THE bugatti chiron er vél ofurmælinga - jafnvel þó hún hafi einhvern veginn verið særð til heiðurs af keppinaut af sænskum uppruna ... - og hefur nýlega fengið enn eina yfirburðarþyngd, með því að bæta við nýjum títan bremsuklossum, sem ætti að koma í þessari gerð síðar á árinu.
Eins og þú veist, þá Bugatti Chiron var þegar „eigandi“ stærstu bremsuklossanna í bílaiðnaðinum. Þessar þykktar voru smíðaðar úr hástyrkri álblokk með átta títan stimplum að framan og sex stimplum að aftan. Hingað til…
sterkari og léttari
Bugatti hefur nú stigið enn eitt skrefið fram á við, með því að þróa bremsudiska úr títaníum - enn þá stærstu í greininni - sem eru nú ekki aðeins stærsti hagnýtur íhluturinn í títan sem framleiddur er með þrívíddarprentun, þar sem hann er fyrsti bremsuklossinn sem framleiddur er með þessari aðferð.
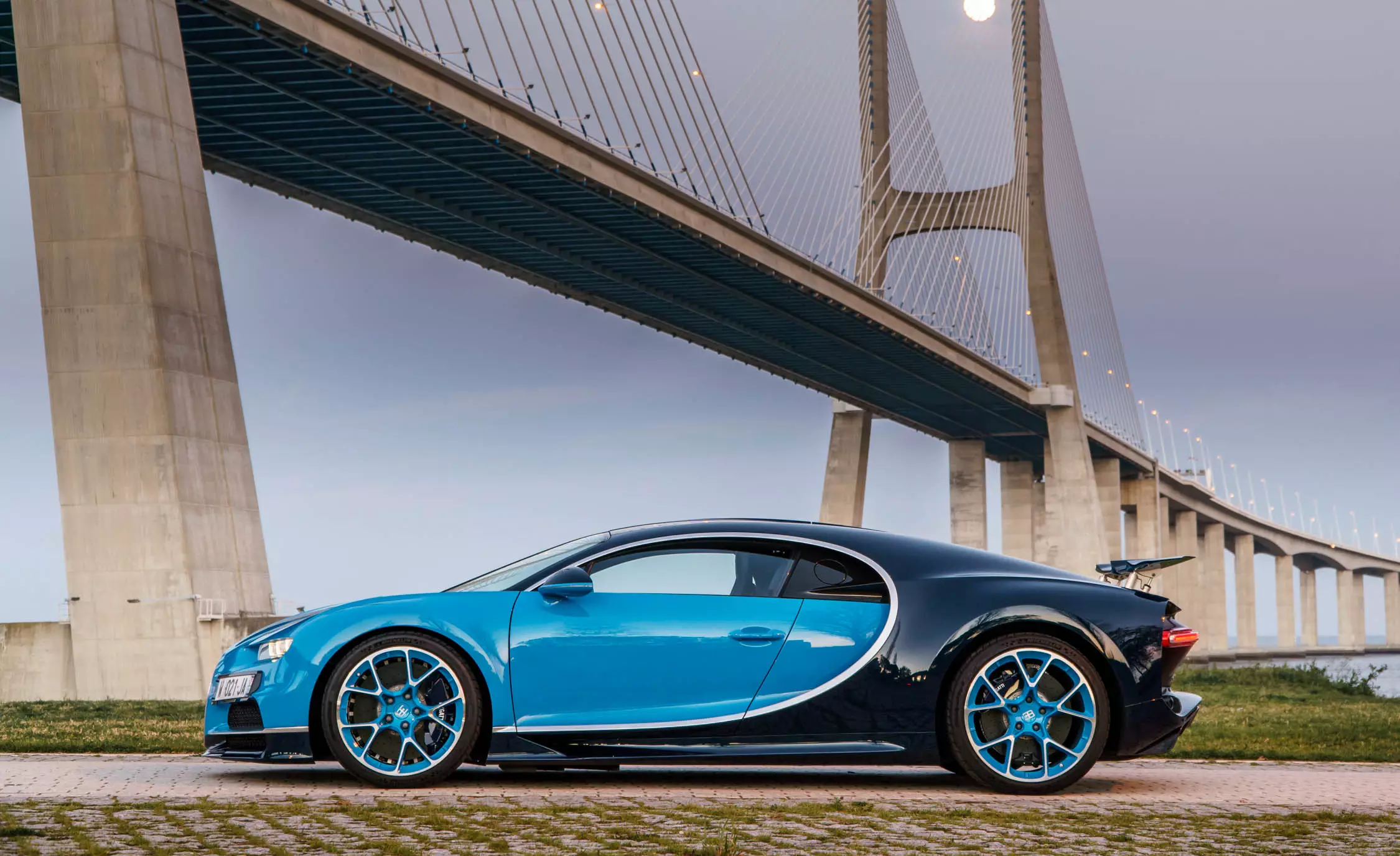
Nýju töngin nota sem efni títan álfelgur - Ti6AI4V af nafni þess -, sem aðallega er notað af fluggeimiðnaðinum í íhlutum sem eru háðir gífurlegu álagi, sem býður upp á frammistöðu mun betri en áli. Togstyrkurinn er auðvitað mjög hár: 1250 N/mm2 , sem þýðir beittur kraftur upp á rúmlega 125 kg á fermillímetra án þess að þessi títaníumblendi brotni.
