THE bugatti chiron ir superlatives mašīna — lai gan to savā godā ievainoja zviedru izcelsmes sāncensis... — un nupat ir ieguvusi vēl vienu svara izcilību, pievienojot jaunus titāna bremžu suportus, kurus šajā modelī vajadzētu ieviest vēlāk. gadā.
Kā jūs zināt, Bugatti Chiron jau bija lielāko bremžu suportu “īpašnieks” automobiļu rūpniecībā. Šie suporti tika kalti no augstas stiprības alumīnija sakausējuma bloka ar astoņiem titāna virzuļiem priekšā un sešiem virzuļiem aizmugurē. Tik tālu…
stiprāks un vieglāks
Bugatti tagad ir spēris vēl vienu soli uz priekšu, izstrādājot titāna bremžu suportus — joprojām lielākos šajā nozarē —, kas tagad ir ne tikai lielākais funkcionālais komponents titānā, kas ražots ar 3D drukāšanu, jo tas ir pirmais bremžu suports, kas ražots ar šo metodi.
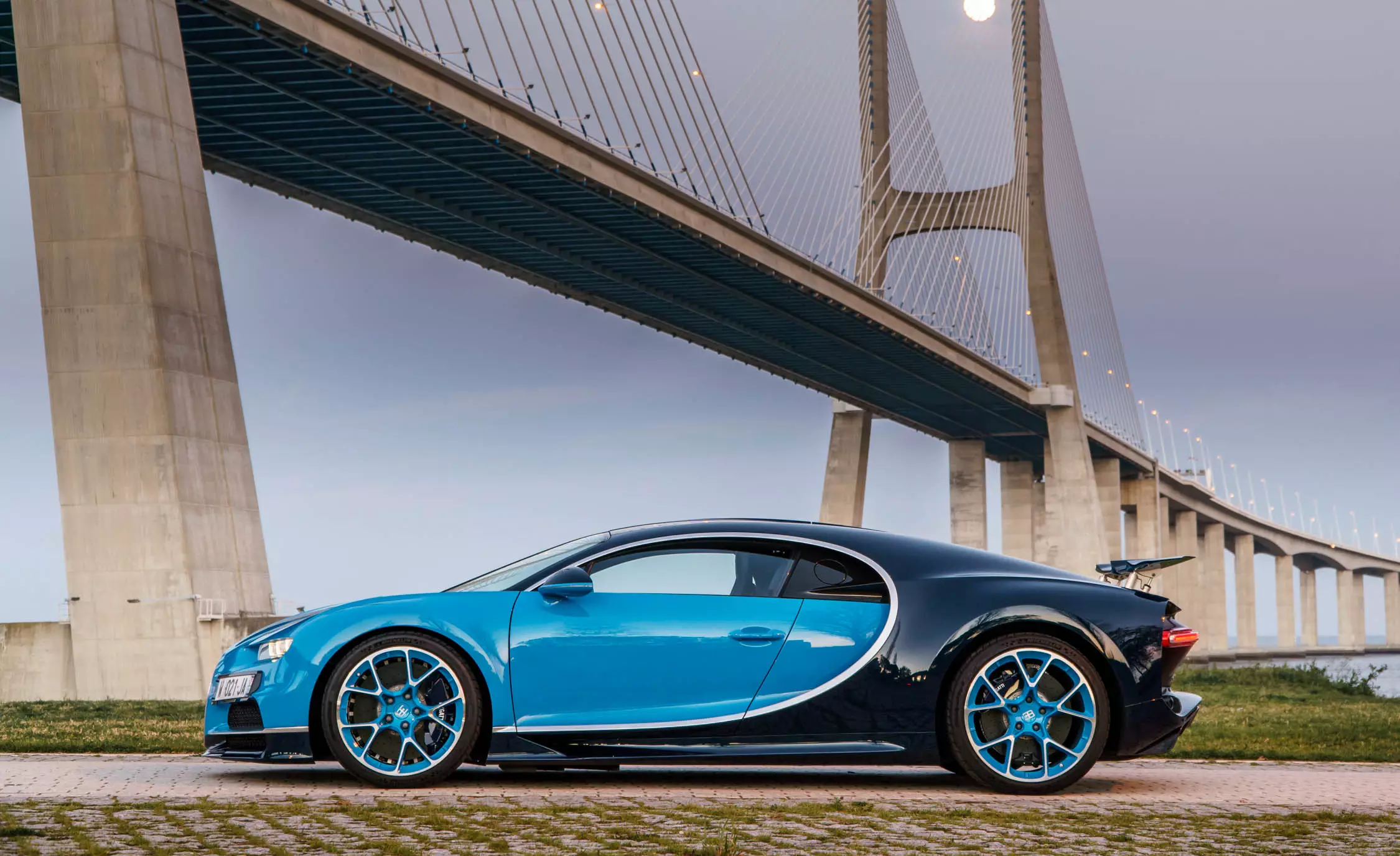
Jaunajās pincetēs kā materiāls tiek izmantots titāna sakausējums — Ti6AI4V no tā nosaukuma —, ko galvenokārt izmanto aviācijas un kosmosa rūpniecībā komponentos, kas pakļauti milzīgam spriegumam, piedāvājot daudz labāku veiktspēju nekā alumīnijam. Stiepes izturība, protams, ir ārkārtīgi augsta: 1250 N/mm2 , kas nozīmē pielikto spēku nedaudz vairāk par 125 kg uz kvadrātmilimetru bez šī titāna sakausējuma pārrāvuma.
