THE bugatti chiron бұл артықшылықтар машинасы — оны швед текті қарсыласы оның құрметіне қандай да бір жолмен жаралағанымен... — және осы модельге кейінірек енгізілуі тиіс жаңа титан тежегіш калибрлері қосылған салмақтың тағы бір артықшылығына ие болды. жылы.
Өздеріңіз білетіндей, Bugatti Chiron қазірдің өзінде автомобиль өнеркәсібіндегі ең үлкен тежегіш калибрлерінің «иесі» болды. Бұл калибрлер алдыңғы жағында сегіз титан поршені және артқы жағында алты поршені бар жоғары берік алюминий қорытпасынан жасалған блоктан жасалған. Осы уакытқа дейін…
күштірек және жеңілірек
Bugatti енді титанды тежегіш калибрлерін жасау арқылы алға тағы бір қадам жасады - әлі де саладағы ең үлкен - олар қазір ғана емес. 3D басып шығару арқылы өндірілген титандағы ең үлкен функционалдық құрамдас, өйткені ол осы әдіспен шығарылатын алғашқы тежегіш суппорт.
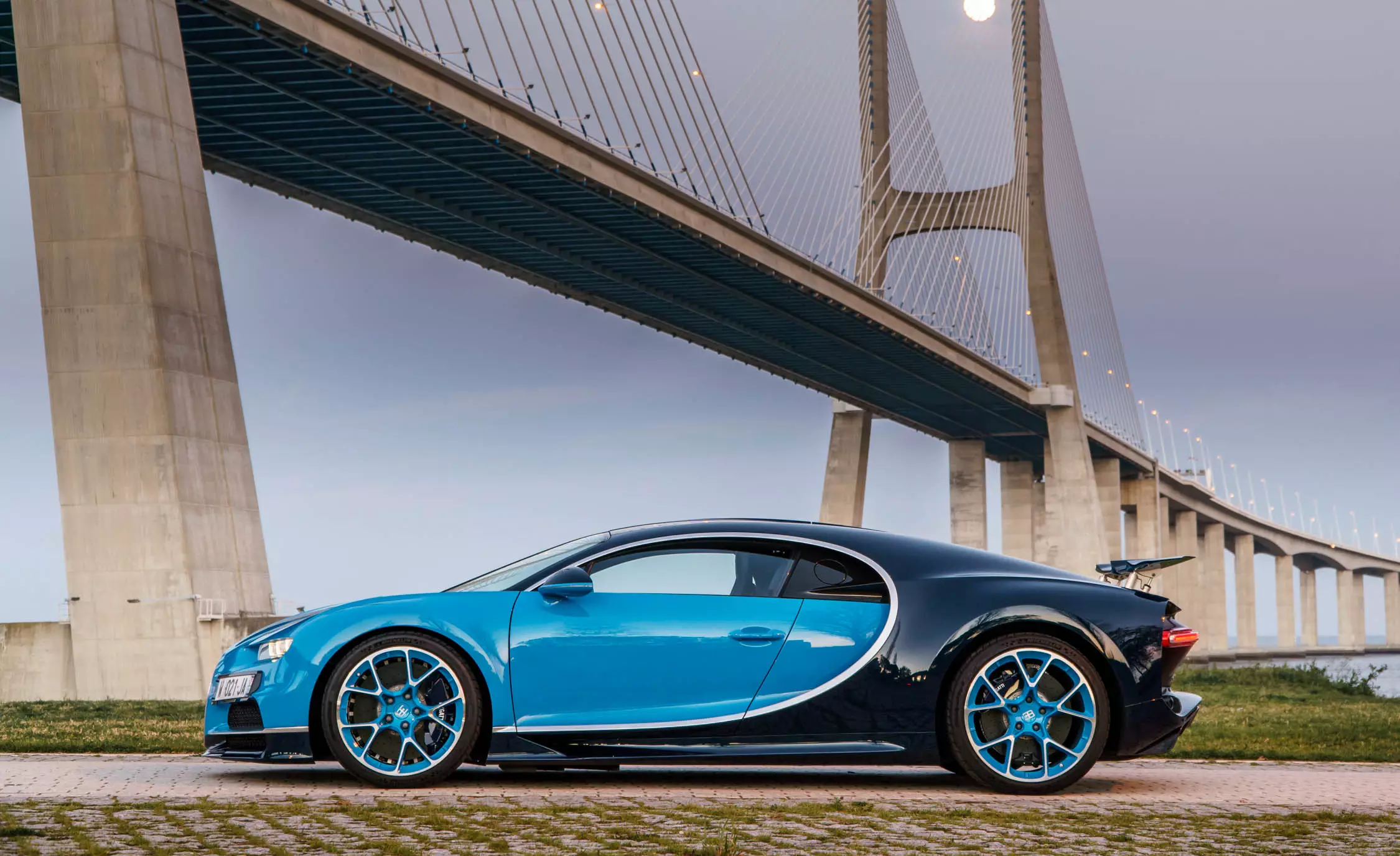
