Vi har allerede nevnt profittpotensialet til Tesla modell 3 . Det var en av konklusjonene fra den uttømmende analysen av modellen – demontert til den «siste skruen» – utført av ingeniørkonsulentfirmaet Munro & Associates.
Administrerende direktør, Sandy Munro, var imponert over modellens teknologi, knyttet til batterier og elektronikk, som han anser for å være den mest avanserte i bransjen i dag.
Munro kom imidlertid med flere kritikk som ifølge ham hindrer Model 3 i å nå sitt potensial, nemlig det dårlige designet (ikke en kritikk av estetikken, men av designet); og produksjon, som til tross for økende antall, krever mange flere ressurser enn andre produksjonslinjer.
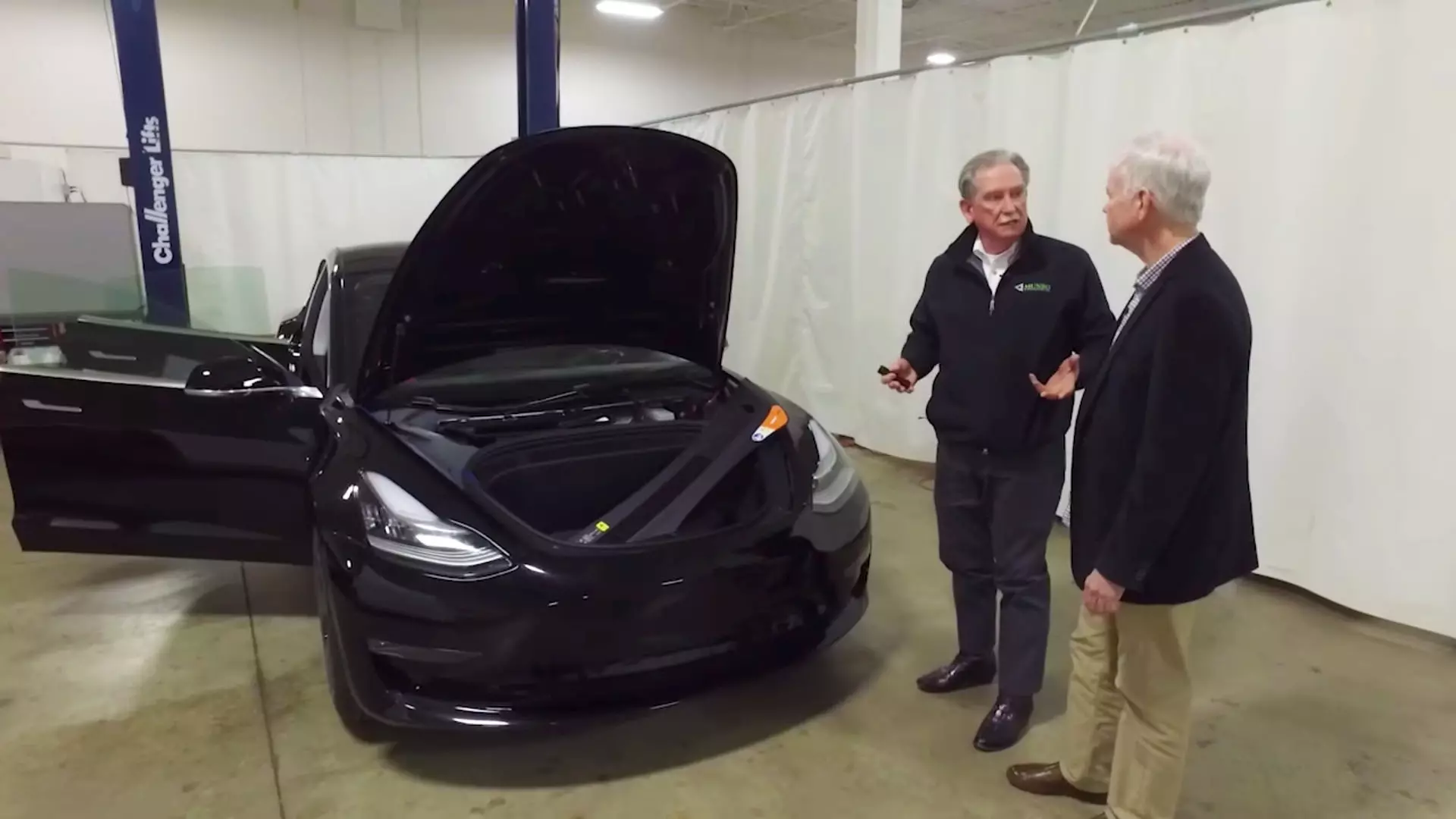
Munro konkluderte med at betongenheten til den demonterte Tesla Model 3 koster 2000 dollar mer (1750 euro) å bygge enn en BMW i3 (en annen av modellene som allerede har passert gjennom silen hans), dette uten å telle tilleggskostnadene som kommer fra monteringen linje.
