bu bugatti chiron bir üstünlükler makinesidir — bir şekilde İsveç kökenli bir rakip tarafından onuruna yaralanmış olsa da… — ve bu modelde daha sonra tanıtılması gereken yeni titanyum fren kaliperlerinin eklenmesiyle bir başka üstün ağırlık kazanmıştır. yılda.
Bildiğiniz gibi, Bugatti Chiron, otomotiv endüstrisindeki en büyük fren kaliperlerinin zaten “sahibiydi”. Bu kaliperler, önde sekiz titanyum pistonlu ve arkada altı pistonlu, yüksek mukavemetli alüminyum alaşımlı bir bloktan dövüldü. Şimdiye kadar…
daha güçlü ve daha hafif
Bugatti, endüstrinin en büyüğü olan titanyum fren kaliperleri geliştirerek şimdi bir adım daha attı. Bu yöntemle üretilen ilk fren kaliperi olduğu için titanyumdan 3D baskı yoluyla üretilen en büyük fonksiyonel bileşen.
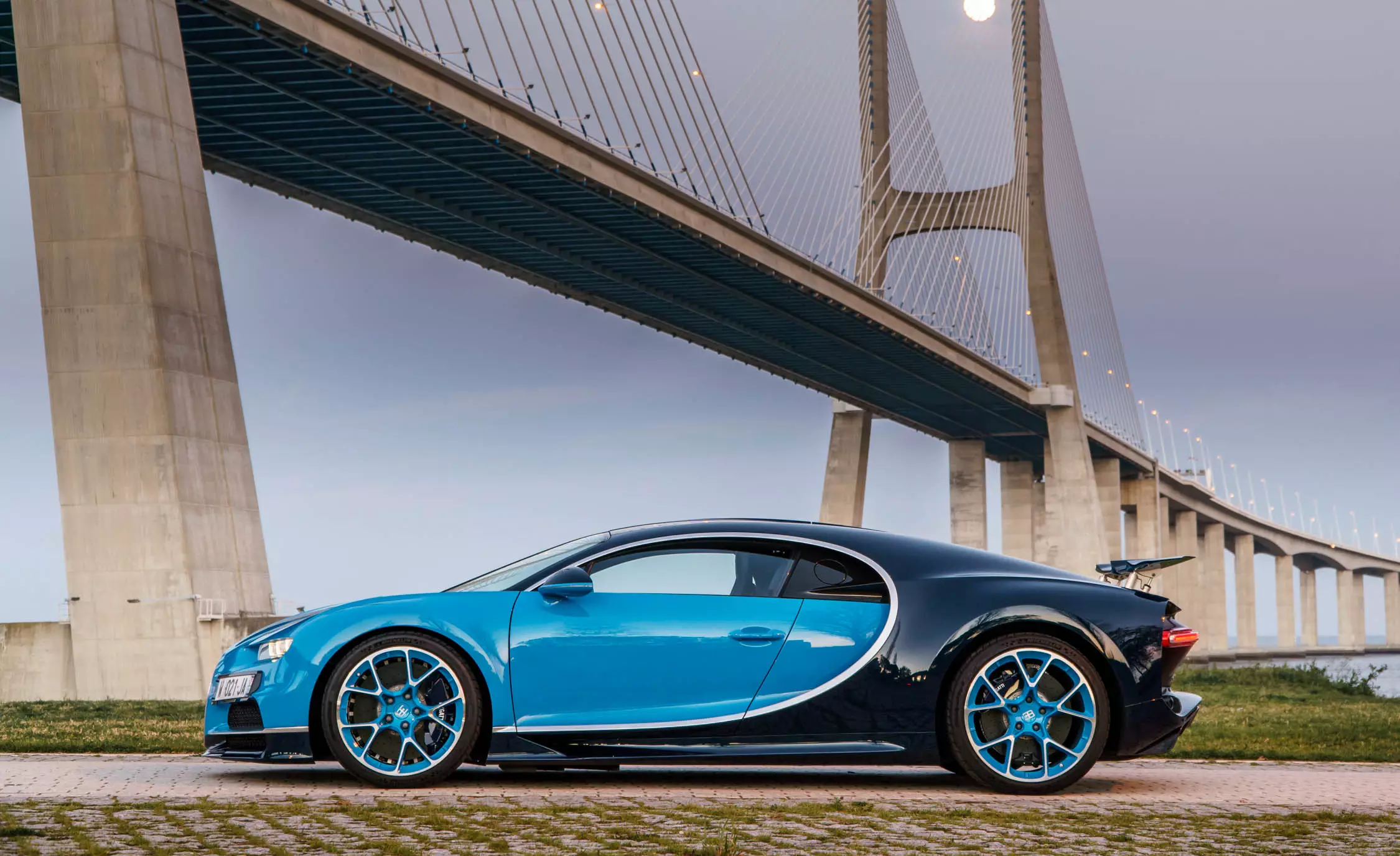
Yeni cımbızlar, malzeme olarak titanyum alaşımı - adından da anlaşılacağı üzere Ti6AI4V - kullanıyor ve bu alaşım, esas olarak havacılık endüstrisi tarafından muazzam strese maruz kalan bileşenlerde kullanılıyor ve alüminyumdan çok daha üstün bir performans sunuyor. Çekme mukavemeti elbette son derece yüksektir: 1250 N/mm2 , bu titanyum alaşımı kırılmadan milimetre kare başına 125 kg'ın biraz üzerinde bir uygulanan kuvvet anlamına gelir.
