Afgelopen jaar SEAT verslaat zijn verkoop- en winstrecord in 70 jaar geschiedenis en het Spaanse merk lijkt zijn toekomst te hebben veroverd na jaren van verliezen.
Als 2019 op een hoogtepunt eindigde - met een omzet van meer dan 11 miljard euro en winst van meer dan 340 miljoen euro (17,5% boven 2018), het beste resultaat ooit - begon 2020 met minder redenen tot feest.
Niet alleen de CEO van SEAT, Luca De Meo, ging de concurrentie aan (Renault), maar - vooral - de pandemie zette een rem op de opeenvolgende jaren van verbetering van alle soorten economische indicatoren, zoals gebeurde in de overgrote meerderheid van de activiteitensectoren en bedrijven over de hele wereld.
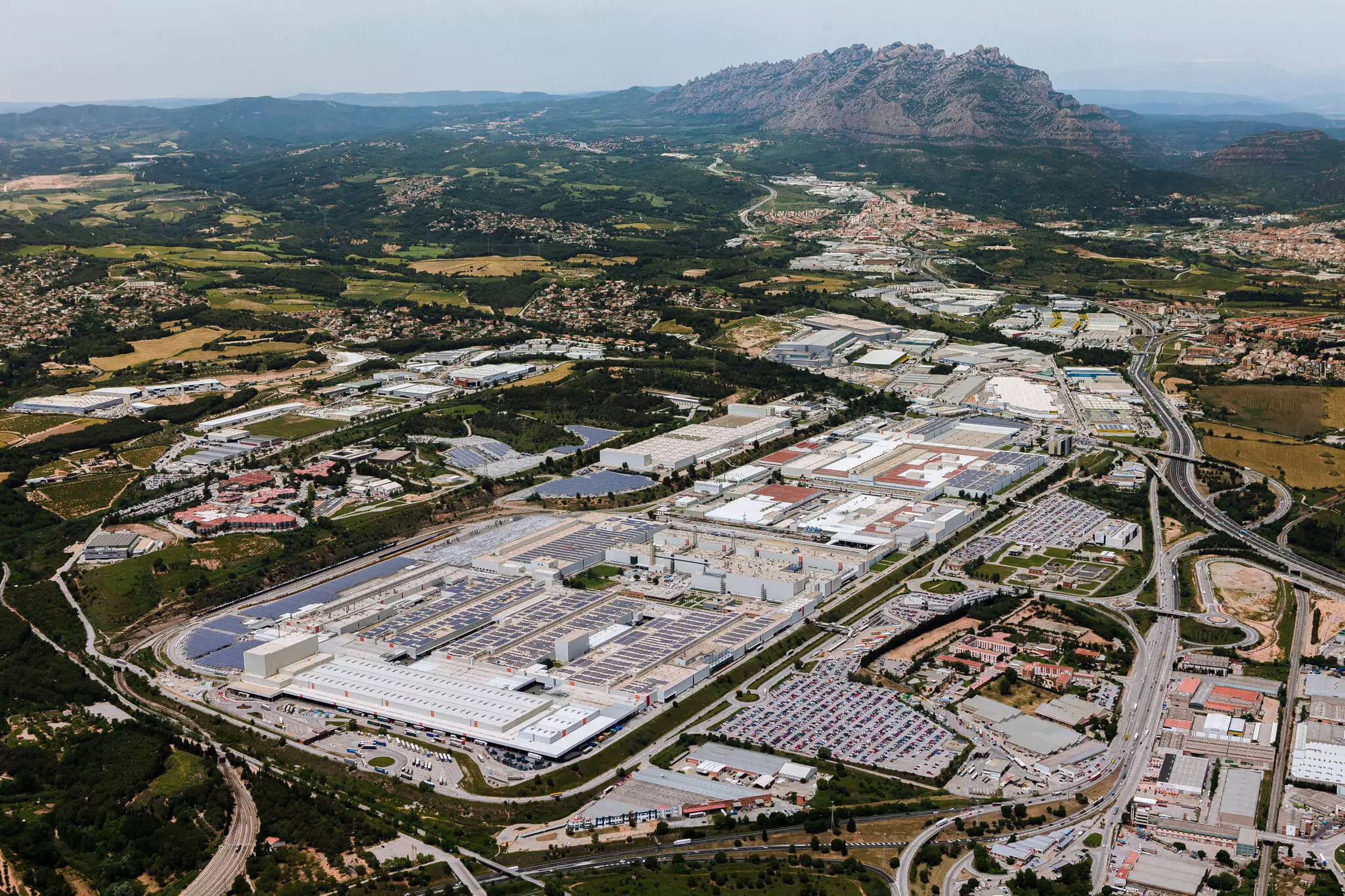
De recente reeks jaar-op-jaar omzetgroei voor het Spaanse merk (van 400.000 in 2015 naar 574.000 in 2019, 43% meer in slechts vier jaar) wordt daarom dit jaar stopgezet.
11 miljoen geproduceerde auto's
De Martorell-fabriek werd in 1993 ingehuldigd, na te zijn gebouwd in slechts 34 maanden (en toen een investering van 244,5 miljoen peseta's, wat overeenkomt met 1470 miljoen euro) en in 27 jaar produceerde het ongeveer 11 miljoen voertuigen, verdeeld over 40 modellen of afgeleiden.
Sindsdien is er veel veranderd, waarbij de oppervlakte van het hele industriële complex zeven keer is toegenomen tot de huidige 2,8 miljoen vierkante meter, waar (om je te helpen visualiseren) 400 voetbalvelden zouden passen.
Abonneer op onze nieuwsbrief
En het is verre van het enige productiecentrum voor het Spaanse merk in dit gebied. In de Free Zone aan de voet van de stad (waar de autoproductie van het bedrijf begon in 1953 en tot 1993) worden verschillende onderdelen geperst (deuren, daken, spatborden, in totaal meer dan 55 miljoen voor 20 fabrieken). in 2019); er is nog een productiecentrum voor componenten (waarvan vorig jaar 560.000 versnellingsbakken uitkwamen) aan de rand van de luchthaven, in Prat de Llobregat; naast een Technisch Centrum (sinds 1975 en waar vandaag meer dan 1100 ingenieurs werken).