Jaunais bremžu suports ir 41 cm garš, 21 cm plats un 13,6 cm augsts, un papildus izcilajai izturībai tā priekšrocība ir ievērojami samazināt svaru, ietekmējot arvien svarīgākās neatsperoto masu. Sver tikai 2,9 kg pret 4,9 kg tās pašas alumīnija daļas, kas atbilst 40% samazinājumam.
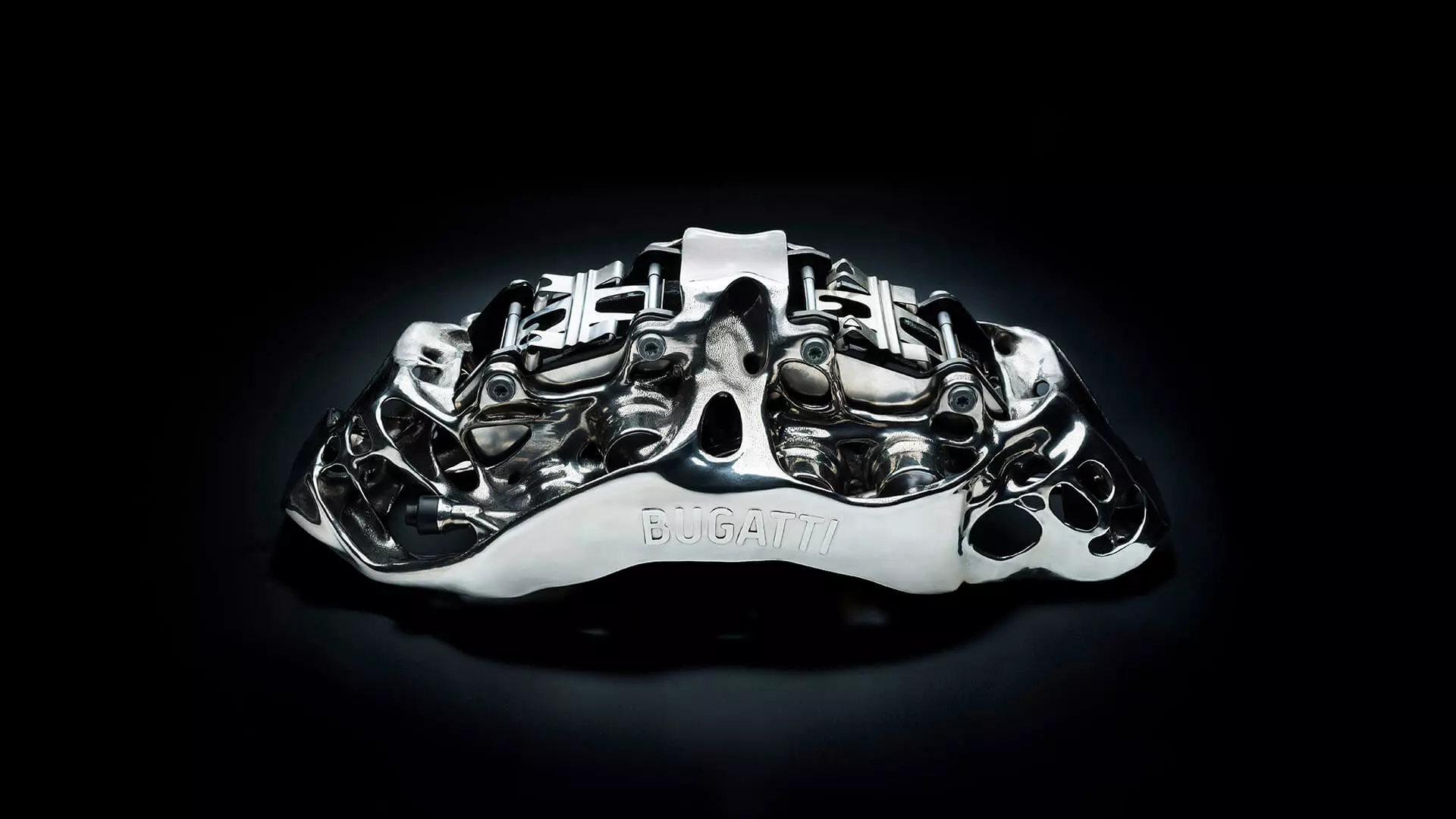
piedevu ražošana
Šie jaunie titāna bremžu suporti ir Bugatti attīstības departamenta un Laser Zentrum Nord sadarbības rezultāts. Pirmo reizi transportlīdzekļu detaļu drukāšanai alumīnija vietā tika izmantots titāns, kas radīja izaicinājumus. Titāna augstā izturība ir bijis galvenais iemesls, kāpēc šis materiāls nav izmantots, kas lika ķerties pie augstas veiktspējas printera.Šis īpašais 3D printeris, kas atrodas uz Laser Zentrum Nord, kas projekta sākumā bija lielākais pasaulē, kas spēja apstrādāt titānu, ir aprīkots ar četriem 400 W lāzeriem.
Katras pincetes izdrukāšanai nepieciešamas 45 stundas.