Yeni fren kaliperi 41 cm uzunluğunda, 21 cm genişliğinde ve 13,6 cm yüksekliğindedir ve üstün gücüne ek olarak, ağırlığı önemli ölçüde azaltma ve her zaman önemli olan yaysız kütleleri etkileme gibi büyük bir avantaja sahiptir. Sadece 2,9 kg ağırlığında Aynı alüminyum parçanın 4,9 kg'ına karşı, bu da %40'lık bir azalmaya eşittir.
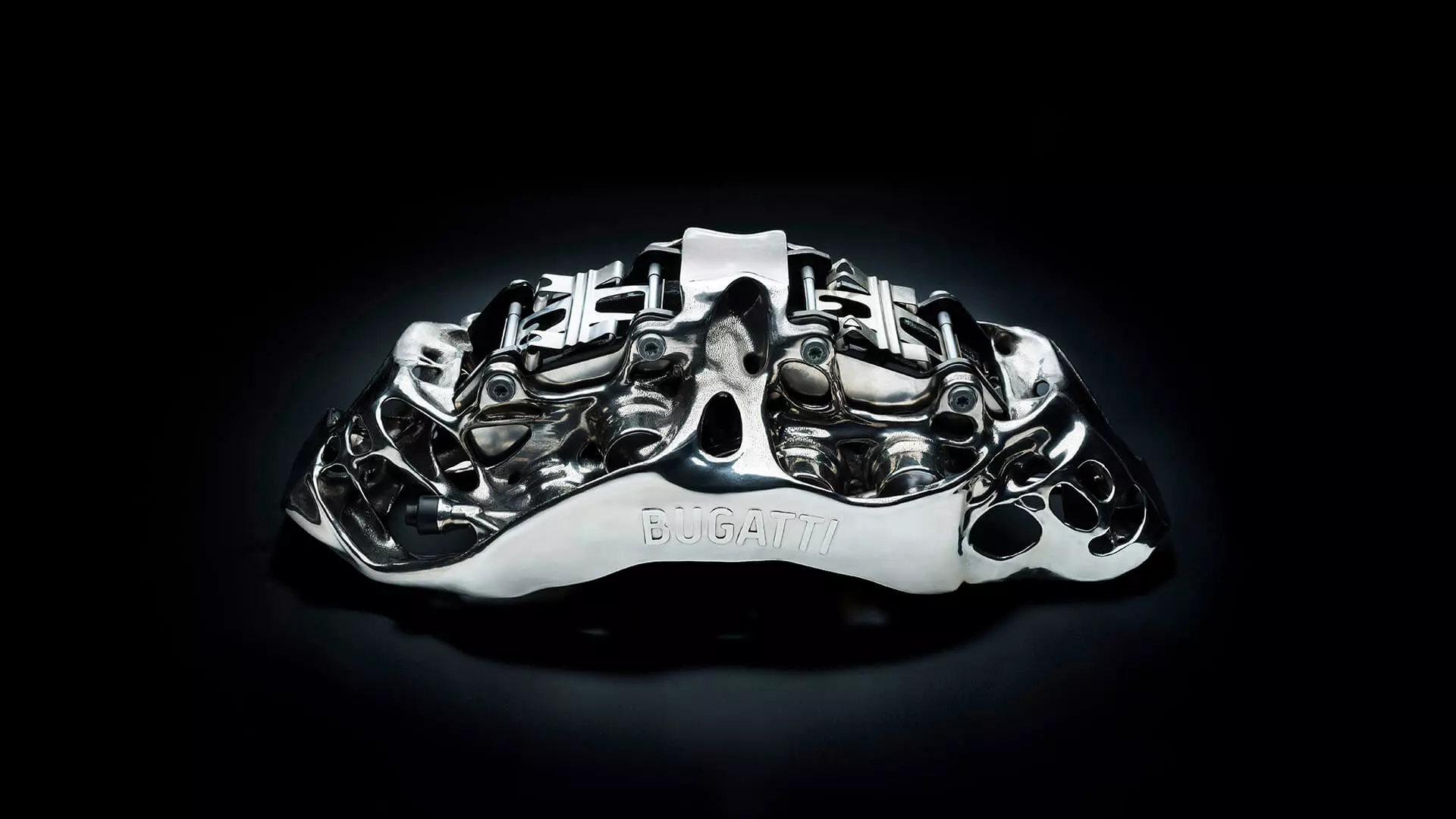
Katmanlı üretim
Bu yeni titanyum fren kaliperleri, Bugatti Geliştirme Departmanı ile Laser Zentrum Nord arasındaki işbirliğinin sonucudur. Araç bileşenlerini basmak için ilk kez alüminyum yerine titanyum kullanıldı ve bu da zorlukları beraberinde getirdi. Titanyumun yüksek mukavemeti, bu malzemenin kullanılmamasının ana nedeni olmuştur ve bu da tesisi yüksek performanslı bir yazıcıya zorlamıştır.Projenin başlangıcında titanyum işleme kapasitesine sahip dünyanın en büyüğü olan Laser Zentrum Nord üzerinde bulunan bu özel 3D yazıcı, dört adet 400W lazerle donatılmıştır.
Her cımbızın yazdırılması 45 saat sürer.
