THE bugatti chiron este o mașină de superlative — chiar dacă a fost oarecum rănită în cinstea sa de un rival de origine suedeză... — și tocmai a câștigat încă un superlativ de greutate, cu adăugarea de noi etriere de frână din titan, care ar trebui introduse mai târziu în acest model. în anul.
După cum știți, Bugatti Chiron era deja „proprietarul” celor mai mari etriere de frână din industria auto. Aceste etriere au fost forjate dintr-un bloc de aliaj de aluminiu de înaltă rezistență, cu opt pistoane de titan în față și șase pistoane în spate. Pana acum…
mai puternică și mai ușoară
Bugatti a făcut acum un alt pas înainte, prin dezvoltarea etrierelor de frână din titan - încă cele mai mari din industrie - care acum nu sunt doar cea mai mare componentă funcțională din titan produsă prin imprimare 3D, deoarece este primul etrier de frână produs prin această metodă.
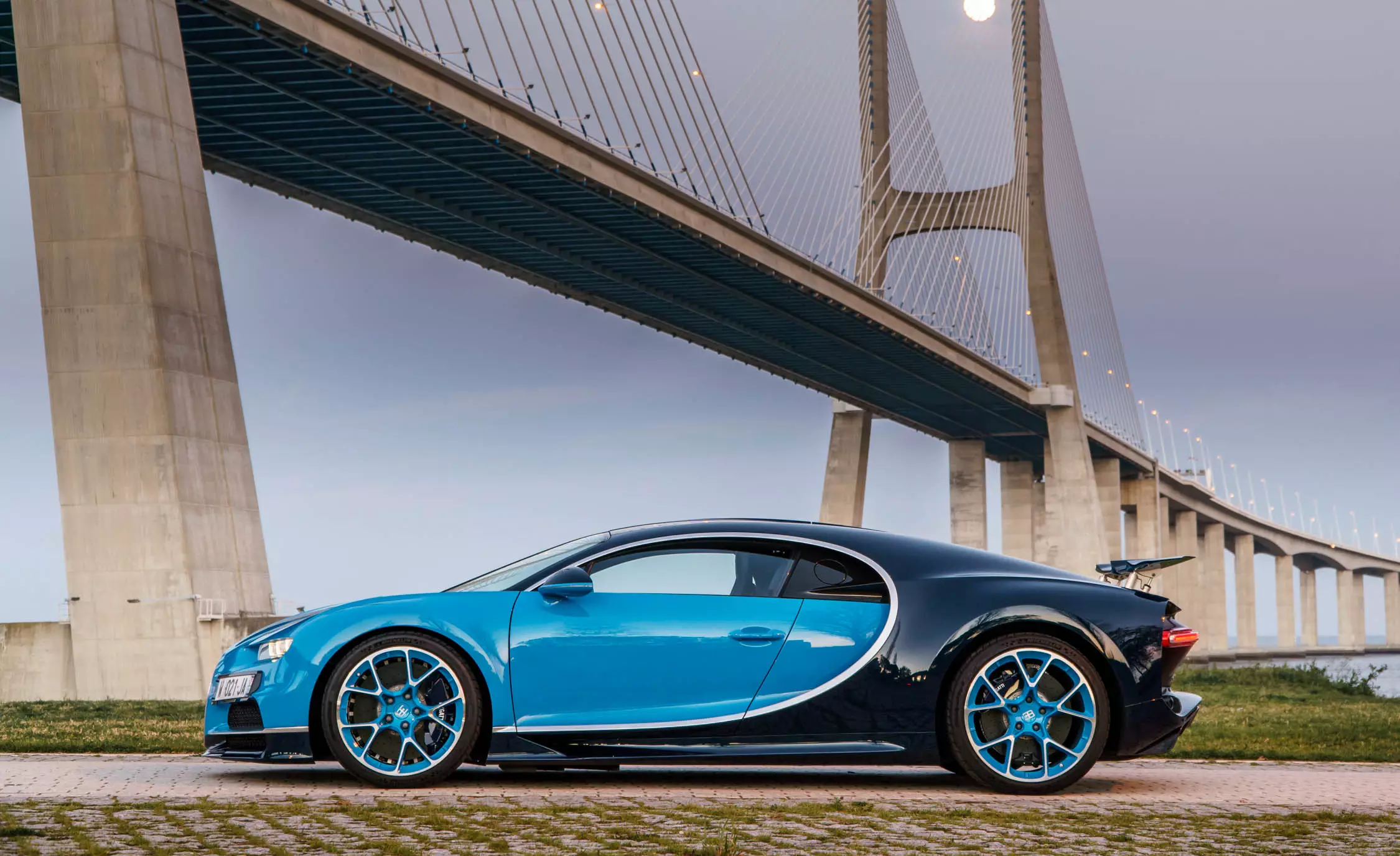
Noile pensete folosesc ca material un aliaj de titan — Ti6AI4V de la numele său —, folosit mai ales de industria aerospațială în componente supuse unor solicitări enorme, oferind o performanță mult superioară celei a aluminiului. Rezistența la tracțiune este, desigur, extrem de mare: 1250 N/mm2 , ceea ce înseamnă o forță aplicată de puțin peste 125 kg pe milimetru pătrat fără ca acest aliaj de titan să se rupă.