Šī procesa laikā titāna pulveris tiek uzklāts slānis pa slānim, četriem lāzeriem izkausējot pulveri iepriekš noteiktā formā. Materiāls gandrīz nekavējoties atdziest, un skava sāk veidot formu.
Kopumā ir nepieciešami aptuveni 2213 slāņi, līdz gabals ir pabeigts.
Pēc pēdējā slāņa uzklāšanas lieko materiālu izņem no drukas kameras, iztīra un konservē atkārtotai izmantošanai. Bremžu suports, jau nokomplektēts, paliek kamerā, atbalstīts ar balstu, kas ļauj tai saglabāt formu. Atbalsts, kas tiek noņemts pēc tam, kad komponents ir saņēmis termisko apstrādi (kas sasniedz 700 ºC), lai to stabilizētu un garantētu vēlamo pretestību.
Virsma ir pabeigta, apvienojot mehāniskos, fizikālos un ķīmiskos procesus, kas arī palīdz uzlabot tās noguruma izturību. Funkcionālo virsmu, piemēram, virzuļu kontaktu, kontūru optimizēšana prasa vairāk nekā 11 stundas, izmantojot piecu asu apstrādes centru.
Bugatti, grupas līderis 3D drukāšanā
Līdz ar to Bugatti ieņem vadošo pozīciju Volkswagen grupā ne tikai 3D drukas tehnoloģiju, bet arī augsto tehnoloģiju lietojumu ziņā. Sava veida miljonāru laboratorija un ļoti, ļoti spēcīga...