Bu işlem sırasında titanyum tozu, dört lazer tozu önceden belirlenmiş bir şekle eriterek katman katman biriktirilir. Malzeme neredeyse anında soğur ve kelepçe şekillenmeye başlar.
Parça tamamlanana kadar toplamda yaklaşık 2213 katmana ihtiyaç vardır.
Son katman yerleştirildikten sonra, fazla malzeme baskı odasından çıkarılır, temizlenir ve yeniden kullanım için korunur. Halihazırda tamamlanmış olan fren kaliperi, şeklini korumasına izin veren bir destek tarafından desteklenen haznede kalır. Bileşeni stabilize etmek ve istenen direnci garanti etmek için (700 ºC'ye ulaşan) bir ısıl işlem gördükten sonra kaldırılan destek.
Yüzey, yorulma mukavemetini artırmaya da katkıda bulunan mekanik, fiziksel ve kimyasal işlemlerin bir kombinasyonu ile tamamlanır. Beş eksenli bir işleme merkezi kullanarak piston kontakları gibi fonksiyonel yüzeylerin konturlarını optimize etmek 11 saatten fazla sürer.
Bugatti, 3D baskıda grup lideri
Bununla Bugatti, Volkswagen Grubu'nda sadece 3D baskı teknolojisinde değil, aynı zamanda yüksek teknolojili uygulamalarda da liderliği alıyor. Bir tür milyoner laboratuvarı ve çok, çok güçlü...
