L'année dernière SEAT a battu son record de ventes et de bénéfices en 70 ans d'histoire et la marque espagnole semble avoir conquis son avenir après des années de pertes.
Si 2019 s'est terminée en beauté — avec un chiffre d'affaires supérieur à 11 milliards d'euros et des bénéfices de plus de 340 millions d'euros (17,5% au-dessus de 2018), le meilleur résultat de tous les temps — l'année 2020 a commencé avec moins de motifs de festivités.
Non seulement le PDG de SEAT, Luca De Meo, s'est lancé dans la compétition (Renault) mais - principalement - la pandémie a freiné les années successives d'amélioration de tous les types d'indicateurs économiques, comme cela s'est produit dans la grande majorité des secteurs d'activité et entreprises du monde entier.
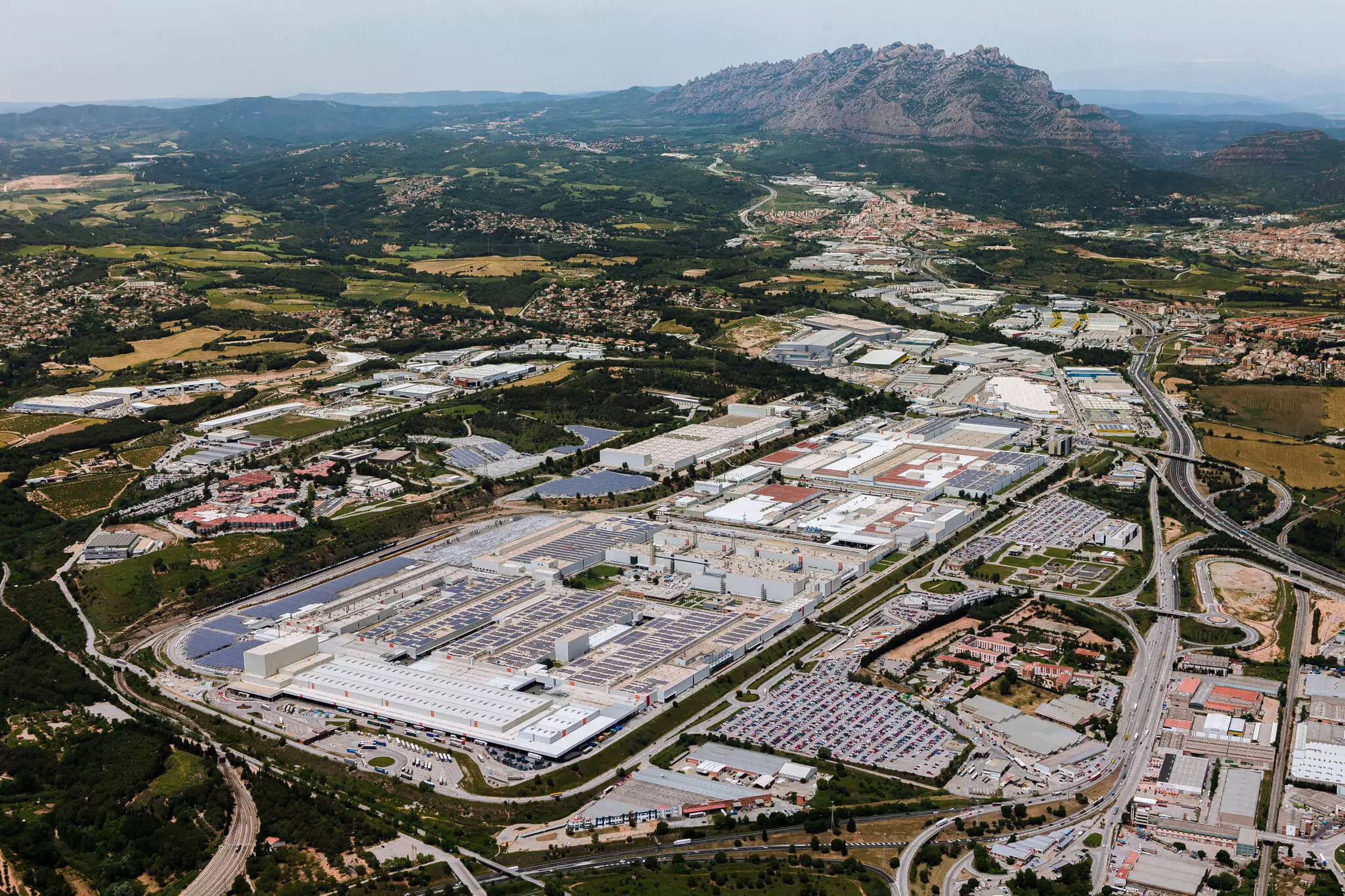
La récente série de croissance annuelle des ventes de la marque espagnole (de 400 000 en 2015 à 574 000 en 2019, soit 43 % de plus en seulement quatre ans) sera donc stoppée cette année.
11 millions de voitures fabriquées
L'usine de Martorell a été inaugurée en 1993, après avoir été construite en seulement 34 mois (et ayant nécessité, à l'époque, un investissement de 244,5 millions de pesetas, soit l'équivalent de 1470 millions d'euros) et en 27 ans, elle a produit environ 11 millions de véhicules, répartis en 40 modèles ou dérivés.
Depuis lors, beaucoup de choses ont changé, la surface de l'ensemble du complexe industriel ayant été multipliée par sept pour atteindre les 2,8 millions de mètres carrés actuels, où (juste pour vous aider à visualiser) 400 terrains de football pourraient tenir.