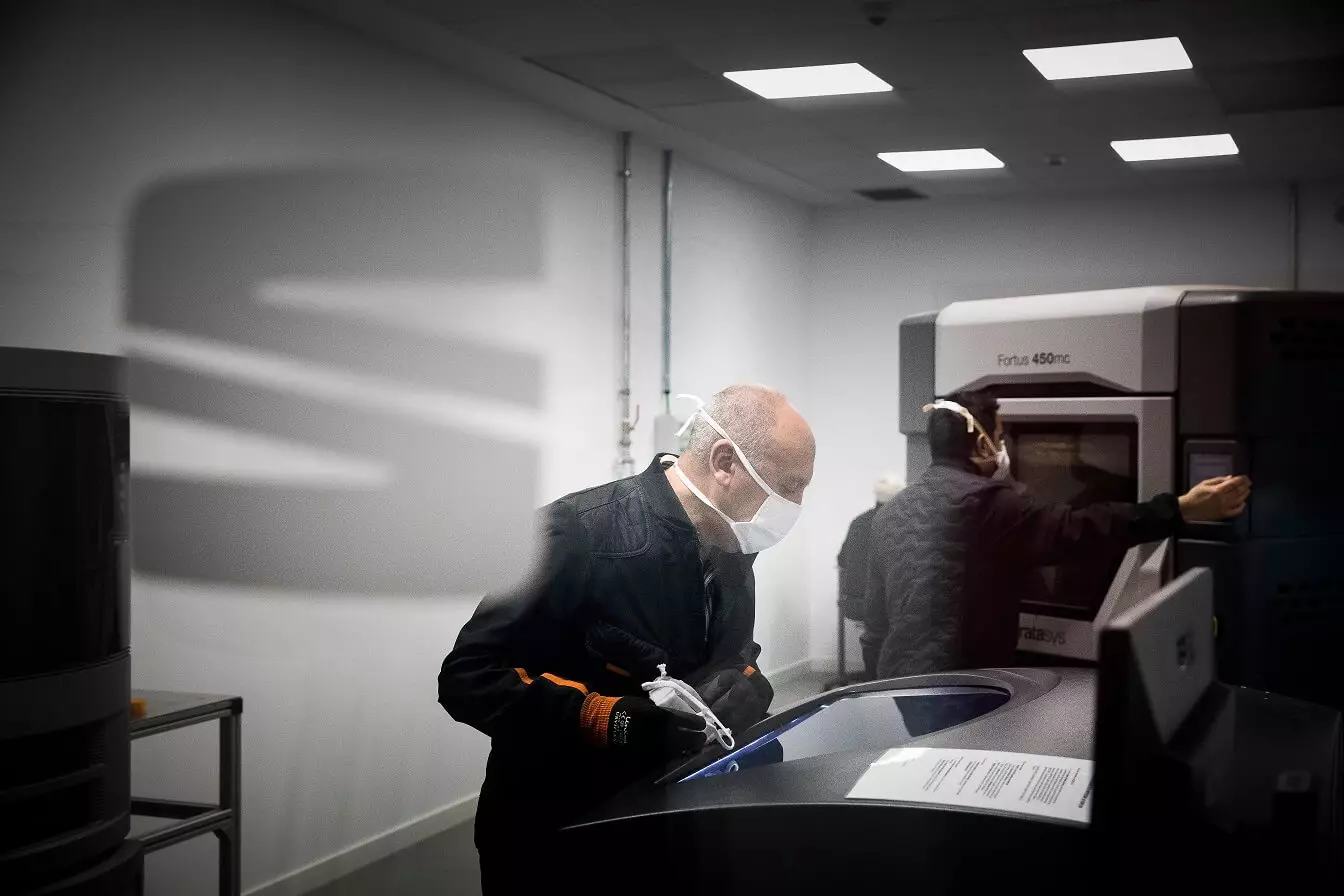
3D-printcentrum
Dit betekent dat SEAT een van de weinige bedrijven in het land is die zijn producten in Spanje ontwerpt, technisch ontwikkelt en produceert. En in de regio en geassocieerd met SEAT is er ook een enorm logistiek centrum, een 3D-printcentrum (onlangs nieuw en in de fabriek zelf) en een Digital Lab (in Barcelona) waar wordt nagedacht over de toekomst van menselijke mobiliteit (met belangrijke integratie van universiteitsstudenten die ook voortdurend worden bijgeschoold in de fabriek, volgens een protocol met de Polytechnische Universiteit van Catalonië).
