THE бугати хирон е машина от суперлативи — въпреки че по някакъв начин беше ранена в нейна чест от съперник от шведски произход... — и току-що е набрала още един суперлатив на тегло, с добавянето на нови титаниеви спирачни апарати, които трябва да бъдат въведени в този модел по-късно в годината.
Както знаете, на Bugatti Chiron вече беше „собственик“ на най-големите спирачни апарати в автомобилната индустрия. Тези шублери са изковани от блок от алуминиева сплав с висока якост с осем титаниеви бутала отпред и шест бутала отзад. До тук…
по-силен и по-лек
Bugatti направи още една стъпка напред, като разработи титаниеви спирачни апарати – все още най-големите в индустрията – които сега са не само най-големият функционален компонент в титана, произведен чрез 3D печат, тъй като това е първият спирачен апарат, произведен по този метод.
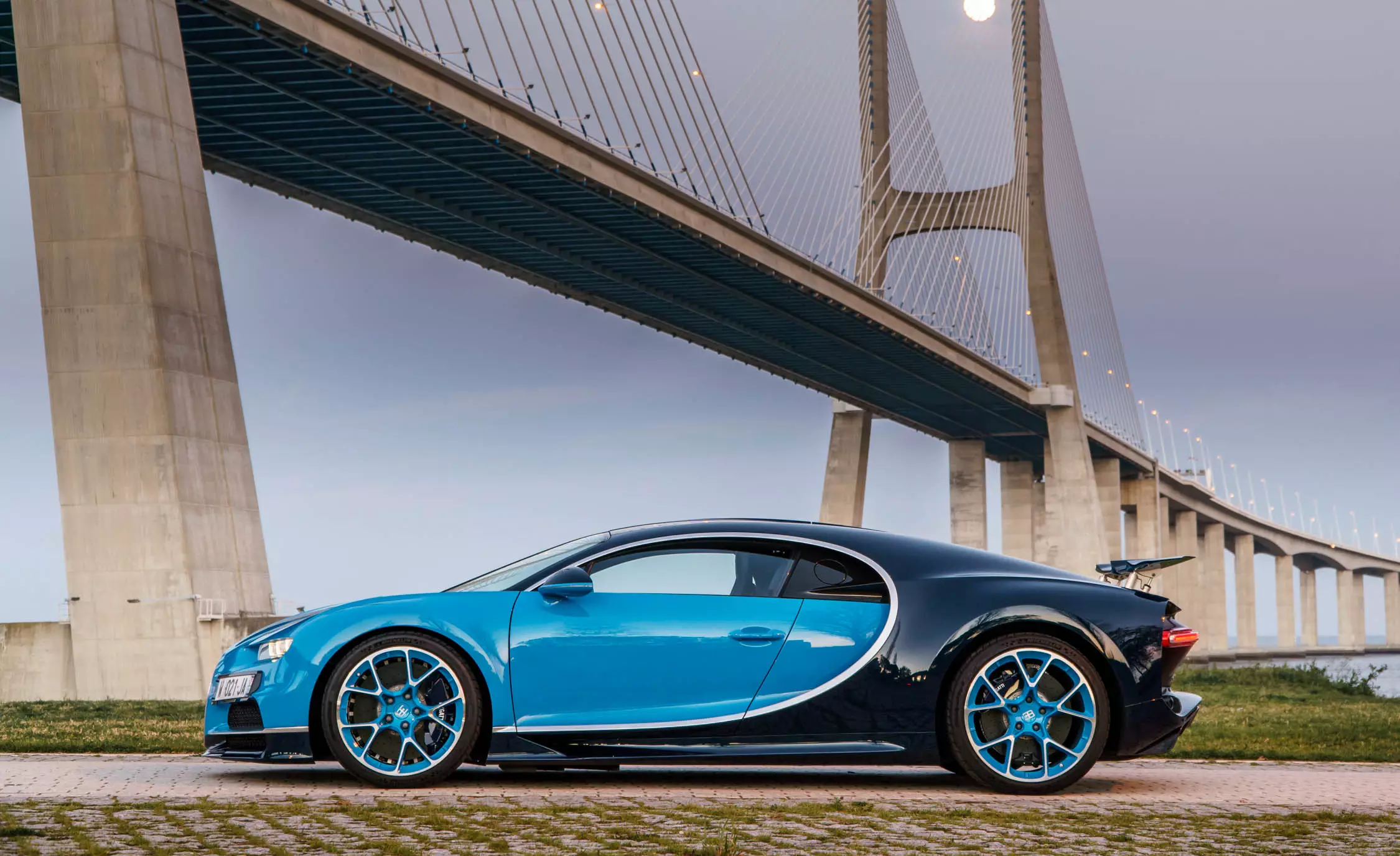
Новите пинсети използват като материал титаниева сплав - Ti6AI4V от името му -, използвана главно от аерокосмическата индустрия в компоненти, подложени на огромен стрес, предлагайки производителност, много по-добра от тази на алуминия. Якостта на опън, разбира се, е изключително висока: 1250 N/mm2 , което означава приложена сила от малко над 125 кг на квадратен милиметър, без тази титаниева сплав да се счупи.