Abonnez-vous à notre newsletter
Et c'est loin d'être le seul centre de production de la marque espagnole dans ce domaine. Dans la Zone Franche au pied de la ville (où la fabrication automobile de l'entreprise a débuté en 1953 et jusqu'en 1993) diverses pièces sont pressées (portes, toits, garde-boue, totalisant plus de 55 millions pour 20 usines) de plusieurs marques du Groupe Volkswagen uniquement. en 2019) ; il existe un autre centre de production de composants (dont 560 000 boîtes de vitesses sont sorties l'an dernier) en périphérie de l'aéroport, à Prat de Llobregat ; en plus d'un Centre Technique (depuis 1975 et où travaillent aujourd'hui plus de 1100 ingénieurs).
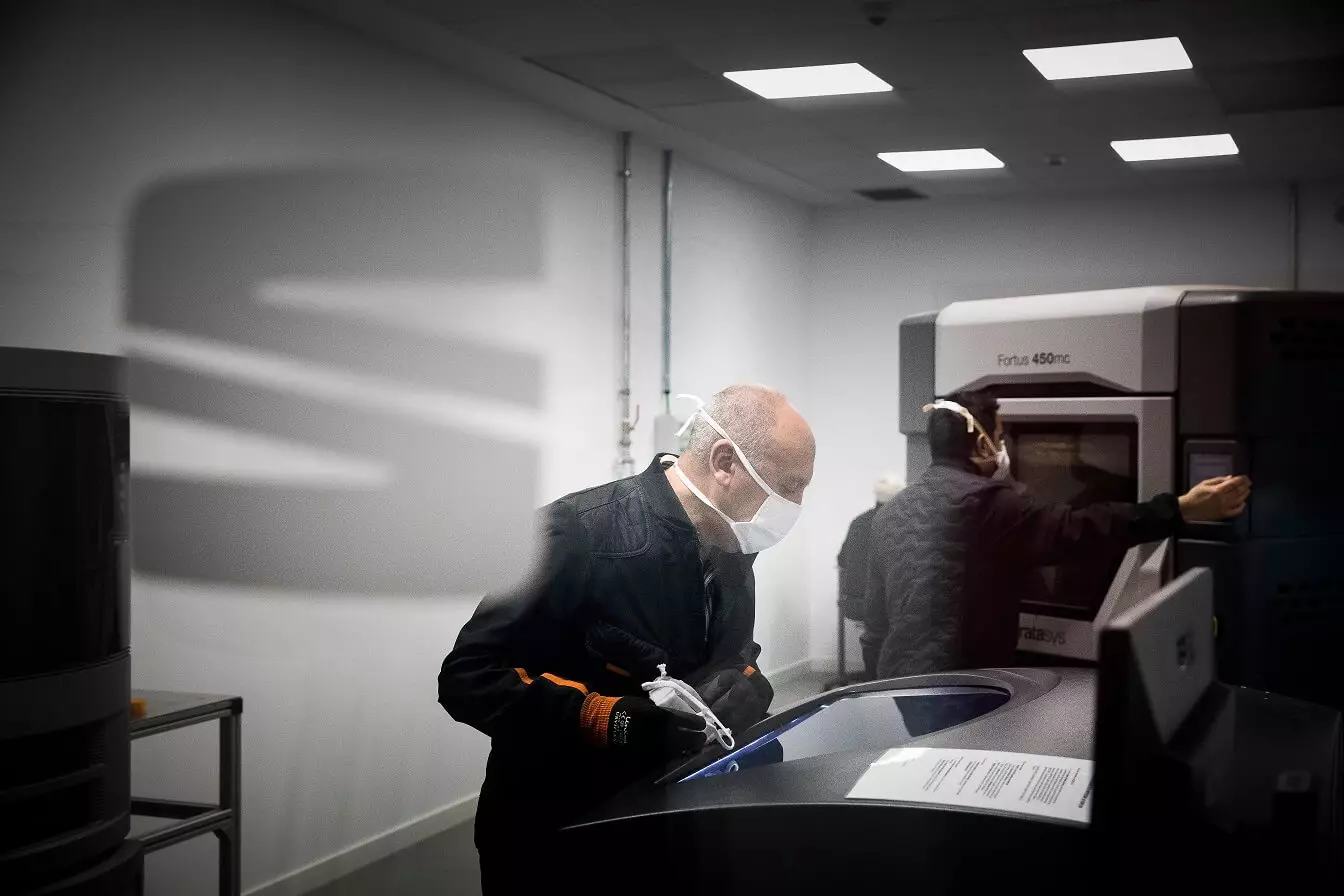
Centre d'impression 3D
Cela signifie que SEAT est l'une des rares entreprises du pays à concevoir, développer techniquement et fabriquer ses produits en Espagne. Et, dans la région et associé à SEAT, il y a aussi un immense centre logistique, un centre d'impression 3D (récemment neuf et dans l'usine elle-même) et un Digital Lab (à Barcelone) où l'on pense l'avenir de la mobilité humaine (avec d'importants intégration d'étudiants universitaires qui suivent également une formation continue à l'usine, dans le cadre d'un protocole avec l'Université polytechnique de Catalogne).
