EL bugatti chiron es una máquina de superlativos, a pesar de que de alguna manera fue herida en su honor por un rival de origen sueco ... y acaba de ganar otro superlativo de peso, con la adición de nuevas pinzas de freno de titanio, que deberían introducirse en este modelo más adelante. en el año.
Como sabes, el Bugatti Chiron ya era el "propietario" de las pinzas de freno más grandes de la industria automotriz. Estas pinzas se forjaron a partir de un bloque de aleación de aluminio de alta resistencia con ocho pistones de titanio en la parte delantera y seis pistones en la parte trasera. Hasta ahora…
más fuerte y ligero
Bugatti ha dado un paso más al desarrollar pinzas de freno de titanio, que siguen siendo las más grandes de la industria, que ahora no solo son el componente funcional más grande de titanio producido mediante impresión 3D, ya que es la primera pinza de freno fabricada con este método.
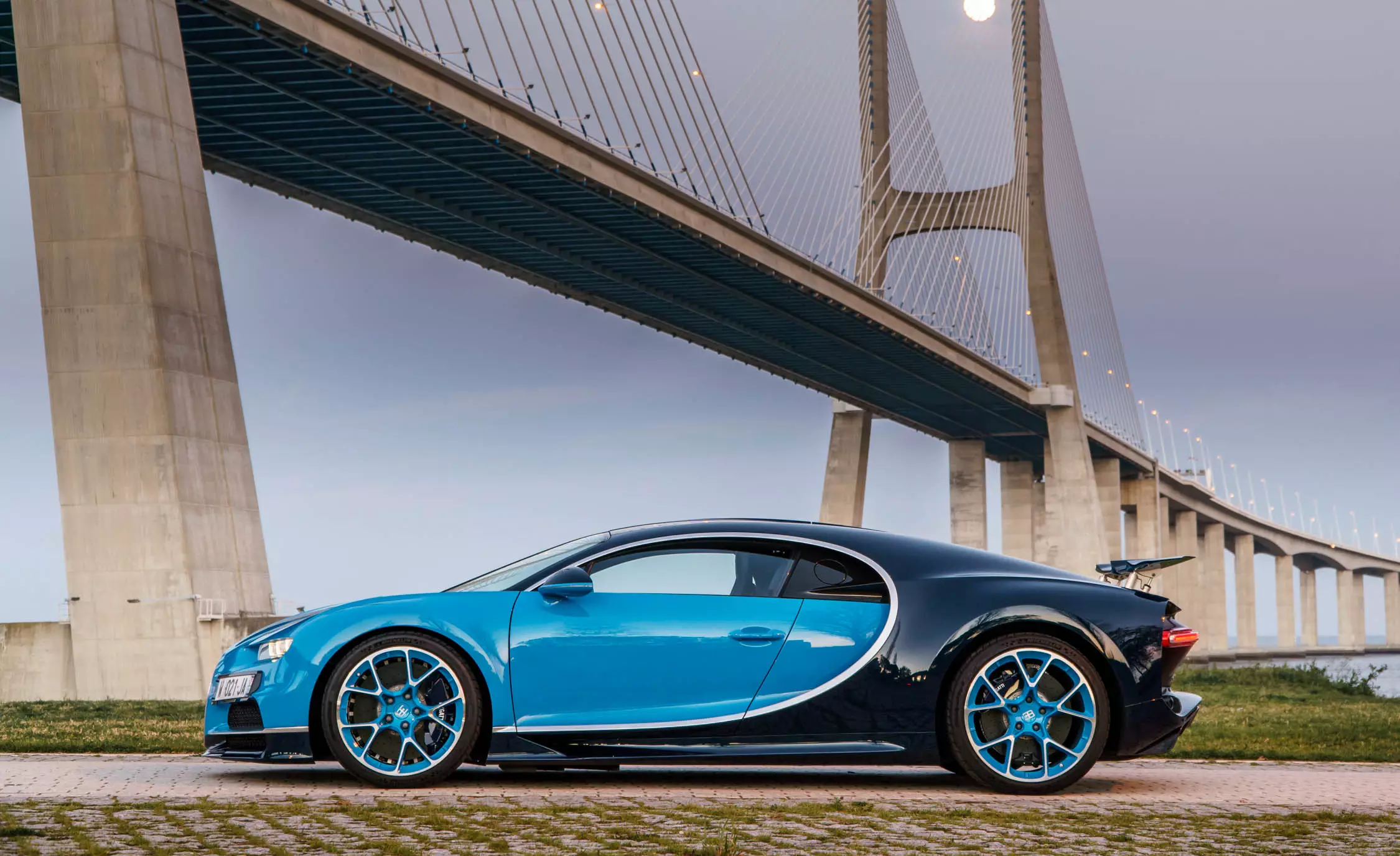
Las nuevas pinzas utilizan como material una aleación de titanio - Ti6AI4V de su nombre -, utilizada principalmente por la industria aeroespacial en componentes sometidos a enormes esfuerzos, ofreciendo un rendimiento muy superior al del aluminio. La resistencia a la tracción es, por supuesto, extremadamente alta: 1250 N / mm2 , lo que significa una fuerza aplicada de poco más de 125 kg por milímetro cuadrado sin que esta aleación de titanio se rompa.