Nýja bremsuklossinn er 41 cm á lengd, 21 cm á breidd og 13,6 cm á hæð og hefur, auk yfirburða styrks, þann mikla kost að draga verulega úr þyngd, sem hefur áhrif á sífellt mikilvægan ófjöðraðan massa. Vegur aðeins 2,9 kg á móti 4,9 kg af sama álhluta sem jafngildir 40% lækkun.
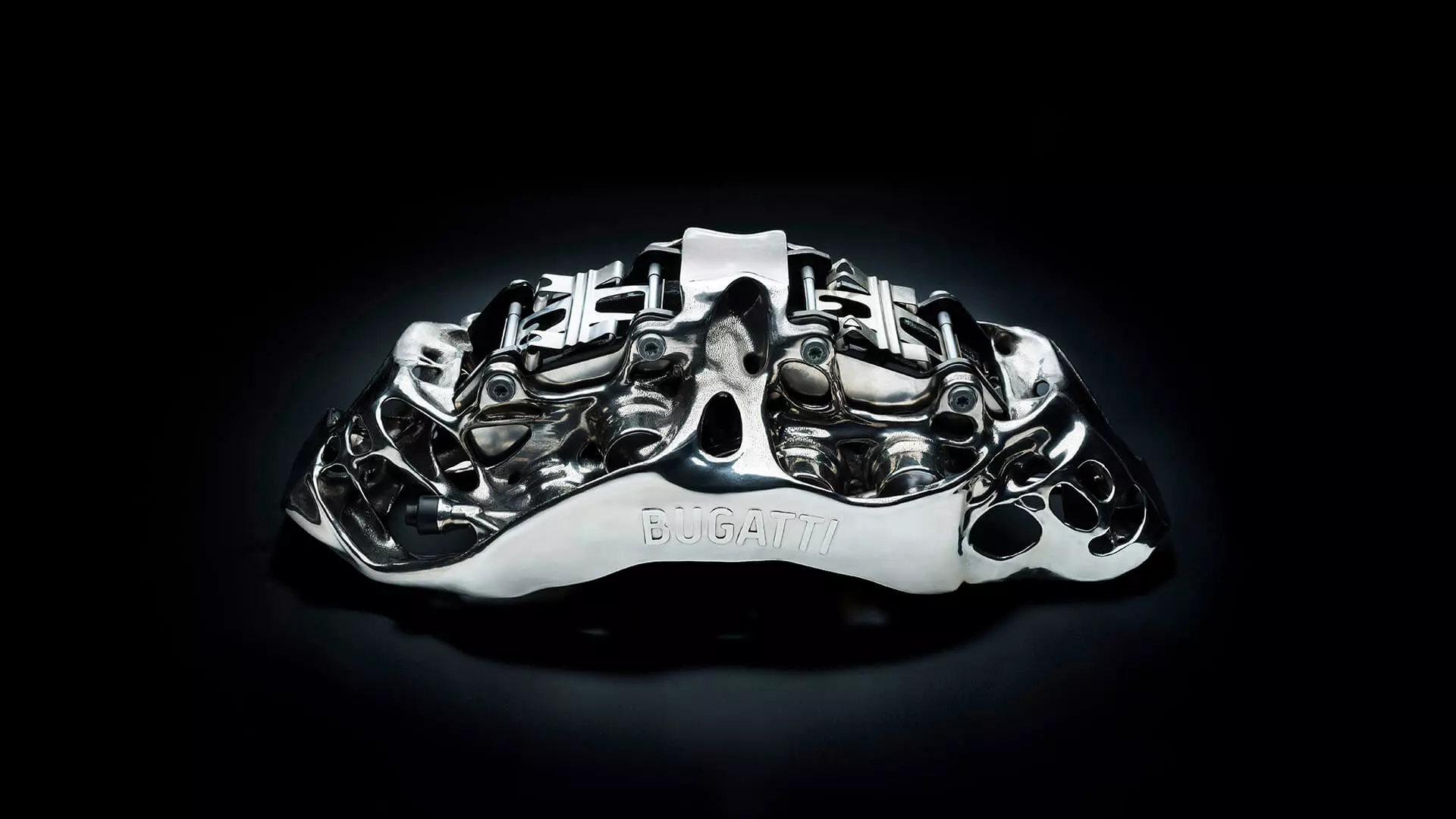
aukaefnaframleiðsla
Þessir nýju títan bremsuklossar eru afrakstur samvinnu Bugatti þróunardeildar og Laser Zentrum Nord. Í fyrsta skipti var títan notað í stað áls til að prenta íhluti ökutækja, sem leiddi til áskorana þess. Mikill styrkur títan hefur verið aðalástæðan fyrir því að þetta efni hefur ekki verið notað, sem neyddi til að grípa til afkastamikils prentara.Þessi sérstaki þrívíddarprentari, sem staðsettur er á Laser Zentrum Nord, sem var sá stærsti í heiminum sem gat meðhöndlað títan í upphafi verkefnisins, er búinn fjórum 400W leysigeislum.
Það tekur 45 klukkustundir að prenta hverja pincet.
