THE bugatti chiron це машина найвищої ланки — незважаючи на те, що її якось поранив на свою честь суперник шведського походження… — і щойно набрала ще один чудовий показник у вазі з додаванням нових титанових гальмівних супортів, які мають бути представлені в цій моделі пізніше в рік.
Як відомо, Bugatti Chiron вже був «власником» найбільших гальмівних супортів в автомобільній промисловості. Ці суппорти були виковані з блоку з високоміцного алюмінієвого сплаву з вісьмома титановими поршнями спереду і шістьма поршнями ззаду. Так далеко…
міцніше і легше
Тепер Bugatti зробила ще один крок вперед, розробивши титанові гальмівні супорти — все ще найбільші в галузі — які тепер є не тільки найбільший функціональний компонент титану, виготовлений за допомогою 3D-друку, оскільки це перший гальмівний супорт, виготовлений цим методом.
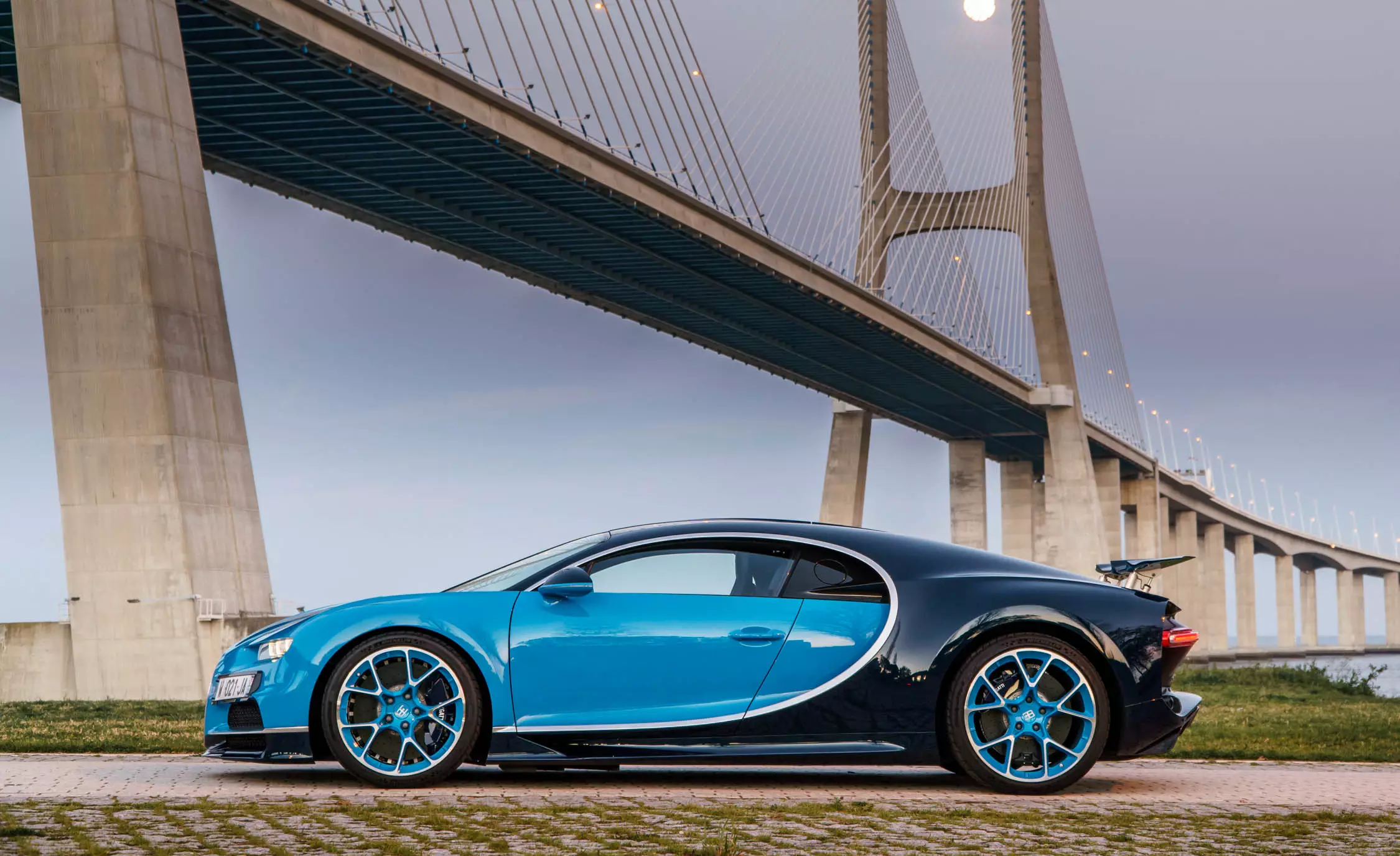
У нових пінцетах в якості матеріалу використовується титановий сплав — Ti6AI4V від його назви —, який використовується в основному в аерокосмічній промисловості для виготовлення компонентів, що піддаються величезному напруженню, що забезпечує продуктивність, яка набагато перевершує алюміній. Міцність на розрив, звичайно, надзвичайно висока: 1250 Н/мм2 , що означає прикладену силу трохи більше 125 кг на квадратний міліметр без розриву цього титанового сплаву.