La nueva pinza de freno tiene 41 cm de largo, 21 cm de ancho y 13,6 cm de alto y, además de su resistencia superior, tiene la gran ventaja de reducir significativamente el peso, afectando las siempre importantes masas no suspendidas. Pesa solo 2,9 kg contra 4,9 kg de la misma pieza de aluminio, lo que equivale a una reducción del 40%.
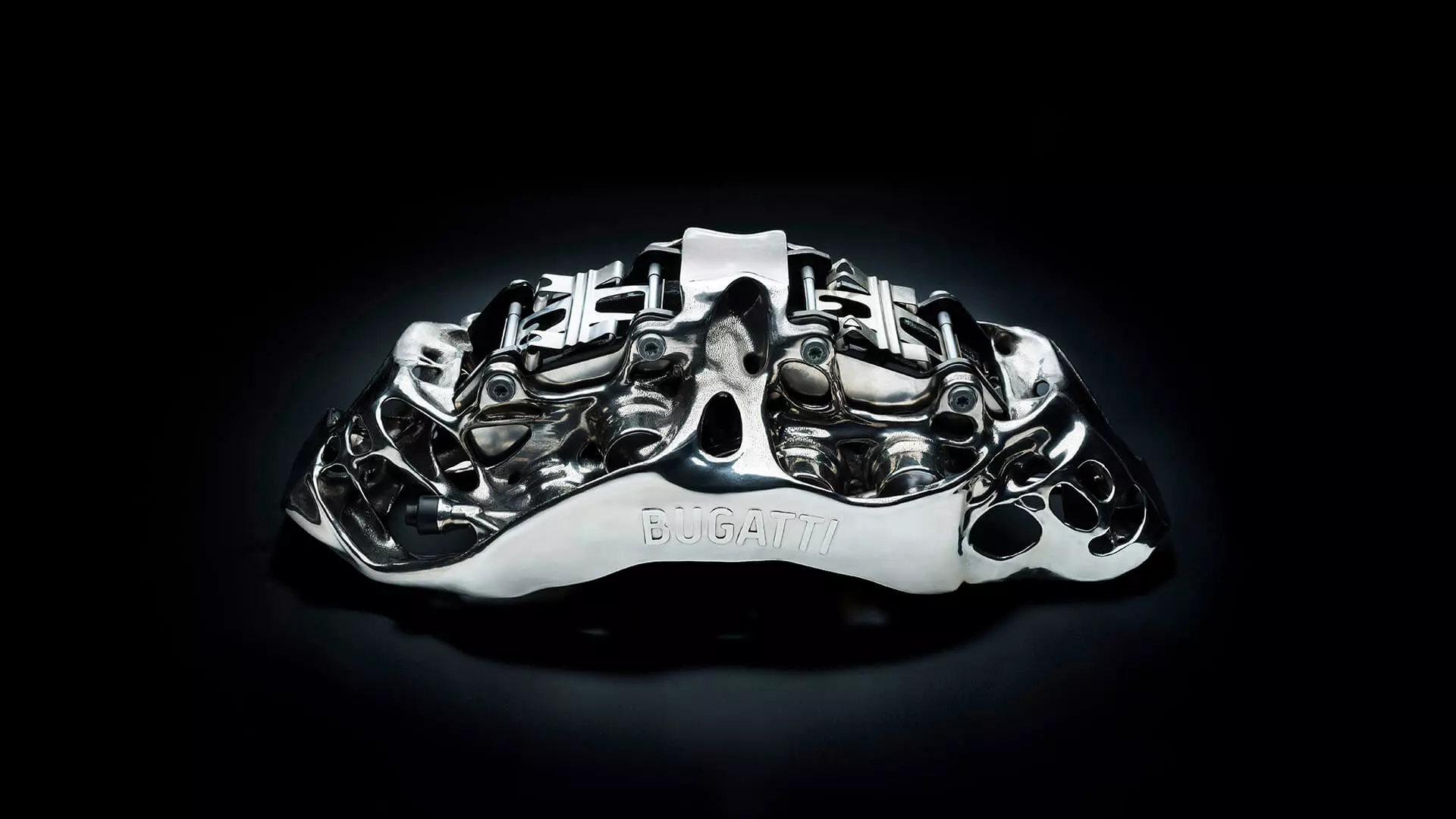
fabricación aditiva
Estas nuevas pinzas de freno de titanio son el resultado de la cooperación entre el Departamento de Desarrollo de Bugatti y Laser Zentrum Nord. Por primera vez, se utilizó titanio en lugar de aluminio para imprimir componentes de vehículos, lo que planteó sus desafíos. La alta resistencia del titanio ha sido la principal razón por la que no se ha utilizado este material, lo que obligó a recurrir a una impresora de alto rendimiento.Esta impresora 3D especial, ubicada en la Laser Zentrum Nord, que era la más grande del mundo capaz de manipular titanio al comienzo del proyecto, está equipada con cuatro láseres de 400W.
Cada pinza tarda 45 horas en imprimirse.
Durante este proceso, el polvo de titanio se deposita capa por capa, y los cuatro láseres derriten el polvo en la forma predeterminada. El material se enfría casi de inmediato y la abrazadera comienza a tomar forma.
En total se necesitan unas 2213 capas hasta completar la pieza.
Una vez depositada la última capa, el material sobrante se retira de la cámara de impresión, se limpia y se conserva para su reutilización. La pinza de freno, ya completa, permanece en la cámara, sostenida por un soporte, que le permite conservar su forma. Soporte que se retira después de que el componente recibe un tratamiento térmico (que alcanza los 700 ºC) para estabilizarlo y garantizar la resistencia deseada.
La superficie se acaba mediante una combinación de procesos mecánicos, físicos y químicos, que también contribuyen a mejorar su resistencia a la fatiga. Se necesitan más de 11 horas para optimizar los contornos de superficies funcionales, como los contactos de pistón, utilizando un centro de mecanizado de cinco ejes.
Bugatti, líder del grupo en impresión 3D
Con esto, Bugatti toma el liderazgo en el Grupo Volkswagen no solo en términos de tecnología de impresión 3D, sino también en términos de aplicaciones de alta tecnología. Una especie de laboratorio millonario y muy, muy poderoso ...