Meðan á þessu ferli stendur er títanduft lag fyrir lag, þar sem leysirnir fjórir bræða duftið í fyrirfram ákveðna lögun. Efnið kólnar nánast samstundis og klemman fer að taka á sig mynd.
Alls þarf um 2213 lög þar til stykkið er fullbúið.
Eftir að síðasta lagið hefur verið sett er umframefnið fjarlægt úr prenthólfinu, hreinsað og varðveitt til endurnotkunar. Bremsuklossinn, sem þegar er búinn, er áfram í hólfinu, studdur af stuðningi, sem gerir honum kleift að varðveita lögun sína. Stuðningur sem er fjarlægður eftir að íhluturinn hefur fengið hitameðferð (sem nær 700 ºC) til að koma á stöðugleika og tryggja æskilega viðnám.
Yfirborðið er klárað með blöndu af vélrænum, eðlisfræðilegum og efnafræðilegum ferlum, sem einnig stuðla að því að bæta þreytustyrk þess. Það tekur meira en 11 klukkustundir að hámarka útlínur virkra yfirborðs, eins og stimpla tengiliða, með því að nota fimm ása vinnslustöð.
Bugatti, hópstjóri í þrívíddarprentun
Með þessu tekur Bugatti forystu í Volkswagen Group, ekki aðeins hvað varðar þrívíddarprentunartækni, heldur einnig hvað varðar hátækninotkun. Einskonar milljónamæringarannsóknarstofa og mjög, mjög öflug...