Новият спирачен апарат е дълъг 41 см, широк 21 см и висок 13,6 см и в допълнение към превъзходната си здравина има голямото предимство да намалява значително теглото, което засяга все по-важните неподрессорени маси. Тежи само 2,9 кг срещу 4,9 кг от същата алуминиева част, което се равнява на 40% намаление.
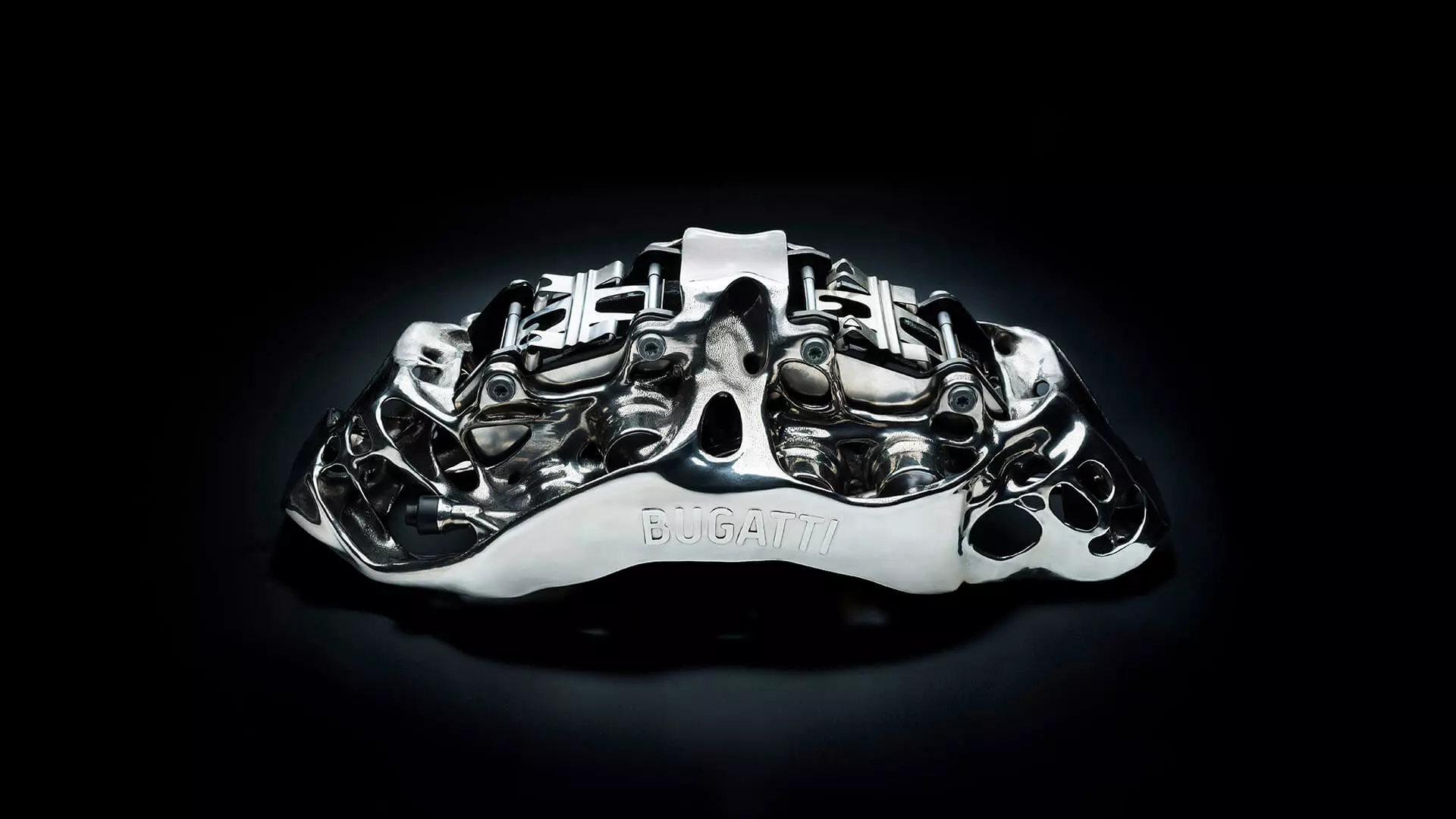
адитивно производство
Тези нови титаниеви спирачни апарати са резултат от сътрудничеството между отдела за развитие на Bugatti и Laser Zentrum Nord. За първи път титанът беше използван вместо алуминий за отпечатване на компоненти на автомобила, което донесе своите предизвикателства. Високата якост на титана е основната причина, поради която този материал не е използван, което принуди прибягването до високопроизводителен принтер.Този специален 3D принтер, разположен на Laser Zentrum Nord, който беше най-големият в света, способен да работи с титан в началото на проекта, е оборудван с четири 400W лазера.