Новий гальмівний супорт має довжину 41 см, ширину 21 см і висоту 13,6 см, і, на додаток до своєї чудової міцності, він має велику перевагу, що значно зменшує вагу, що впливає на завжди важливі непідресорені маси. Вага всього 2,9 кг проти 4,9 кг тієї ж алюмінієвої деталі, що дорівнює зниженню на 40%.
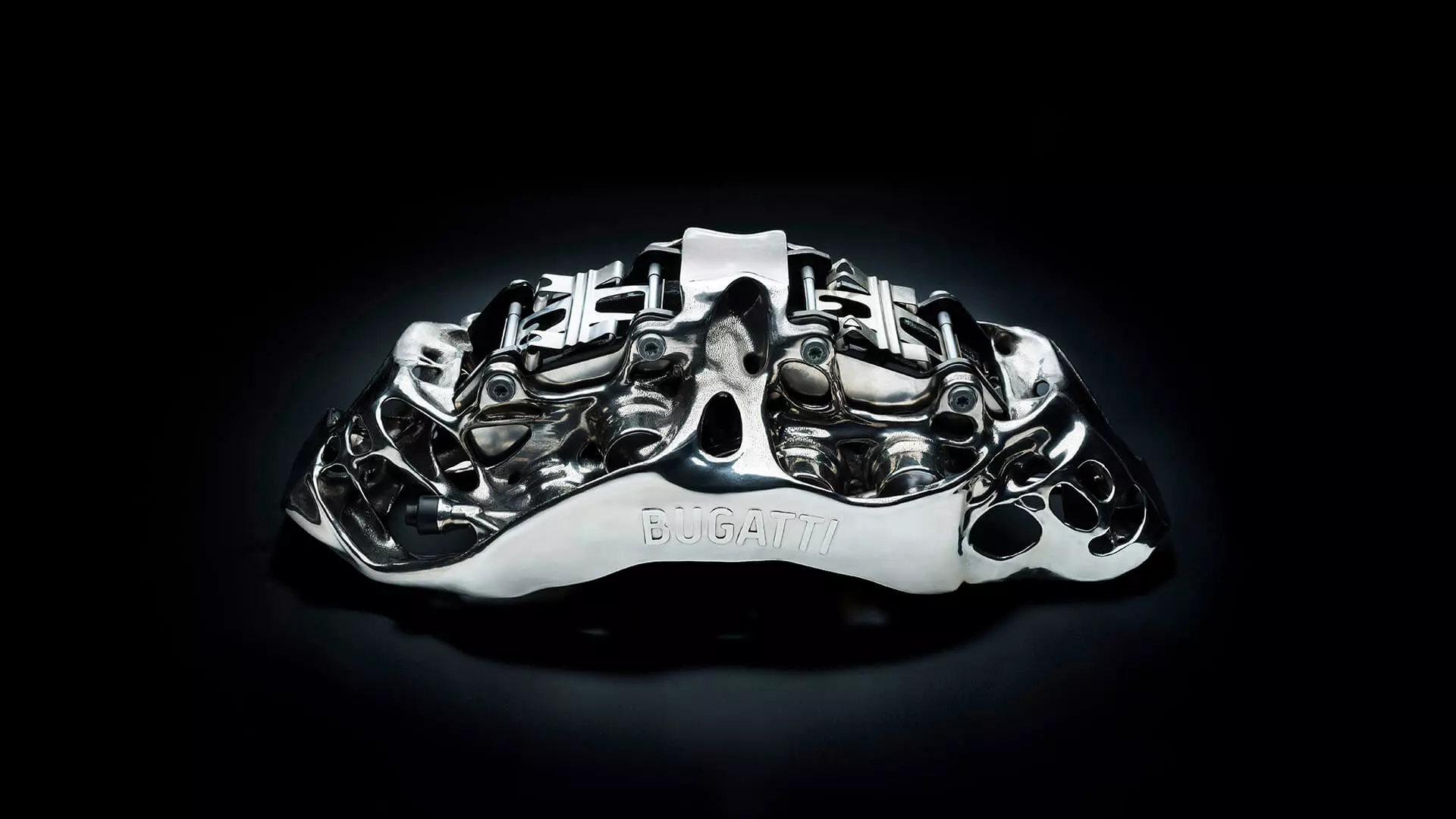
адитивне виробництво
Ці нові титанові гальмівні супорти є результатом співпраці між Департаментом розвитку Bugatti та Laser Zentrum Nord. Вперше титан був використаний замість алюмінію для друку компонентів автомобіля, що створило проблеми. Висока міцність титану була основною причиною, чому цей матеріал не використовувався, що змусило вдатися до високопродуктивного принтера.Цей спеціальний 3D-принтер, розташований на Laser Zentrum Nord, який на початку проекту був найбільшим у світі, здатним обробляти титан, оснащений чотирма лазерами потужністю 400 Вт.