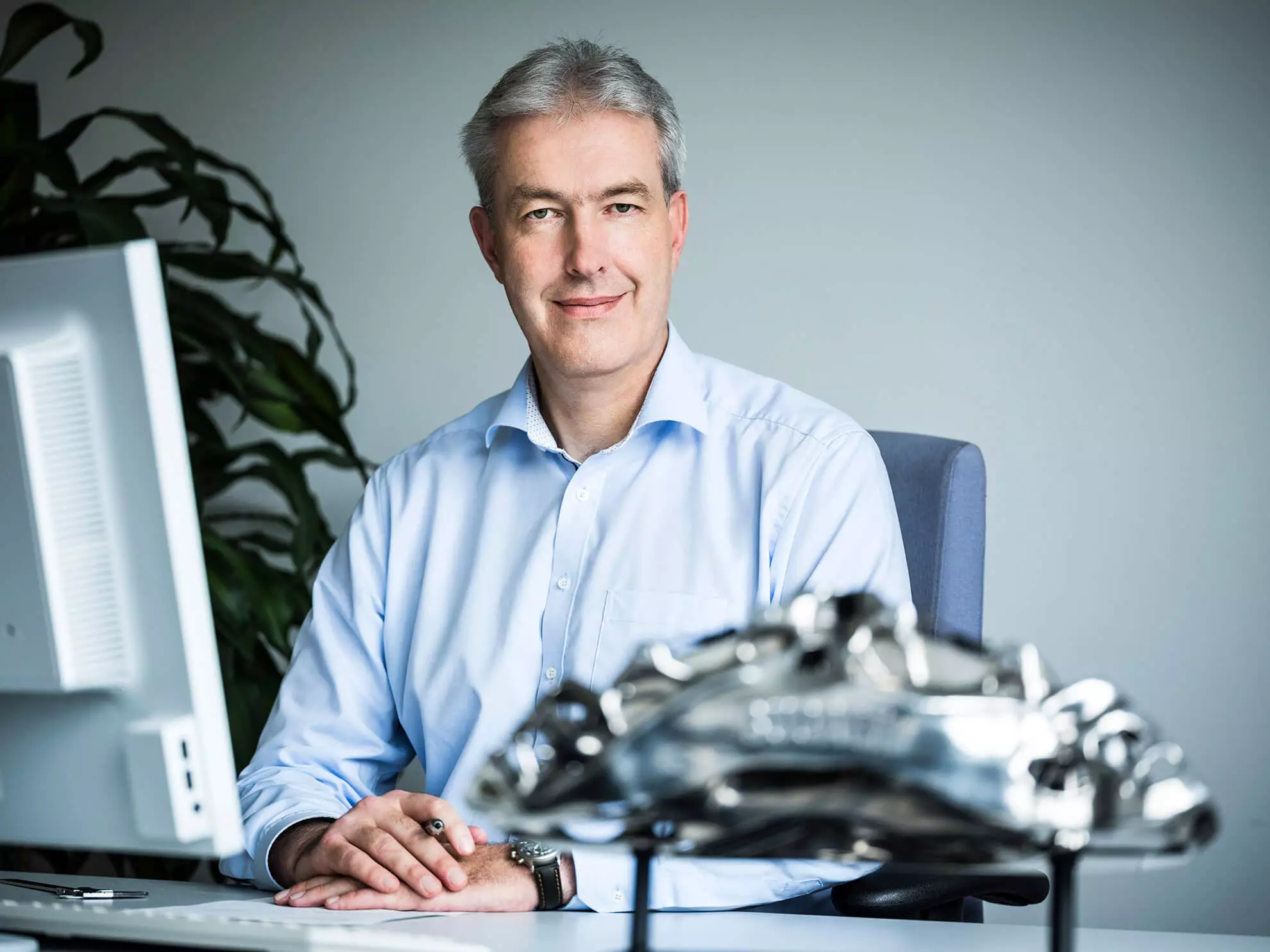