Noul etrier de frână are 41 cm lungime, 21 cm lățime și 13,6 cm înălțime și, pe lângă rezistența sa superioară, are marele avantaj de a reduce considerabil greutatea, afectând masele mereu importante neressortate. Cântărește doar 2,9 kg față de 4,9 kg din aceeași piesă de aluminiu, ceea ce echivalează cu o reducere de 40%.
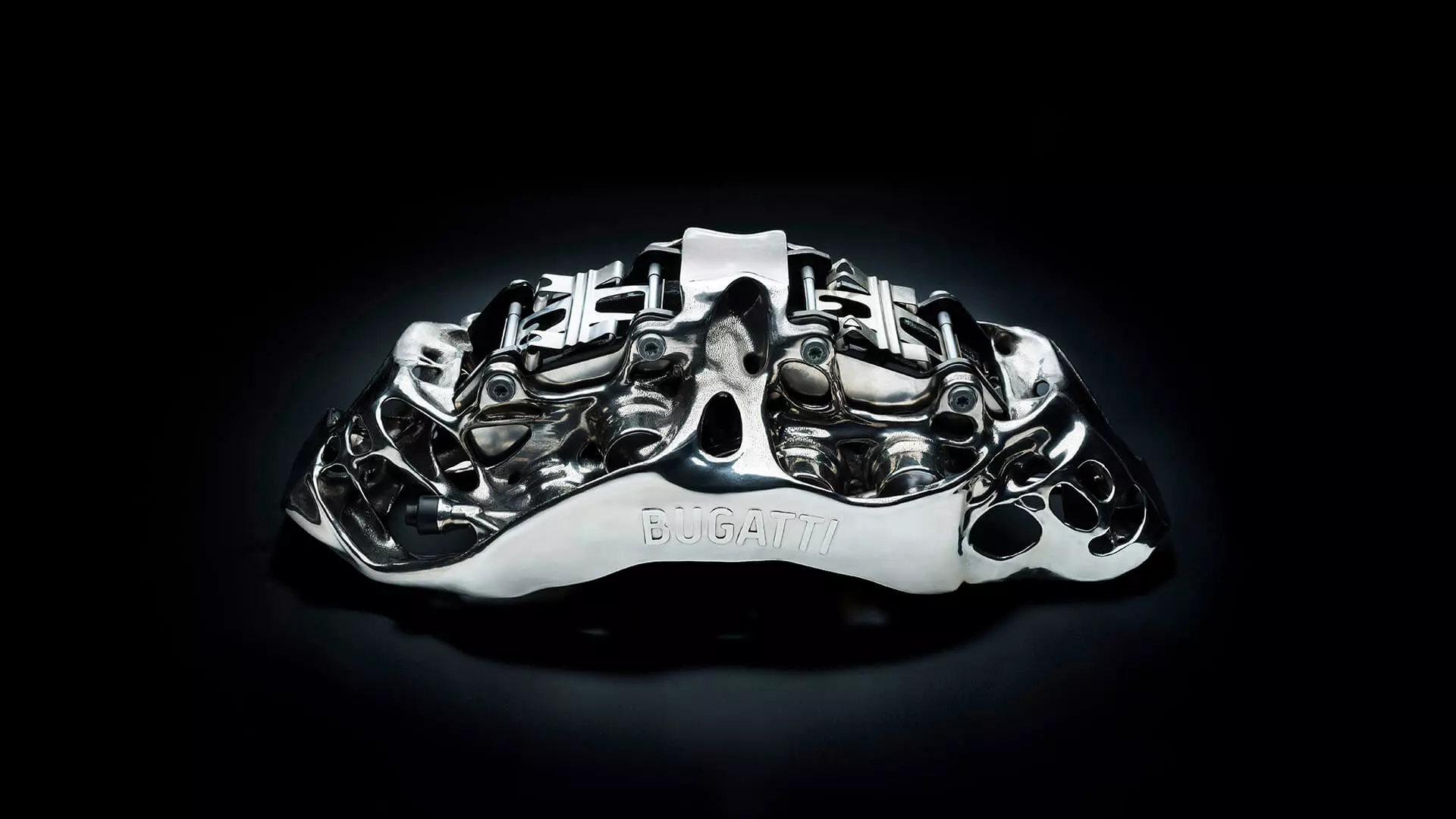
fabricație aditivă
Aceste noi etriere de frână din titan sunt rezultatul cooperării dintre Departamentul de Dezvoltare Bugatti și Laser Zentrum Nord. Pentru prima dată, titanul a fost folosit în loc de aluminiu pentru a imprima componentele vehiculelor, ceea ce a adus provocări. Rezistența ridicată a titanului a fost principalul motiv pentru care acest material nu a fost folosit, ceea ce a forțat recurgerea la o imprimantă de înaltă performanță.Această imprimantă 3D specială, situată pe Laser Zentrum Nord, care era cea mai mare din lume capabilă să manipuleze titanul la începutul proiectului, este echipată cu patru lasere de 400 W.
Tipărirea fiecărei pensete durează 45 de ore.