Жаңа пинцет материал ретінде титан қорытпасын — Ti6AI4V өз атауынан — пайдаланады, оны негізінен аэроғарыш өнеркәсібі үлкен кернеуге ұшырайтын құрамдас бөліктерде қолданады, бұл алюминийден әлдеқайда жоғары өнімділікті ұсынады. Созылу күші, әрине, өте жоғары: 1250 Н/мм2 , бұл титан қорытпасының үзілуінсіз бір шаршы миллиметрге 125 кг-нан сәл асатын әсер ету күшін білдіреді.
Жаңа тежегіш суппорттың ұзындығы 41 см, ені 21 см және биіктігі 13,6 см және оның жоғары беріктігінен басқа, салмақты айтарлықтай азайтудың үлкен артықшылығы бар, бұл әрқашан маңызды болып табылатын серіппе массасына әсер етеді. Салмағы небәрі 2,9 кг бірдей алюминий бөлігінің 4,9 кг қарсы, бұл 40% азайтуға тең.
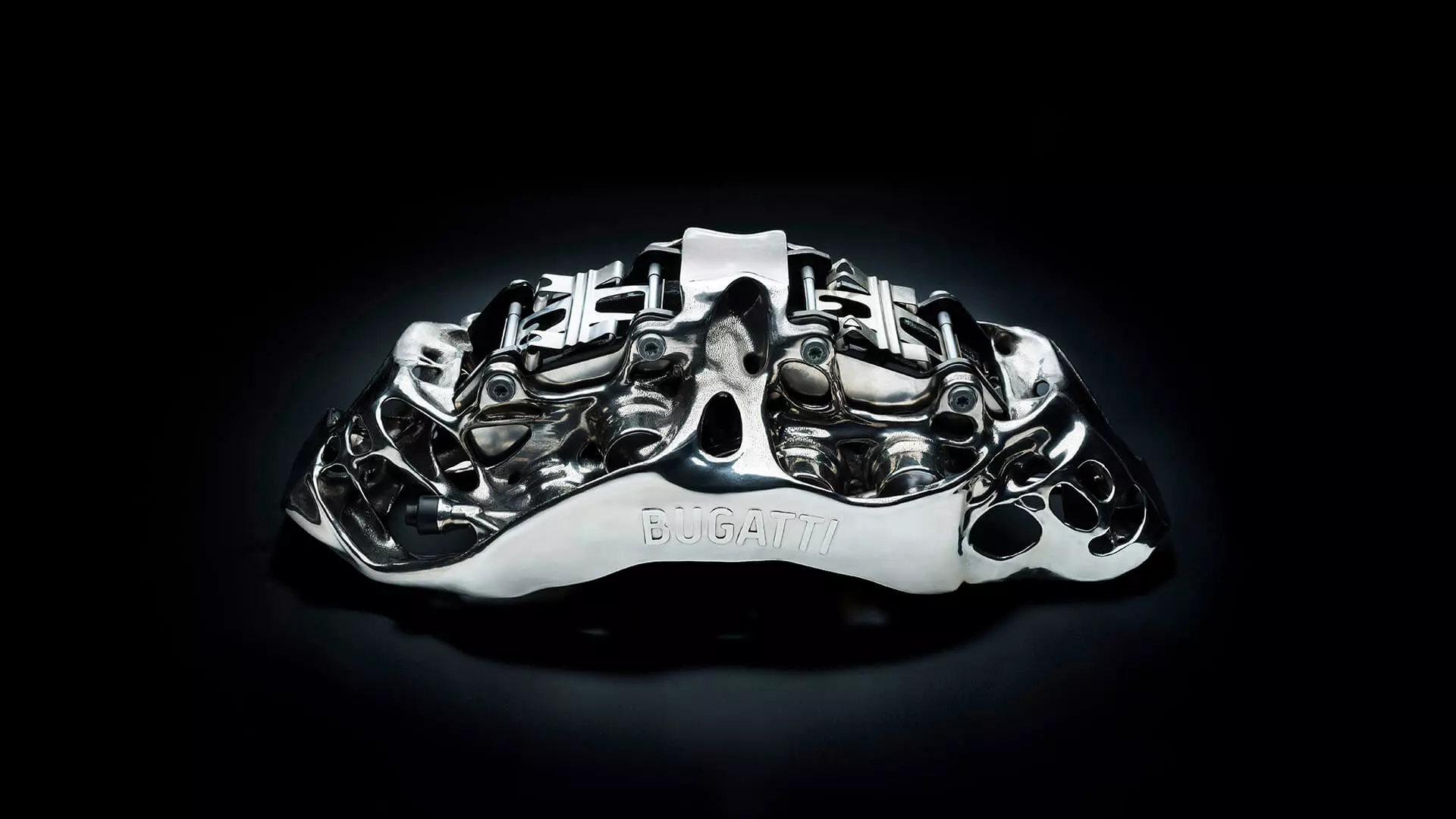
қосымша өндіріс
Бұл жаңа титан тежегіш калибрлері Bugatti әзірлеу бөлімі мен Laser Zentrum Nord арасындағы ынтымақтастықтың нәтижесі. Алғаш рет көлік компоненттерін басып шығару үшін алюминийдің орнына титан қолданылды, бұл оның қиындықтарын тудырды. Титанның жоғары беріктігі бұл материалдың пайдаланылмауының басты себебі болды, бұл өнімділігі жоғары принтерге жүгінуге мәжбүр болды.Жобаның басында титанды өңдеуге қабілетті әлемдегі ең үлкен Laser Zentrum Nord-да орналасқан бұл арнайы 3D принтері 400 Вт төрт лазермен жабдықталған.
Әрбір пинцет басып шығаруға 45 сағат кетеді.
Бұл процесс барысында титан ұнтағы қабат-қабат қойылады, төрт лазер ұнтақты алдын ала белгіленген пішінге дейін балқытады. Материал бірден дерлік салқындайды, ал қысқыш пішінді ала бастайды.
Кесек аяқталғанша барлығы шамамен 2213 қабат қажет.
Соңғы қабат салынғаннан кейін артық материал басып шығару камерасынан шығарылады, тазартылады және қайта пайдалану үшін сақталады. Аяқталған тежегіш суппорт камерада қалады, тіреуішпен бекітіледі, бұл оның пішінін сақтауға мүмкіндік береді. Құрамдас бөлікті тұрақтандыру және қажетті қарсылықты қамтамасыз ету үшін термиялық өңдеуден өткеннен кейін (ол 700 ºC жетеді) жойылатын тірек.
Беткей механикалық, физикалық және химиялық процестердің комбинациясы арқылы өңделеді, бұл оның шаршауға төзімділігін арттыруға ықпал етеді. Бес осьті өңдеу орталығын пайдаланып, поршеньді контактілер сияқты функционалды беттердің контурларын оңтайландыру үшін 11 сағаттан астам уақыт қажет.