Друк кожного пінцета займає 45 годин.
Під час цього процесу титановий порошок наноситься шар за шаром, при цьому чотири лазери розплавляють порошок до заданої форми. Матеріал майже відразу остигає, і затискач починає набувати форму.
Всього потрібно близько 2213 шарів, поки деталь не буде готова.
Після нанесення останнього шару надлишок матеріалу видаляється з друкарської камери, очищається і зберігається для повторного використання. Вже укомплектований гальмівний супорт залишається в камері, спираючись на опору, що дозволяє йому зберігати форму. Опора, яка видаляється після того, як компонент пройшов термічну обробку (яка досягає 700 ºC), щоб стабілізувати його та гарантувати бажаний опір.
Поверхня обробляється за допомогою комбінації механічних, фізичних і хімічних процесів, які також сприяють підвищенню її втомної міцності. Оптимізація контурів функціональних поверхонь, таких як поршневі контакти, за допомогою п’ятиосьового обробного центру займає більше 11 годин.
Bugatti, лідер групи з 3D-друку
Завдяки цьому Bugatti займає лідерство в Volkswagen Group не тільки з точки зору технології 3D-друку, але і з точки зору високотехнологічних застосувань. Якась лабораторія мільйонера і дуже-дуже потужна...
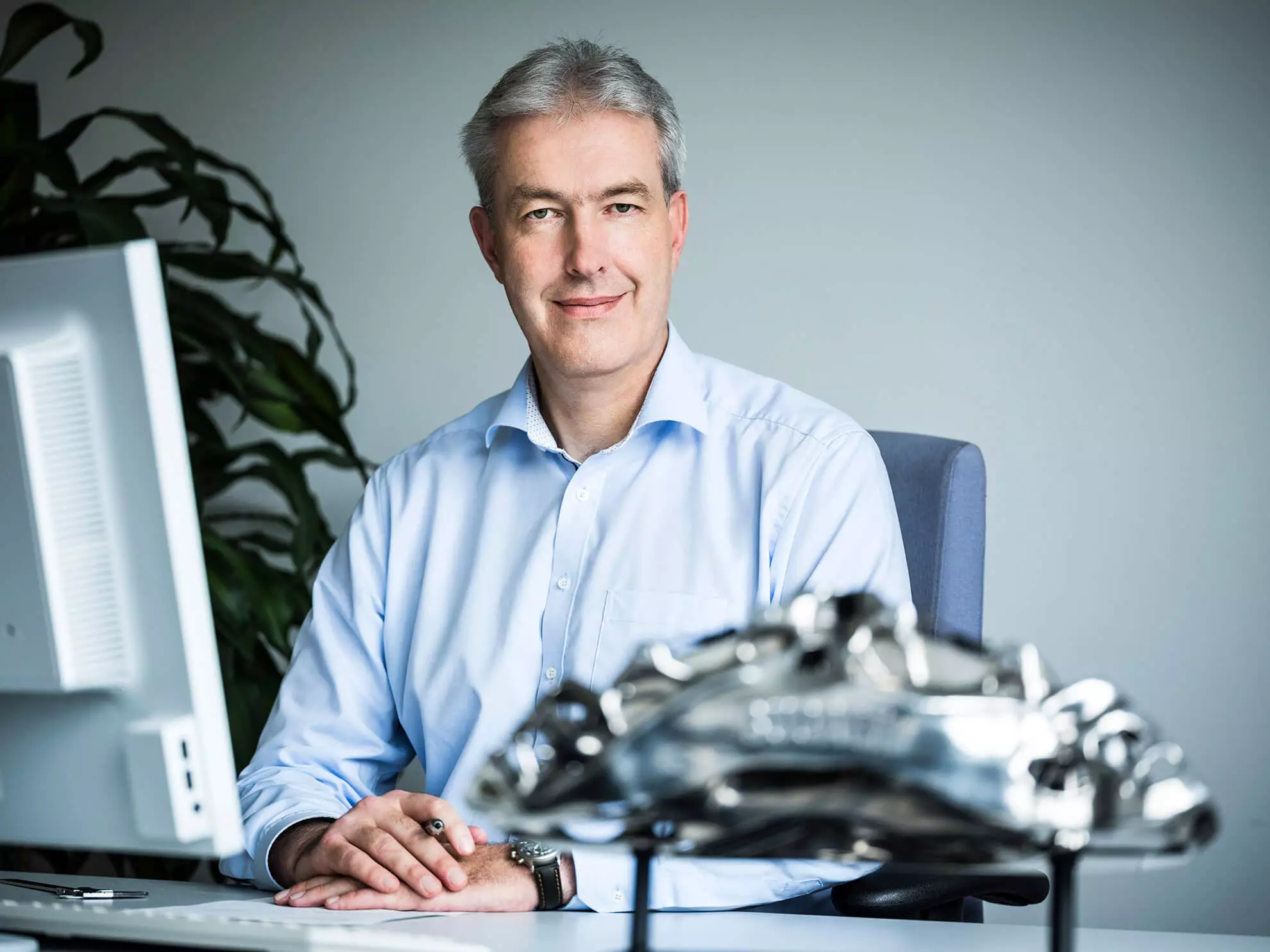
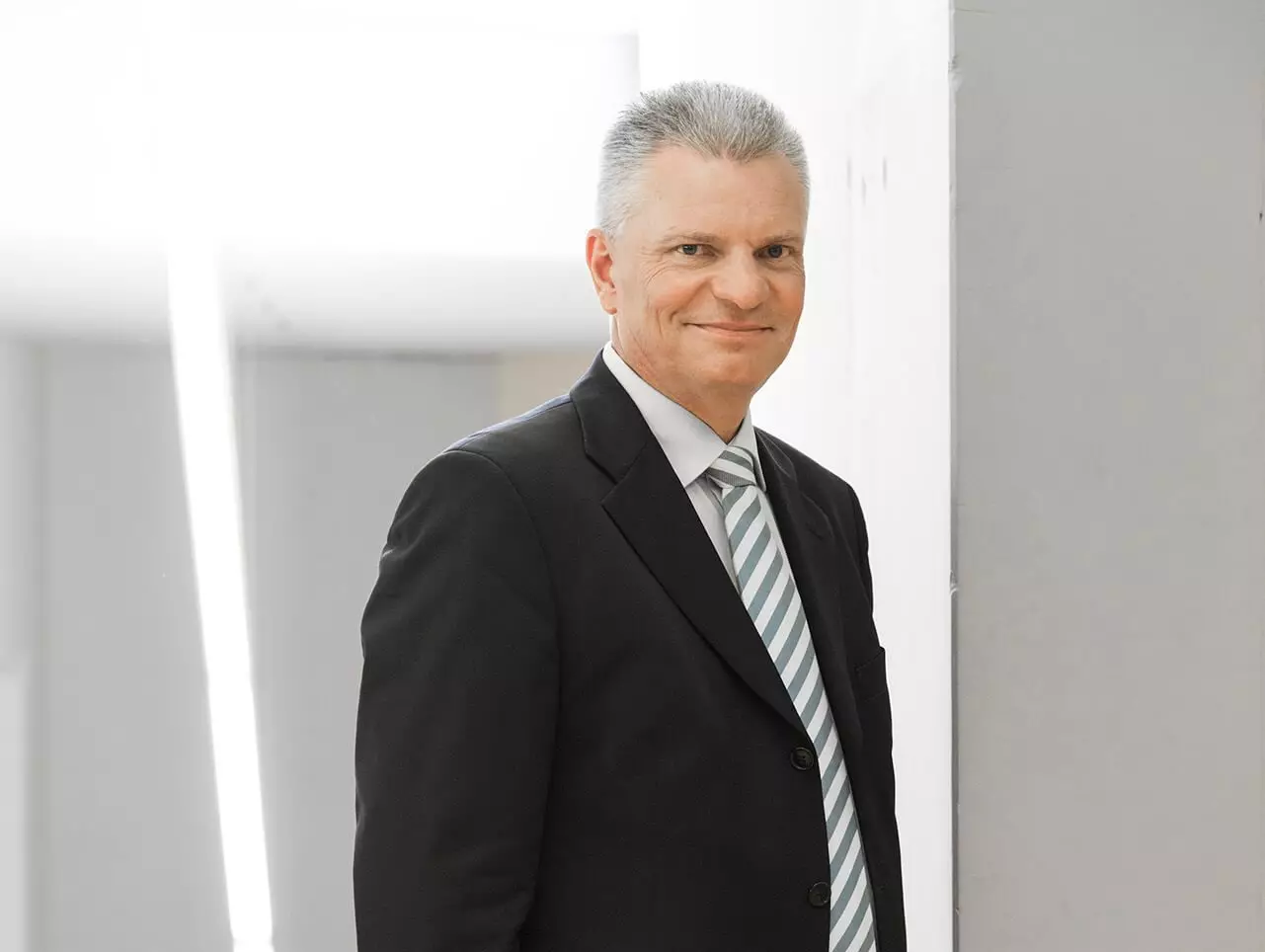