DE bugatti chiron är en maskin av superlativ - även om den på något sätt skadades till sin ära av en rival av svenskt ursprung... - och har precis fått ännu en superlativ av vikt, med tillägget av nya bromsok i titan, som bör introduceras i denna modell senare år.
Som ni vet är Bugatti Chiron var redan "ägare" till de största bromsoken i bilindustrin. Dessa bromsok var smidda av ett höghållfast aluminiumlegeringsblock med åtta titankolvar fram och sex kolvar bak. Än så länge…
starkare och lättare
Bugatti har nu tagit ytterligare ett steg framåt genom att utveckla bromsok i titan – fortfarande de största i branschen – som nu inte bara är den största funktionella komponenten i titan som produceras genom 3D-utskrift, eftersom det är det första bromsoket som produceras med denna metod.
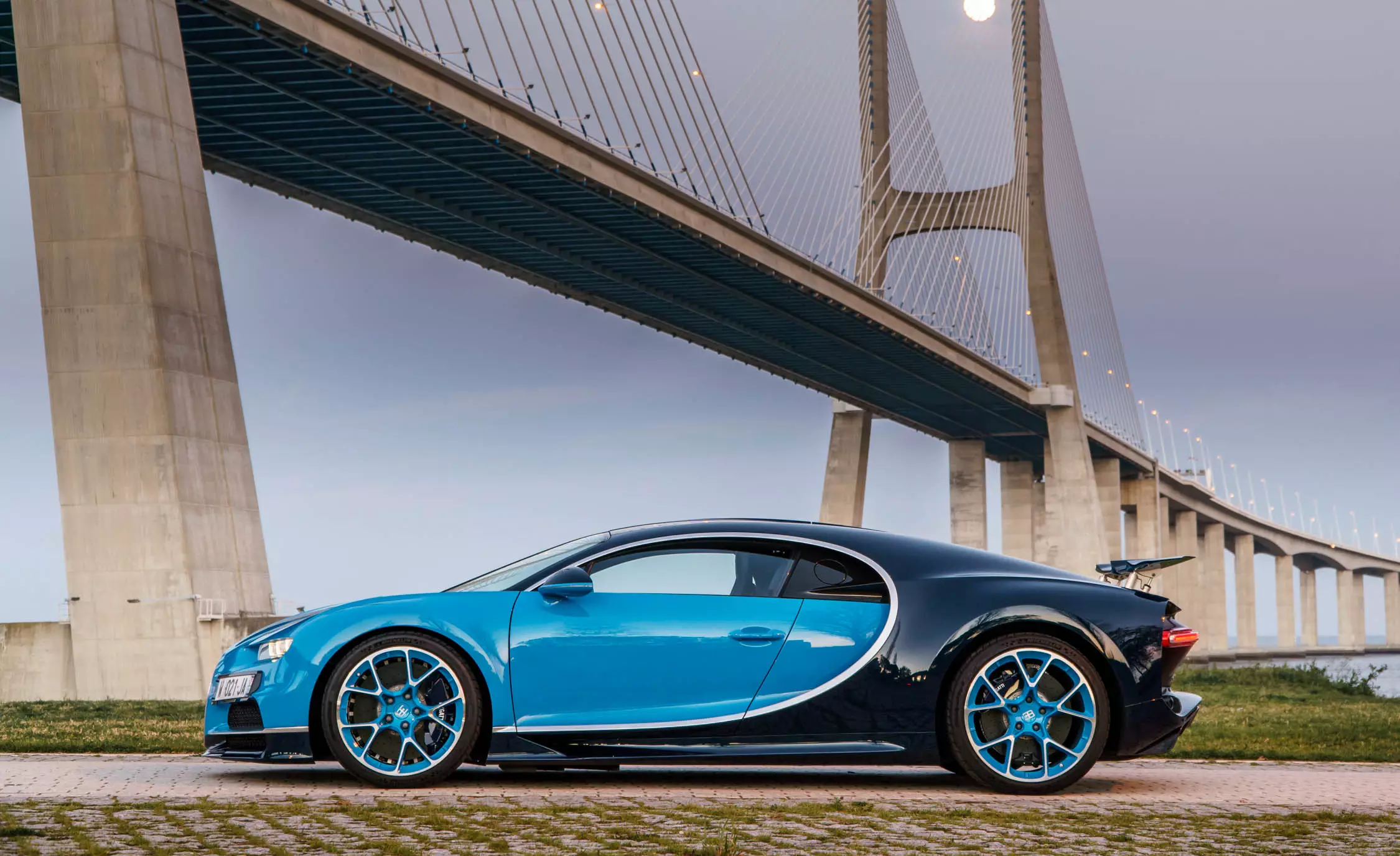
Den nya pincetten använder som material en titanlegering - Ti6AI4V från dess namn -, som främst används av flygindustrin i komponenter som utsätts för enorma påfrestningar, och erbjuder en prestanda som är mycket överlägsen aluminium. Draghållfastheten är naturligtvis extremt hög: 1250 N/mm2 , vilket innebär en applicerad kraft på drygt 125 kg per kvadratmillimeter utan att denna titanlegering går sönder.
