LA bugatti chiron estas maŝino de superlativoj — kvankam ĝi estis iel vundita en sia honoro de rivalo de sveda deveno... — kaj ĵus akiris ankoraŭ plian superlativon de pezo, kun aldono de novaj titanaj bremskalibriloj, kiuj devus esti enkondukitaj en ĉi tiu modelo poste. en la jaro.
Kiel vi scias, la Bugatti Chiron jam estis la "posedanto" de la plej grandaj bremsoj en la aŭtindustrio. Tiuj kalibriloj estis forĝitaj de alt-forta aluminialojbloko kun ok titaniopiŝtoj ĉe la fronto kaj ses piŝtoj ĉe la malantaŭo. Ĝis nun…
pli forta kaj malpeza
Bugatti nun faris alian paŝon antaŭen, disvolvante titanajn bremskurilojn - ankoraŭ la plej grandajn en la industrio - kiuj nun estas ne nur la plej granda funkcia komponento en titanio produktita per 3D-presado, ĉar ĝi estas la unua bremskalibrilo estanta produktita per tiu metodo.
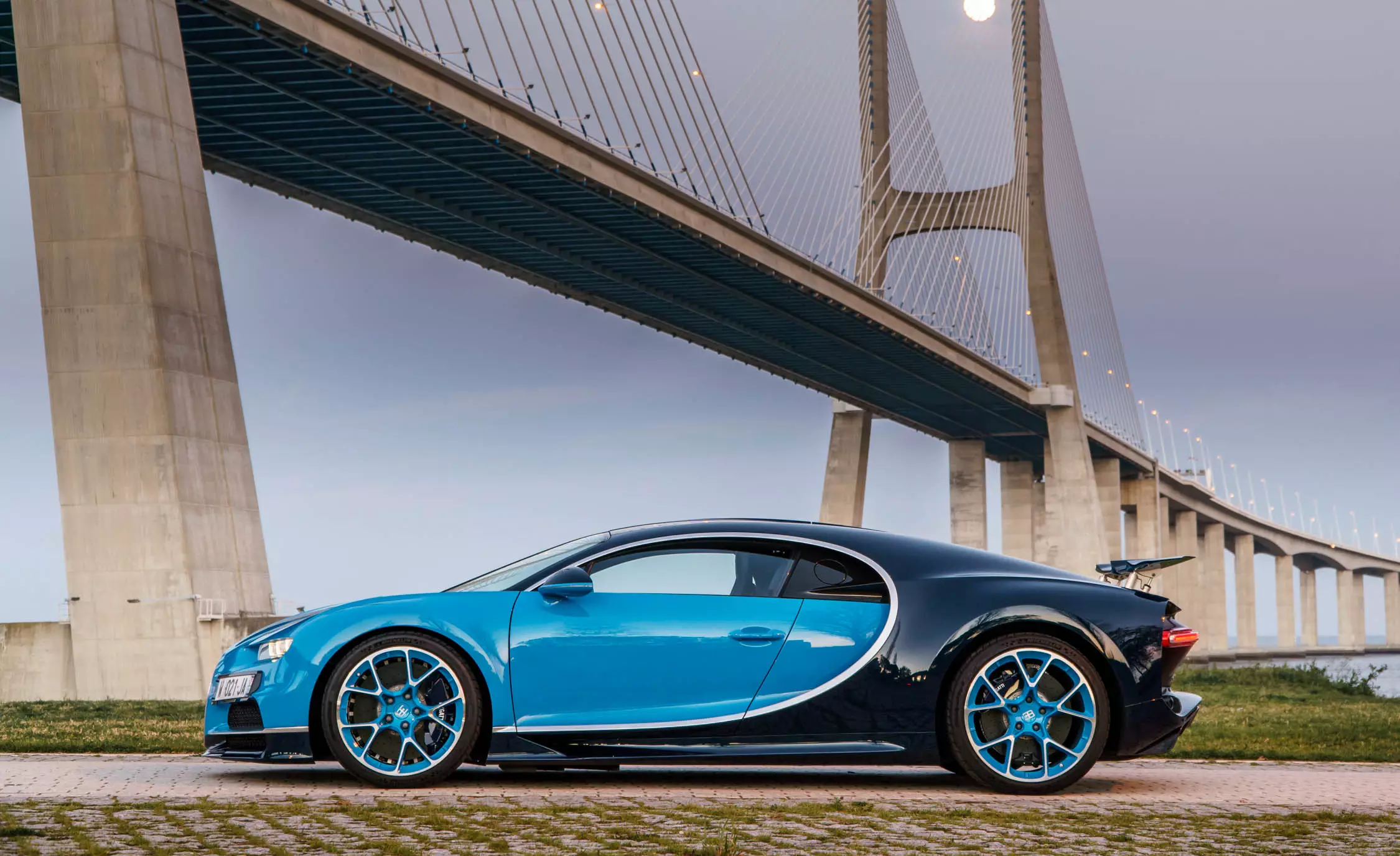
La novaj pinĉiloj uzas kiel materialon titanan alojon — Ti6AI4V el sia nomo —, uzatan ĉefe de la aerspaca industrio en komponantoj submetitaj al grandega streĉo, proponante rendimenton multe pli alta ol tiu de aluminio. La tirforto estas, kompreneble, ekstreme alta: 1250 N/mm2 , kio signifas aplikatan forton de iom pli ol 125 kg po kvadrata milimetro sen rompi ĉi tiu titana alojo.