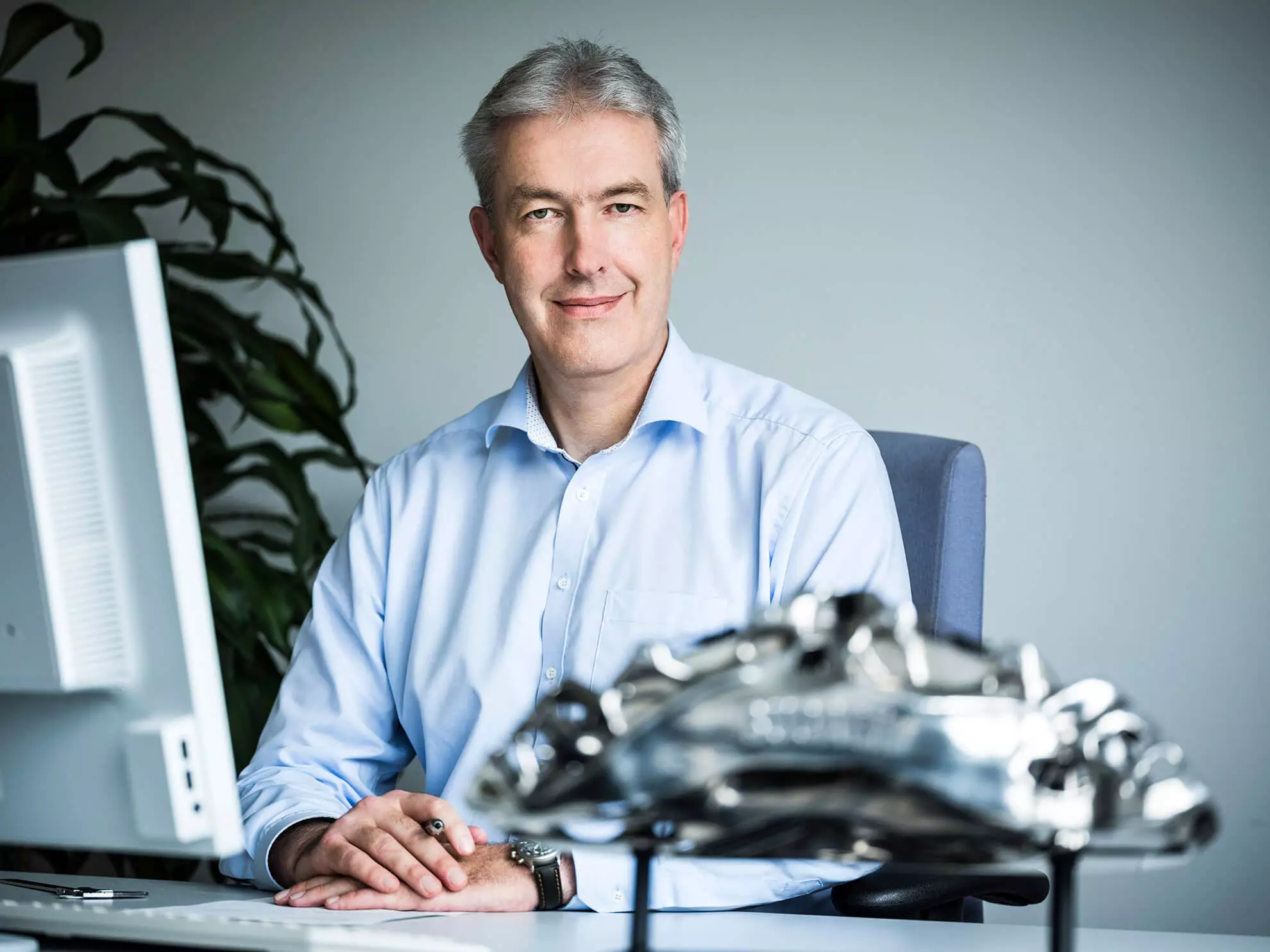
