DAS bugatti chiron ist eine Maschine der Superlative – auch wenn sie von einem Rivalen schwedischer Herkunft irgendwie zu ihren Ehren verwundet wurde… – und hat gerade einen weiteren Superlativ an Gewicht gewonnen, mit den neuen Titan-Bremssätteln, die später in diesem Modell eingeführt werden sollen im Jahr.
Wie Sie wissen, Bugatti Chiron war bereits „Besitzer“ der größten Bremssättel der Automobilindustrie. Diese Bremssättel wurden aus einem hochfesten Aluminiumlegierungsblock mit acht Titankolben vorne und sechs Kolben hinten geschmiedet. Bis jetzt…
stärker und leichter
Bugatti ist jetzt einen weiteren Schritt nach vorne gegangen und hat Titan-Bremssättel entwickelt – immer noch die größten der Branche – die jetzt nicht nur das größte im 3D-Druck hergestellte Funktionsbauteil aus Titan, da es der erste Bremssattel ist, der in diesem Verfahren hergestellt wird.
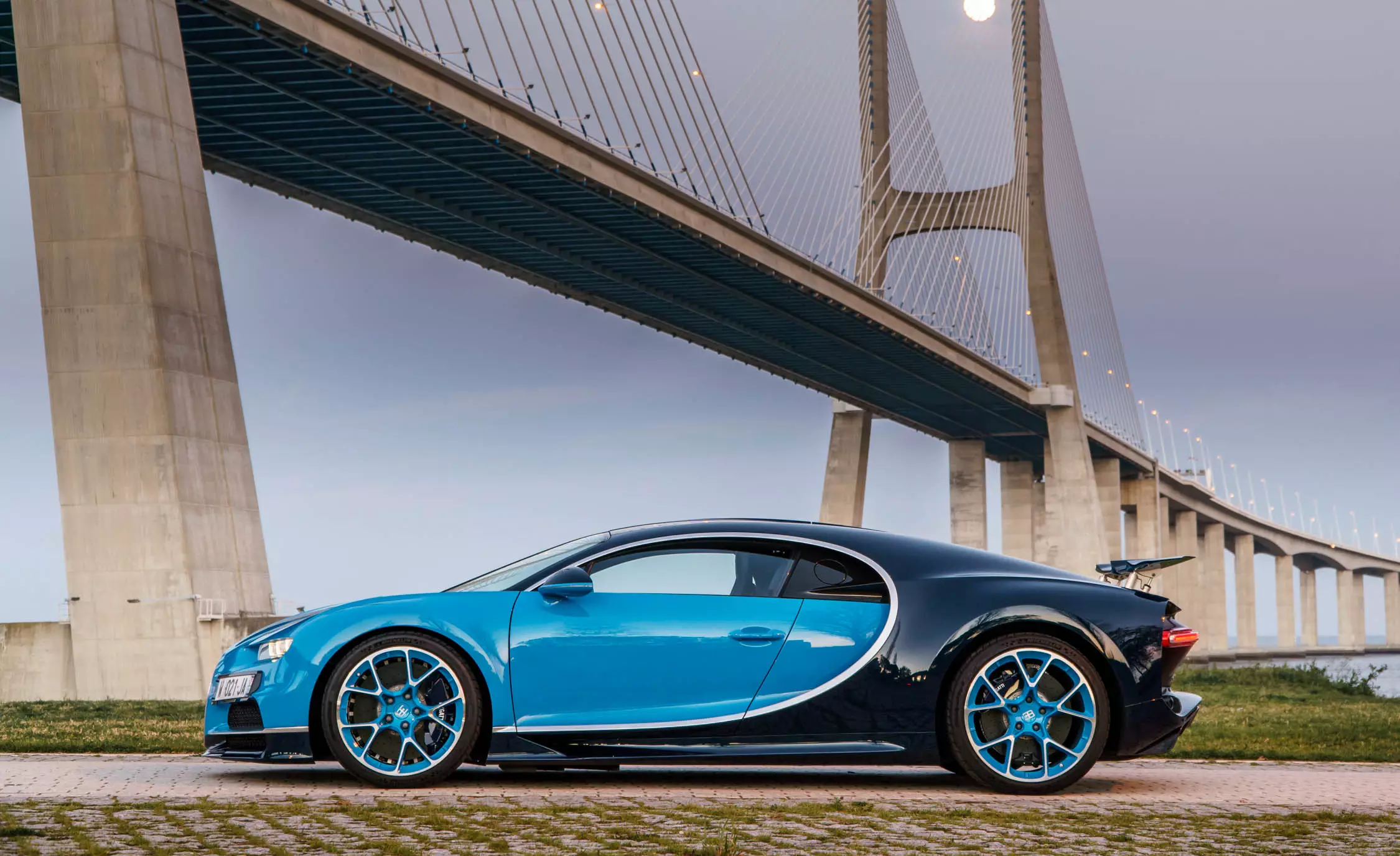
Die neue Pinzette verwendet als Material eine Titanlegierung – Ti6AI4V vom Namen –, die vor allem in der Luft- und Raumfahrtindustrie in stark beanspruchten Bauteilen verwendet wird und eine Leistung bietet, die der von Aluminium weit überlegen ist. Die Zugfestigkeit ist natürlich extrem hoch: 1250 N/mm2 , was eine aufgebrachte Kraft von knapp über 125 kg pro Quadratmillimeter bedeutet, ohne dass diese Titanlegierung bricht.
