O bugatti chiron é unha máquina de superlativos —aínda que foi ferida na súa honra por un rival de orixe sueca...— e acaba de gañar outro superlativo de peso, coa incorporación de novas pinzas de freo de titanio, que deberían ser introducidas neste modelo máis tarde. no ano.
Como sabedes, o Bugatti Chiron xa era o "propietario" das pinzas de freo máis grandes da industria do automóbil. Estas pinzas foron forxadas a partir dun bloque de aliaxe de aluminio de alta resistencia con oito pistóns de titanio na parte dianteira e seis na parte traseira. Moi lonxe…
máis forte e lixeiro
Agora Bugatti deu outro paso adiante, desenvolvendo pinzas de freo de titanio, aínda as máis grandes da industria, que agora non son só o maior compoñente funcional en titanio producido mediante impresión 3D, xa que é a primeira pinza de freo que se produce mediante este método.
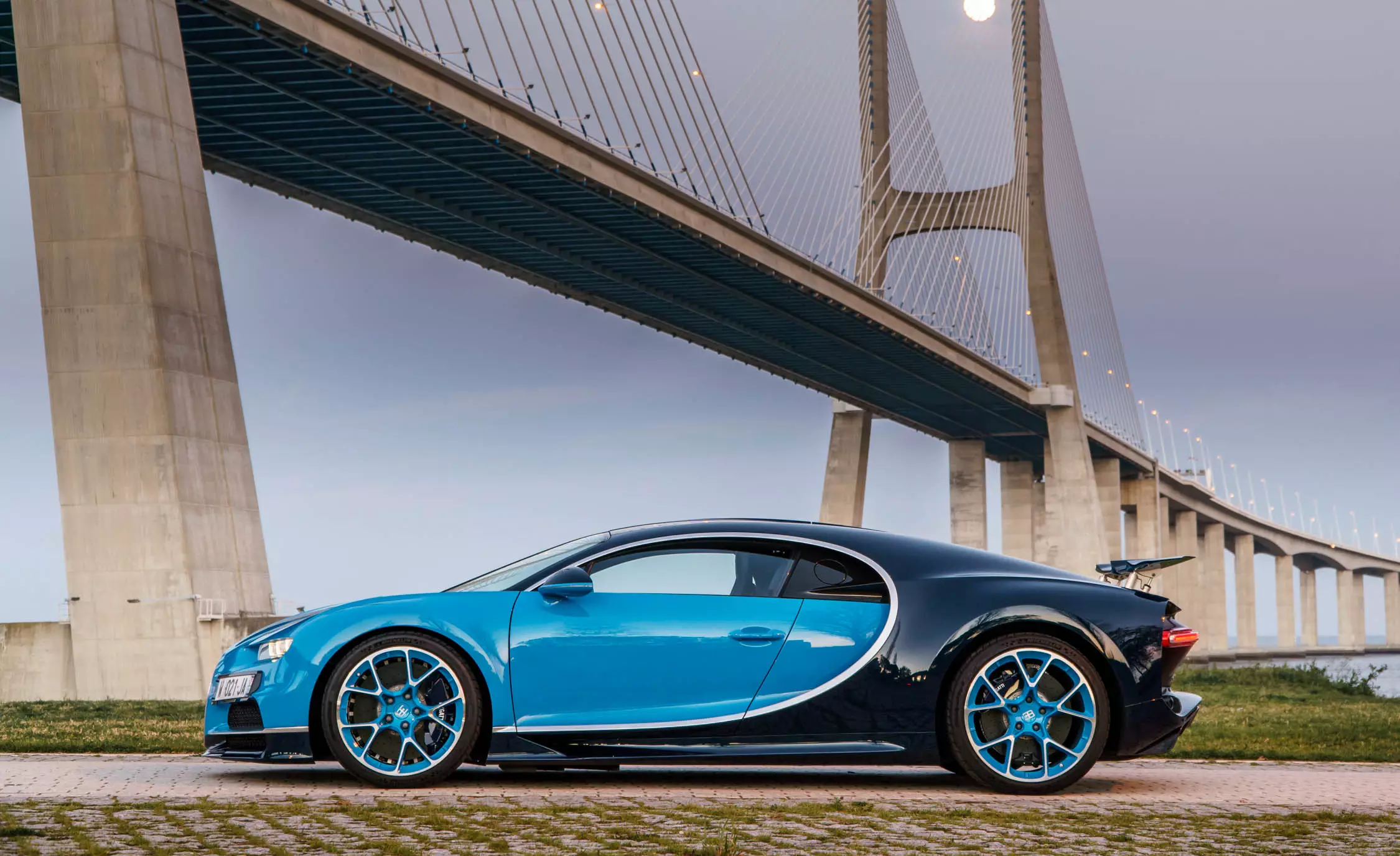
As novas pinzas empregan como material unha aliaxe de titanio —Ti6AI4V do seu nome—, utilizada principalmente pola industria aeroespacial en compoñentes sometidos a enormes tensións, ofrecendo un rendemento moi superior ao do aluminio. A resistencia á tracción é, por suposto, moi alta: 1250 N/mm2 , o que supón unha forza aplicada de algo máis de 125 kg por milímetro cadrado sen que se rompa esta aliaxe de titanio.