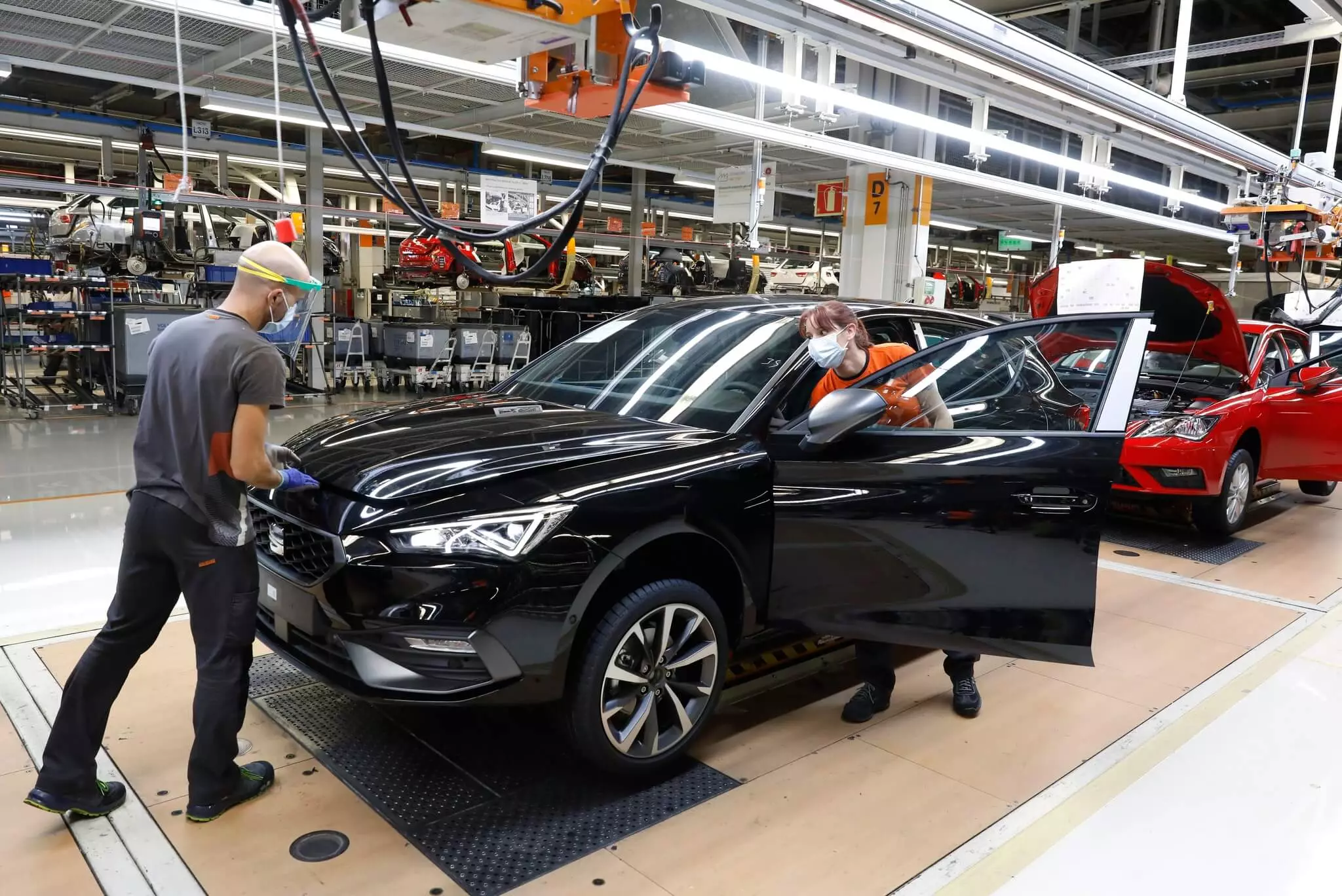
27 ans changent tout
A ses débuts, en 1993, Martorell terminait 1500 voitures par jour, aujourd'hui il y en a 2300 qui roulent « de son propre pied », c'est-à-dire une nouvelle voiture prête à être expédiée à un client impatient toutes les 30 secondes.
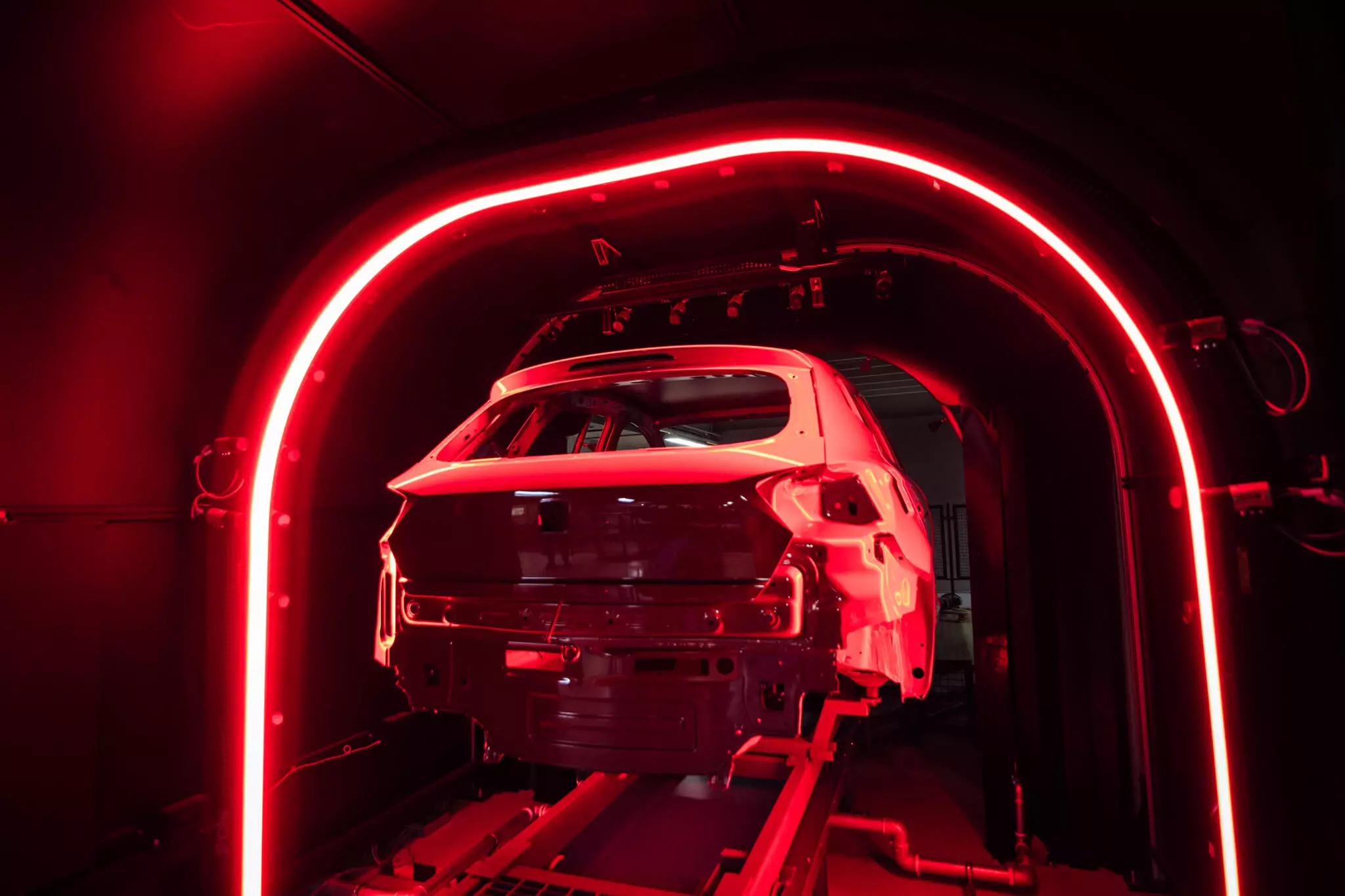
De 60 heures à 22 heures pour créer une nouvelle voiture : aujourd'hui, 84 robots appliquent de fines couches de peinture dans une cabine de peinture et un scanner de pointe inspecte le lissé de la surface en seulement 43 secondes. La réalité virtuelle, l'impression 3D et la réalité augmentée sont d'autres innovations apparues avec l'arrivée de l'Industrie 4.0.