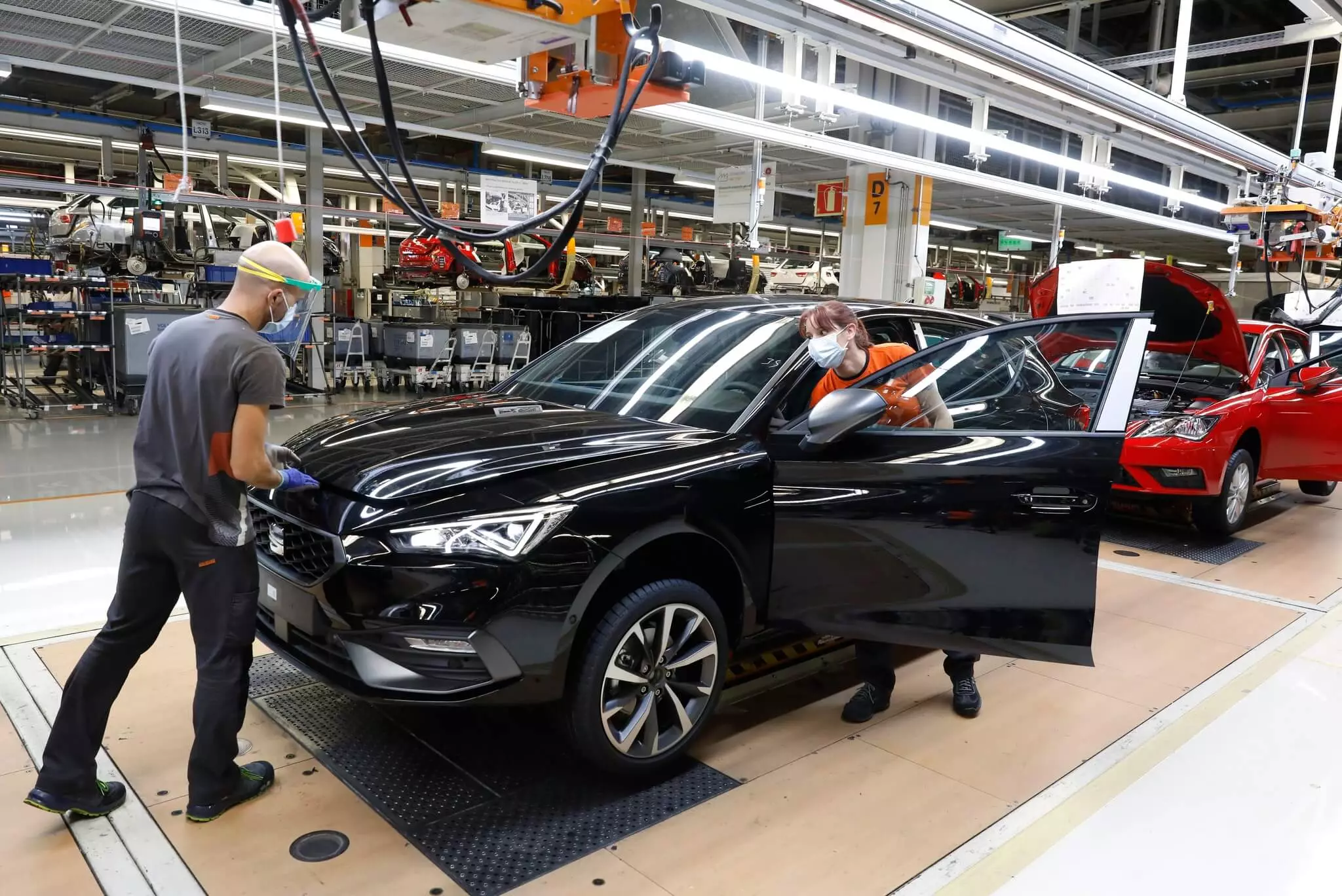
27 jaar verandert alles
Bij de start, in 1993, voltooide Martorell 1500 auto's per dag, vandaag zijn er 2300 die "op eigen voet" rollen, wat betekent elke 30 seconden een nieuwe auto klaar om naar een enthousiaste klant te worden verzonden.
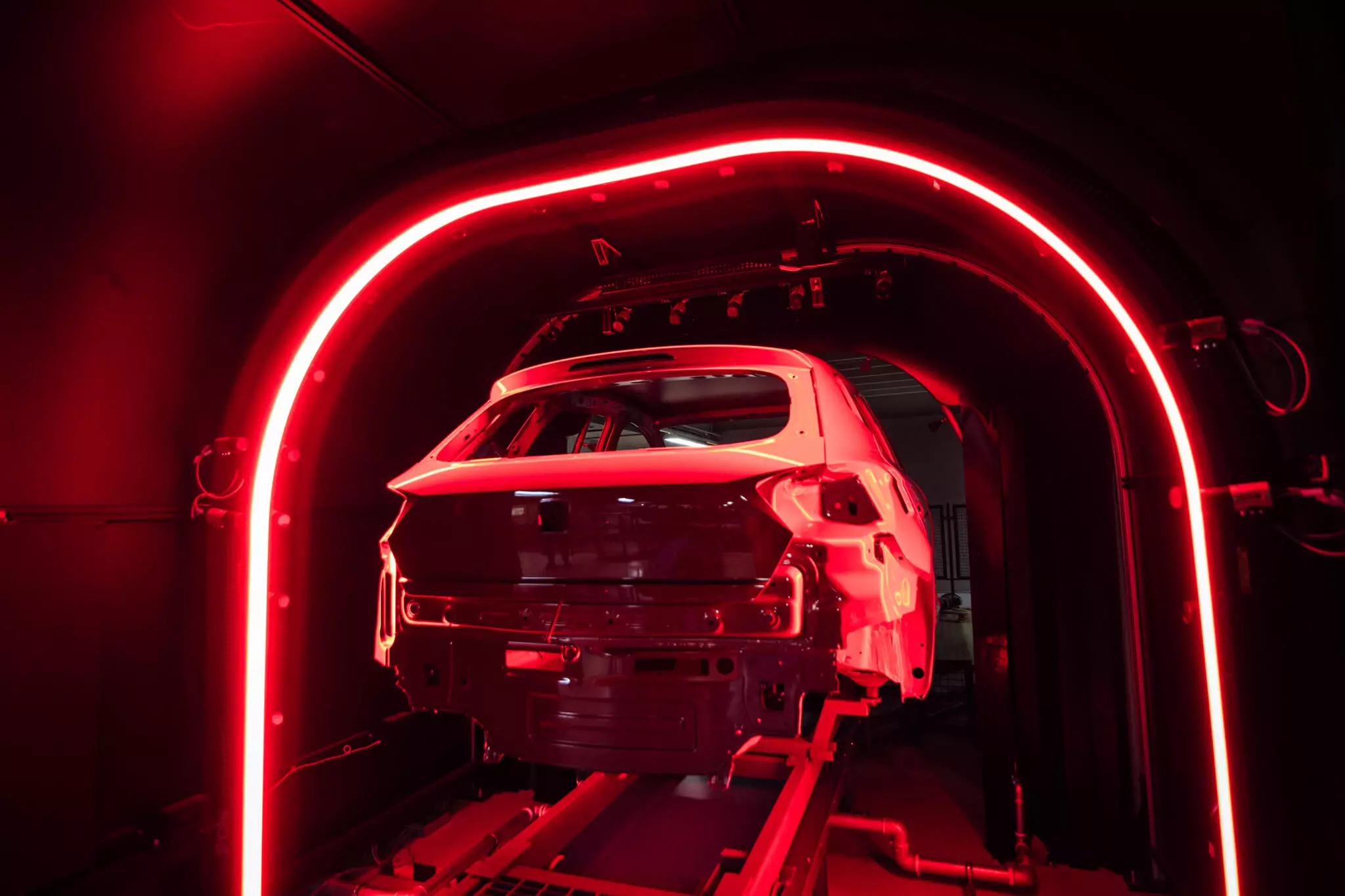
Van 60 uur naar 22 uur om een nieuwe auto te maken: vandaag brengen 84 robots dunne verflagen aan in een spuitcabine en een ultramoderne scanner inspecteert de gladheid van het oppervlak in slechts 43 seconden. Virtual reality, 3D-printen en augmented reality zijn andere innovaties die ontstonden met de komst van Industrie 4.0.