Der neue Bremssattel ist 41 cm lang, 21 cm breit und 13,6 cm hoch und bietet neben seiner überlegenen Festigkeit den großen Vorteil einer deutlichen Gewichtsreduzierung, die sich auf die immer wichtiger werdenden ungefederten Massen auswirkt. Wiegt nur 2,9 kg gegenüber 4,9 kg des gleichen Aluminiumteils, was einer Reduzierung von 40 % entspricht.
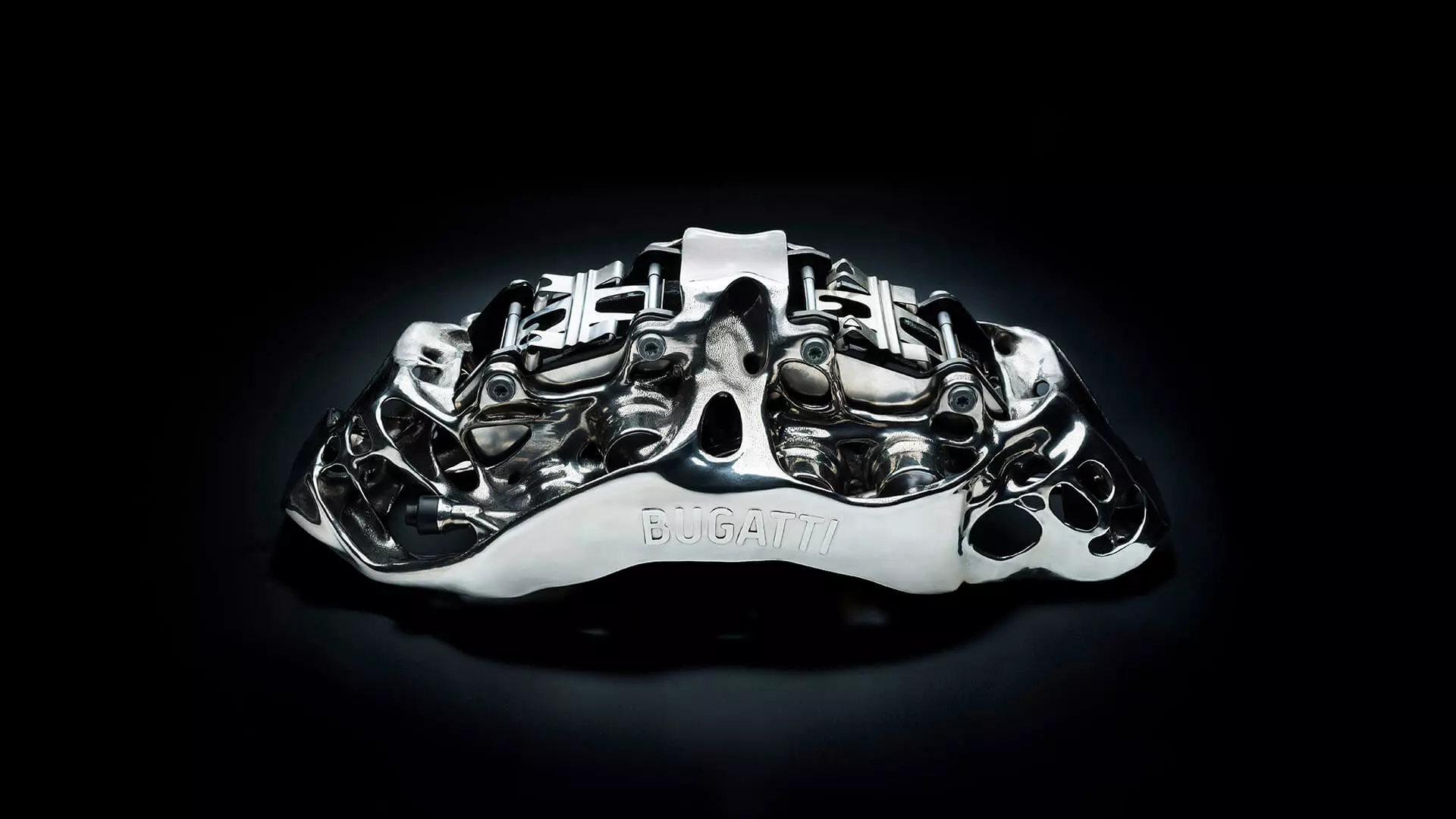
additive Fertigung
Diese neuen Titan-Bremssättel sind das Ergebnis einer Kooperation zwischen der Bugatti Entwicklungsabteilung und dem Laser Zentrum Nord. Zum ersten Mal wurde Titan anstelle von Aluminium zum Bedrucken von Fahrzeugkomponenten verwendet, was seine Herausforderungen mit sich brachte. Die hohe Festigkeit von Titan war der Hauptgrund für den Verzicht auf dieses Material, was den Umstieg auf einen Hochleistungsdrucker zwang.Dieser spezielle 3D-Drucker im Laser Zentrum Nord, der zu Beginn des Projekts der größte der Welt war, der Titan verarbeiten konnte, ist mit vier 400-W-Lasern ausgestattet.
Jede Pinzette benötigt 45 Stunden zum Drucken.