A nova pinza de freo ten 41 cm de longo, 21 cm de ancho e 13,6 cm de alto e, ademais da súa superior resistencia, ten a gran vantaxe de reducir significativamente o peso, afectando ás sempre importantes masas non suspendidas. Pesa só 2,9 kg fronte a 4,9 kg da mesma peza de aluminio, o que supón unha redución do 40%.
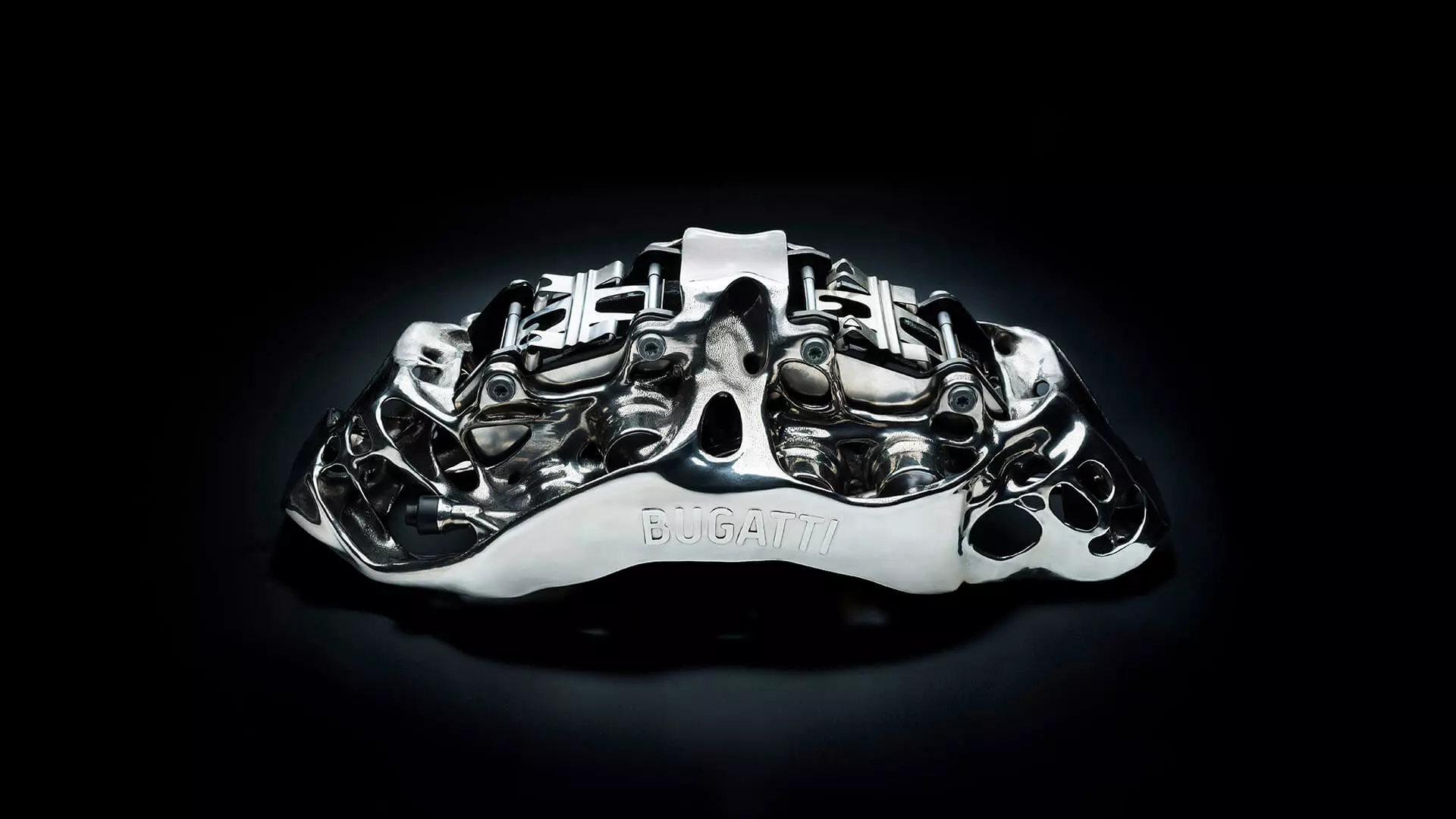
fabricación aditiva
Estas novas pinzas de freo de titanio son o resultado da cooperación entre o Departamento de Desenvolvemento de Bugatti e o Laser Zentrum Nord. Por primeira vez, utilizouse o titanio en lugar do aluminio para imprimir compoñentes dos vehículos, o que provocou os seus desafíos. A alta resistencia do titanio foi a principal razón pola que non se utilizou este material, o que obrigou ao recurso a unha impresora de alto rendemento.Esta impresora 3D especial, situada no Laser Zentrum Nord, que era a máis grande do mundo capaz de manexar titanio ao comezo do proxecto, está equipada con catro láseres de 400 W.
Cada pinza tarda 45 horas en imprimirse.
Durante este proceso, o po de titanio é depositado capa por capa, cos catro láseres que funden o po na forma predeterminada. O material arrefríase case de inmediato e a abrazadeira comeza a tomar forma.
En total son necesarias unhas 2213 capas ata completar a peza.
Despois de depositar a última capa, o material sobrante elimínase da cámara de impresión, límpase e consérvase para a súa reutilización. A pinza de freo, xa completa, permanece na cámara, apoiada por un soporte, que lle permite conservar a súa forma. Soporte que se retira despois de que o compoñente recibe un tratamento térmico (que chega aos 700 ºC) para estabilizalo e garantir a resistencia desexada.
A superficie realízase mediante unha combinación de procesos mecánicos, físicos e químicos, que tamén contribúen a mellorar a súa resistencia á fatiga. Leva máis de 11 horas optimizar os contornos das superficies funcionais, como os contactos dos pistóns, mediante un centro de mecanizado de cinco eixes.
Bugatti, líder do grupo en impresión 3D
Con isto, Bugatti toma o liderado do Grupo Volkswagen non só en tecnoloxía de impresión 3D, senón tamén en aplicacións de alta tecnoloxía. Unha especie de laboratorio millonario e moi, moi poderoso...
