DE bugatti chiron er en maskin av superlativer – selv om den på en eller annen måte ble såret til sin ære av en rival av svensk opprinnelse … – og har nettopp fått enda en superlativ av vekt, med tillegg av nye bremsekalipere i titan, som bør introduseres i denne modellen senere i året.
Som du vet, Bugatti Chiron var allerede "eieren" av de største bremsekaliperne i bilindustrien. Disse kaliperne ble smidd fra en blokk av høystyrke aluminiumslegering med åtte titanstempler foran og seks stempler bak. Så langt…
sterkere og lettere
Bugatti har nå tatt et nytt skritt fremover, ved å utvikle titan bremsekalipere – fortsatt de største i bransjen – som nå ikke bare er den største funksjonelle komponenten i titan produsert gjennom 3D-utskrift, da det er den første bremsekaliperen som er produsert med denne metoden.
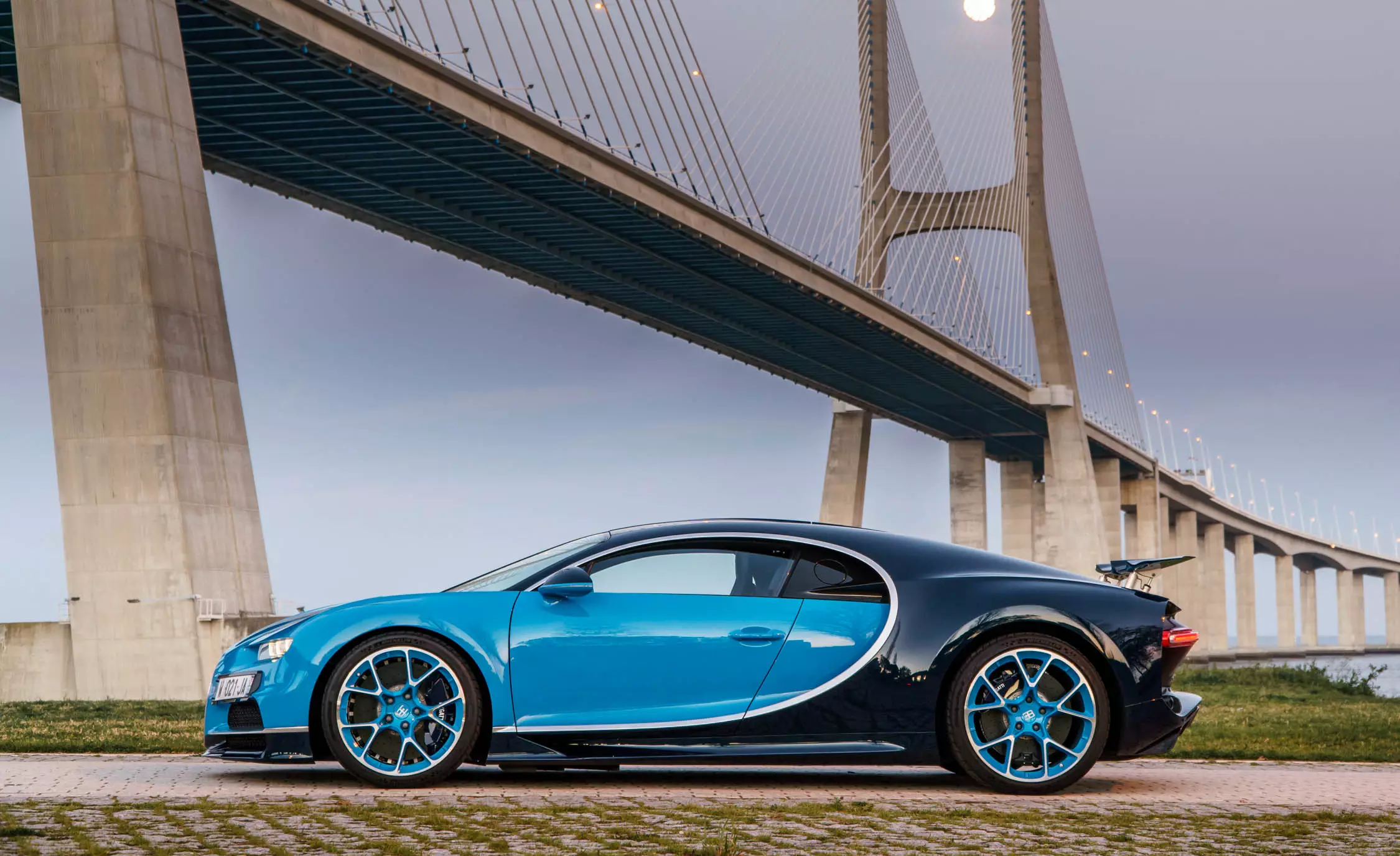
Den nye pinsetten bruker som materiale en titanlegering – Ti6AI4V fra navnet – som hovedsakelig brukes av romfartsindustrien i komponenter som er utsatt for enorm belastning, og gir en ytelse som er langt overlegen aluminium. Strekkfastheten er selvfølgelig ekstremt høy: 1250 N/mm2 , som betyr en påført kraft på vel 125 kg per kvadratmillimeter uten at denne titanlegeringen går i stykker.