Juan Pérez, responsable des processus d'impressionJe n'avais que 18 ans lorsque je suis entré pour la première fois dans l'usine de Martorell et je me souviens de l'ambiance euphorique de la ville qui venait d'accueillir les Jeux Olympiques. Il était apprenti et mes collègues et moi avions de grands espoirs pour l'avenir : tout était nouveau et on nous a dit que c'était l'usine la plus moderne d'Europe.
C'est ainsi que Juan Pérez, qui dirige actuellement les processus d'impression, se souvient de ces premiers jours, il y a 27 ans, à l'usine de Martorell, où les employés parcouraient 10 km par jour : « Quand je rentrais chez moi, je ne trouvais même pas le casier pièce. C'était très facile de se perdre ».
Aujourd'hui, il existe des véhicules autonomes, qui aident les employés à transporter environ 25 000 pièces par jour jusqu'à la ligne, en plus de 10,5 km de voies ferrées et 51 lignes de bus.
Un Portugais mène la Qualité
Les progrès qualitatifs constants, même ces derniers temps, sont tout aussi ou plus importants, comme le montrent les derniers indicateurs : entre 2014 et 2018, le nombre de plaintes des propriétaires de modèles de marque espagnole a chuté de 48% et Martorell est pratiquement au niveau des records de qualité / fiabilité de l'usine mère de Volkswagen à Wolfsburg.
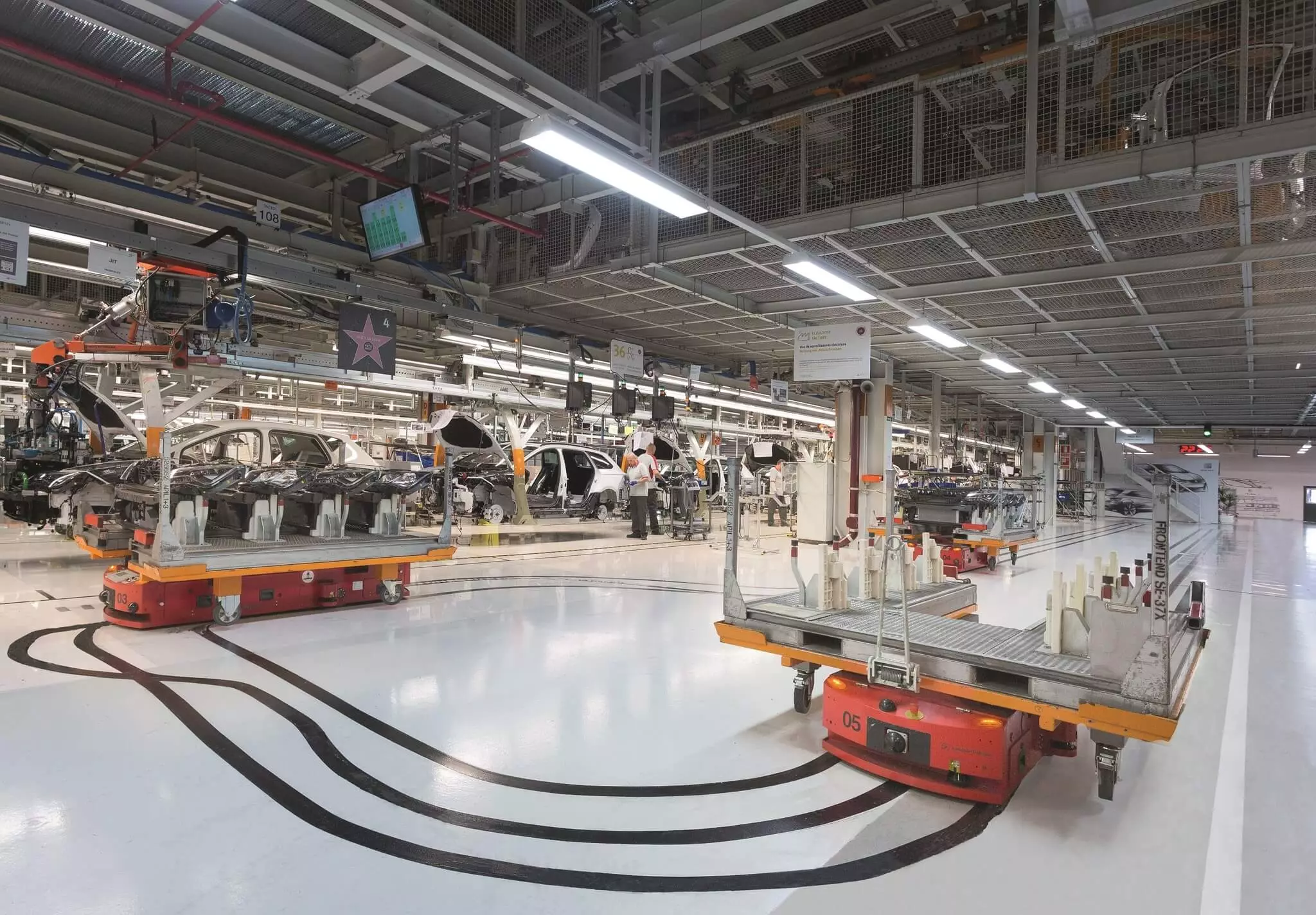
Cela ne devrait pas être surprenant étant donné que les mêmes processus industriels sont suivis de A à Z, comme le confirme José Machado, le Portugais qui dirige désormais le contrôle qualité à Martorell, après avoir débuté chez Autoeuropa (à Palmela), d'où il s'est rendu à Puebla ( Mexique), pour assumer cette position importante dans le berceau de presque tous les SEAT :
José Machado, directeur du contrôle qualitéNous suivons tous le même guide et c'est ce qui compte, car au final nos 11 000 collaborateurs – directs et indirects – comprennent 67 nationalités et 26 langues différentes.