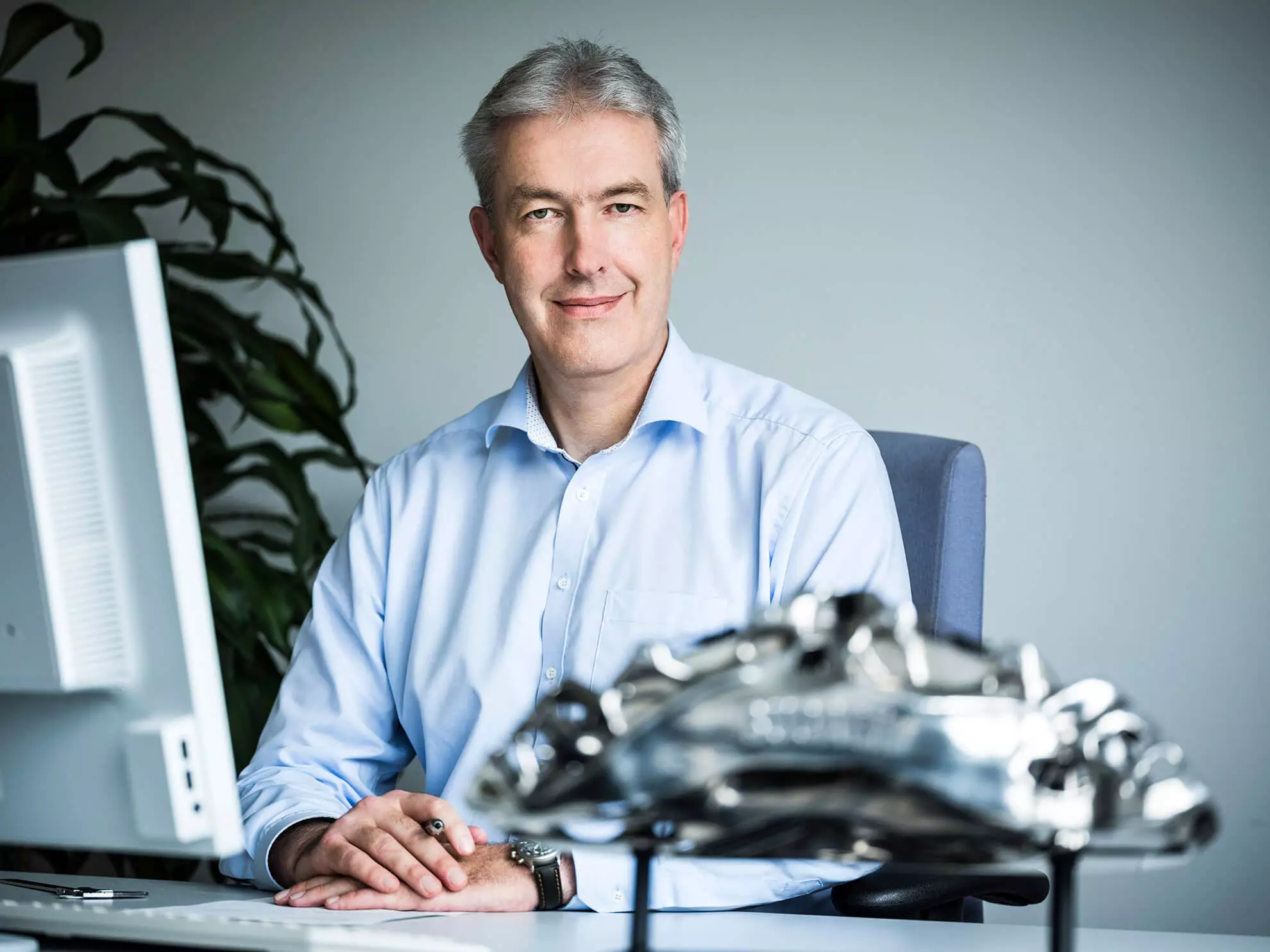