Den nye bremsekaliperen er 41 cm lang, 21 cm bred og 13,6 cm høy og har i tillegg til sin overlegne styrke den store fordelen at den reduserer vekten betydelig, og påvirker de stadig viktige ufjærede massene. Veier kun 2,9 kg mot 4,9 kg av samme aluminiumsdel, noe som tilsvarer 40 % reduksjon.
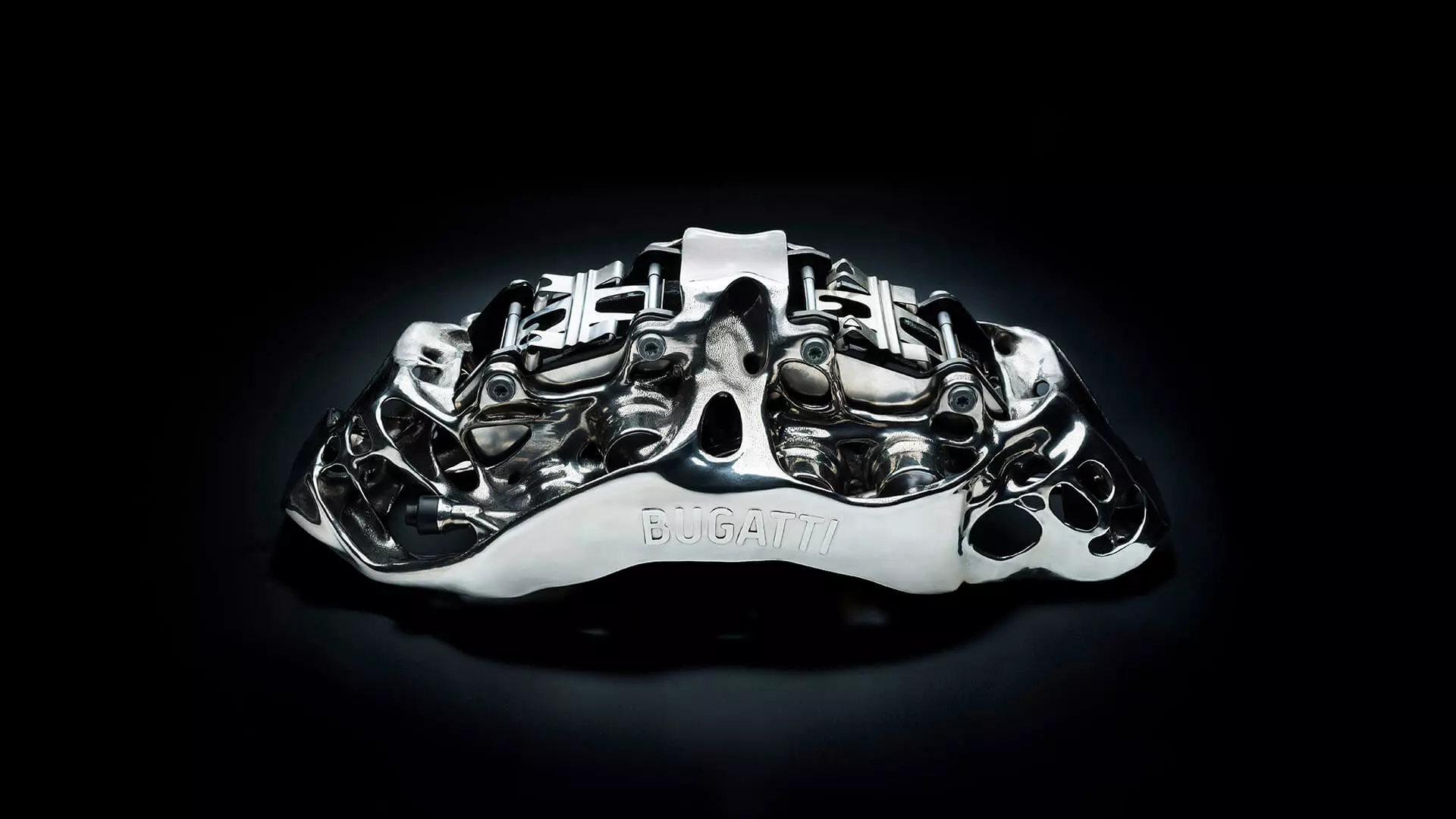
additiv produksjon
Disse nye bremsekaliperne i titan er et resultat av samarbeid mellom Bugatti Development Department og Laser Zentrum Nord. For første gang ble titan brukt i stedet for aluminium for å skrive ut kjøretøykomponenter, noe som ga utfordringene. Den høye styrken til titan har vært hovedårsaken til at dette materialet ikke har blitt brukt, noe som tvang stedet til en høyytelsesskriver.Denne spesielle 3D-skriveren, som ligger på Laser Zentrum Nord, som var den største i verden som var i stand til å håndtere titan i begynnelsen av prosjektet, er utstyrt med fire 400W lasere.
Hver pinsett tar 45 timer å skrive ut.