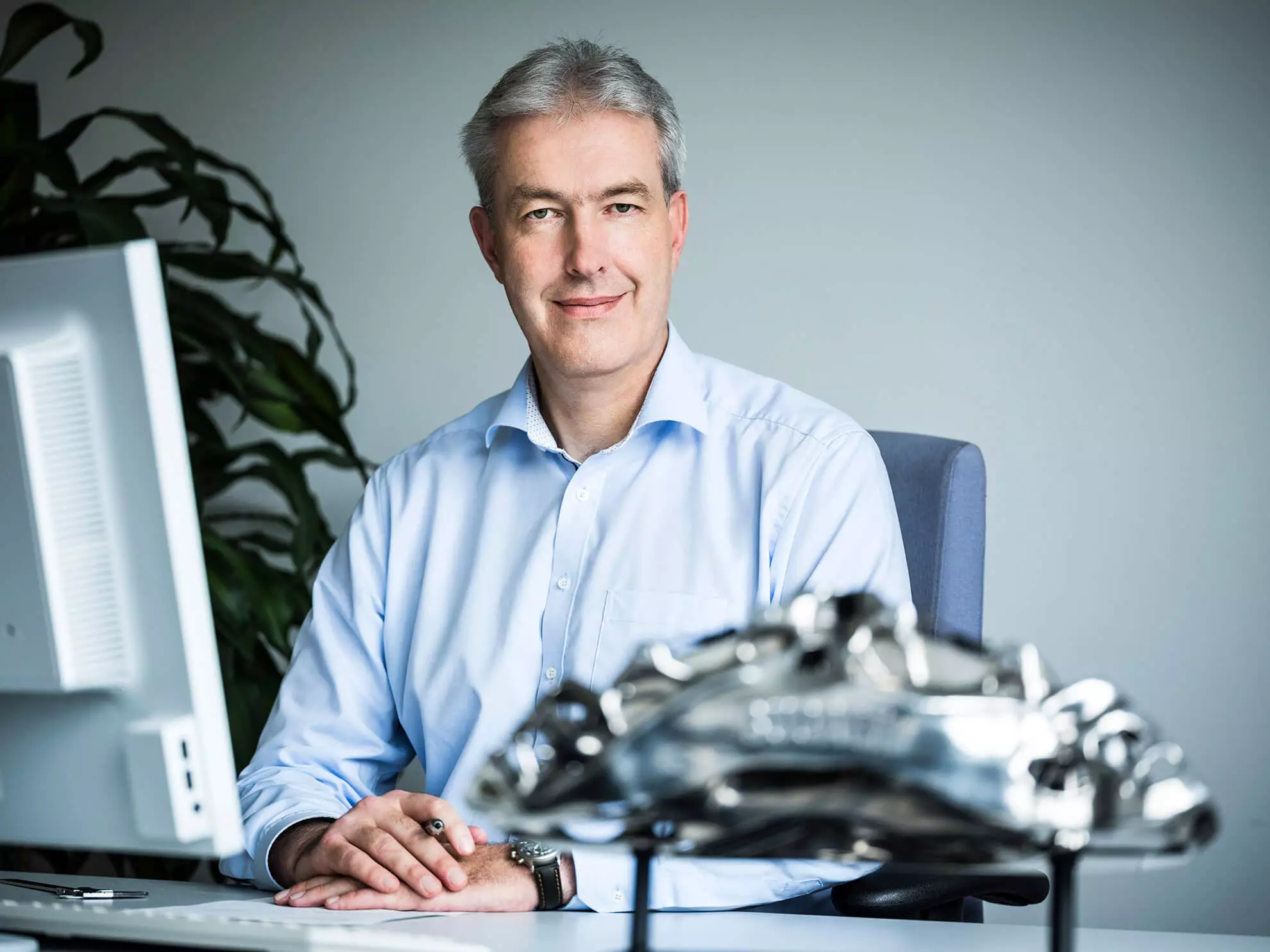