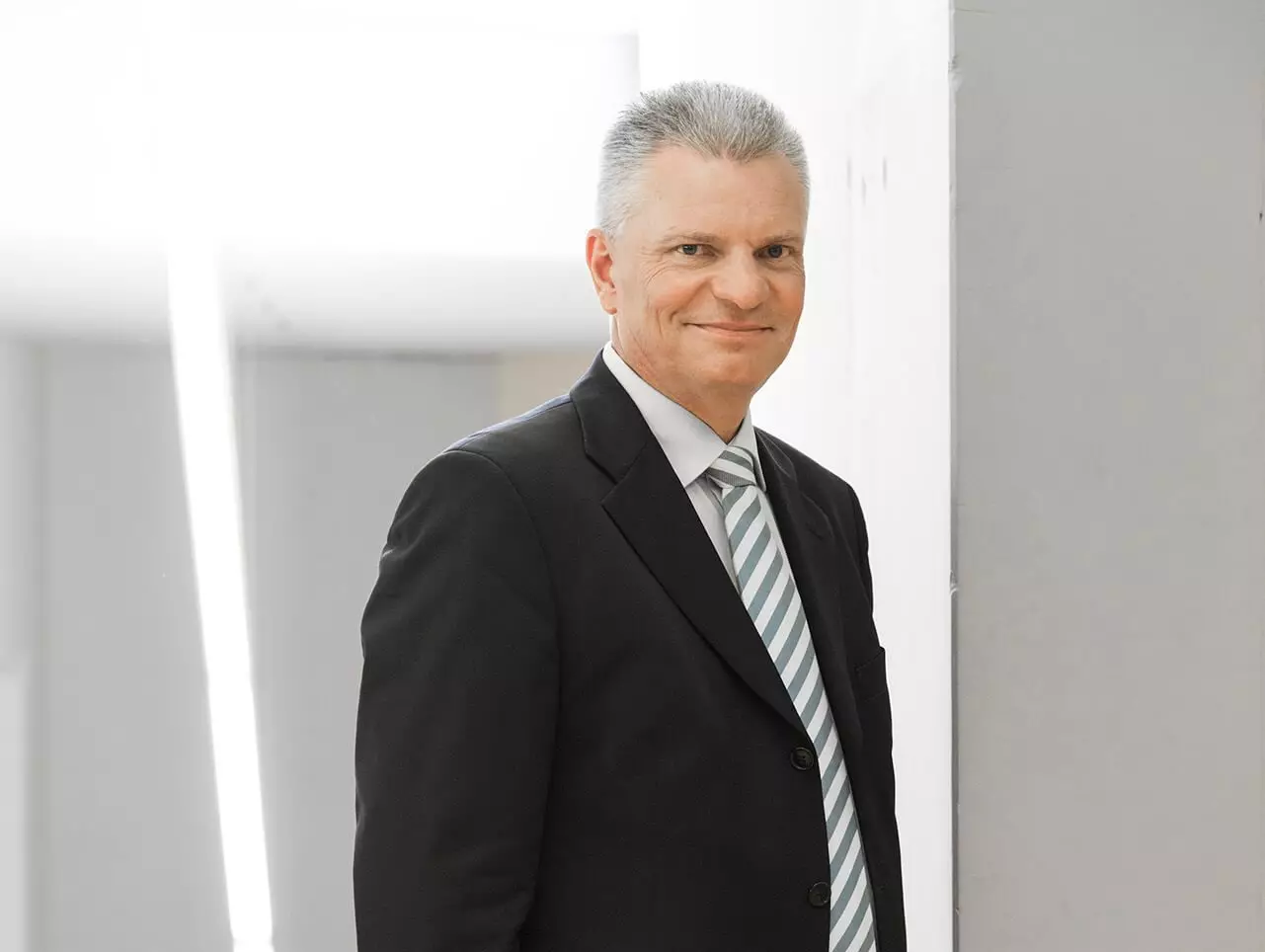