Juan Pérez, verantwoordelijk voor drukprocessenIk was net 18 jaar oud toen ik voor het eerst de Martorell-fabriek binnenging en ik herinner me de euforische sfeer in de stad waar net de Olympische Spelen waren gehouden. Hij was een leerling en mijn collega's en ik hadden hoge verwachtingen van de toekomst - alles was nieuw en ons werd verteld dat het de modernste fabriek van Europa was.
Zo herinnert Juan Pérez, momenteel hoofd van de Printing Processes, zich die eerste dagen, 27 jaar geleden, in de Martorell-fabriek, waar werknemers 10 km per dag liepen: “Toen ik naar huis ging, kon ik de locker niet eens vinden Kamer. Het was heel gemakkelijk om te verdwalen".
Tegenwoordig zijn er autonome voertuigen, die werknemers helpen om ongeveer 25.000 onderdelen per dag naar de lijn te vervoeren, naast 10,5 km spoor en 51 buslijnen.
Een Portugees leidt Kwaliteit
Even belangrijk of belangrijker is de constante kwalitatieve vooruitgang, zelfs in de afgelopen tijd, zoals blijkt uit de nieuwste indicatoren: tussen 2014 en 2018 daalde het aantal klachten van eigenaren van Spaanse merkmodellen met 48% en Martorell bevindt zich praktisch op het niveau van kwaliteitsrecords / betrouwbaarheid van de moederfabriek van Volkswagen in Wolfsburg.
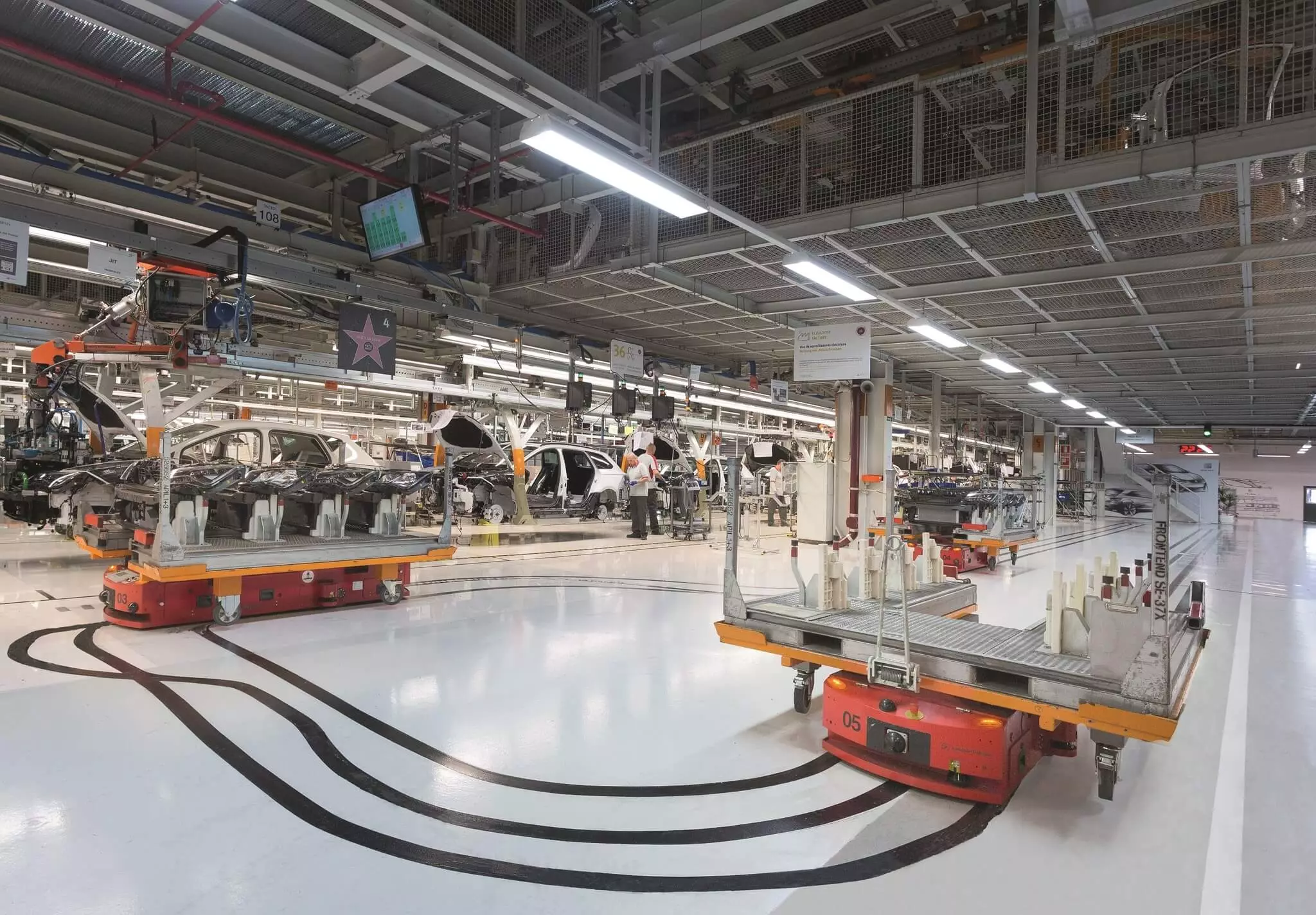
Dit is niet verwonderlijk gezien het feit dat dezelfde industriële processen van A tot Z worden gevolgd, zoals bevestigd door José Machado, de Portugees die nu de kwaliteitscontrole leidt in Martorell, na te zijn begonnen bij Autoeuropa (in Palmela), van waaruit hij naar Puebla ging ( Mexico), om deze belangrijke positie in de wieg van bijna alle SEAT in te nemen:
José Machado, directeur kwaliteitscontroleWe volgen allemaal dezelfde gids en dat is wat telt, want uiteindelijk hebben onze 11.000 medewerkers – direct en indirect – 67 nationaliteiten en 26 verschillende talen.