Отпечатването на всяка пинсета отнема 45 часа.
По време на този процес титановият прах се отлага слой по слой, като четирите лазера разтопяват праха в предварително определената форма. Материалът се охлажда почти веднага и скобата започва да се оформя.
Общо са необходими около 2213 слоя, докато парчето е завършено.
След нанасяне на последния слой излишният материал се отстранява от печатащата камера, почиства се и се запазва за повторна употреба. Спирачният апарат, вече завършен, остава в камерата, поддържан от опора, която му позволява да запази формата си. Подпора, която се отстранява след термична обработка на компонента (която достига 700 ºC), за да се стабилизира и да се гарантира желаната устойчивост.
Повърхността е завършена чрез комбинация от механични, физични и химични процеси, които също допринасят за подобряване на нейната якост на умора. Необходими са повече от 11 часа, за да се оптимизират контурите на функционални повърхности, като контактите на буталата, с помощта на петосен обработващ център.
Bugatti, лидер на групата в 3D печат
С това Bugatti заема водеща позиция във Volkswagen Group не само по отношение на технологията за 3D печат, но и по отношение на високотехнологичните приложения. Един вид милионерска лаборатория и много, много мощна...
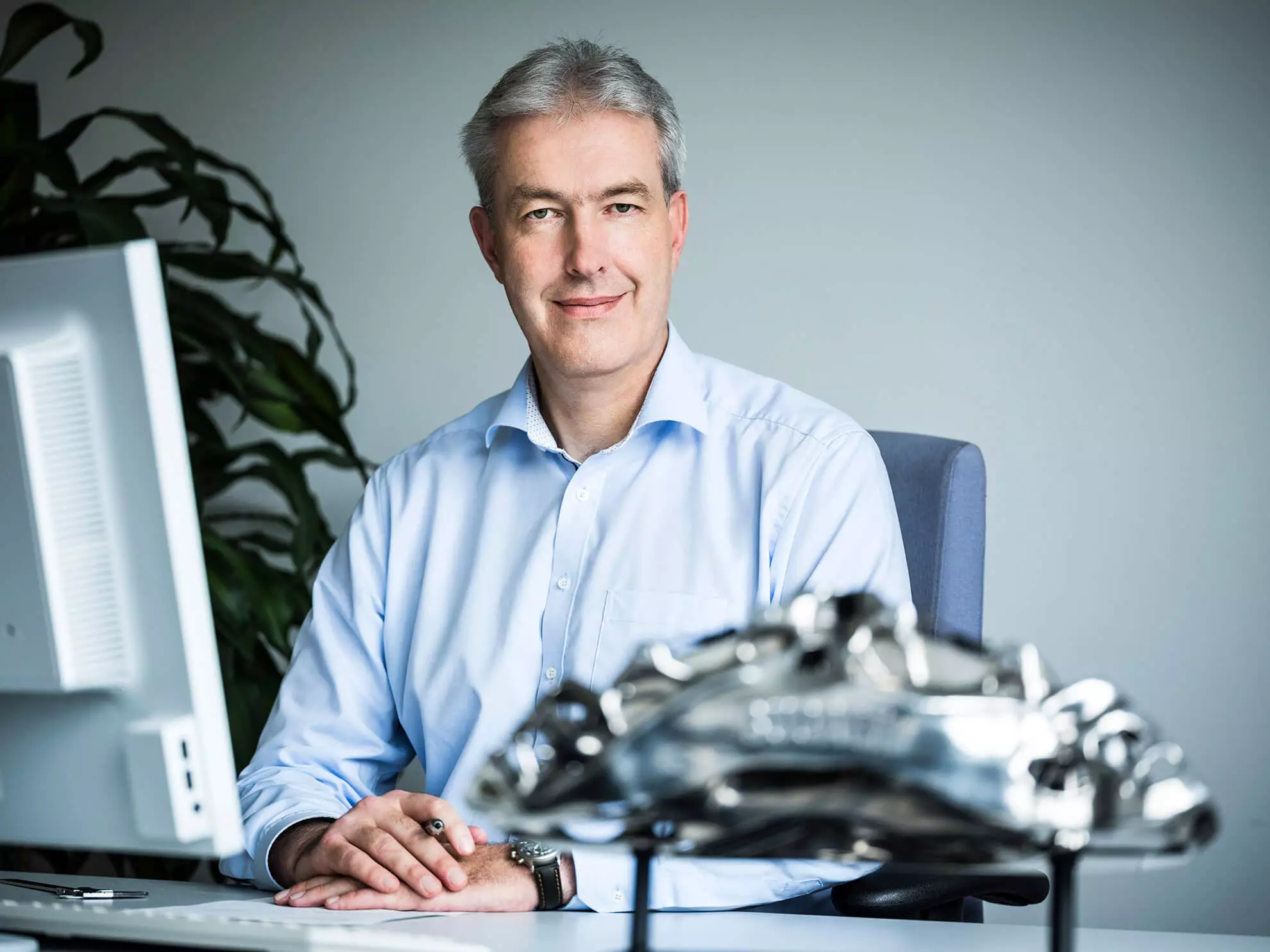
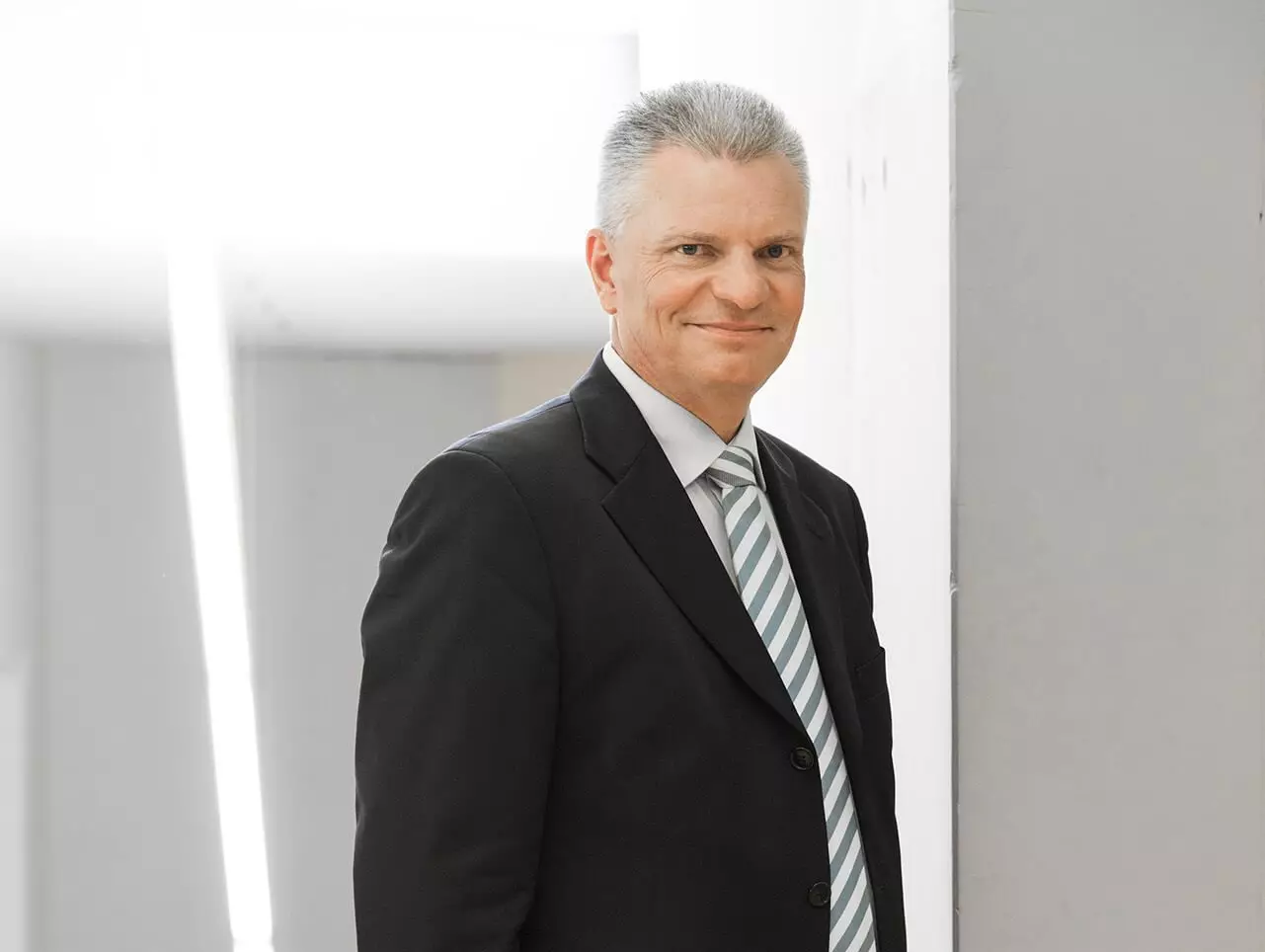