THE bugatti chiron on superlatiivide masin — kuigi Rootsi päritolu rivaal sai selle kuidagi oma auks haavata... — ja on just saanud järjekordse ülima kaalu, millele on lisatud uued titaanist pidurisadulad, mida tuleks selles mudelis hiljem kasutusele võtta. aastal.
Nagu teate, Bugatti Chiron oli juba autotööstuse suurimate pidurisadulate “omanik”. Need pidurisadulad olid sepistatud ülitugevast alumiiniumisulamist plokist, mille ees oli kaheksa titaankolvi ja taga kuus kolvi. Nii kaugel…
tugevam ja kergem
Bugatti on nüüd astunud järjekordse sammu edasi, arendades välja titaanist pidurisadulad – endiselt suurimad selles valdkonnas –, mis nüüd ei ole ainult 3D-printimise teel toodetud titaani suurim funktsionaalne komponent, kuna see on esimene pidurisadul, mis on selle meetodiga toodetud.
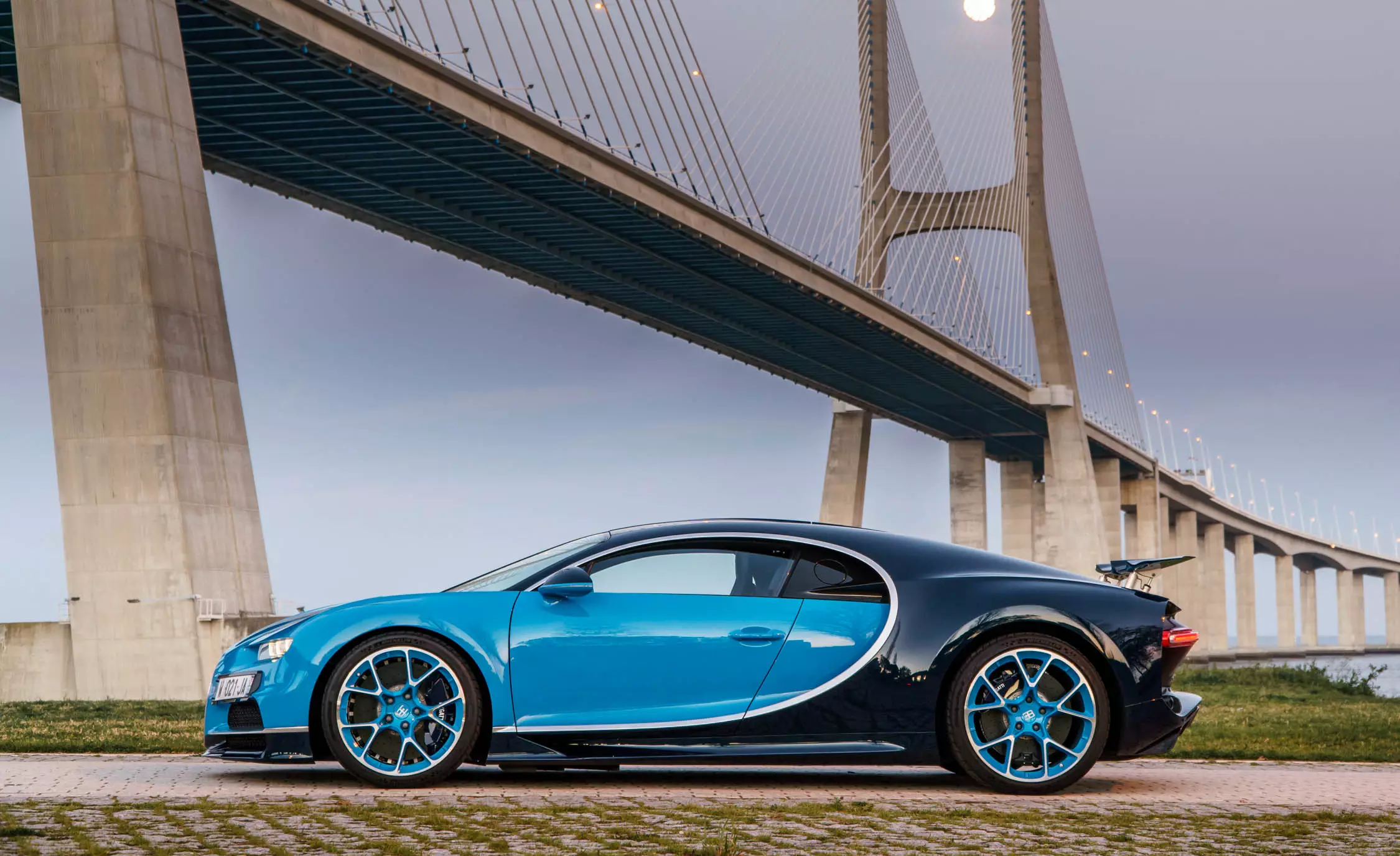
Uute pintsettide materjalina on kasutatud titaanisulamit – nimest Ti6AI4V –, mida kasutatakse peamiselt kosmosetööstuses tohutu pinge all olevates komponentides, pakkudes alumiiniumist palju paremat jõudlust. Tõmbetugevus on loomulikult äärmiselt kõrge: 1250 N/mm2 , mis tähendab rakendatavat jõudu veidi üle 125 kg ruutmillimeetri kohta, ilma et see titaanisulam puruneks.
