THE bugatti chiron yra superlatyvų mašina – nors ją savo garbei kažkaip sužeidė švedų kilmės varžovas… – ir ką tik įgavo dar vieną svorio superlatyvą, pridėjus naujus titano stabdžių apkabas, kurios šiame modelyje turėtų būti pristatytos vėliau. metuose.
Kaip žinote, Bugatti Chiron jau buvo didžiausių stabdžių apkabų „savininkas“ automobilių pramonėje. Šie suportai buvo nukaldinti iš didelio stiprumo aliuminio lydinio bloko su aštuoniais titano stūmokliais priekyje ir šešiais stūmokliais gale. Iki šiol…
stipresnis ir lengvesnis
„Bugatti“ žengė dar vieną žingsnį į priekį – sukūrė titano stabdžių apkabas – vis dar didžiausias pramonėje – kurios dabar yra ne tik didžiausias funkcinis titano komponentas, pagamintas 3D spausdinimo būdu, nes tai pirmasis stabdžių apkaba, pagaminta šiuo metodu.
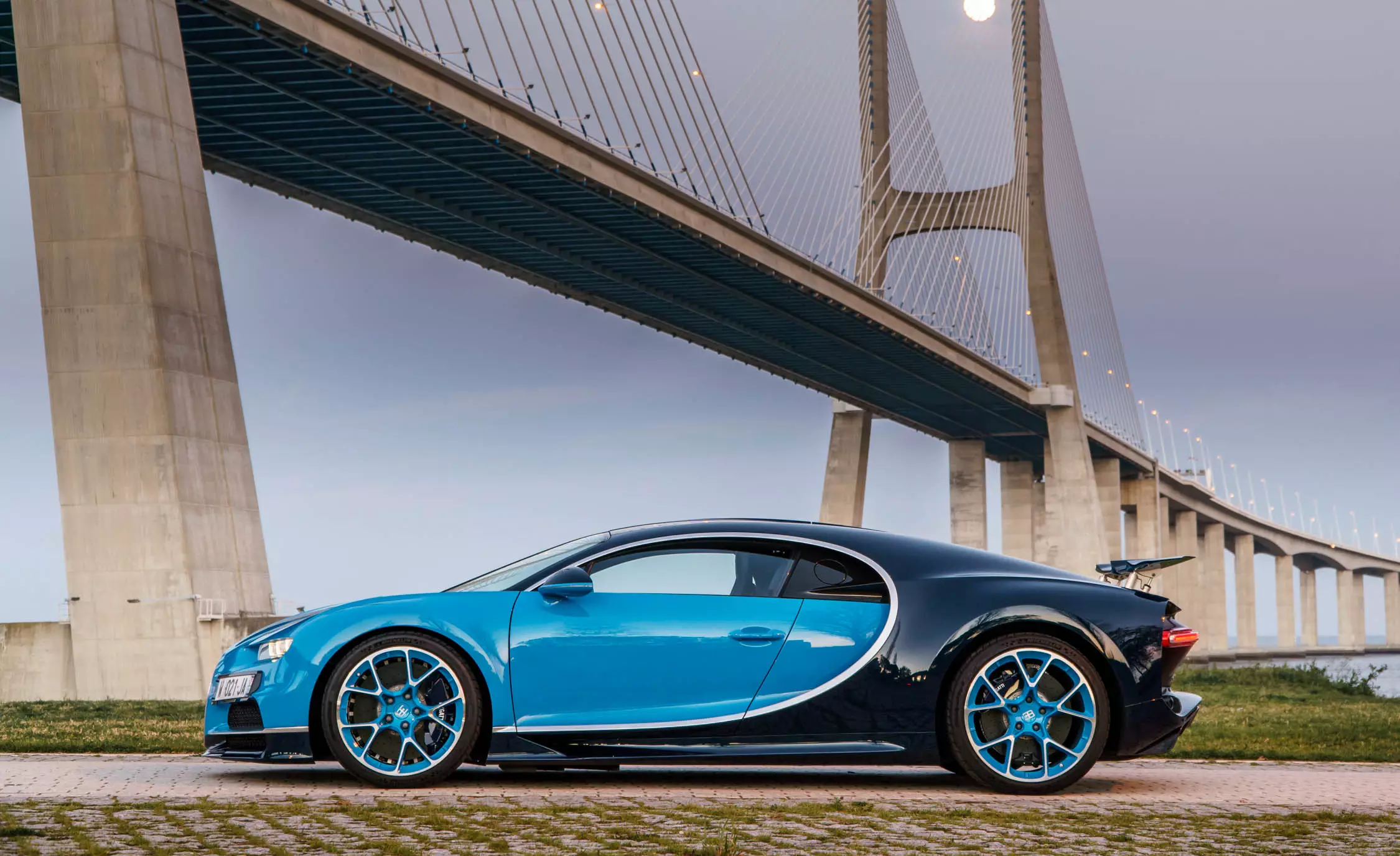
Naujuosiuose pincetuose kaip medžiaga naudojamas titano lydinys – Ti6AI4V pagal pavadinimą, kurį daugiausia naudoja aviacijos ir kosmoso pramonė komponentams, patiriantiems didžiulį įtempimą, o tai yra daug pranašesnė už aliuminį. Žinoma, atsparumas tempimui yra labai didelis: 1250 N/mm2 , o tai reiškia, kad vienam kvadratiniam milimetrui taikoma kiek daugiau nei 125 kg jėga, nesulaužant šio titano lydinio.