Det nya bromsoket är 41 cm långt, 21 cm brett och 13,6 cm högt och har, förutom sin överlägsna styrka, den stora fördelen att det minskar vikten avsevärt, vilket påverkar de ständigt viktiga ofjädrade massorna. Väger endast 2,9 kg mot 4,9 kg av samma aluminiumdel, vilket motsvarar en minskning med 40 %.
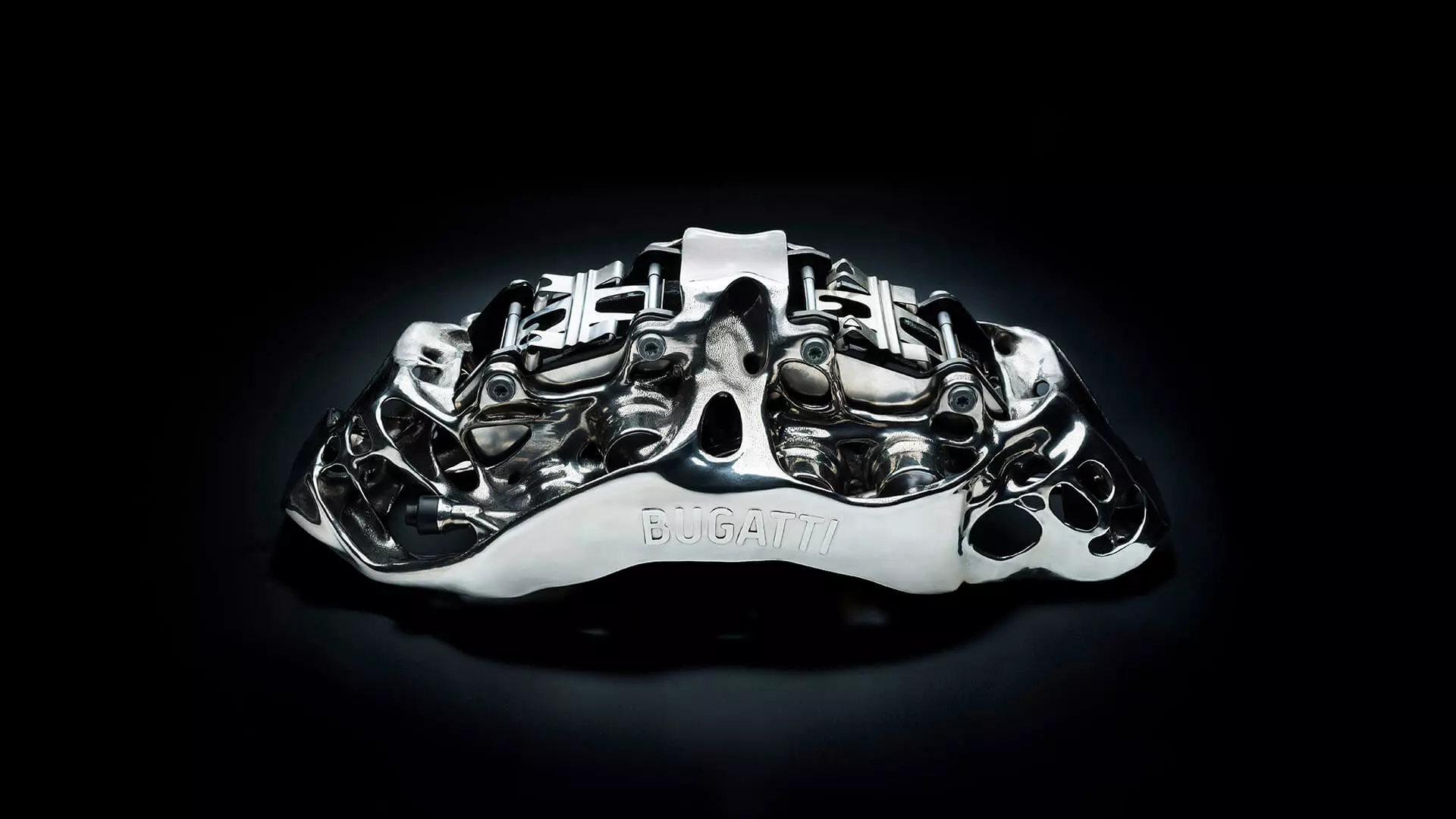
additiv tillverkning
Dessa nya bromsok i titan är resultatet av samarbete mellan Bugatti Development Department och Laser Zentrum Nord. För första gången användes titan i stället för aluminium för att skriva ut fordonskomponenter, vilket medförde utmaningar. Den höga styrkan hos titan har varit den främsta anledningen till att detta material inte har använts, vilket tvingade tillvägagången till en högpresterande skrivare.Denna speciella 3D-skrivare, belägen på Laser Zentrum Nord, som var den största i världen som kunde hantera titan i början av projektet, är utrustad med fyra 400W lasrar.