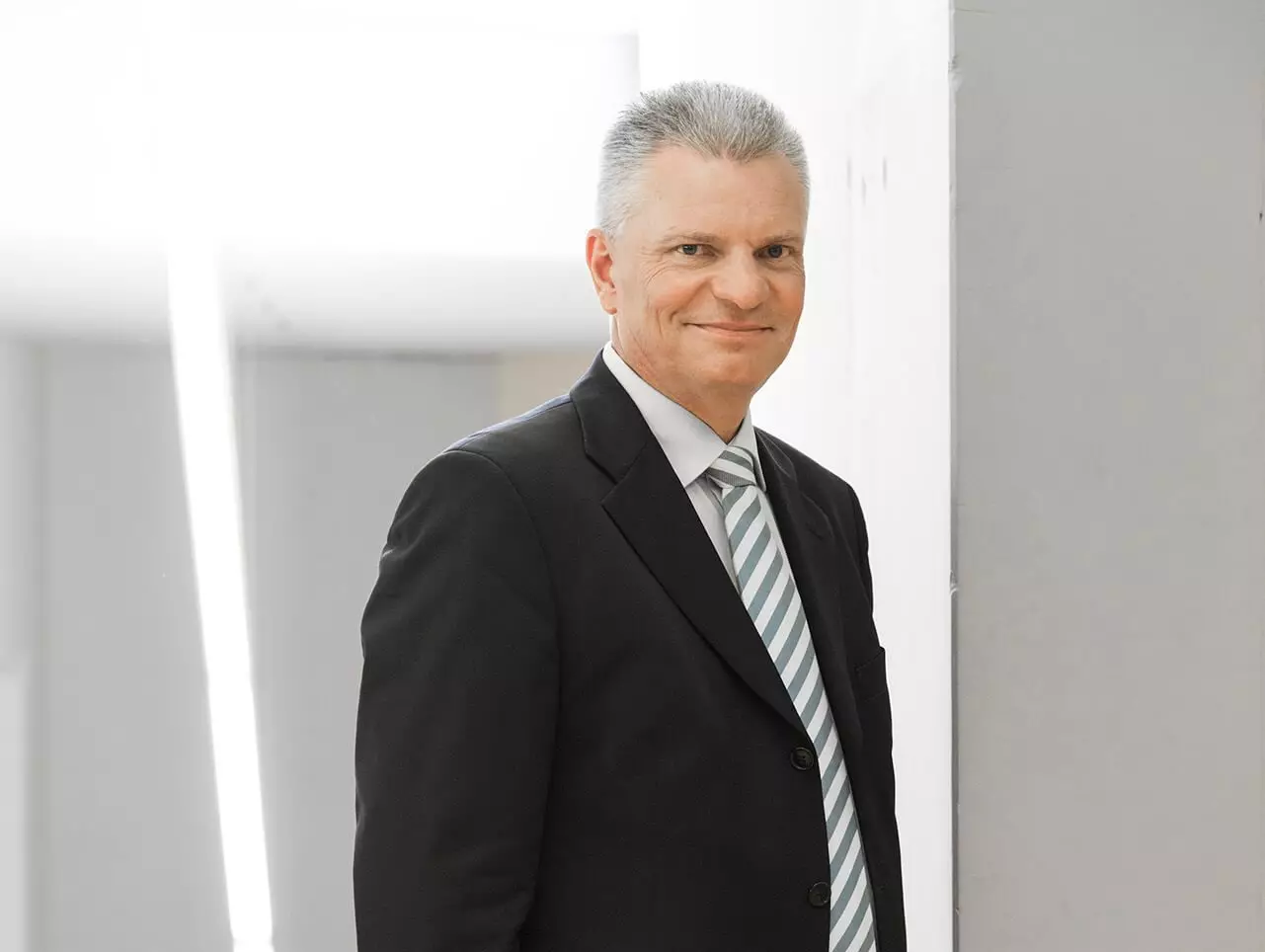