Uus pidurisadul on 41 cm pikk, 21 cm lai ja 13,6 cm kõrge ning lisaks suurepärasele tugevusele on selle suureks eeliseks see, et see vähendab oluliselt kaalu, mõjutades üha tähtsamaid vedrustuseta masse. Kaalub ainult 2,9 kg 4,9 kg sama alumiiniumosa vastu, mis võrdub 40% vähendamisega.
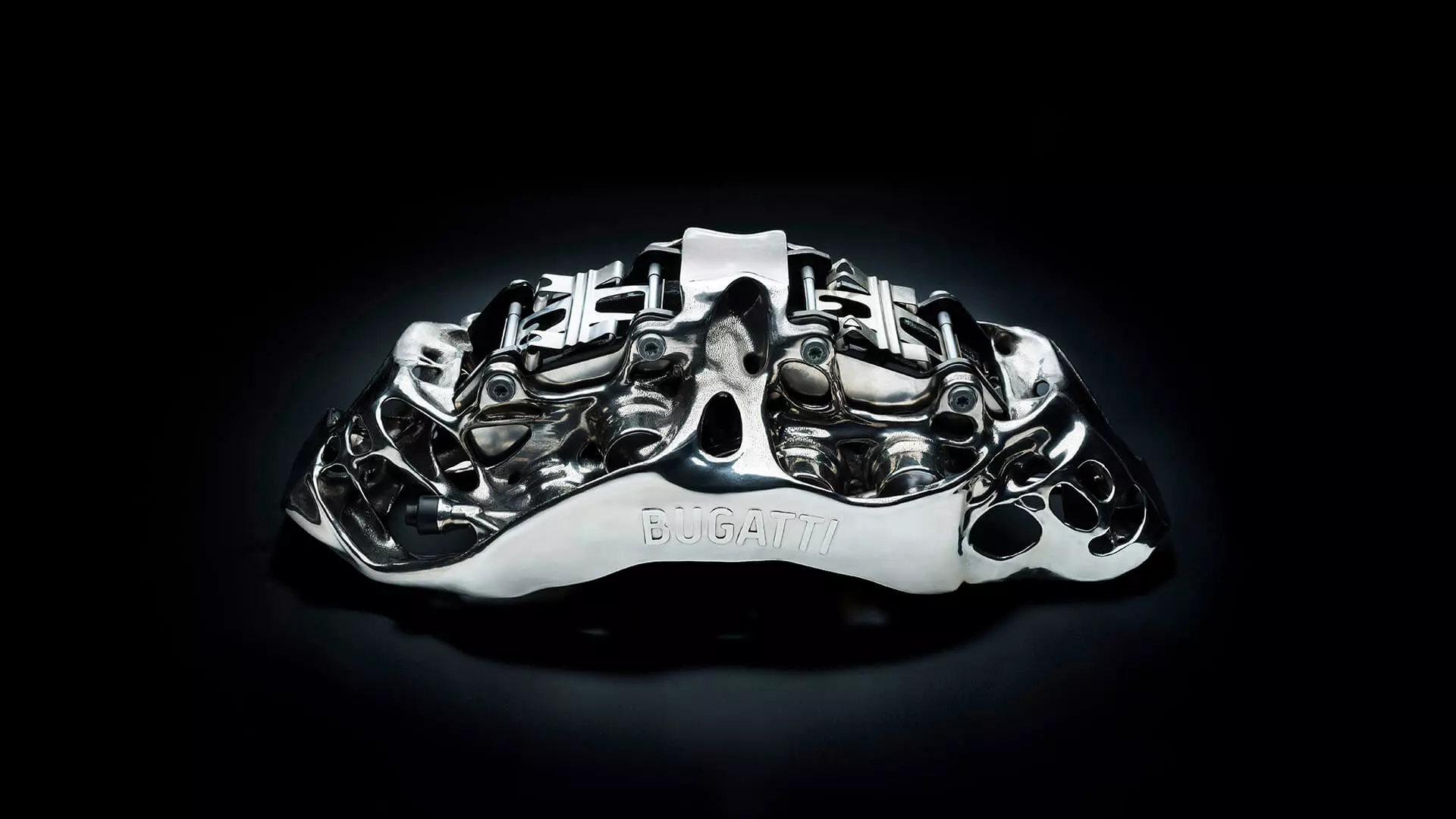
lisandite tootmine
Need uued titaanist pidurisadulad on Bugatti arendusosakonna ja Laser Zentrum Nordi koostöö tulemus. Esimest korda kasutati sõidukikomponentide printimisel alumiiniumi asemel titaani, mis tõi oma väljakutsed. Titaani kõrge tugevus on olnud peamine põhjus, miks seda materjali pole kasutatud, mis sundis kasutama suure jõudlusega printerit.See spetsiaalne 3D-printer, mis asub Laser Zentrum Nordil, mis oli projekti alguses maailma suurim titaaniga hakkama saanud, on varustatud nelja 400W laseriga.
Iga pintseti printimiseks kulub 45 tundi.