80% sont des hommes, 80% ont moins de 50 ans, sont dans l'entreprise depuis 16,2 ans en moyenne et 98% ont un contrat de travail à durée indéterminée, ce qui contribue à créer une stabilité chez les personnes, qui se reflète ensuite dans la qualité de leur travail.
Léon est celui qui fabrique et vend le plus
Aussi fier voire plus fier de ce qui se fait ici, Ramón Casas – directeur de la section Montage et revêtement intérieur – est le principal guide de cette visite, qui se concentre sur ce domaine dont il est principalement responsable : « nous avons trois lignes au total, 1 vient d'Ibiza/Arona (qui achève 750 voitures/jour), 2 de Léon et Formentor (900) et 3 d'une Audi A1 exclusive (500) ».
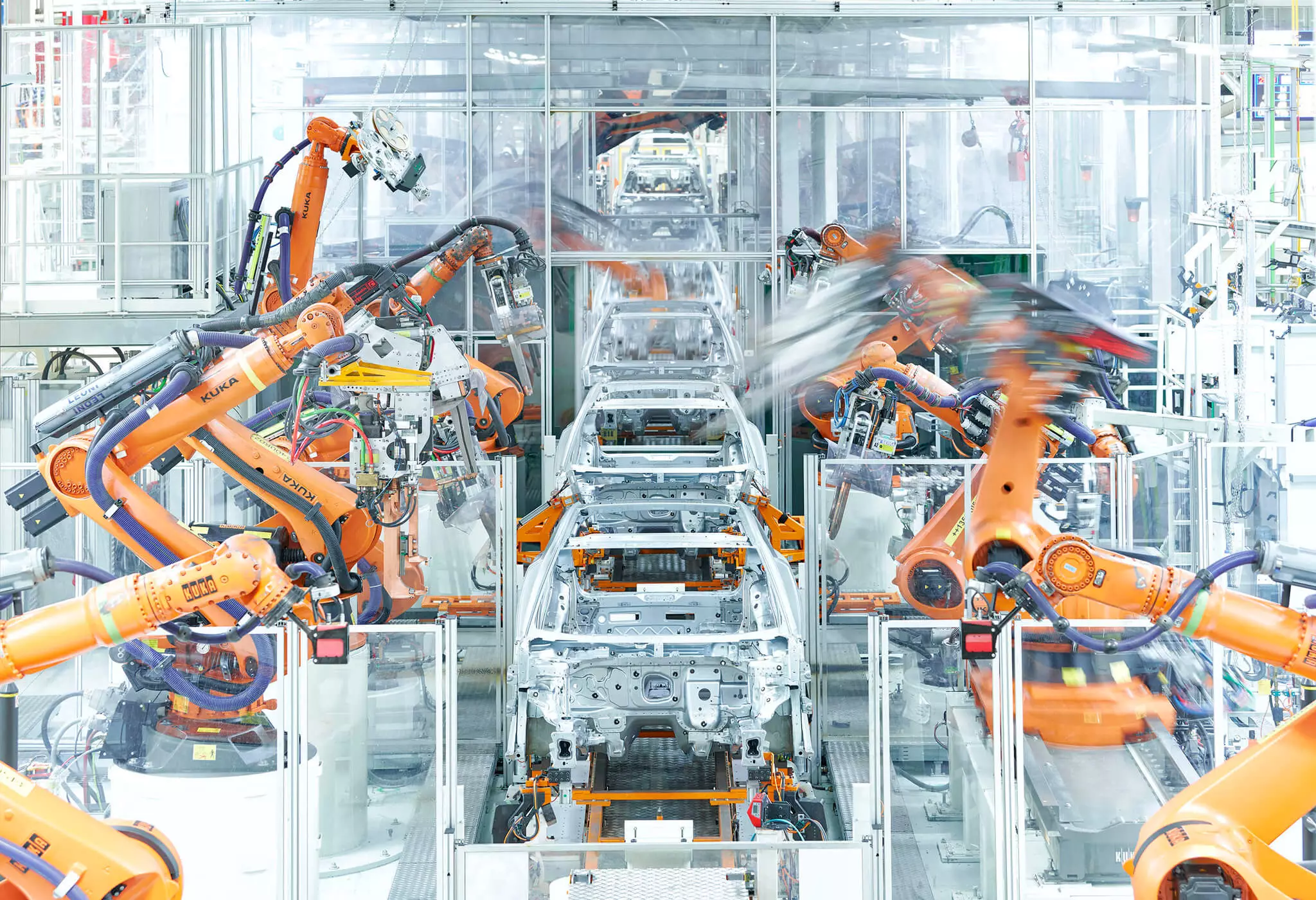
Dans ce cas, nous sommes dans le berceau de Leon et dérivés car cette visite a été effectuée en plus d'un déplacement à l'usine pour récupérer le fourgon Leon Sportstourer avant qu'il n'arrive, par les canaux habituels, sur le marché portugais.