Naujoji stabdžių apkaba yra 41 cm ilgio, 21 cm pločio ir 13,6 cm aukščio ir, be ypatingo tvirtumo, turi didelį pranašumą – žymiai sumažina svorį, paveikiant vis svarbias nespyruokliškas mases. Sveria tik 2,9 kg prieš 4,9 kg tos pačios aliuminio dalies, o tai prilygsta 40% sumažinimui.
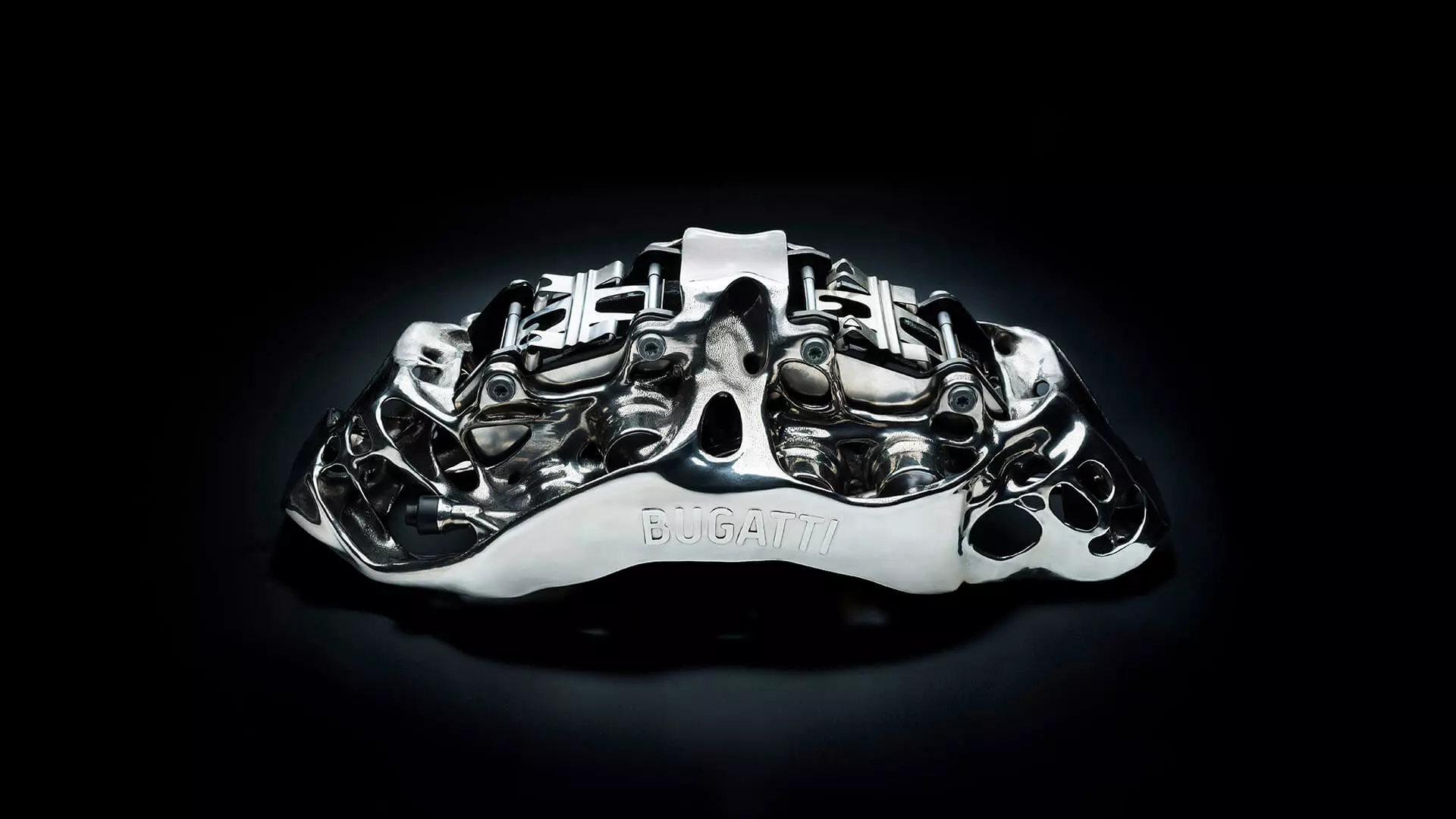
priedų gamyba
Šios naujos titano stabdžių apkabos yra Bugatti plėtros departamento ir Laser Zentrum Nord bendradarbiavimo rezultatas. Pirmą kartą transporto priemonių komponentams spausdinti vietoj aliuminio buvo naudojamas titanas, o tai atnešė iššūkių. Didelis titano stiprumas buvo pagrindinė priežastis, kodėl ši medžiaga nebuvo naudojama, todėl teko griebtis didelio našumo spausdintuvo.Šiame specialiame 3D spausdintuve, esančiame Laser Zentrum Nord, kuris projekto pradžioje buvo didžiausias pasaulyje, galintis apdoroti titaną, yra aprūpintas keturiais 400 W lazeriais.
Kiekvienas pincetas atspausdinamas per 45 valandas.