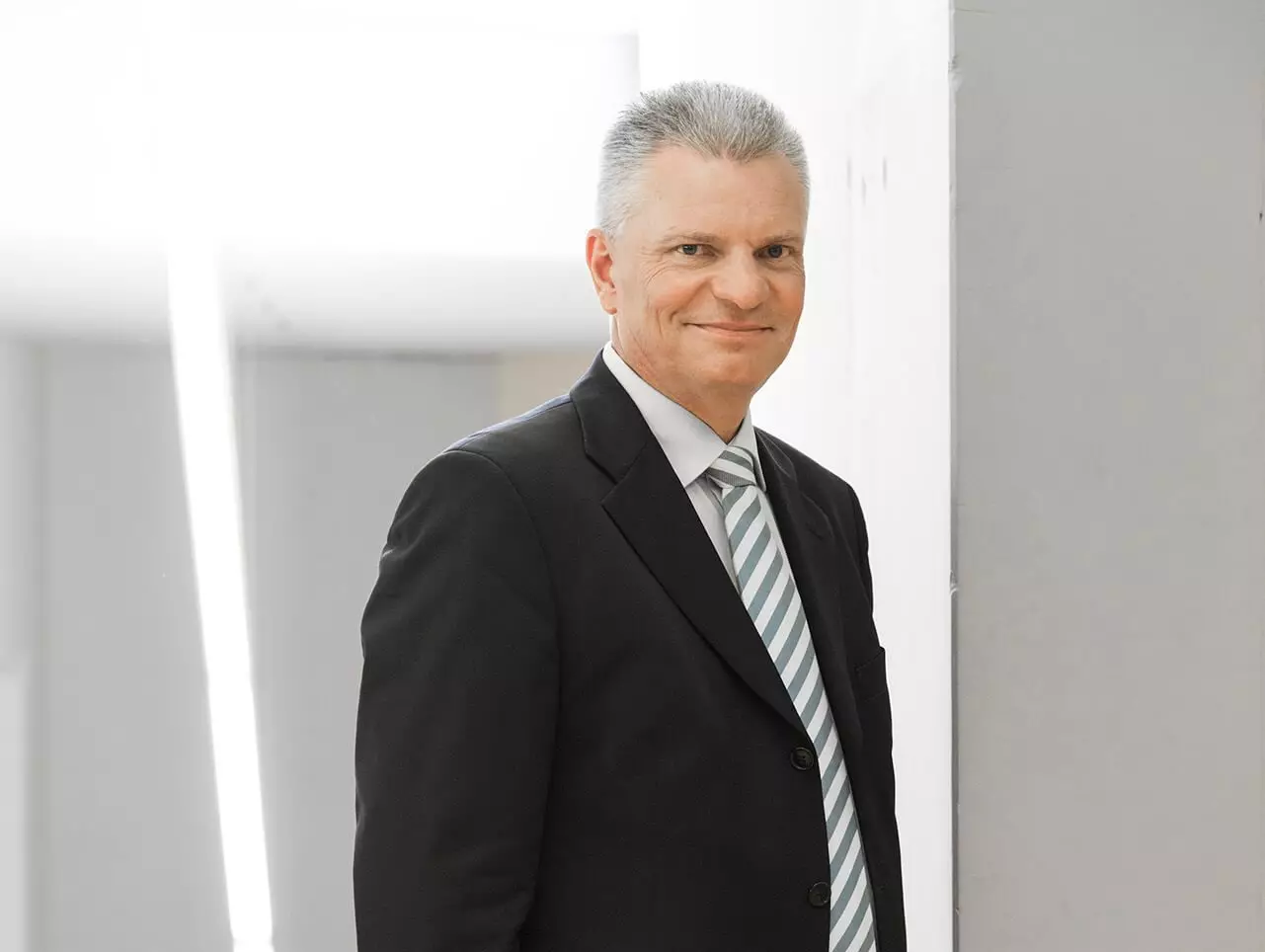