Selle protsessi käigus sadestatakse titaanipulber kiht kihi haaval, kusjuures neli laserit sulatavad pulbri etteantud kuju. Materjal jahtub peaaegu kohe ja klamber hakkab kuju võtma.
Kokku on vaja umbes 2213 kihti, kuni tükk on valmis.
Pärast viimase kihi ladestamist eemaldatakse üleliigne materjal trükikambrist, puhastatakse ja konserveeritakse taaskasutamiseks. Juba komplekteeritud pidurisadul jääb kambrisse toetuna, mis võimaldab sellel oma kuju säilitada. Tugi, mis eemaldatakse pärast komponendi kuumtöötlust (mis ulatub 700 ºC-ni), et seda stabiliseerida ja tagada soovitud vastupidavus.
Pinna viimistlemisel kombineeritakse mehaanilisi, füüsikalisi ja keemilisi protsesse, mis samuti aitavad parandada selle väsimustugevust. Funktsionaalsete pindade, näiteks kolvikontaktide, kontuuride optimeerimiseks viieteljelise töötluskeskuse abil kulub rohkem kui 11 tundi.
Bugatti, 3D-printimise grupijuht
Sellega haarab Bugatti Volkswageni kontsernis juhtpositsiooni mitte ainult 3D-printimise tehnoloogia, vaid ka kõrgtehnoloogiliste rakenduste osas. Omamoodi miljonärilabor ja väga-väga võimas...