Bugatti, 3D басып шығару бойынша топ жетекшісі
Осы арқылы Bugatti Volkswagen тобында 3D басып шығару технологиясы бойынша ғана емес, сонымен қатар жоғары технологиялық қолданбалар бойынша да жетекші орын алады. Миллионер зертханасының бір түрі және өте күшті...
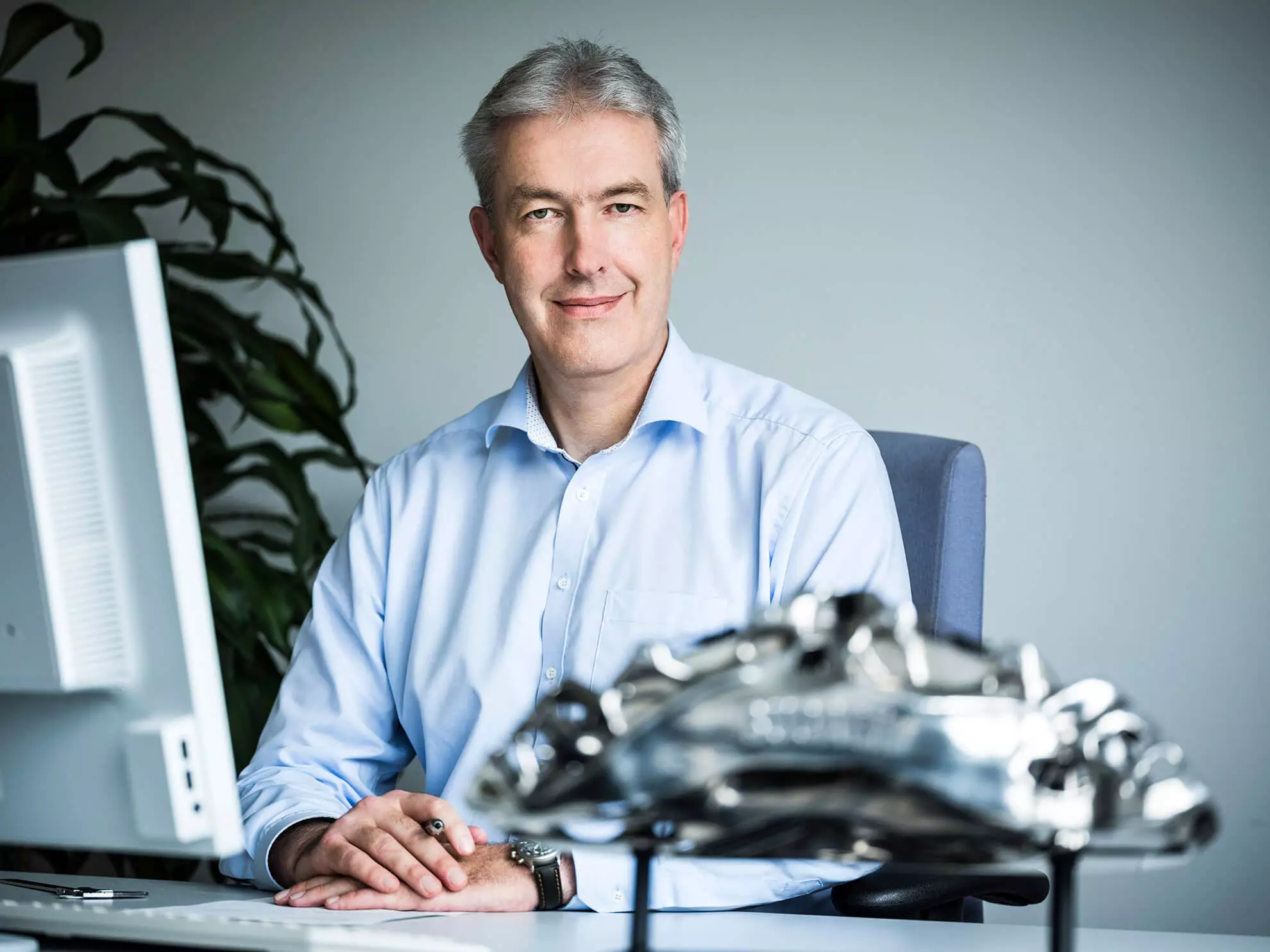
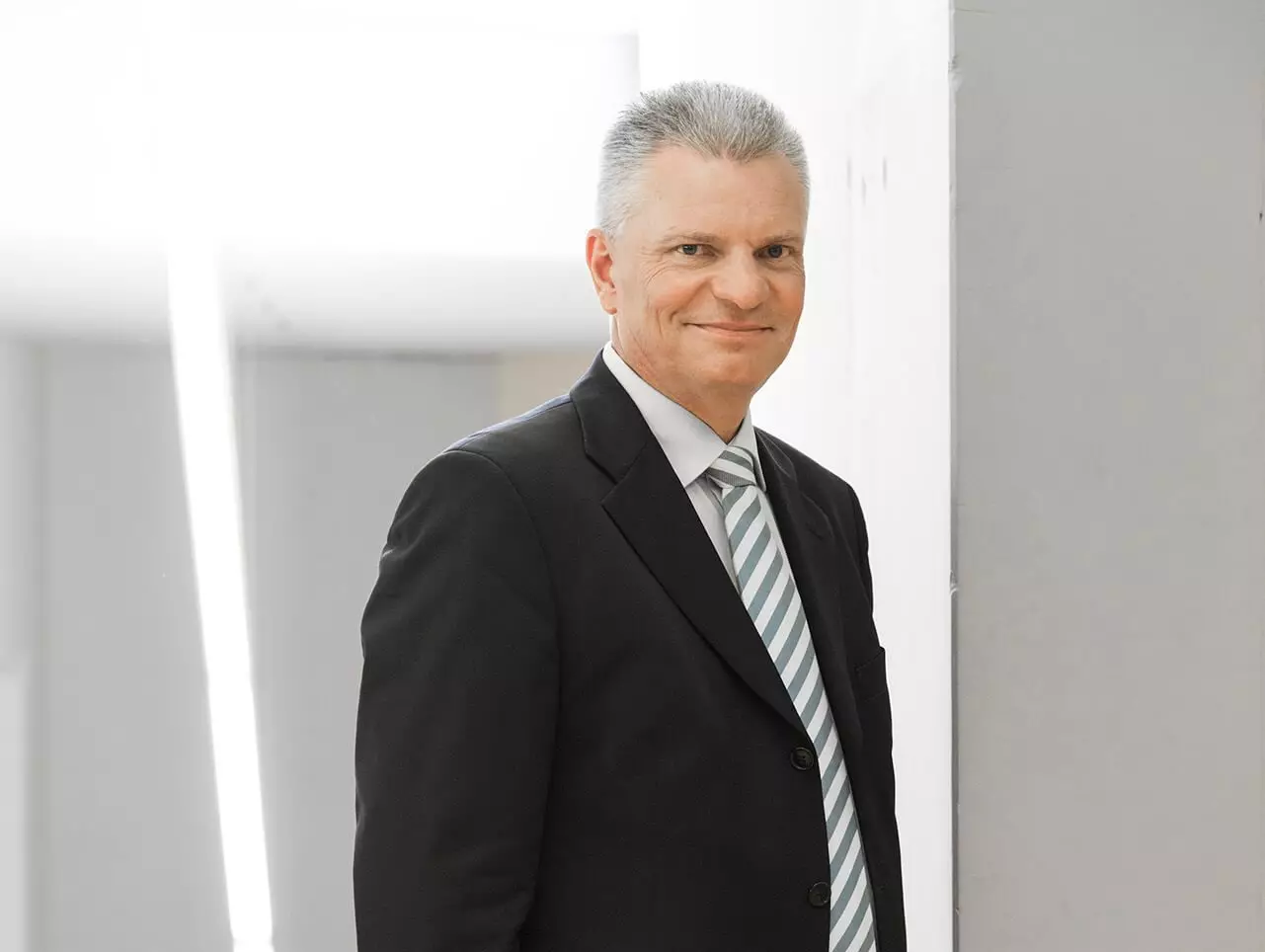