НА бугати хирон е машина на суперлативи - иако беше некако ранета во нејзина чест од ривал со шведско потекло... - и штотуку доби уште еден суперлатив на тежина, со додавање на нови титаниумски сопирачки клешти, кои треба да бидат претставени во овој модел подоцна во годината.
Како што знаете, на Bugatti Chiron веќе беше „сопственик“ на најголемите сопирачки клешти во автомобилската индустрија. Овие дебеломер беа ковани од блок од алуминиумска легура со висока јачина со осум титаниумски клипови напред и шест клипови назад. До сега…
посилни и полесни
Bugatti сега направи уште еден чекор напред, развивајќи титаниумски сопирачки клешти - сè уште најголеми во индустријата - кои сега не се само најголемата функционална компонента во титаниум произведена преку 3D печатење, бидејќи е првата кочница што е произведена со овој метод.
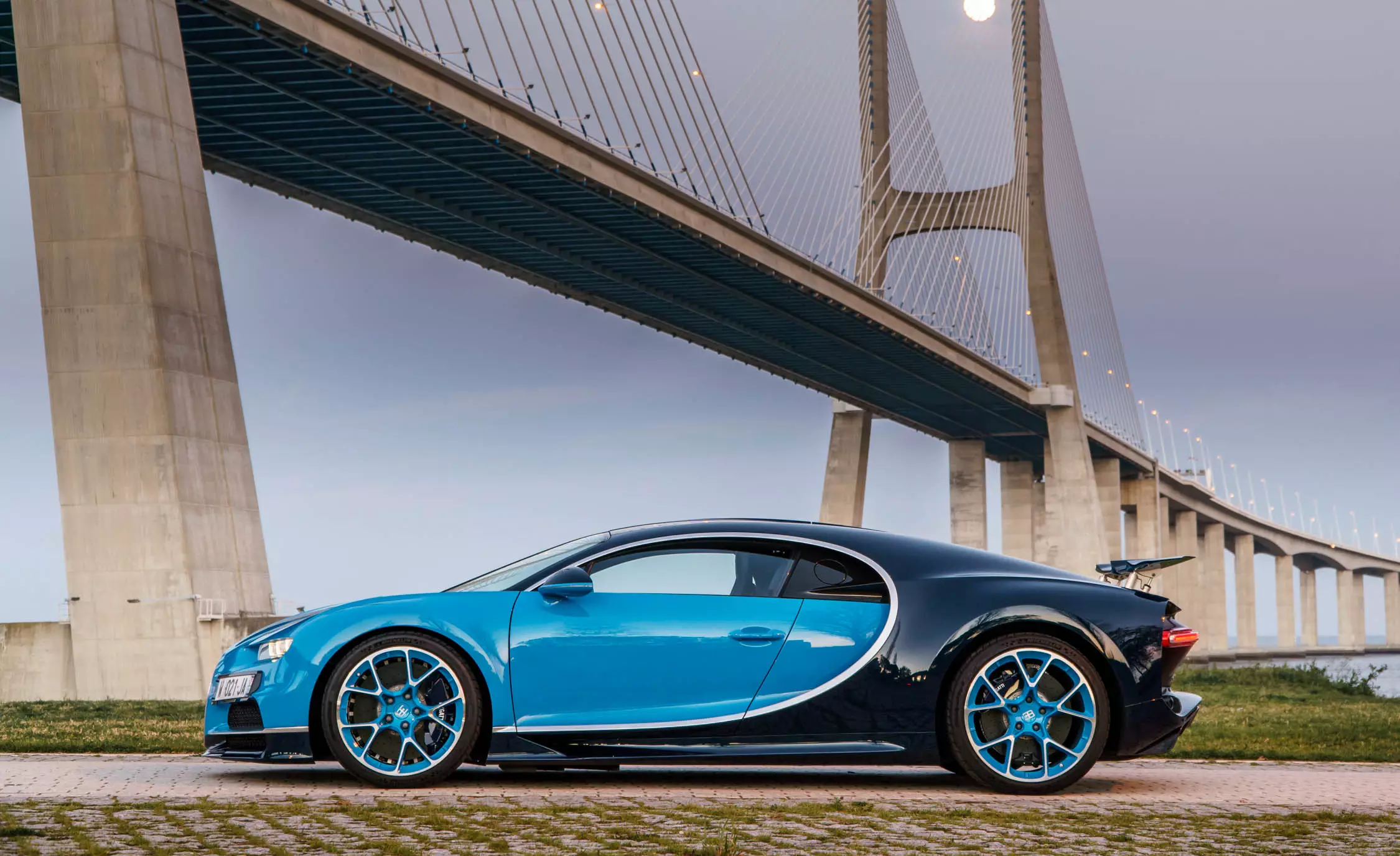
Новите пинцети како материјал користат легура на титаниум - Ti6AI4V од неговото име -, користена главно од воздушната индустрија во компоненти кои се подложни на огромен стрес, нудејќи перформанси далеку подобри од оние на алуминиумот. Јачината на истегнување е, се разбира, исклучително висока: 1250 N/mm2 , што значи применета сила од нешто повеќе од 125 kg на квадратен милиметар без оваа легура на титаниум да се скрши.