Under denne prosessen avsettes titanpulver lag for lag, med de fire laserne som smelter pulveret til den forhåndsbestemte formen. Materialet avkjøles nesten umiddelbart, og klemmen begynner å ta form.
Totalt trengs ca 2213 lag til stykket er ferdig.
Etter at det siste laget er avsatt, fjernes overskuddsmaterialet fra trykkekammeret, renses og konserveres for gjenbruk. Bremsekaliperen, som allerede er komplett, forblir i kammeret, støttet av en støtte, som lar den bevare formen. Støtte som fjernes etter at komponenten får en varmebehandling (som når 700 ºC) for å stabilisere den og garantere ønsket motstand.
Overflaten er ferdigbehandlet gjennom en kombinasjon av mekaniske, fysiske og kjemiske prosesser, som også bidrar til å forbedre utmattelsesstyrken. Det tar mer enn 11 timer å optimalisere konturene til funksjonelle overflater, for eksempel stempelkontakter, ved å bruke et femakset maskineringssenter.
Bugatti, gruppeleder innen 3D-printing
Med dette tar Bugatti ledelsen i Volkswagen-konsernet ikke bare når det gjelder 3D-utskriftsteknologi, men også når det gjelder høyteknologiske applikasjoner. Et slags millionærlaboratorium og veldig, veldig kraftig...