Šio proceso metu titano milteliai nusodinami sluoksnis po sluoksnio, o keturi lazeriai išlydo miltelius į iš anksto nustatytą formą. Medžiaga beveik iš karto atvėsta, o spaustukas pradeda formuotis.
Iš viso reikia apie 2213 sluoksnių, kol gabalas bus baigtas.
Po to, kai nusodinamas paskutinis sluoksnis, medžiagos perteklius pašalinamas iš spausdinimo kameros, išvalomas ir konservuojamas pakartotiniam naudojimui. Jau sukomplektuota stabdžių apkaba lieka kameroje, palaikoma atramos, kuri leidžia išsaugoti formą. Atrama, kuri pašalinama po komponento terminio apdorojimo (kuris pasiekia 700 ºC), kad jį stabilizuotų ir būtų garantuotas norimas atsparumas.
Paviršius baigiamas derinant mechaninius, fizinius ir cheminius procesus, kurie taip pat padeda pagerinti jo atsparumą nuovargiui. Norint optimizuoti funkcinių paviršių, tokių kaip stūmokliniai kontaktai, kontūrus, naudojant penkių ašių apdirbimo centrą, reikia daugiau nei 11 valandų.
Bugatti, 3D spausdinimo grupės lyderis
Taip „Bugatti“ pirmauja „Volkswagen“ grupėje ne tik pagal 3D spausdinimo technologijas, bet ir pagal aukštųjų technologijų taikymą. Savotiška milijonierių laboratorija ir labai labai galinga...