Новиот дебеломер на сопирачките е долг 41 cm, широк 21 cm и висок 13,6 cm и, покрај својата супериорна цврстина, има и голема предност што значително ја намалува тежината, што влијае на секогаш важните неизраснати маси. Тежи само 2,9 кг против 4,9 kg од истиот алуминиумски дел, што е еднакво на намалување од 40%.
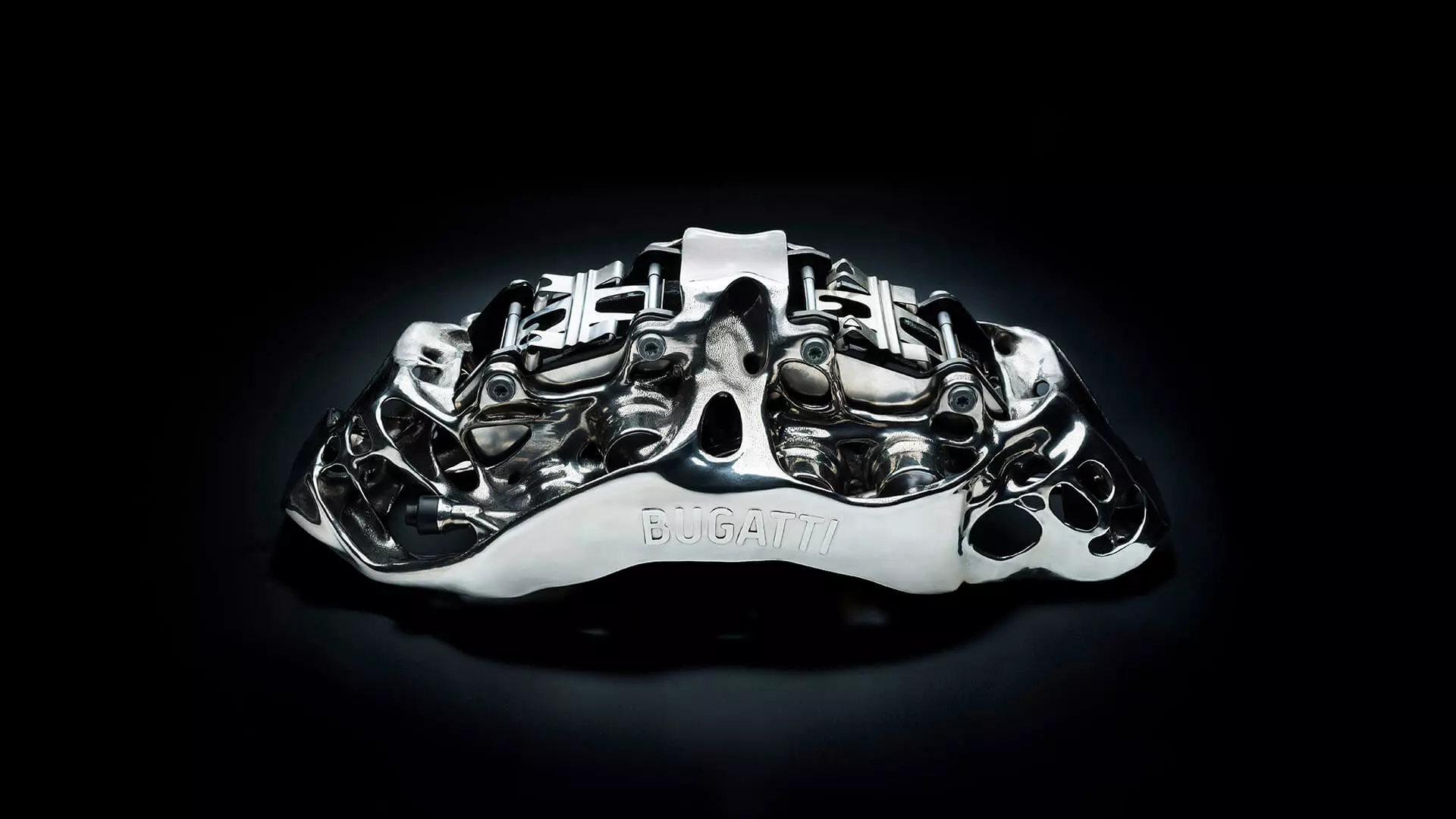
производство на адитиви
Овие нови титаниумски сопирачки клешти се резултат на соработката помеѓу Одделот за развој на Bugatti и Laser Zentrum Nord. За прв пат, наместо алуминиум се користеше титаниум за печатење на компоненти на возилото, што ги донесе своите предизвици. Високата јачина на титаниумот е главната причина зошто овој материјал не се користи, што го принуди прибегнувањето кон печатач со високи перформанси.Овој специјален 3D печатач, сместен на Laser Zentrum Nord, кој беше најголемиот во светот способен да ракува со титаниум на почетокот на проектот, е опремен со четири ласери од 400W.
Секоја пинцета трае 45 часа за печатење.