Casas explique que « cette ligne 2 est celle qui fabrique le plus de voitures car la Leon est la SEAT la plus vendue au monde (environ 150 000/an) un peu plus élevée que les Ibiza et Arona (environ 130 000 chacune) et maintenant que le SUV Formentor a rejoint cette chaîne de montage, la capacité de production sera très proche de l'épuisement ».
Les 500 005 voitures fabriquées à Martorell en 2019 (dont 81 000 Audi A1), soit 5,4% de plus qu'en 2018, ont utilisé 90% de la capacité installée de l'usine, l'un des taux les plus élevés de toute l'Europe et un indicateur très positif de la santé financière de l'entreprise.
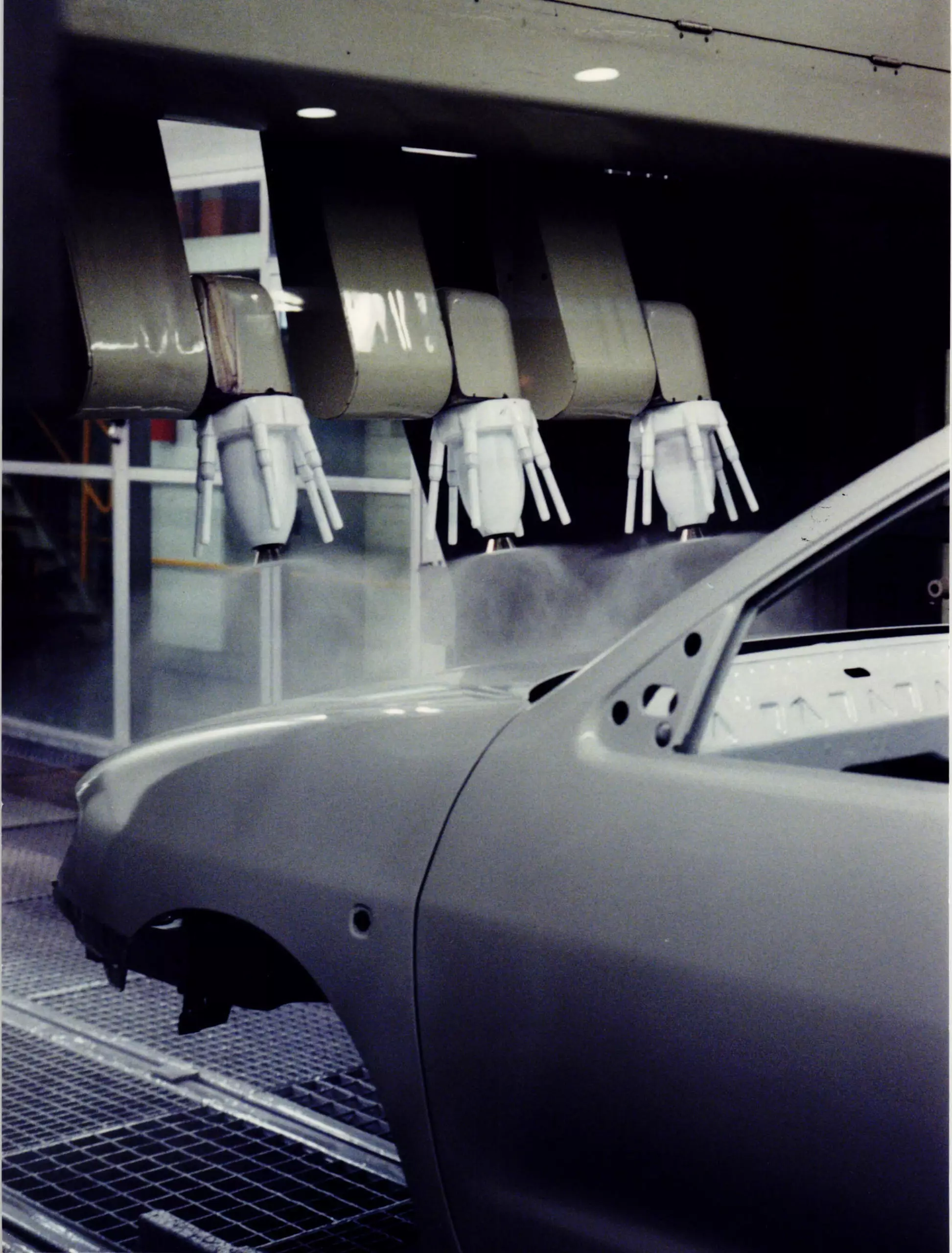
La marque espagnole a cependant enregistré des ventes supérieures aux 420 000 SEAT produites à Martorell l'an dernier, car certains de ses modèles sont fabriqués hors d'Espagne : l'Ateca en République tchèque (Kvasiny), la Tarraco en Allemagne (Wolfsburg), la Mii en Slovaquie (Bratislava) et l'Alhambra au Portugal (Palmela).
Au total, SEAT a produit 592 000 voitures en 2019, avec l'Allemagne, l'Espagne et le Royaume-Uni comme principaux marchés, dans cet ordre (80 % de la production est destinée à être exportée vers environ 80 pays différents).