Abonner på vårt nyhetsbrev her
Roten til problemene? Elon Musks uerfarenhet
Elon Musk, Teslas administrerende direktør, har uten tvil visjonen, men det gjør ham ikke til en ekspert på å lage biler. Problemene rapportert av Sandy Munro avslører Musks uerfarenhet i bilindustrien:
Hvis denne bilen ble laget et annet sted, og Elon (Musk) ikke var en del av produksjonsprosessen, ville de (Tesla) tjent mye penger. De lærer alle de gamle feilene alle andre gjorde for år siden.
Men Munro er en selverkjent beundrer av teknologien unnfanget og brukt av den amerikanske produsenten – som demonstrerer hans “Sillicon Valley”-røtter – så, med tanke på analysen utført av selskapet hans, utdypet han en liste over 227 forbedringstiltak for å "rette ut" Model 3 en gang for alle.
Liste han sendte til Tesla selv ... gratis.
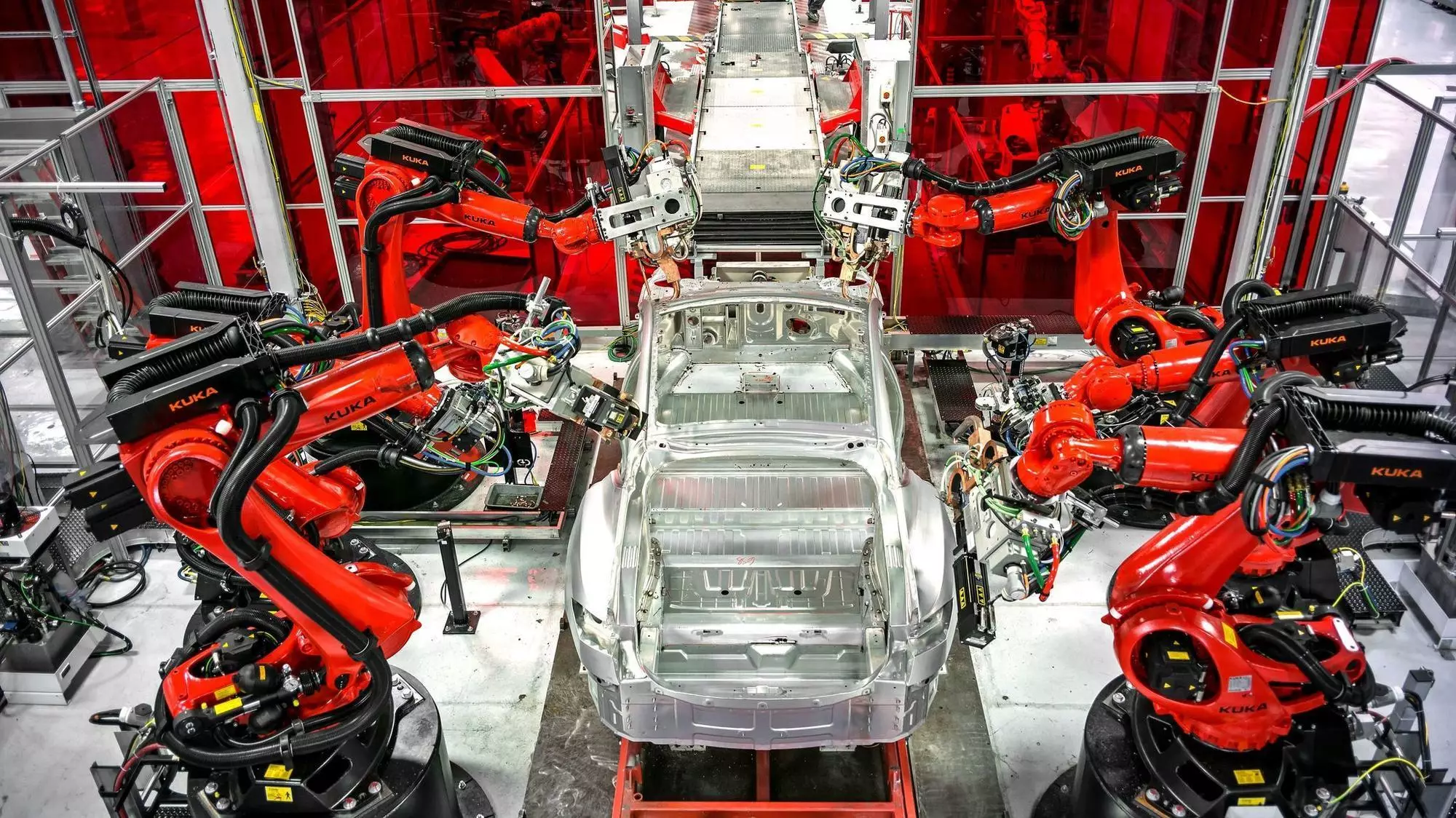
Hva kan forbedres
De fleste av løsningene er knyttet til Model 3s karosseridesign, det vil si unibody-struktur og karosseripaneler, som Munro anser som hovedproblemet, og tilfører unødvendig vekt, kostnad og kompleksitet.