Во текот на овој процес, титаниумскиот прав се таложи слој по слој, при што четирите ласери го топат прашокот во однапред одредена форма. Материјалот се лади речиси веднаш, а стегачот почнува да се обликува.
Севкупно се потребни околу 2213 слоеви додека парчето не се заврши.
Откако ќе се наталожи последниот слој, вишокот материјал се отстранува од комората за печатење, се чисти и се чува за повторна употреба. Дебелината на сопирачката, веќе завршена, останува во комората, поддржана од потпора, што му овозможува да ја зачува својата форма. Поддршката што се отстранува откако компонентата ќе добие термичка обработка (која достигнува 700 ºC) за да се стабилизира и да се гарантира посакуваниот отпор.
Површината е завршена преку комбинација на механички, физички и хемиски процеси, кои исто така придонесуваат за подобрување на нејзината сила на замор. Потребни се повеќе од 11 часа за да се оптимизираат контурите на функционалните површини, како што се контактите на клипот, користејќи центар за обработка со пет оски.
Bugatti, лидер на групата во 3D печатење
Со ова, Bugatti го презема водството во групацијата Volkswagen не само во однос на технологијата за 3D печатење, туку и во однос на високотехнолошките апликации. Еден вид милионерска лабораторија и многу, многу моќна...