În timpul acestui proces, pulberea de titan este depusă strat cu strat, cele patru lasere topind pulberea în forma predeterminată. Materialul se răcește aproape imediat, iar clema începe să prindă contur.
În total, sunt necesare aproximativ 2213 straturi până la finalizarea piesei.
După ce ultimul strat a fost depus, excesul de material este îndepărtat din camera de imprimare, curățat și păstrat pentru reutilizare. Etrierul de frână, deja complet, rămâne în cameră, susținut de un suport, care îi permite să-și păstreze forma. Suport care este îndepărtat după ce componenta primește un tratament termic (care ajunge la 700 ºC) pentru a o stabiliza și a garanta rezistența dorită.
Suprafața este finisată printr-o combinație de procese mecanice, fizice și chimice, care contribuie, de asemenea, la îmbunătățirea rezistenței sale la oboseală. Este nevoie de mai mult de 11 ore pentru a optimiza contururile suprafețelor funcționale, cum ar fi contactele pistonului, folosind un centru de prelucrare cu cinci axe.
Bugatti, lider de grup în imprimarea 3D
Prin aceasta, Bugatti preia conducerea în Grupul Volkswagen nu numai în ceea ce privește tehnologia de imprimare 3D, ci și în ceea ce privește aplicațiile high-tech. Un fel de laborator milionar și foarte, foarte puternic...