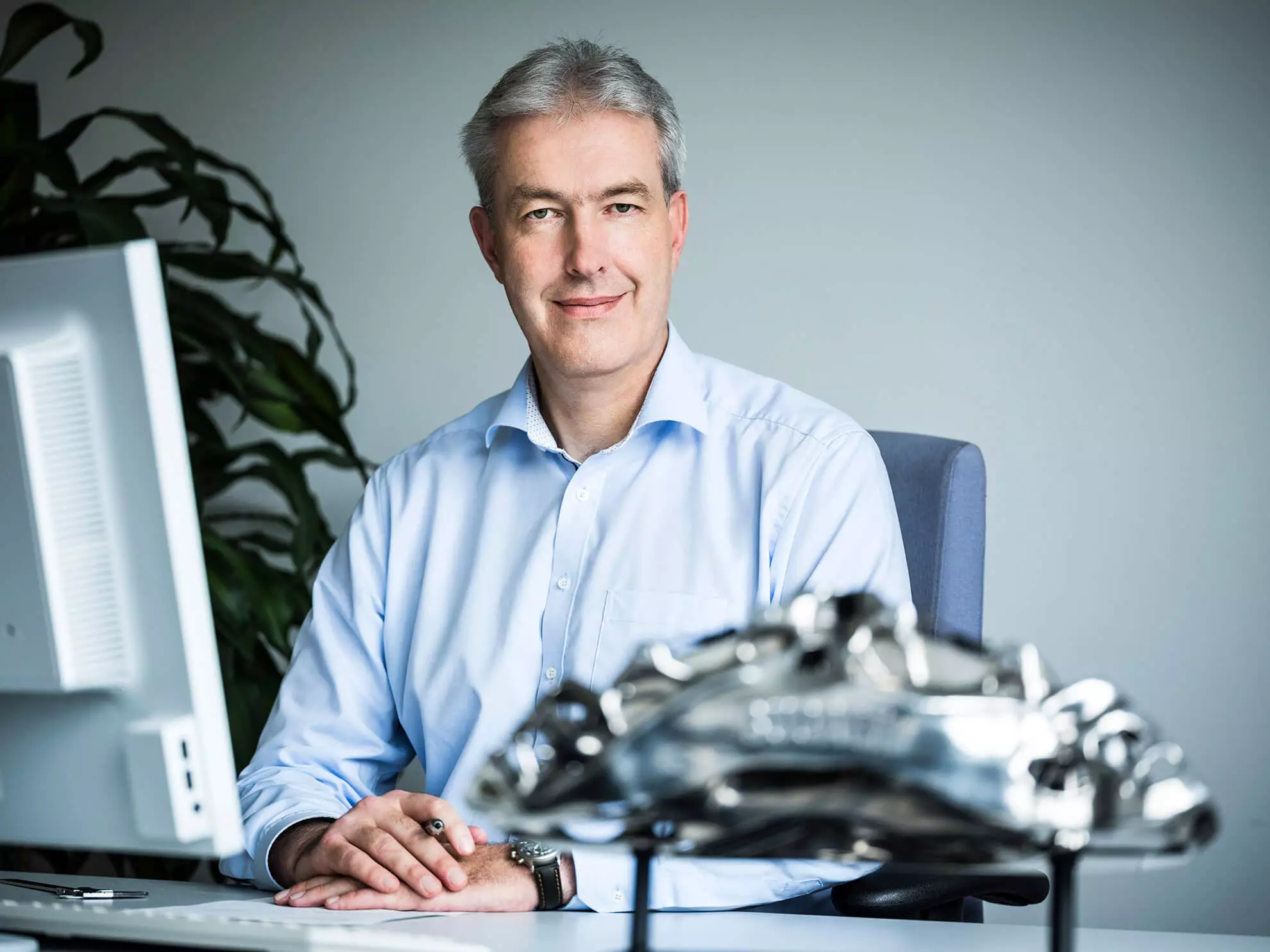