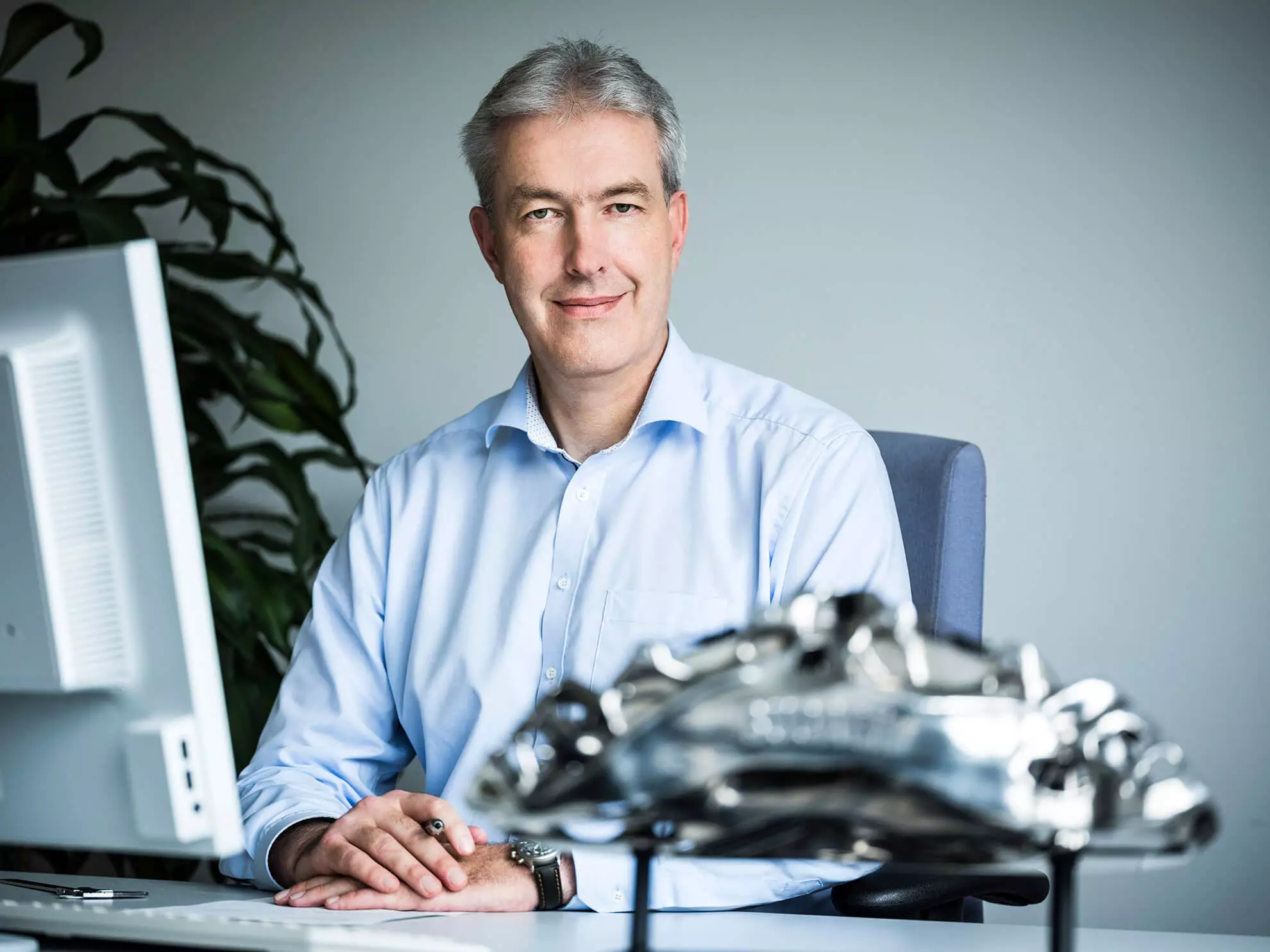