Han trekker frem noen eksempler - dessverre har vi ikke tilgang til alle 227 tiltakene - og mer effektive løsninger for å løse det samme problemet som finnes i konkurranse:
- Stål- og aluminiumsramme i bunnen av bilen - designet for å øke sikkerheten, Munro sier at det ikke er nødvendig, da batteripakken, plassert på plattformens gulv, gir all nødvendig stivhet. Resultat: økt vekt og kostnader uten å gi store fordeler.
- Bakluke i aluminium — bestående av ni deler forbundet med sveisepunkter og nagler. Munro foreslår å erstatte den med et enkelt stykke i glassfiber som sett hos andre byggere.
- Bakre hjulbue - også laget av ni metallstykker som er naglet, sveiset og limt sammen. På Chevrolet Bolt er det bare et stemplet stykke i stål, for eksempel.
Tesla har selv nevnt ved tidligere anledninger at de fortsetter å gjøre stadige forbedringer av produksjonslinjen og bilen. Vi har allerede nevnt f.eks. undertrykking av 300 sveisepunkter som har vist seg unødvendige og konstante optimaliseringer i produksjonslinjen er rapportert.
Selv om Model 3 som Munro demonterte fortsatt er en av de første som ble produsert, og ikke integrerer mange av forbedringene som har funnet sted i mellomtiden, gikk han så langt som å si at Tesla burde sparke ingeniørsjefen som designet strukturen /body av Model 3, forsterket med "de skulle ikke ha ansatt ham", siden det er her mesteparten av "hodepinen" ligger på produksjonslinjen.
Selv om ingen navn faktisk ble nevnt, sparket Tesla Doug Field, leder for kjøretøyteknikk i juni i fjor. Det er nå kjent at Tesla Model 3 var den første bilen utviklet av ham.
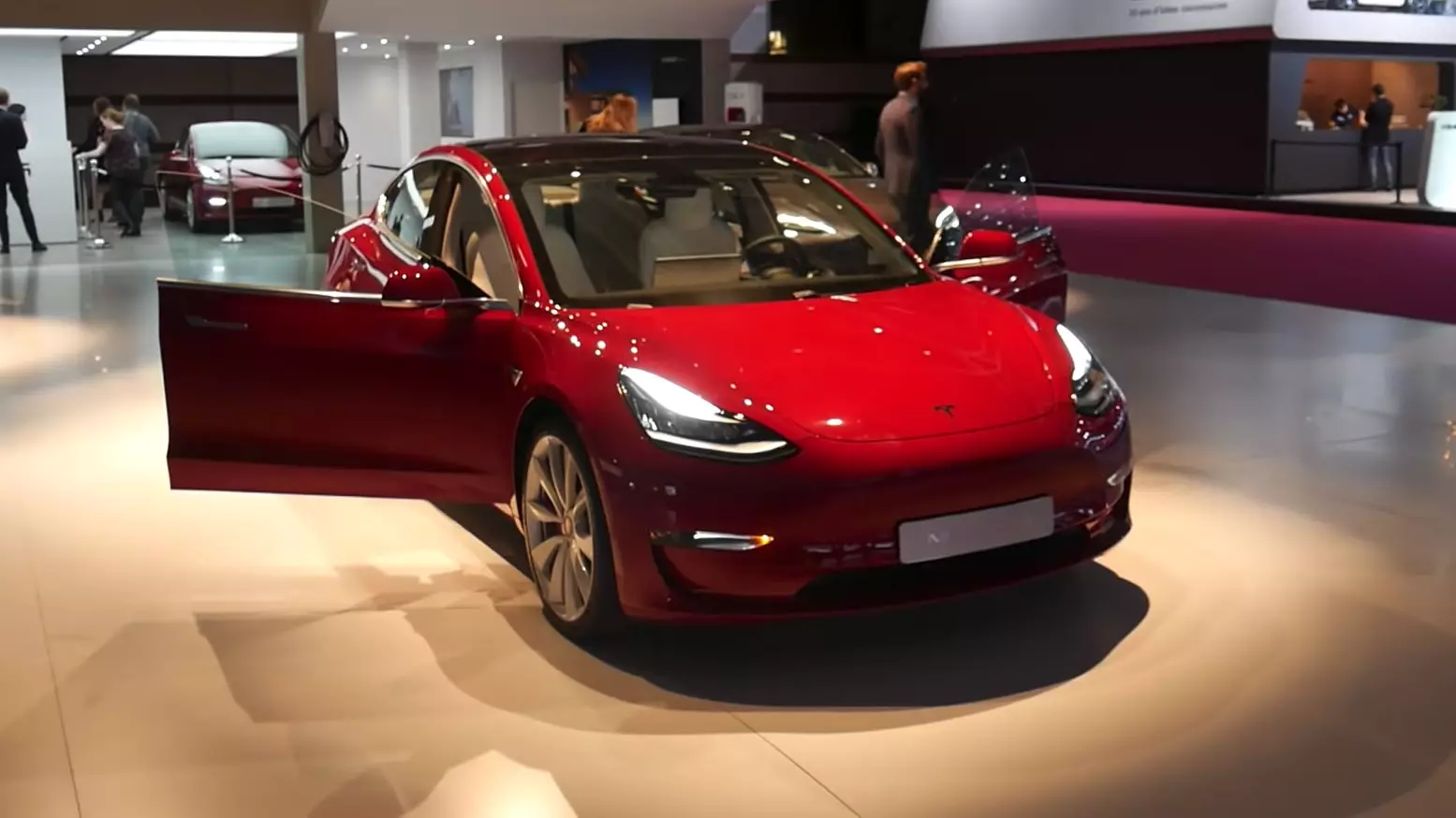
"Den overdrevne automatiseringen hos Tesla var en feil"