Varje pincett tar 45 timmar att skriva ut.
Under denna process avsätts titanpulver lager för lager, med de fyra lasrarna som smälter pulvret till den förutbestämda formen. Materialet svalnar nästan omedelbart och klämman börjar ta form.
Totalt behövs cirka 2213 lager tills stycket är färdigt.
Efter att det sista lagret har avsatts, avlägsnas överskottsmaterialet från tryckkammaren, rengörs och konserveras för återanvändning. Bromsoket, som redan är färdigt, förblir i kammaren, uppburet av ett stöd, vilket gör att det kan bevara sin form. Stöd som tas bort efter att komponenten genomgått en värmebehandling (som når 700 ºC) för att stabilisera den och garantera önskat motstånd.
Ytan ytbehandlas genom en kombination av mekaniska, fysikaliska och kemiska processer, vilket också bidrar till att förbättra dess utmattningshållfasthet. Det tar mer än 11 timmar att optimera konturerna av funktionella ytor, såsom kolvkontakter, med hjälp av ett femaxligt bearbetningscenter.
Bugatti, gruppledare inom 3D-utskrift
Med detta tar Bugatti ledningen i Volkswagen-koncernen inte bara när det gäller 3D-utskriftsteknik, utan även när det gäller högteknologiska applikationer. Ett slags miljonärslaboratorium och väldigt, väldigt kraftfullt...
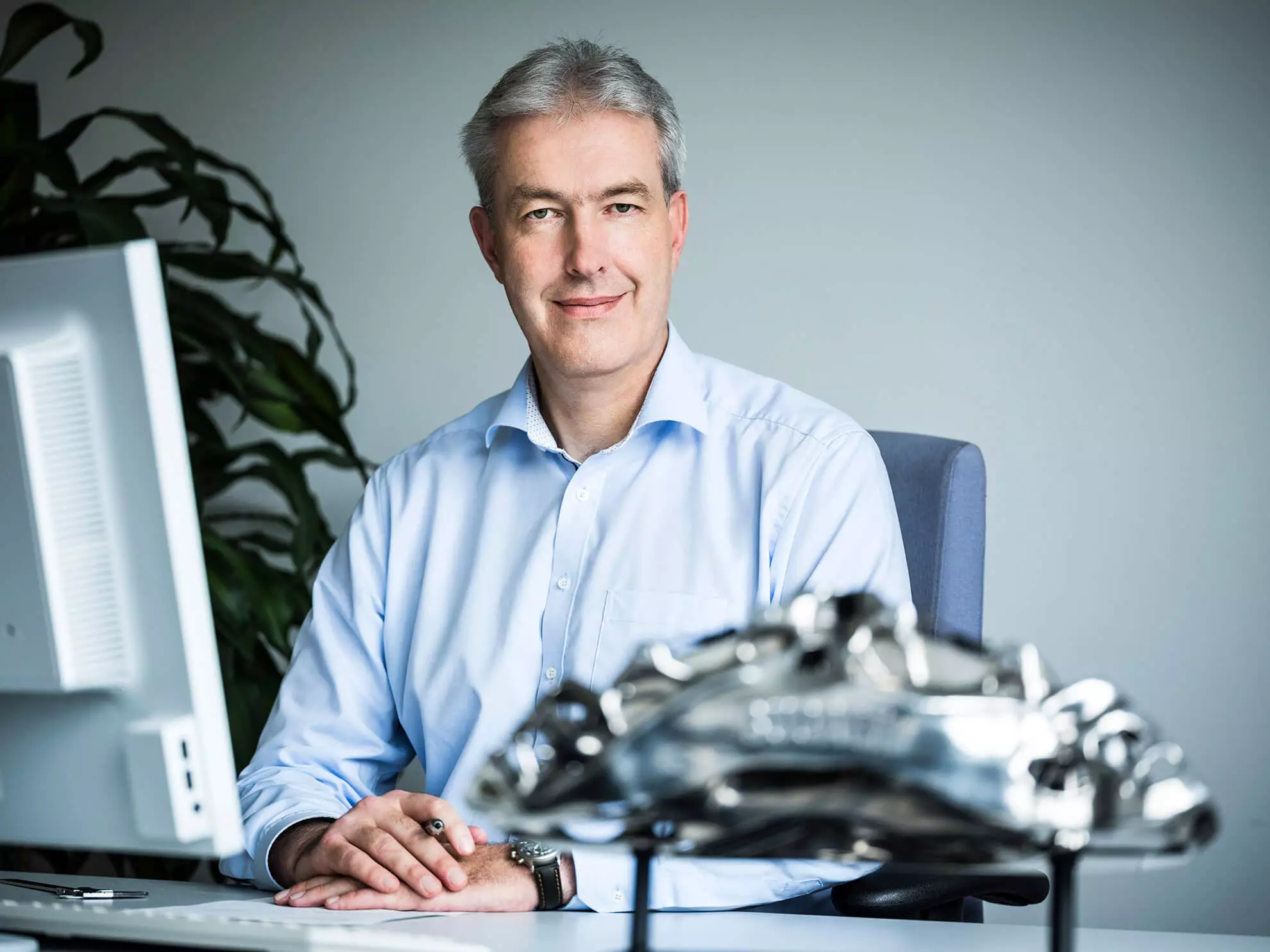
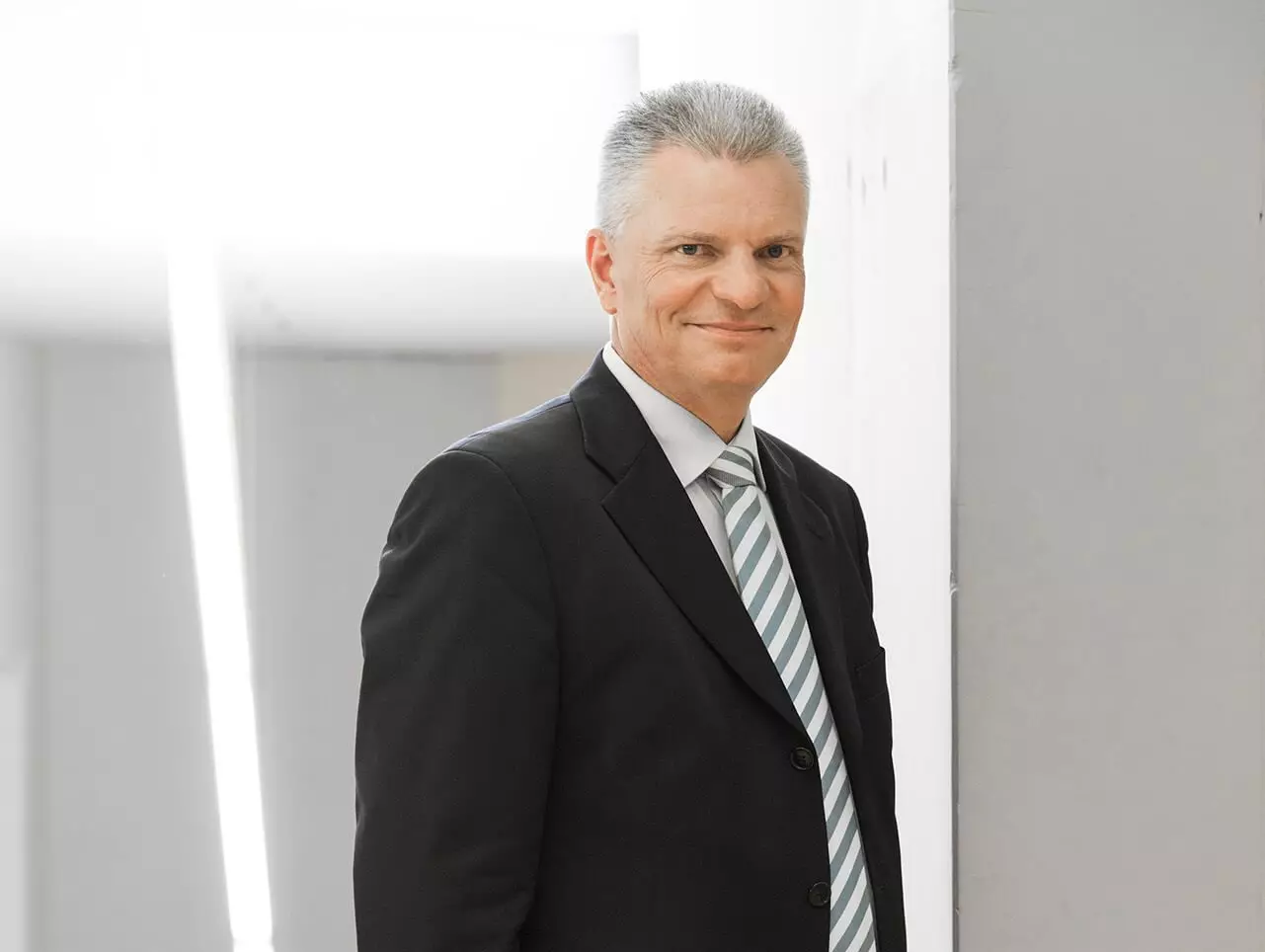