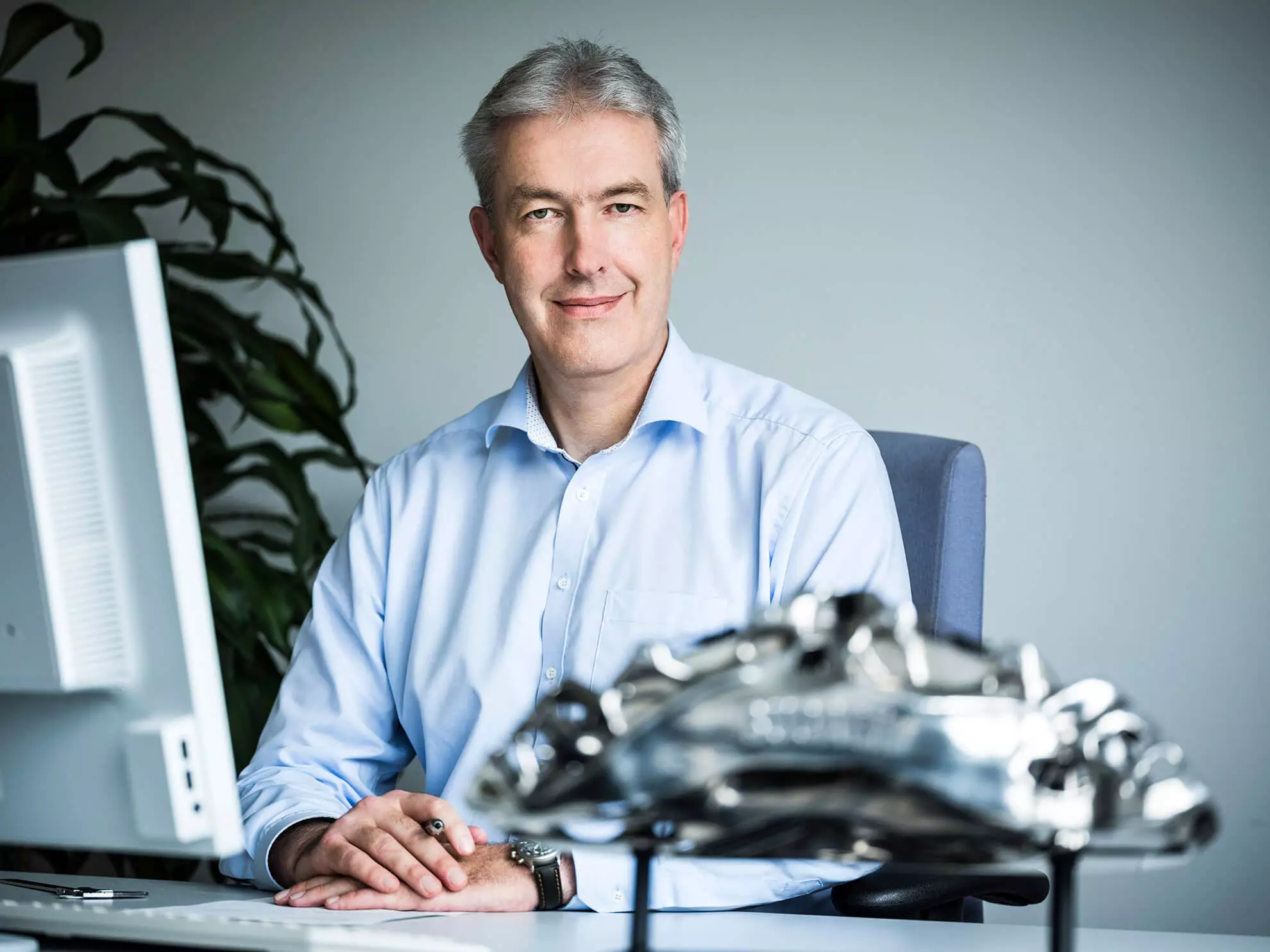