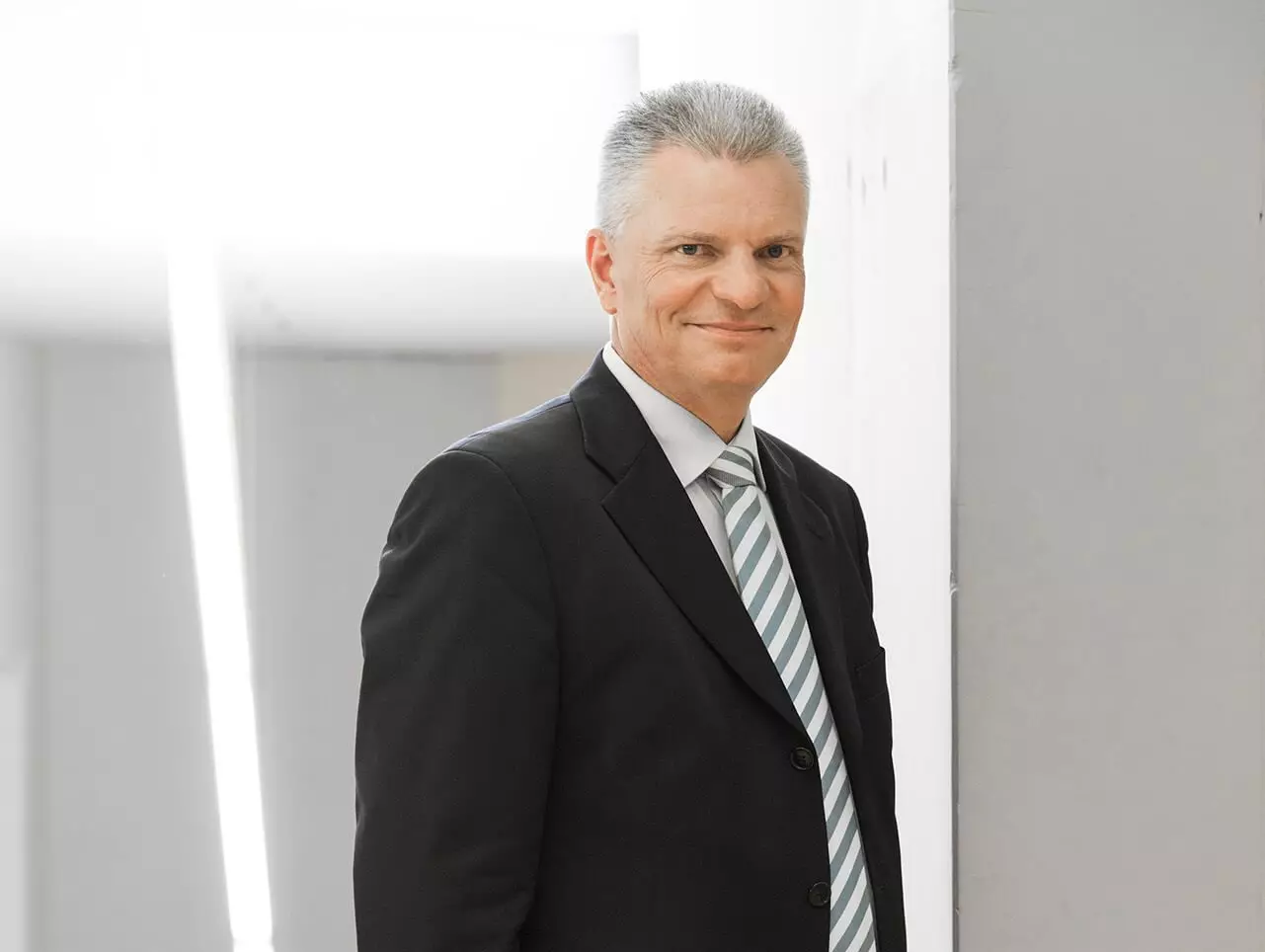