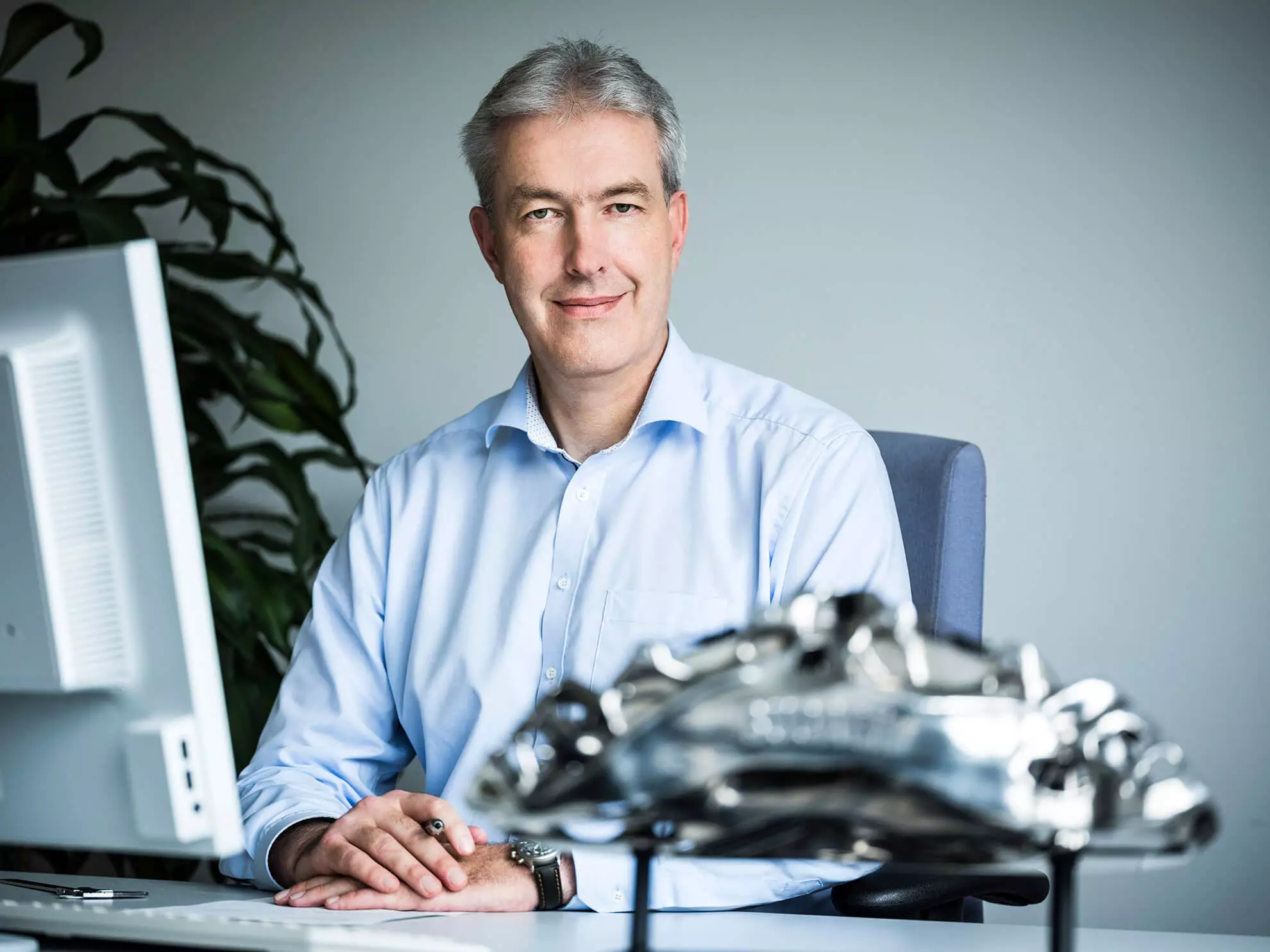