Dabei wird Titanpulver Schicht für Schicht abgeschieden, wobei die vier Laser das Pulver in die vorgegebene Form schmelzen. Das Material kühlt fast sofort ab und die Klammer nimmt Form an.
Insgesamt werden ca. 2213 Lagen benötigt, bis das Stück fertig ist.
Nach dem Auftragen der letzten Schicht wird das überschüssige Material aus der Druckkammer entfernt, gereinigt und zur Wiederverwendung konserviert. Der bereits fertige Bremssattel verbleibt in der Kammer, unterstützt von einer Halterung, die es ihm ermöglicht, seine Form zu bewahren. Träger, der entfernt wird, nachdem das Bauteil einer Wärmebehandlung unterzogen wurde (die 700 °C erreicht), um es zu stabilisieren und die gewünschte Widerstandsfähigkeit zu gewährleisten.
Die Oberflächenveredelung erfolgt durch eine Kombination mechanischer, physikalischer und chemischer Verfahren, die auch zur Verbesserung der Dauerfestigkeit beitragen. Die Konturoptimierung von Funktionsflächen, wie beispielsweise Kolbenkontakten, dauert mit einem 5-Achs-Bearbeitungszentrum über 11 Stunden.
Bugatti, Gruppenleiter 3D-Druck
Damit ist Bugatti nicht nur in Sachen 3D-Druck-Technologie, sondern auch in Sachen Hightech-Anwendungen führend im Volkswagen Konzern. Eine Art Millionärslabor und sehr, sehr mächtig...