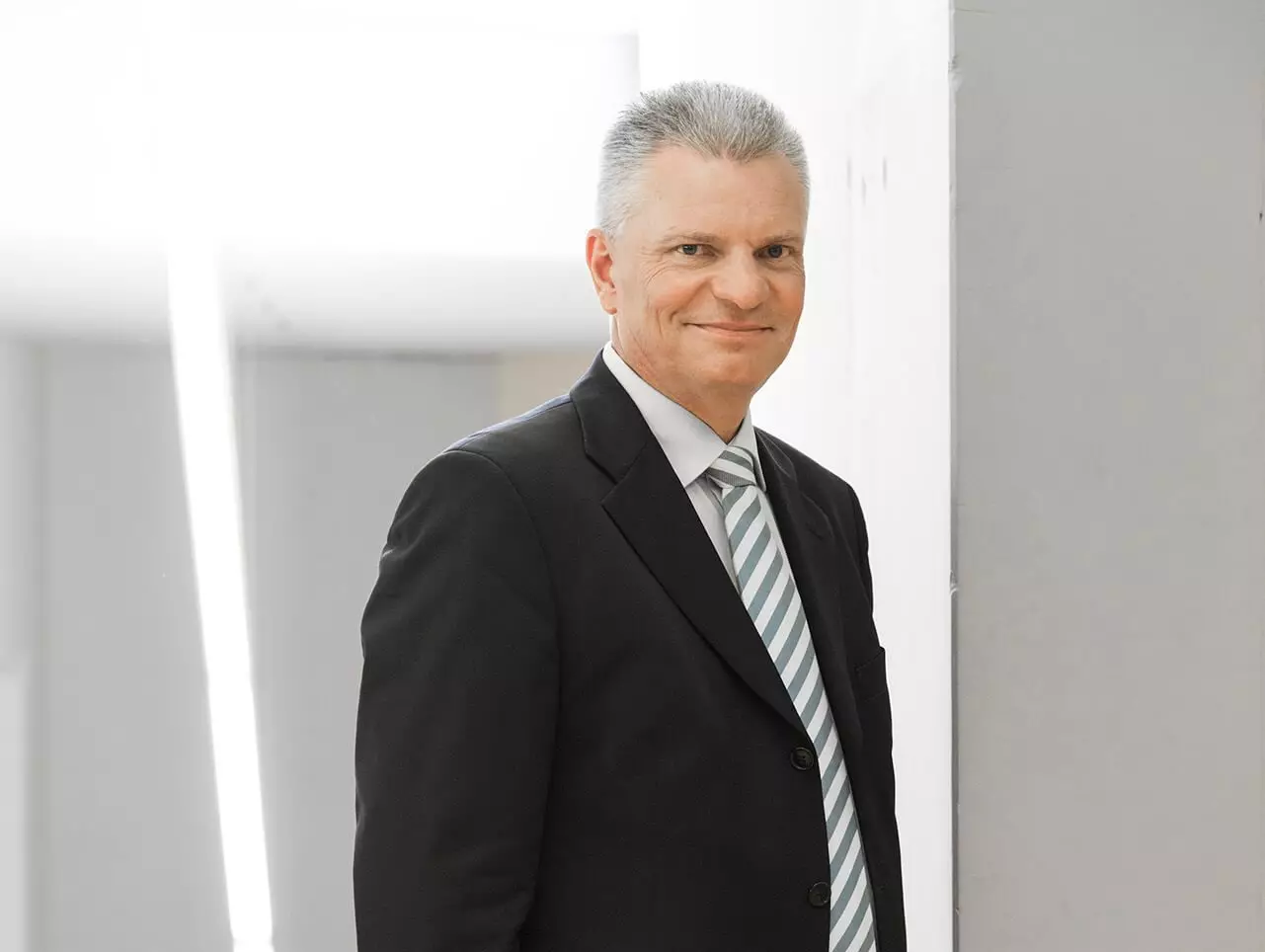