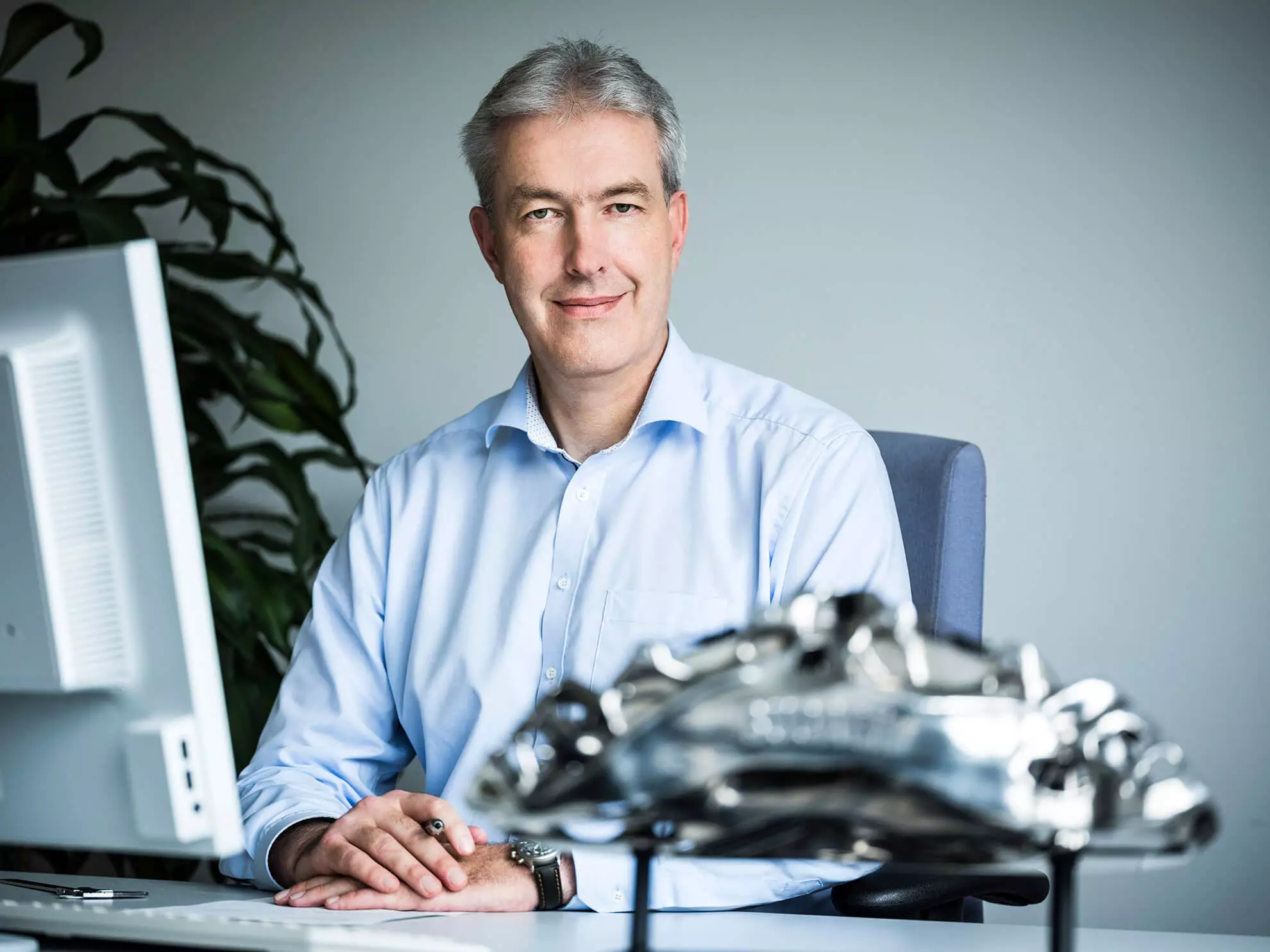