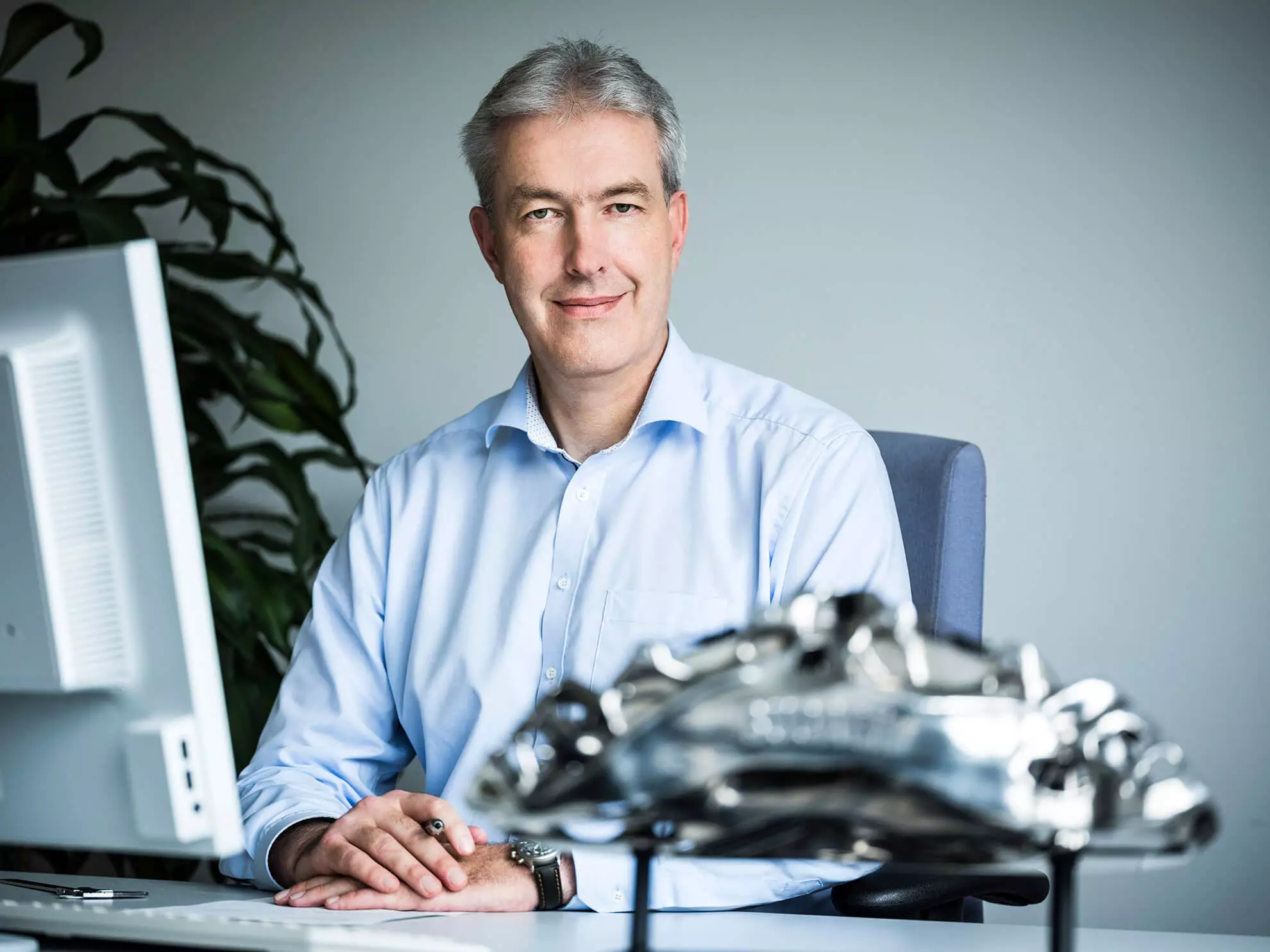