80% is man, 80% is jonger dan 50 jaar, werkt gemiddeld 16,2 jaar bij het bedrijf en 98% heeft een vast dienstverband, wat bijdraagt aan het creëren van stabiliteit bij mensen, wat dan weerspiegeld wordt in de kwaliteit van hun werk. werk.
Leon is degene die het meest produceert en verkoopt
Net zo trots of zelfs nog trotser op wat hier wordt gedaan, is Ramón Casas – directeur van de sectie Assemblage en Interieurbekleding – de belangrijkste gids van dit bezoek, dat zich richt op dit gebied waarvoor hij voornamelijk verantwoordelijk is: “we hebben drie lijnen in totaal, 1 is van Ibiza/Arona (die 750 auto's per dag voltooit), 2 van Leon en Formentor (900) en 3 van een exclusieve Audi A1 (500)”.
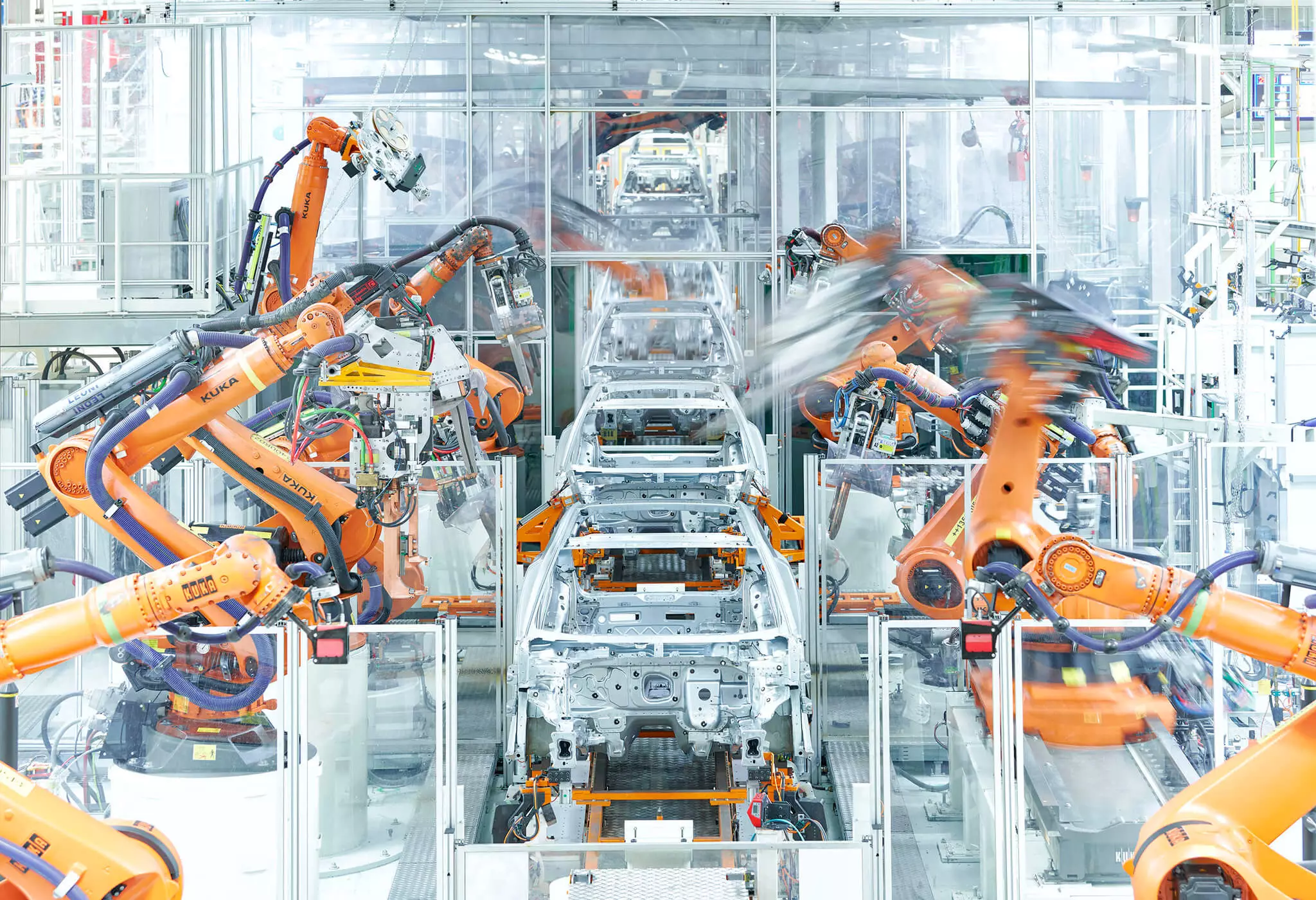
In dit geval staan we aan de wieg van Leon en afgeleiden omdat dit bezoek werd gedaan naast een reis naar de fabriek om de Leon Sportstourer-bus op te halen voordat deze via de gebruikelijke kanalen op de Portugese markt arriveerde.