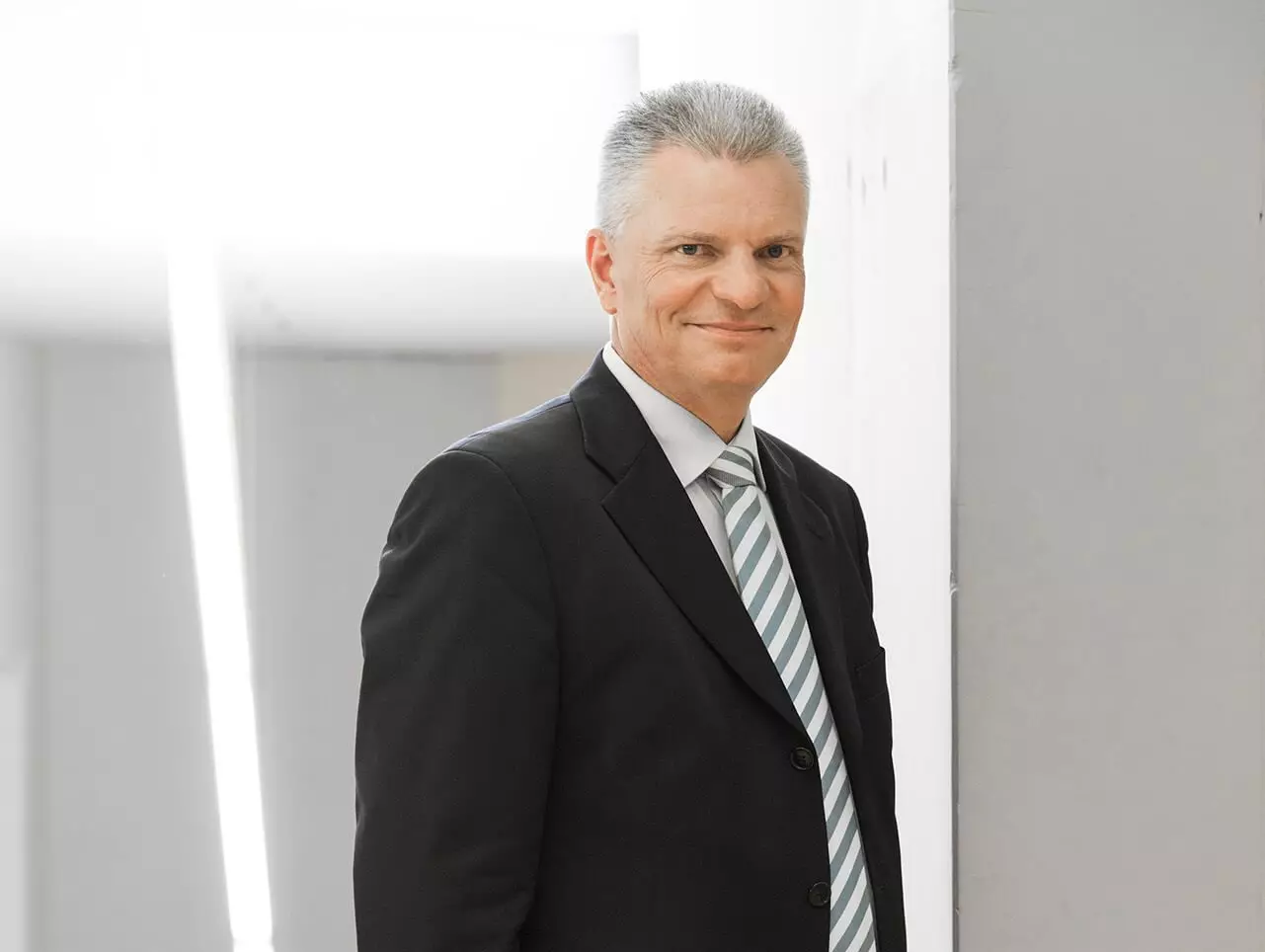