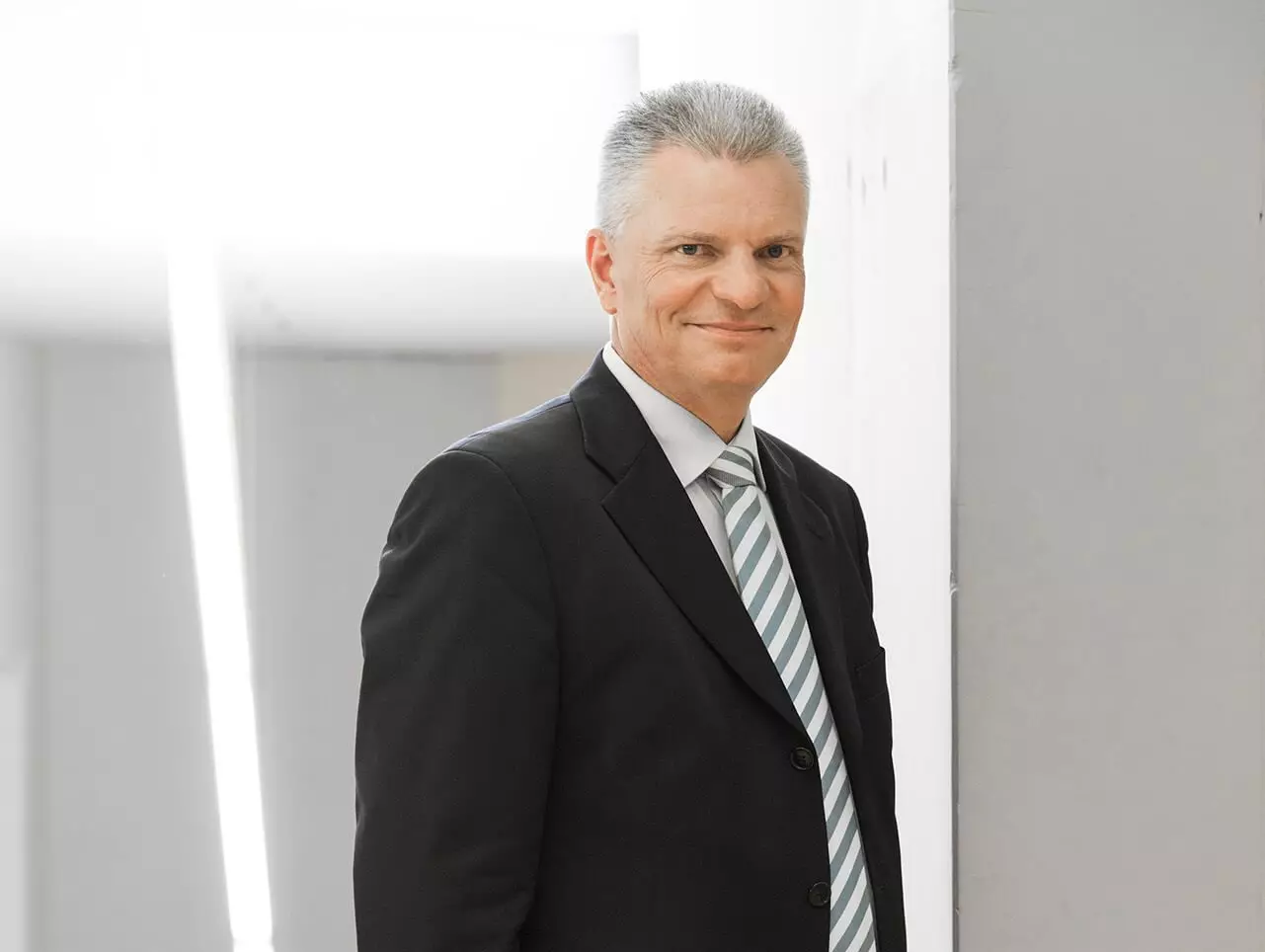