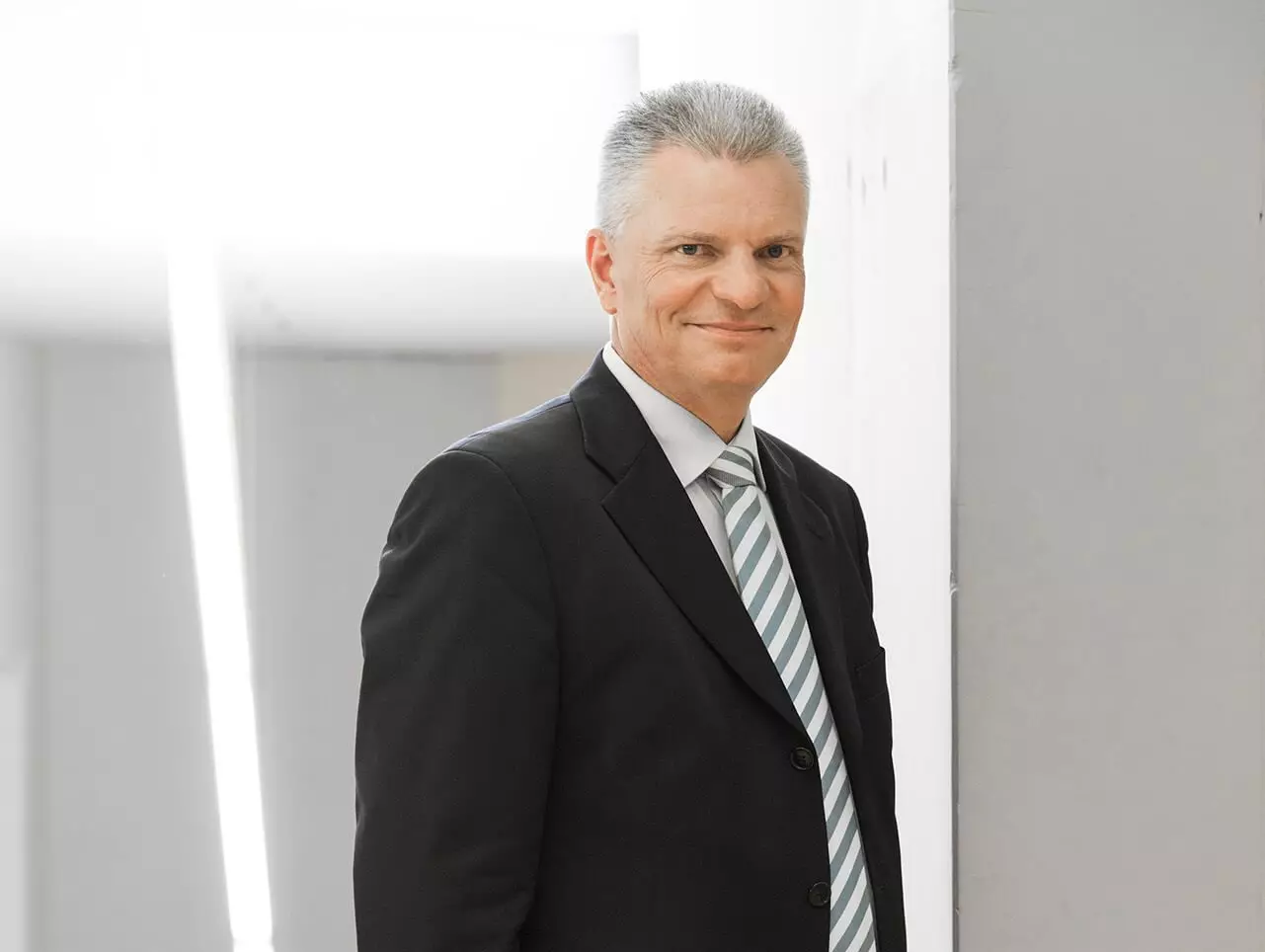