22 heures pour fabriquer une SEAT Leon
Je poursuis mon parcours sur une partie des 17 km de voies avec des rails électrifiés, puis des carrosseries suspendues et des bases roulantes avec des moteurs/boîtes déjà montés (que l'on retrouvera plus tard dans ce que les usines appellent « Mariage »), tandis que les deux guides fournissent davantage détails : il y a trois zones principales dans chacune des lignes d'assemblage, Carrosserie, Peinture et Assemblage, "mais la dernière est celle où les voitures passent le plus de temps", s'empressa-t-il d'ajouter Ramón Casas, ou si ce n'était pas ça aussi le un sous sa responsabilité directe.
Sur un total de 22 heures qu'il faut à chaque Leon pour être produit, il reste 11:45min en Assemblage, 6:10min en Carrosserie, 2:45min en Peinture et 1:20min en Finition et Vérification Finale.

Les directeurs d'usine sont très fiers de pouvoir changer de génération de modèle sans avoir à interrompre la chaîne d'assemblage. « Même avec des voies plus larges et un empattement différent, nous avons pu intégrer la production de la nouvelle Leon sans avoir à arrêter la production de la génération précédente », souligne Casas, pour qui il existe d'autres défis plus délicats :
Ramón Casas, directeur de la section Montage et revêtement intérieurla précédente Leon avait 40 unités de traitement électronique, la nouvelle en a au moins le double et si l'on considère l'hybride rechargeable on parle de 140 ! Et ils doivent tous être testés avant d'être installés.
L'enchaînement des pièces est également compliqué pour que la configuration de la voiture suive exactement ce qui a été commandé. Rien que dans le cas de la face avant de la Leon, il peut y avoir 500 variantes, ce qui donne une idée de la difficulté de la tâche.
José Machado explique également qu'« il n'y a pas de décalage horaire entre la production d'une Leon cinq portes ou d'un Sportstourer van et le fait que ce dernier ait gagné en popularité ces dernières années – 40 % des ventes contre 60 % de la cinq portes – n'a pas affecté la chaîne de montage ».

Des drones et des robots pour aider...
À Martorell, il existe plus d'un type de robot. Il y a ceux qui livrent entre les différentes zones du gigantesque complexe industriel (comme les drones et les véhicules terrestres automatisés, au total 170 à l'intérieur et à l'extérieur de l'usine) puis les robots qui aident à assembler les voitures elles-mêmes.
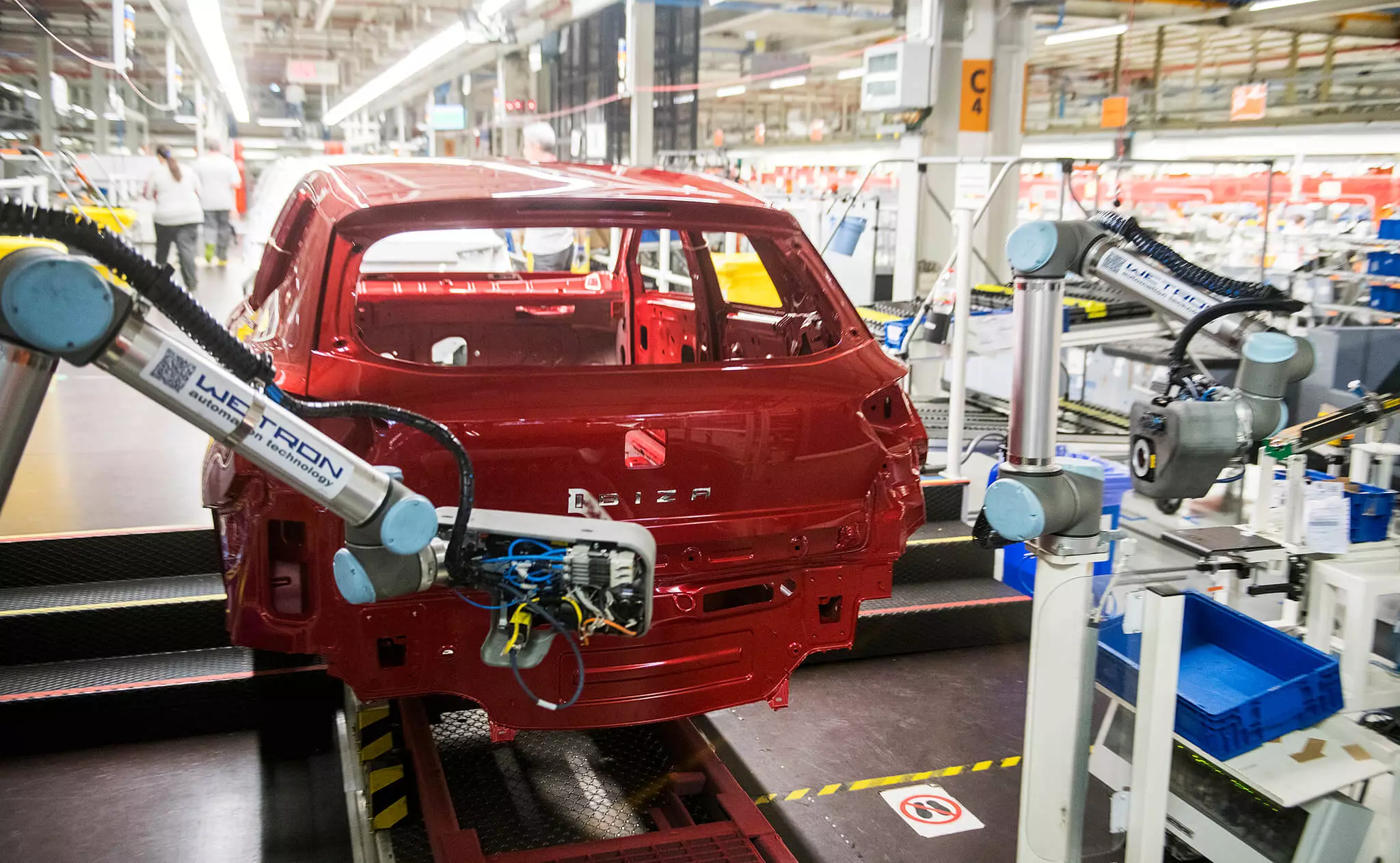
Machado précise qu'« il existe différents taux de robotisation selon la zone de la chaîne de montage, avec environ 15 % dans la zone d'assemblage, 92 % dans le placage et 95 % dans la peinture ». Dans la zone d'assemblage, de nombreux robots aident les employés à prendre des pièces plus lourdes, comme les portes (pouvant atteindre 35 kg) et à les faire pivoter avant de les insérer dans la carrosserie.