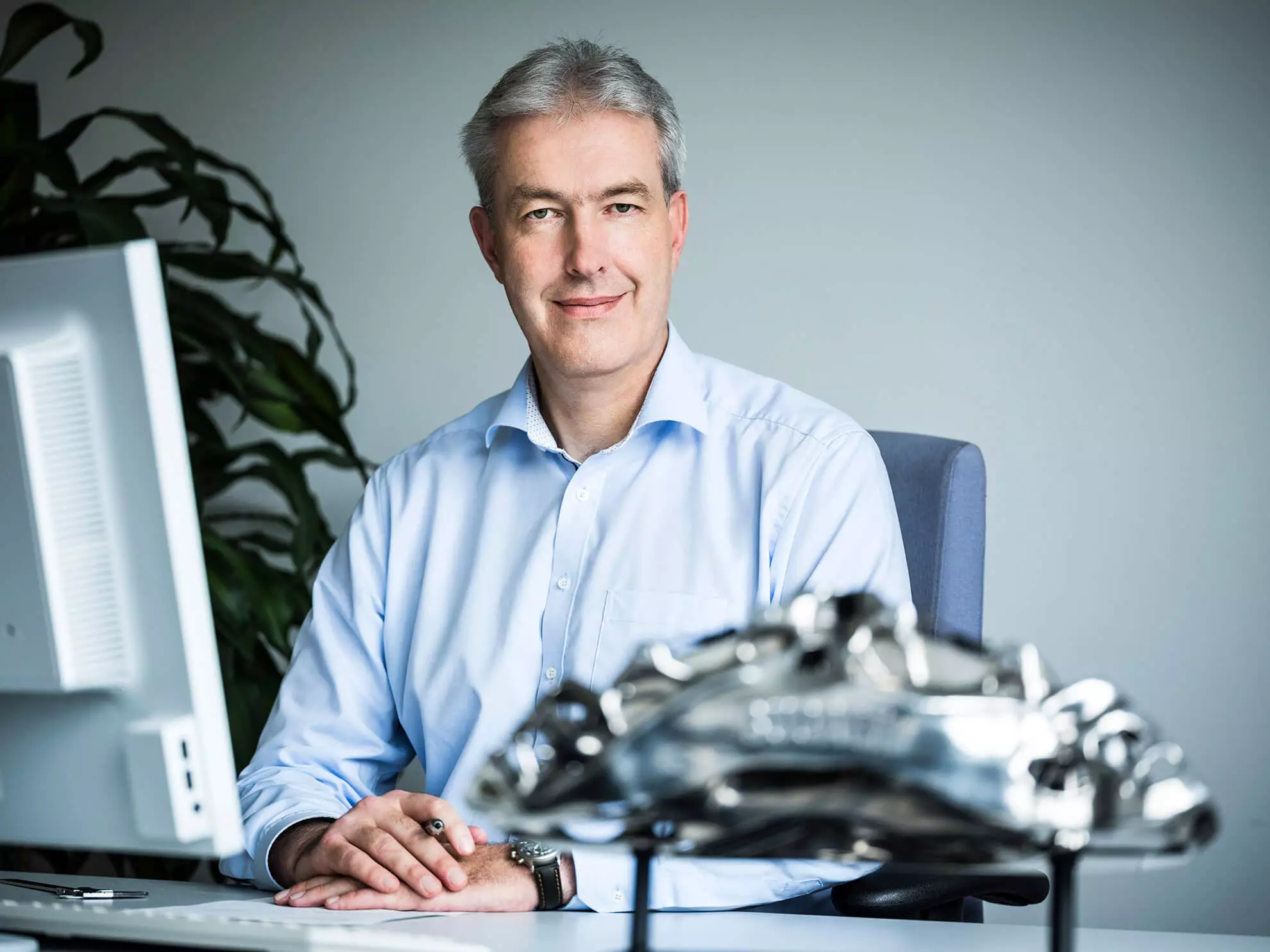
