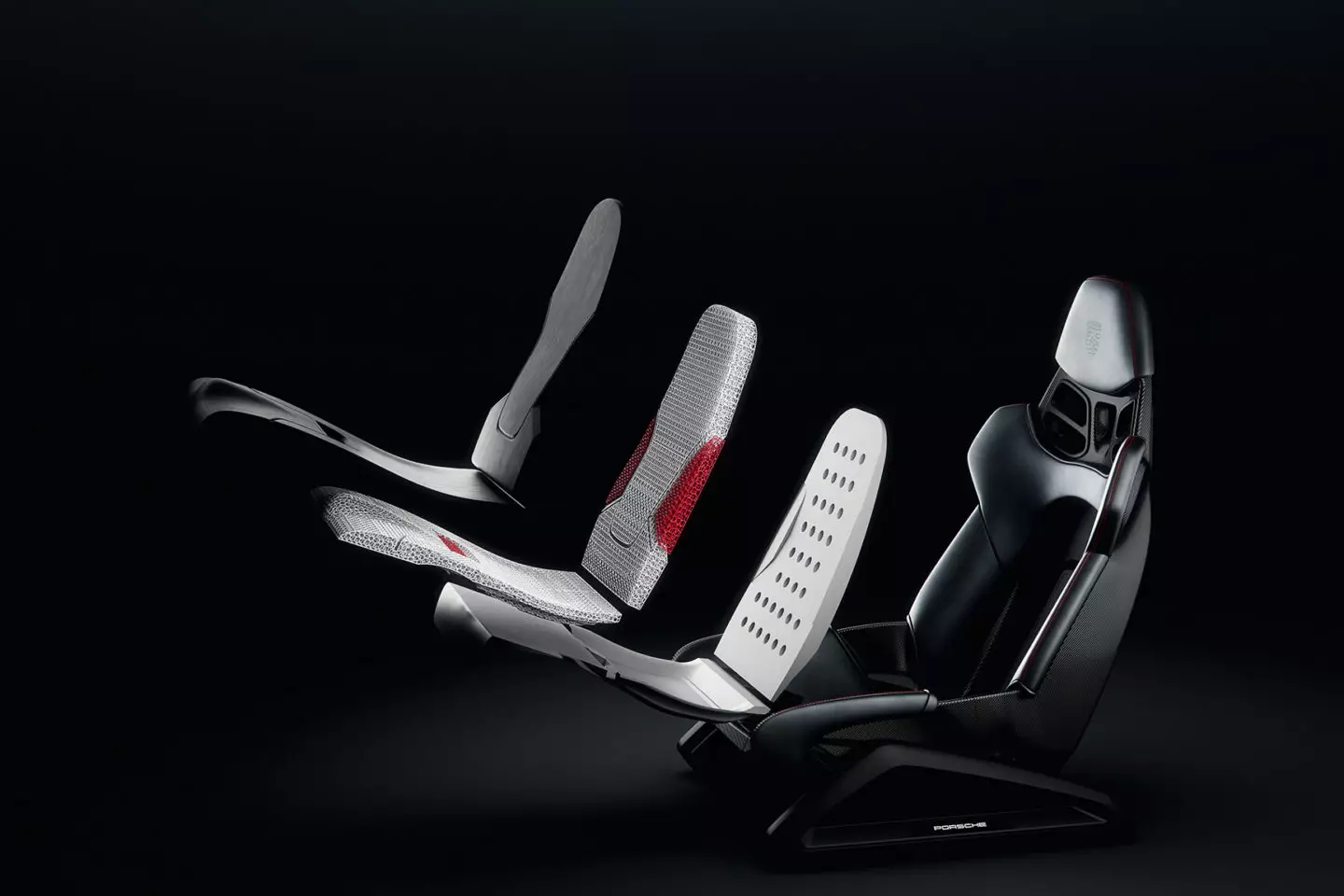
Der Prototyp der Trommelbank im 3D-Druck
Auch Porsche arbeitet daran, diese Technologie langfristig in Serienmodelle umzusetzen. Wie lange? Das haben wir Frank Ickinger gefragt, und seine Antwort, ohne absolute Sicherheit zu geben, „mindestens 10 Jahre (2030)“ – wir müssen warten, aber das Potenzial des 3D-Drucks sowie sein Störfaktor sind unbestreitbar.