В bugatti chiron машина в превосходной степени - хотя ее каким-то образом ранил в ее честь соперник шведского происхождения… - и только что приобрел еще одну превосходную степень веса с добавлением новых титановых тормозных суппортов, которые должны быть введены в эту модель позже в год.
Как известно, Bugatti Chiron уже был «владельцем» самых больших тормозных суппортов в автомобильной промышленности. Эти суппорты были выкованы из высокопрочного блока из алюминиевого сплава с восемью титановыми поршнями спереди и шестью поршнями сзади. Уже…
сильнее и легче
Теперь Bugatti сделала еще один шаг вперед, разработав титановые тормозные суппорты - все еще самые большие в отрасли, - которые теперь не только самый большой функциональный компонент из титана, произведенный с помощью 3D-печати, поскольку это первый тормозной суппорт, изготовленный этим методом.
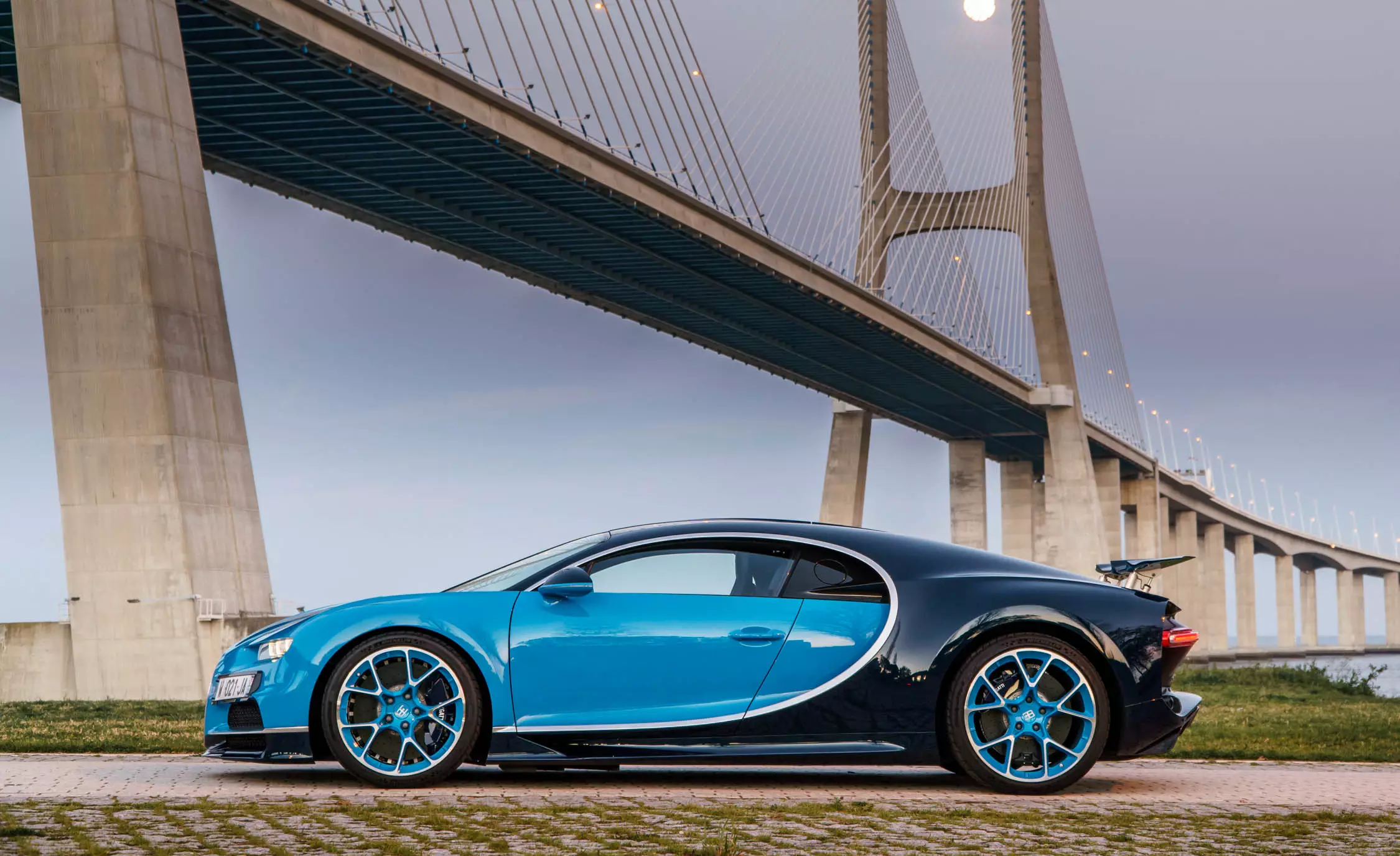
В новых пинцетах в качестве материала используется титановый сплав - Ti6AI4V из его названия - который используется, в основном, в аэрокосмической промышленности в компонентах, подверженных огромным нагрузкам, и по своим характеристикам намного превосходит алюминий. Предел прочности на разрыв, конечно, чрезвычайно высок: 1250 Н / мм2 , что означает приложенное усилие чуть более 125 кг на квадратный миллиметр без разрушения титанового сплава.