Casas legt uit dat "deze lijn 2 degene is die de meeste auto's produceert, omdat de Leon wereldwijd de bestverkochte SEAT is (ongeveer 150.000 per jaar), iets hoger dan de Ibiza en Arona (elk ongeveer 130.000) en nu de SUV Formentor zich bij deze assemblagelijn heeft aangesloten, zal de productiecapaciteit bijna uitgeput raken”.
De 500 005 auto's die in 2019 in Martorell werden geproduceerd (81 000 waarvan Audi A1), 5,4% meer dan in 2018, gebruikten 90% van de in de fabriek geïnstalleerde capaciteit, een van de hoogste percentages in heel Europa en een zeer positieve indicator van de financiële gezondheid van het bedrijf.
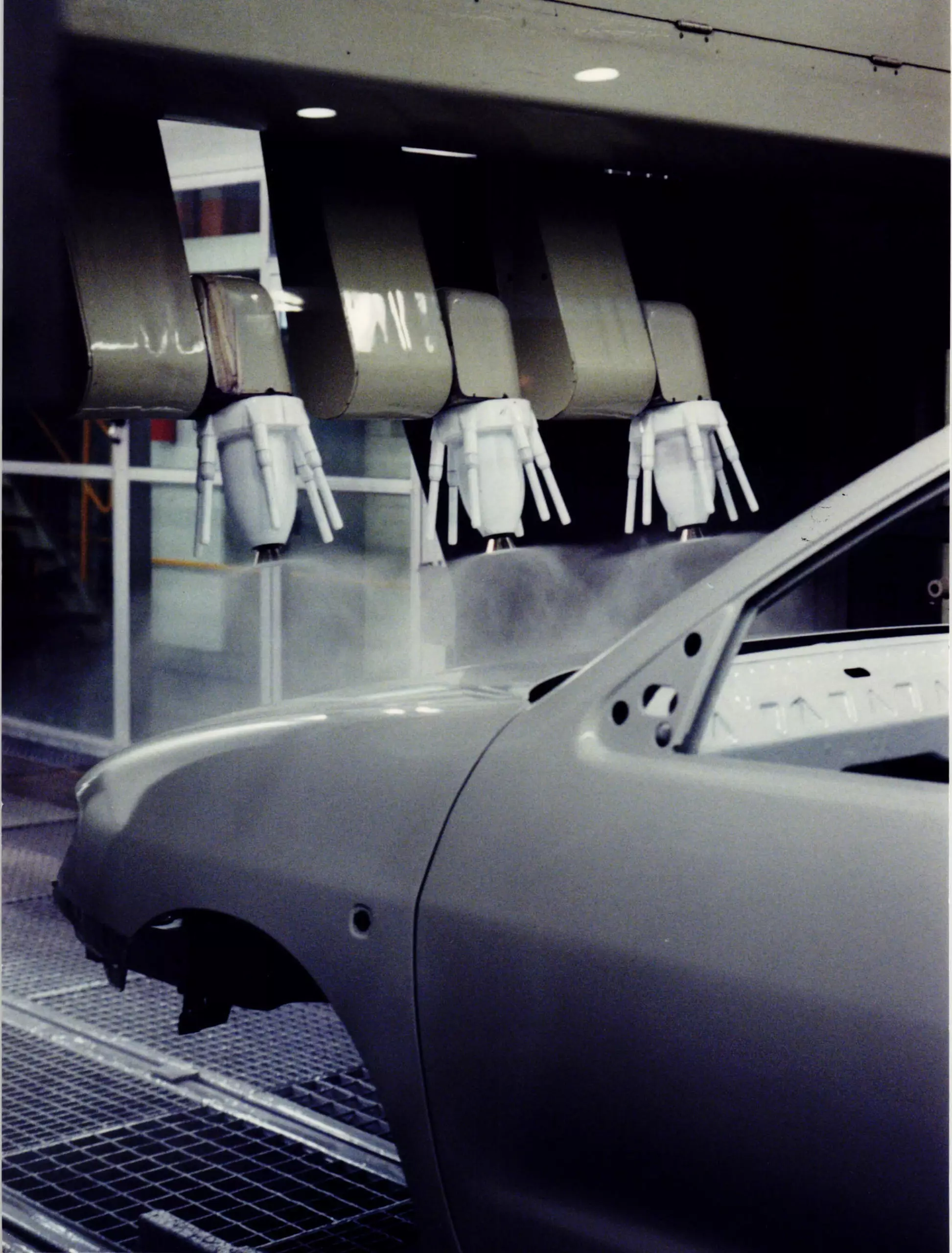
Het Spaanse merk had echter meer verkopen dan de 420.000 SEAT die vorig jaar in Martorell werden geproduceerd, aangezien sommige van zijn modellen buiten Spanje worden gemaakt: de Ateca in Tsjechië (Kvasiny), de Tarraco in Duitsland (Wolfsburg), de Mii in Slowakije (Bratislava) en het Alhambra in Portugal (Palmela).
In totaal produceerde SEAT in 2019 592.000 auto's, met Duitsland, Spanje en het VK als belangrijkste markten, in die volgorde (80% van de productie is bedoeld om naar ongeveer 80 verschillende landen te worden geëxporteerd).