…mais c'est l'être humain qui fait la différence
Le responsable Qualité de Martorell souligne également l'importance de l'équipe humaine au sein de cette unité industrielle :
José Machado, directeur du contrôle qualité.Ce sont eux qui donnent le signal en cas de problème dans la chaîne de montage, en appelant le superviseur qui essaie de résoudre le problème avec la ligne en cours, en faisant tout pour que cela ne s'arrête pas. Ils changent de rôle toutes les deux heures pour éviter une routine excessive et aussi pour les motiver davantage, donnant même des idées pour rendre l'ensemble du processus plus productif. Et si l'une des suggestions est appliquée, ils finissent par recevoir un pourcentage de ce que l'usine a économisé avec ce changement.
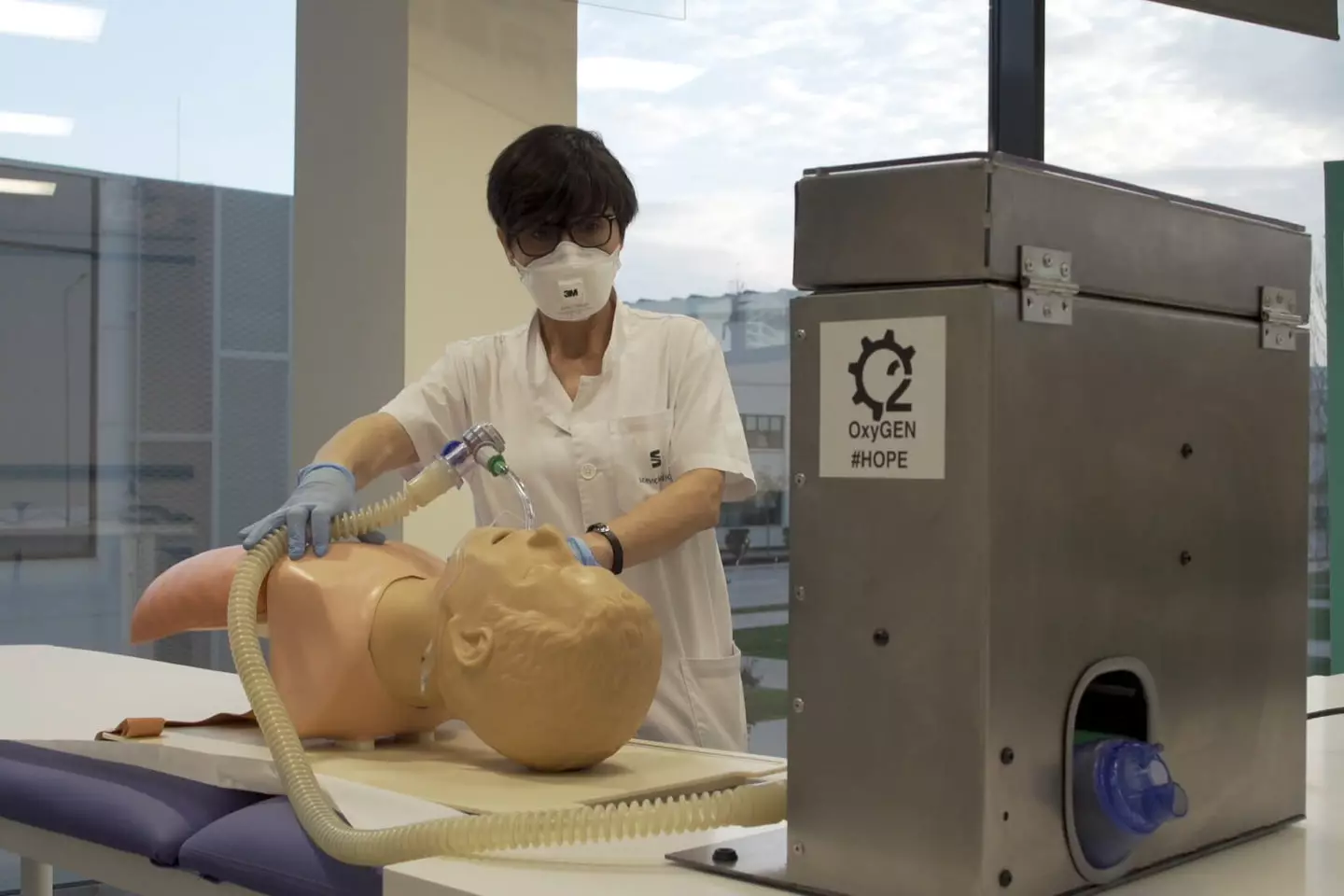
SEAT a rapidement commencé à produire des fans dans la lutte contre Covid-19.
Martorell a été fermée pendant la phase la plus grave de la propagation du covid-19, comme m'explique Ramón Casas :
Ramón Casas, directeur de la section Montage et revêtement intérieurNous sommes tous rentrés chez nous fin février, le 3 avril nous avons commencé la production de fans et sommes retournés au travail le 27 avril, faisant progressivement des tests de virus sur tous les employés. Le port du masque est obligatoire pendant toute la durée du séjour à l'usine, il y a du gel partout et de nombreuses protections acryliques dans les espaces de repos, cafétéria, etc.