Новый тормозной суппорт имеет длину 41 см, ширину 21 см и высоту 13,6 см, и, помимо превосходной прочности, он обладает большим преимуществом, заключающимся в значительном уменьшении веса, влияя на неизменно важные неподрессоренные массы. Весит всего 2,9 кг. по сравнению с 4,9 кг той же алюминиевой детали, что соответствует снижению на 40%.
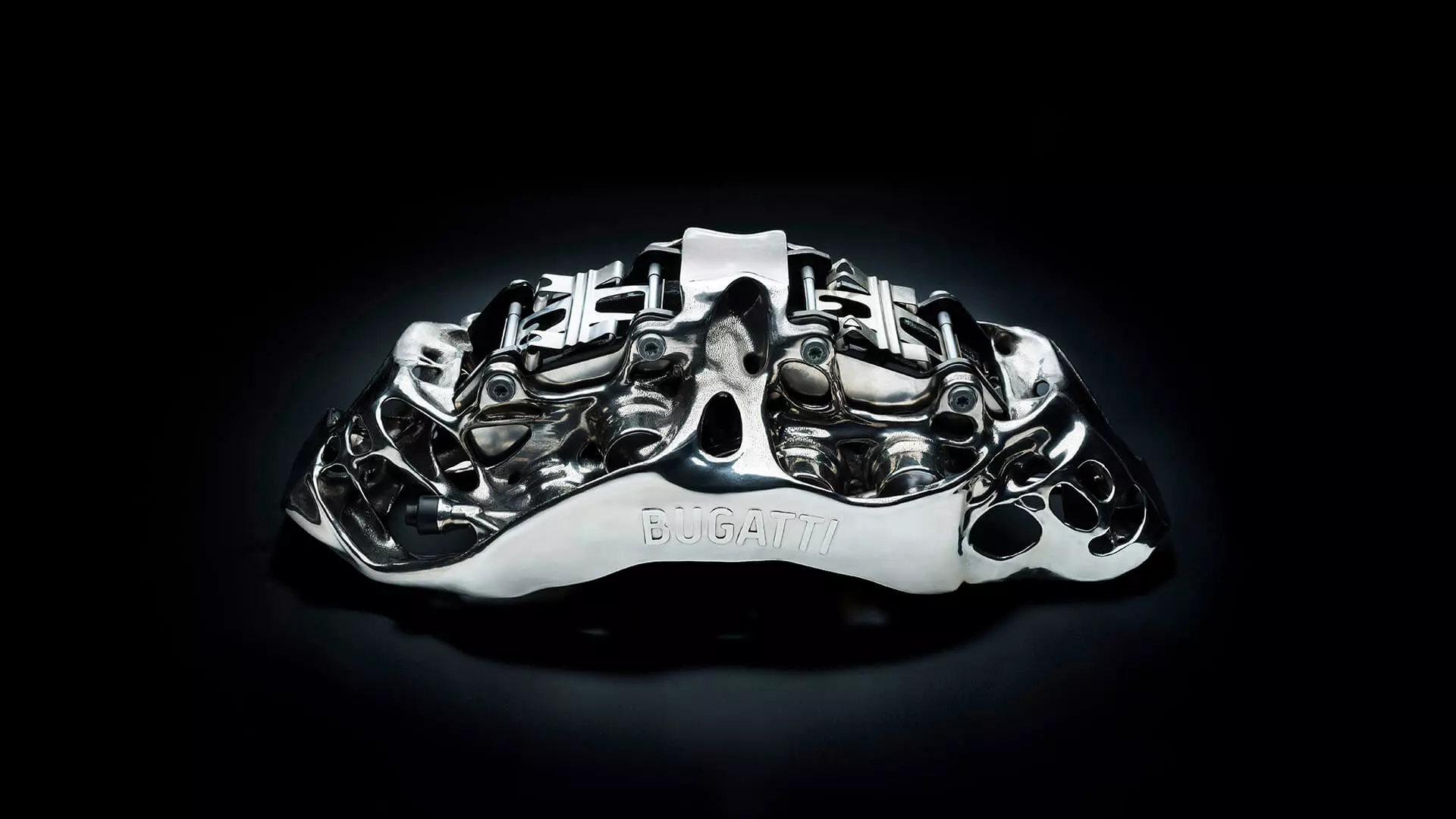
производство добавок
Эти новые титановые тормозные суппорты являются результатом сотрудничества отдела разработок Bugatti и Laser Zentrum Nord. Впервые для печати компонентов автомобилей вместо алюминия был использован титан, что вызвало определенные проблемы. Высокая прочность титана была основной причиной того, что этот материал не использовался, что вынудило прибегнуть к высокопроизводительному принтеру.Этот специальный 3D-принтер, расположенный в Laser Zentrum Nord, который в начале проекта был крупнейшим в мире, способным обрабатывать титан, оснащен четырьмя лазерами мощностью 400 Вт.