22 uur om een SEAT Leon . te maken
Ik vervolg mijn tocht langs een deel van de 17 km sporen met geëlektrificeerde rails, daarna hangende carrosserieën en rollende basissen met reeds gemonteerde motoren/kasten (die later terug te vinden zijn in wat de fabrieken “Wedding” noemen), terwijl de twee gidsen verdere details: er zijn drie hoofdgebieden in elk van de assemblagelijnen, carrosserie, lak en montage, "maar de laatste is waar de auto's meer tijd doorbrengen", haastte hij zich om Ramón Casas toe te voegen, of als dat niet zo was, ook de één onder zijn directe verantwoordelijkheid.
In een totaal van 22 uur die elke Leon nodig heeft om te worden geproduceerd, blijft er 11:45 min over voor montage, 6:10 min voor carrosserie, 2:45 min voor schilderen en 1:20 min voor afwerking en eindcontrole.

Fabrieksdirecteuren zijn erg trots op het feit dat ze de generatie van modellen kunnen veranderen zonder de assemblageketen te hoeven onderbreken. "Zelfs met bredere rijstroken en een andere wielbasis konden we de productie van de nieuwe Leon integreren zonder de productie van de vorige generatie te hoeven stoppen", benadrukt Casas, voor wie er andere, meer delicate uitdagingen zijn:
Ramón Casas, directeur van de afdeling Assemblage en Interieurbekledingde vorige Leon had 40 elektronische verwerkingseenheden, de nieuwe heeft er minstens twee keer zoveel en als we de plug-in hybride beschouwen, hebben we het over 140! En ze moeten allemaal worden getest voordat ze worden geïnstalleerd.
Ook ingewikkeld is de volgorde van de onderdelen, zodat de configuratie van de auto precies volgt wat is besteld. Alleen in het geval van de voorkant van de Leon kunnen er 500 variaties zijn, wat een idee geeft van de moeilijkheidsgraad van de taak.
José Machado legt ook uit dat “er geen tijdsverschil is tussen de productie van een Leon vijfdeurs of een Sportstourer bestelwagen en het feit dat deze laatste de laatste jaren aan populariteit heeft gewonnen – 40% van de omzet tegen 60% van de vijfdeurs – heeft de lopende band niet beïnvloed”.

Drones en robots helpen...
In Martorell is er meer dan één type robot. Er zijn mensen die leveren tussen verschillende delen van het gigantische industriële complex (zoals drones en geautomatiseerde landvoertuigen, in totaal 170 binnen en buiten de fabriek) en vervolgens robots die helpen de auto's zelf in elkaar te zetten.
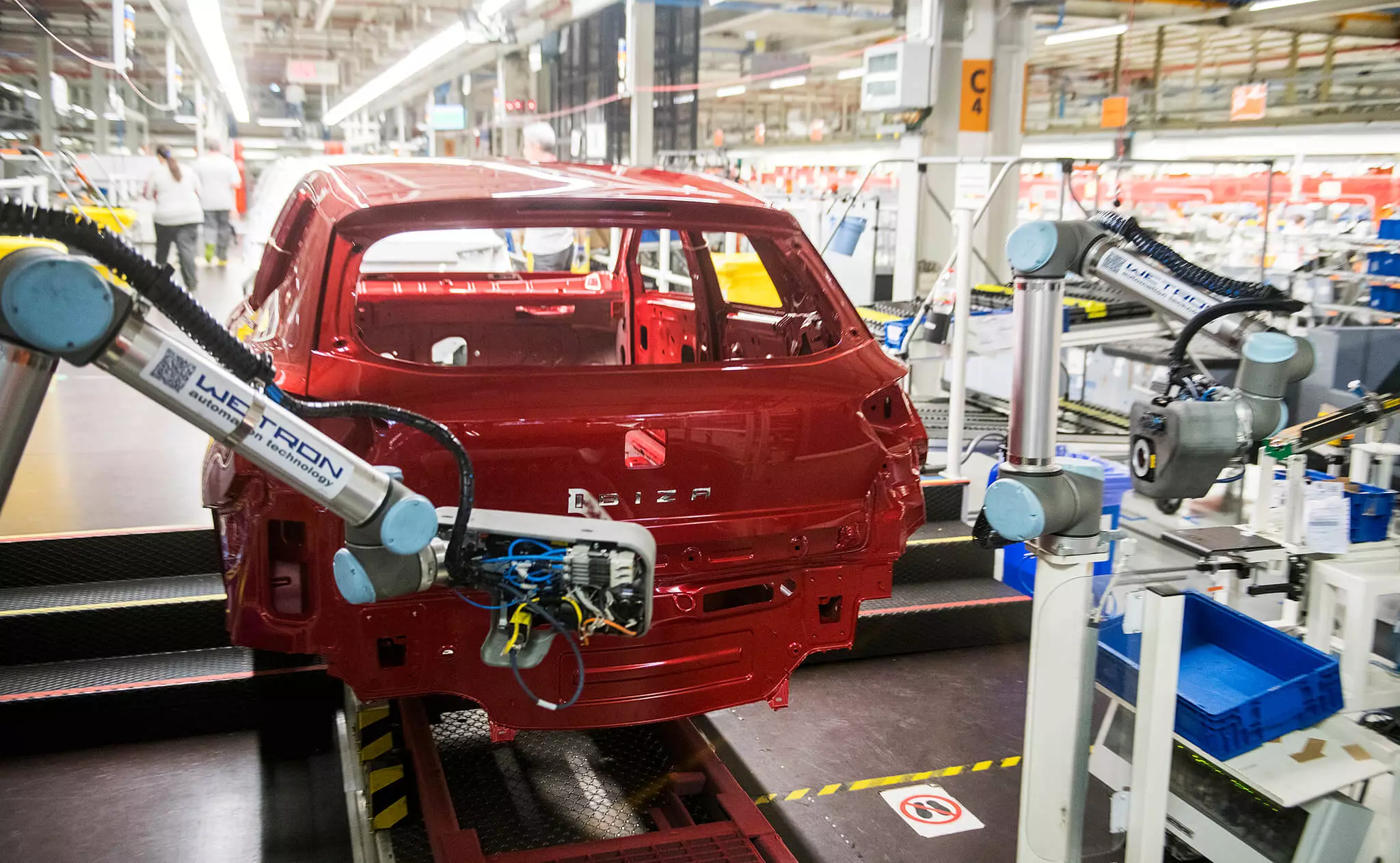
Machado zegt dat "er verschillende robotiseringssnelheden zijn, afhankelijk van het gebied van de assemblagelijn, met ongeveer 15% in het assemblagegebied, 92% in de beplating en 95% in het schilderen". In de montageruimte helpen veel van de robots werknemers om zwaardere onderdelen, zoals de deuren (tot 35 kg) te nemen en te draaien voordat ze in de carrosserie worden gemonteerd.