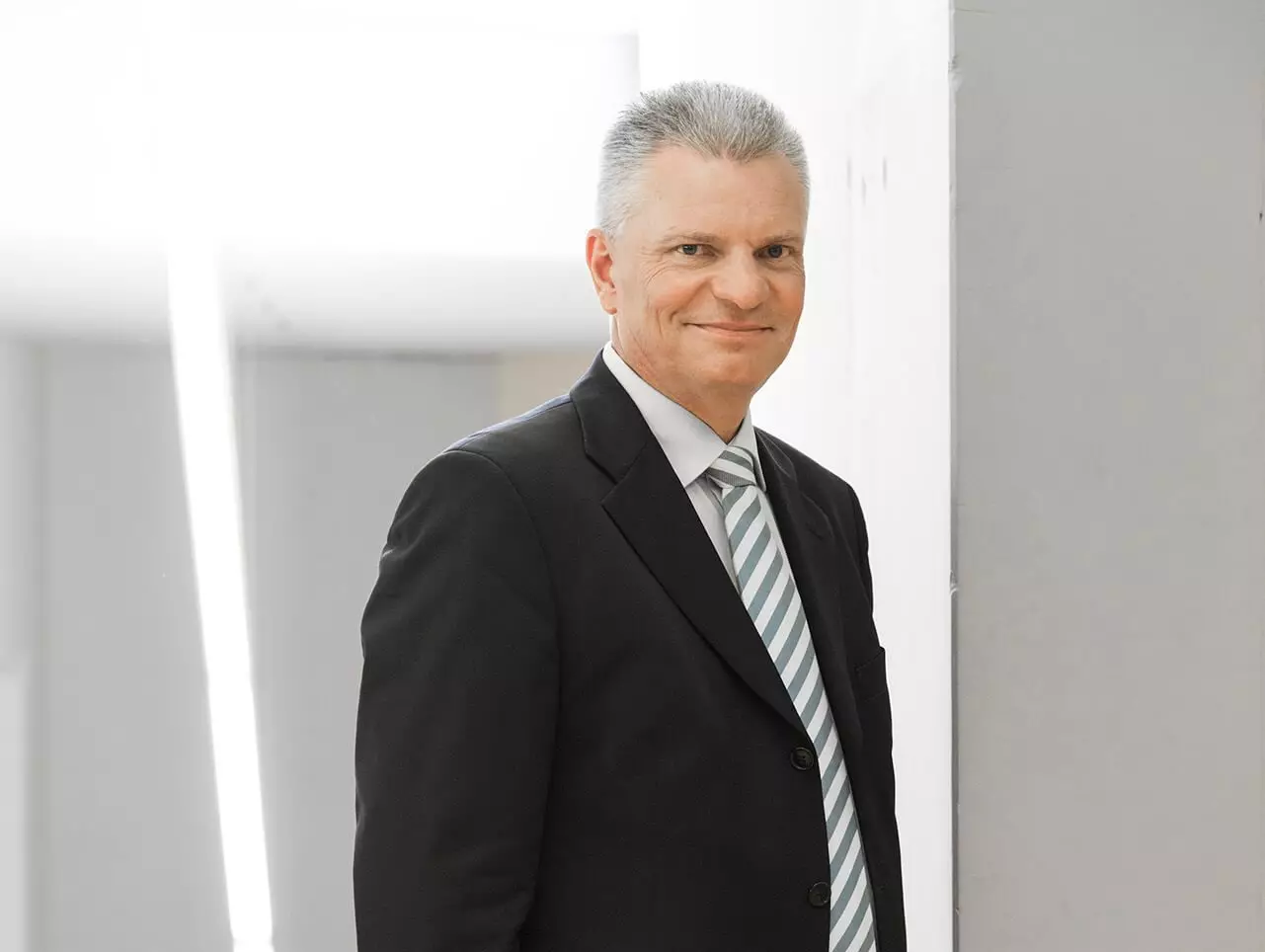