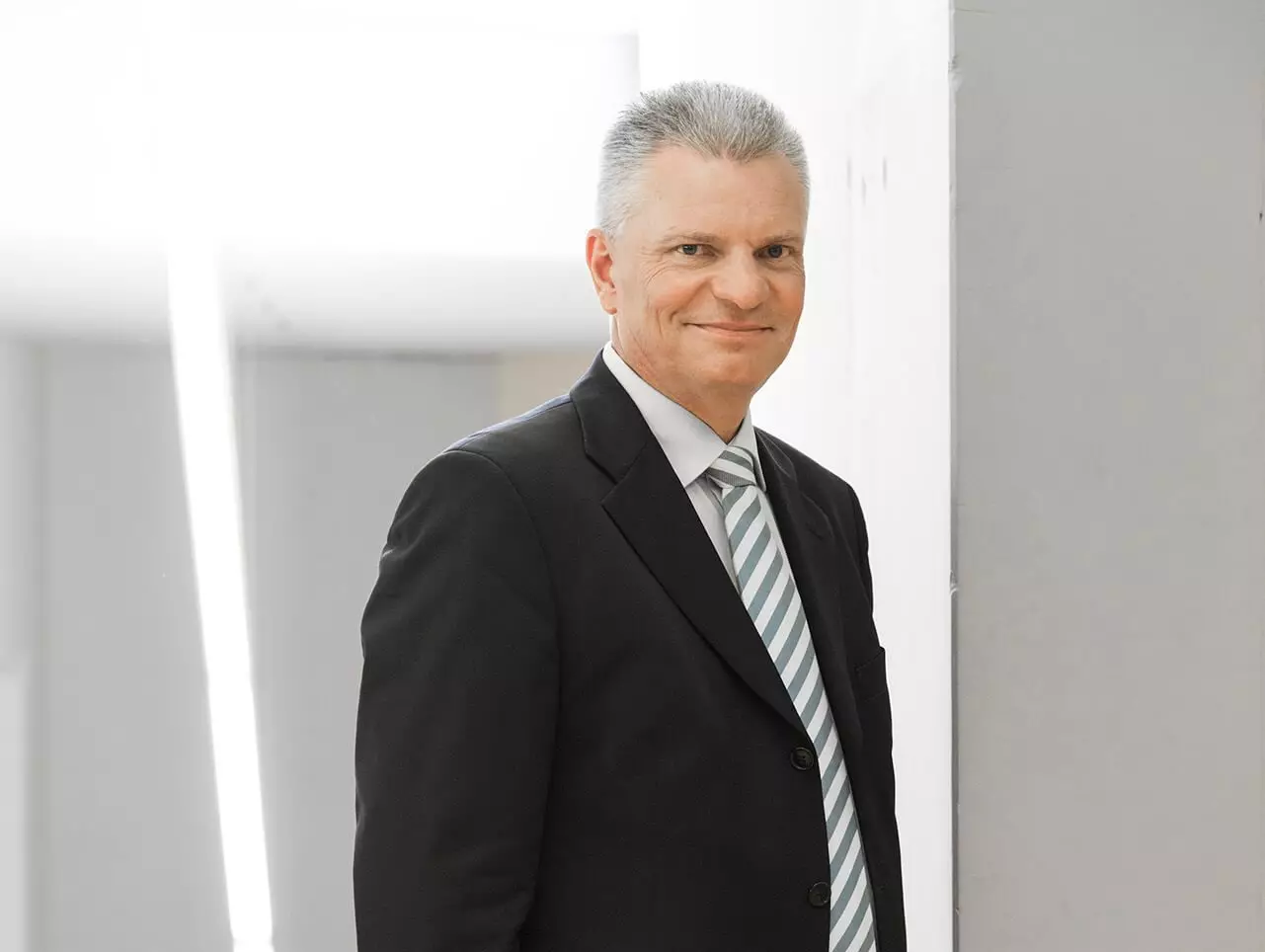