…maar het is de mens die het verschil maakt
Het hoofd Kwaliteit bij Martorell benadrukt ook het belang van het menselijke team in deze industriële eenheid:
José Machado, directeur kwaliteitscontrole.Zij zijn degenen die het signaal geven als er een probleem is in de assemblageketen, de supervisor bellen die het probleem probeert op te lossen terwijl de lijn in uitvoering is, en er alles aan doen om te voorkomen dat het stopt. Ze wisselen om de twee uur van rol om buitensporige routine te vermijden en ook om hen meer te motiveren, en zelfs ideeën te geven om het hele proces productiever te maken. En als een van de suggesties wordt toegepast, krijgen ze uiteindelijk een percentage van wat de fabriek met die wijziging heeft bespaard.
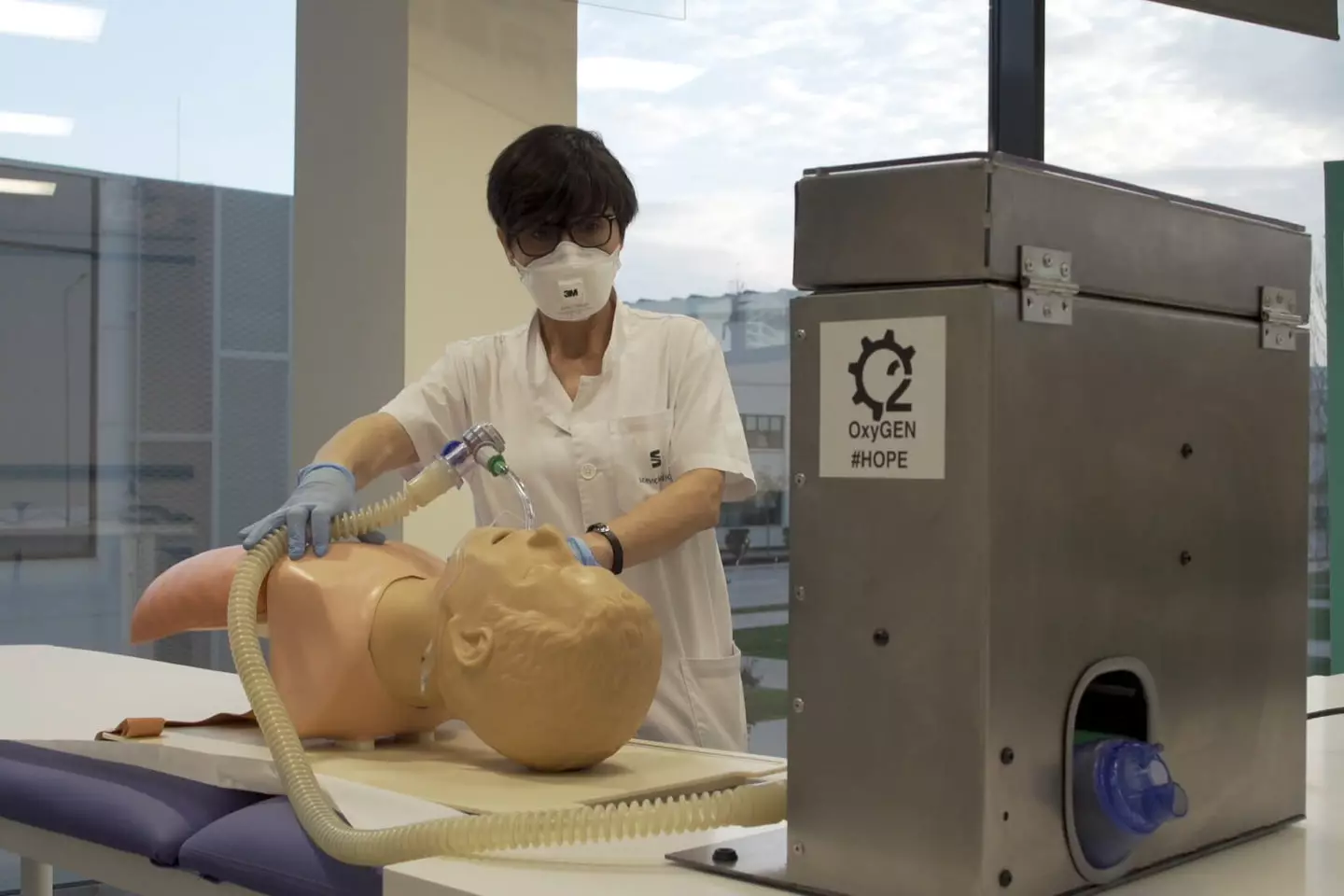
SEAT begon al snel met het produceren van fans in de strijd tegen Covid-19.
Martorell was gesloten tijdens de ernstigste fase van de verspreiding van covid-19, zoals Ramón Casas me uitlegt:
Ramón Casas, directeur van de afdeling Assemblage en InterieurbekledingWe gingen allemaal eind februari naar huis, op 3 april begonnen we met de productie van fans en gingen we op 27 april weer aan het werk, waarbij we geleidelijk virustests deden op alle medewerkers. Het is verplicht om een masker te dragen tijdens de gehele periode van verblijf in de fabriek, er is overal gel en veel acrylbeschermingen in de rustruimtes, cafetaria, enz.