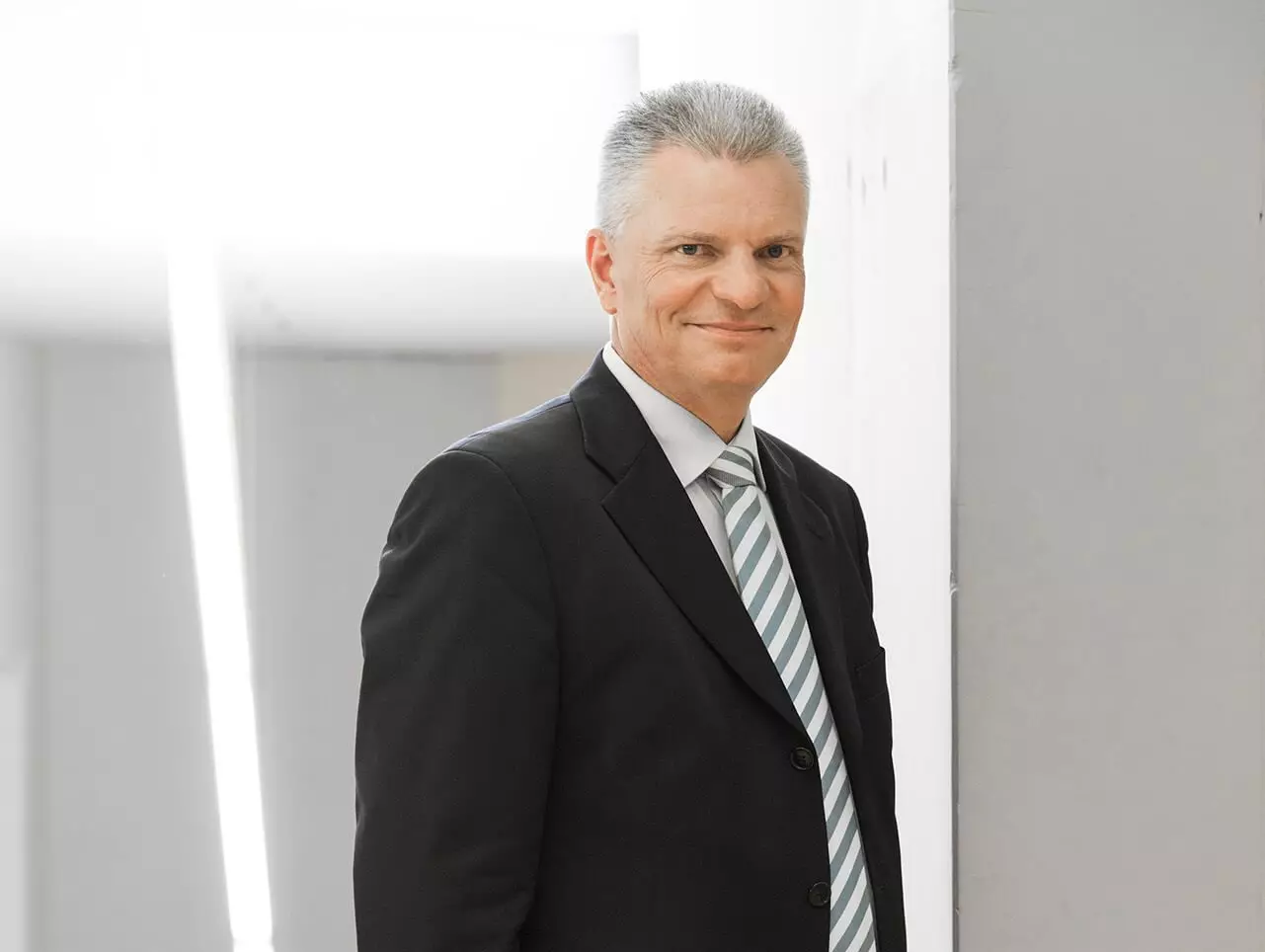