На печать каждого пинцета уходит 45 часов.
Во время этого процесса слой за слоем наносится титановый порошок, при этом четыре лазера расплавляют порошок до заданной формы. Материал практически сразу остывает, и зажим начинает приобретать форму.
Всего нужно около 2213 слоев, пока изделие не будет готово.
После нанесения последнего слоя излишки материала удаляются из печатной камеры, очищаются и сохраняются для повторного использования. Уже собранный тормозной суппорт остается в камере, опираясь на опору, что позволяет ему сохранять свою форму. Опора, которая удаляется после термообработки компонента (до 700 ºC), чтобы стабилизировать его и гарантировать желаемое сопротивление.
Поверхность обрабатывается с помощью комбинации механических, физических и химических процессов, которые также способствуют повышению ее усталостной прочности. Оптимизация контуров функциональных поверхностей, таких как контакты поршня, с помощью пятиосевого обрабатывающего центра занимает более 11 часов.
Bugatti, лидер группы в области 3D-печати
Благодаря этому Bugatti занимает лидирующие позиции в Volkswagen Group не только с точки зрения технологий 3D-печати, но и с точки зрения высокотехнологичных приложений. Этакая лаборатория миллионеров и очень и очень мощная ...
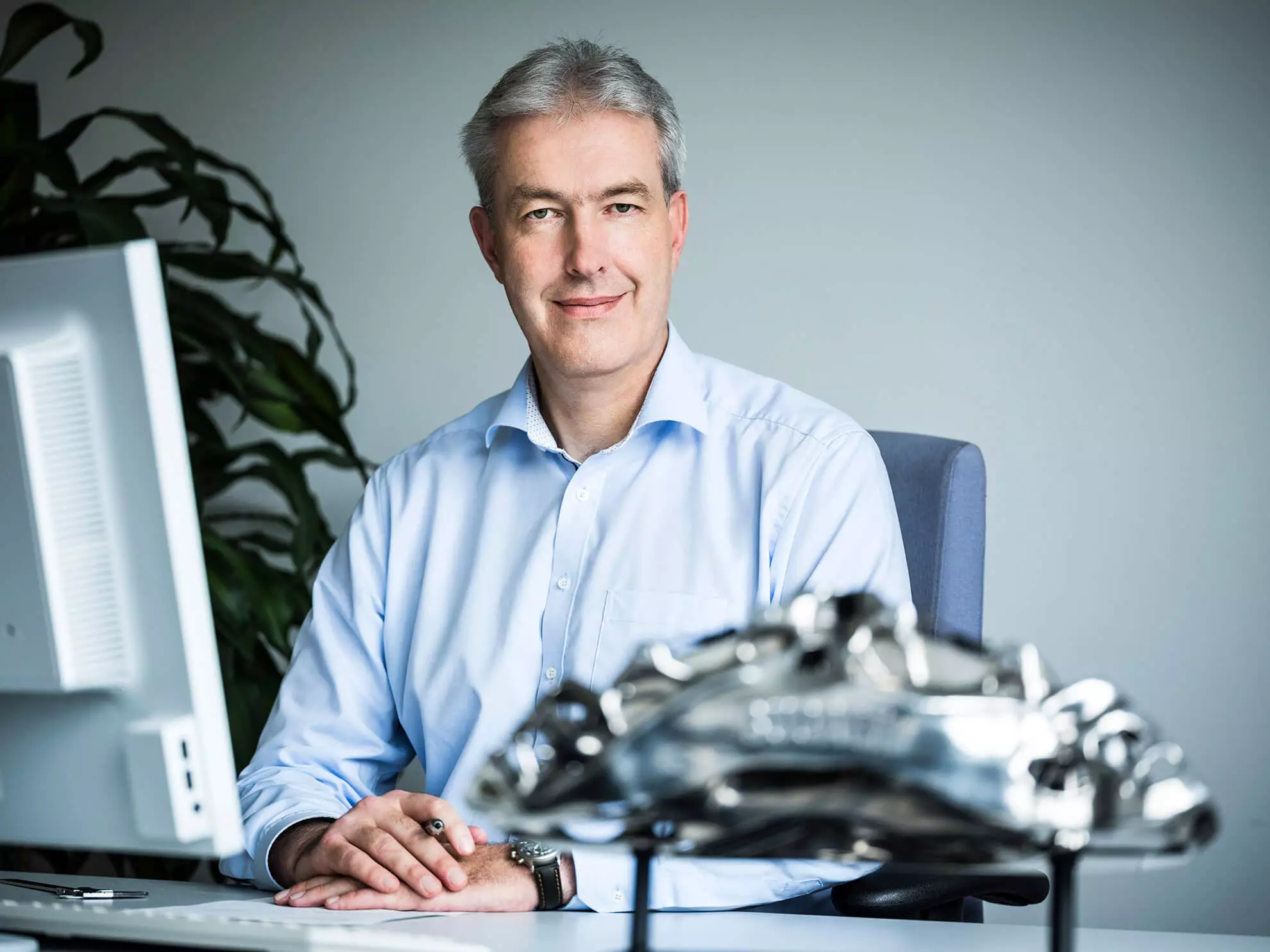
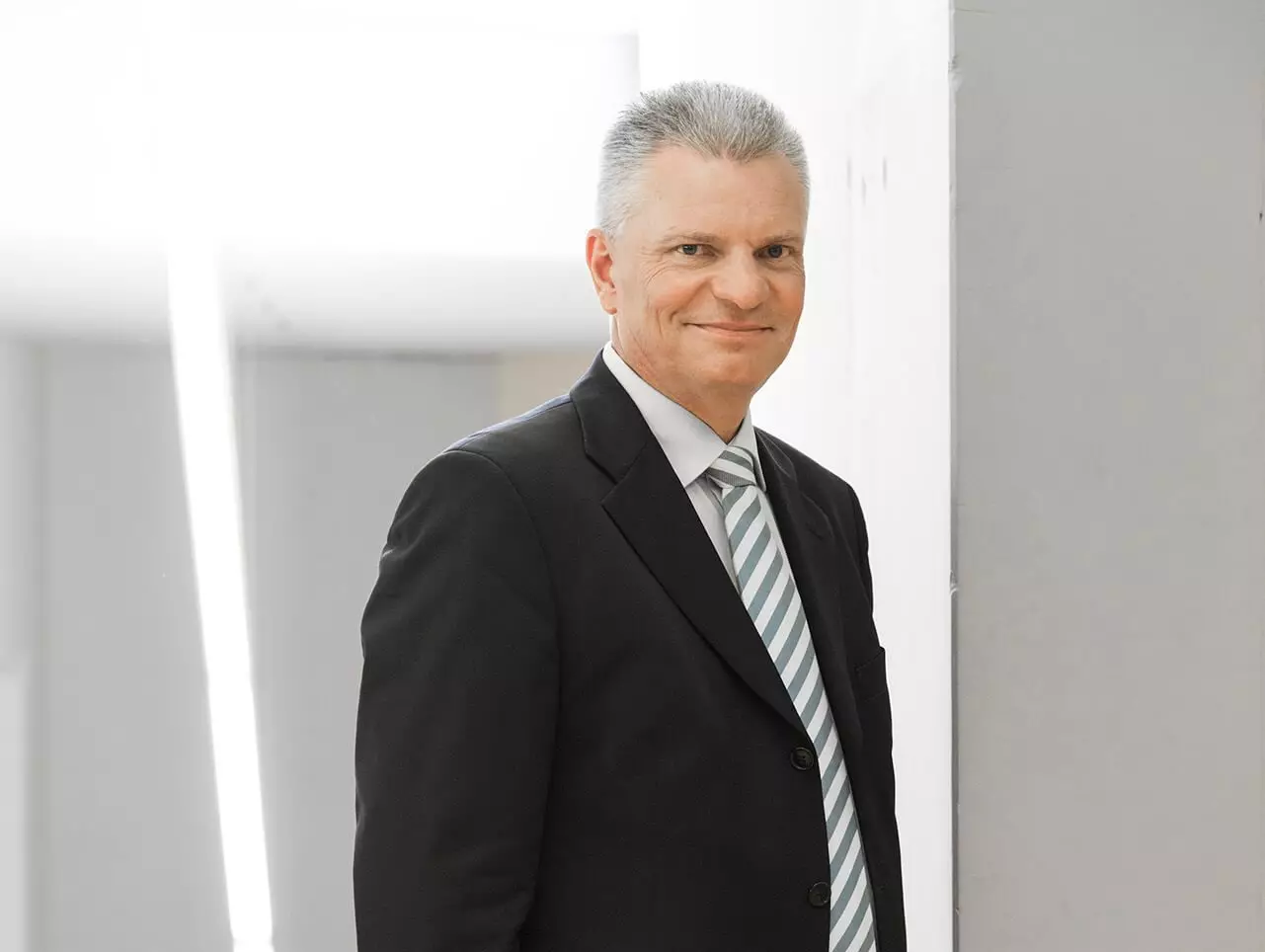