Det andre store problemet, ifølge Munro, er overskuddet av ansatte på produksjonslinjen. Hvis veddemålet på automatisering i utgangspunktet ble forsvart av Elon Musk, viste dette seg å være feil – i stor grad på grunn av bilens designproblemer, slik som overskuddet av loddepunkter, nevnt av Munro –, en feil innrømmet av Musk selv for noen år siden måneder.Først nå har vi gått fra "8 til 80", med Fremont-fabrikken, hvor alle Tesla-er produseres - en tidligere enhet som tilhører Toyota og GM - sysselsetter rundt 10 tusen ansatte , som i år vil produsere noe sånt som 350 000 Tesla (S, X og 3).
Sammenlign tallene på den tiden Toyota og GM produserte biler der. på topp 4400 ansatte produserte 450 000 kjøretøyer per år.
Begrunnelsen for et så stort antall ansatte kan delvis forklares med "in-house" produksjon av deler som vanligvis produseres eksternt av leverandører som banker; begrunnelse avvist av Munro: "Selv med tre skift og mye arbeid hjemme, er det ingen begrunnelse for å trenge 10 000 mennesker."
Abonner på vår Youtube-kanal.
Kostnader og fortjenestepotensial
Den demonterte Tesla Model 3 ble priset til $50.000, med produksjonskostnaden beregnet av Munro til $34.700 (30.430 euro) — ingeniør-, forsknings- og utviklingskostnader er ikke inkludert i denne beregningen. Selv om man legger til logistikkkostnader og en sjenerøs beregning for arbeidskraft, forventes brutto fortjenestemargin å overstige 30 %, et bemerkelsesverdig tall i bilindustrien.
Han anslår at selv i en startversjon kan Model 3 oppnå en margin på 10 %, med en produksjonskostnad på mindre enn $30 000 (€26 300) - takket være et mindre (og billigere) batteri og mindre installert utstyr. Litt bedre tall enn litt over 30 000 dollar for en Chevrolet Bolt og omtrent 33 000 dollar for en BMW i3 (begge også tidligere anmeldt av Munro & Associates).
I følge Sandy Munro, nå er det et spørsmål om at Tesla skal gjøre sin teknologiske fordel lønnsom. . For dette må ikke bare merket opprettholde et visst produksjonsnivå, det anbefaler også at Elon Musk ansetter ledere med erfaring i oppgaven med å bygge og montere biler. Hvis han lykkes, sier Munro at Elon «ikke er langt unna å tjene penger».
Kilde: Bloomberg