La nova bremskalibrilo longas 41 cm, larĝas 21 cm kaj altas 13,6 cm kaj, krom sia supera forto, ĝi havas la grandan avantaĝon grave malpliigi pezon, tuŝante la ĉiam gravajn nesaltiĝintajn masojn. Pezas nur 2,9 kg kontraŭ 4,9 kg de la sama aluminia parto, kio egalas al 40% redukto.
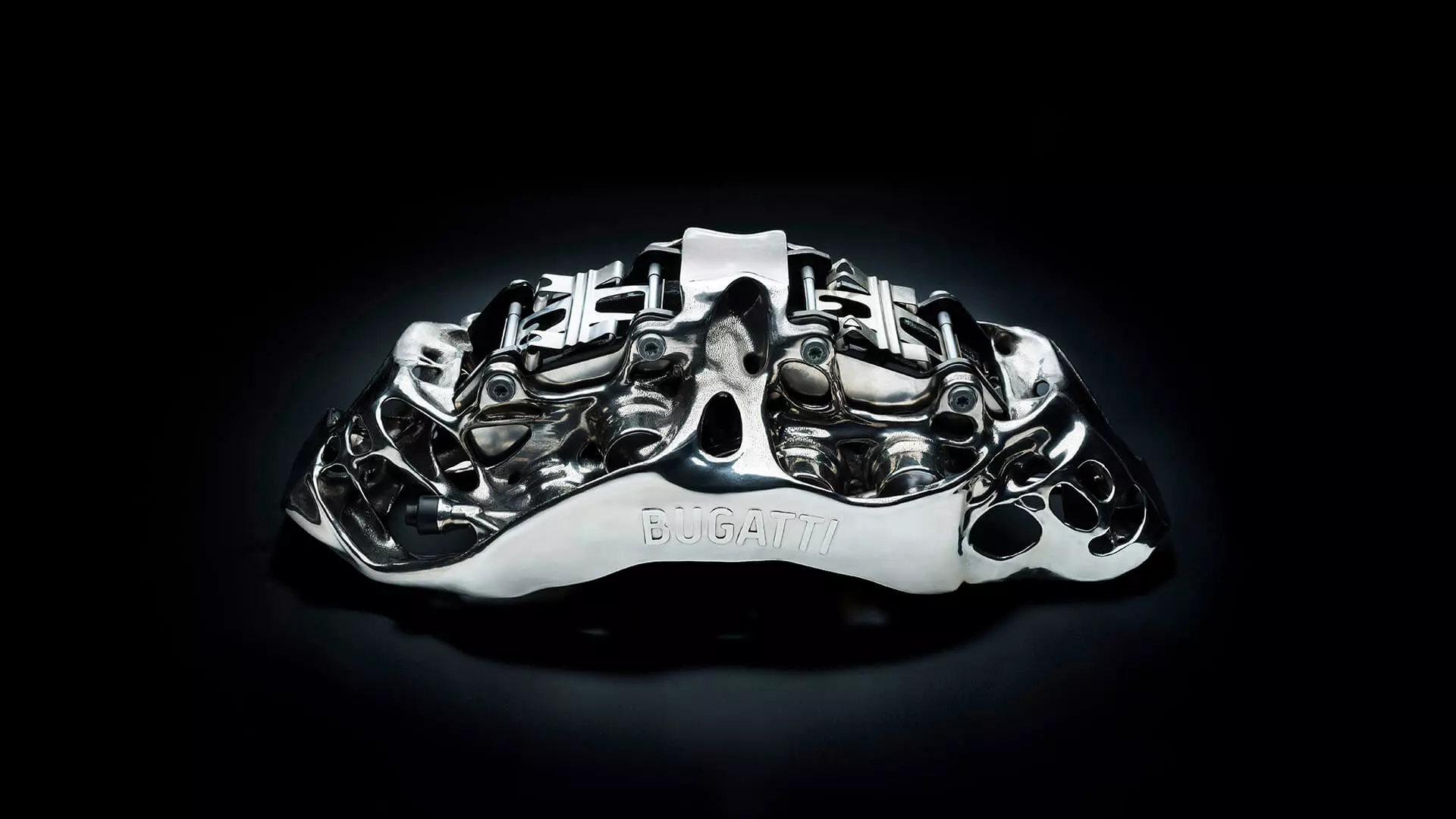
aldona fabrikado
Ĉi tiuj novaj titanaj bremskalibriloj estas la rezulto de kunlaboro inter la Bugatti Development Department kaj Laser Zentrum Nord. Por la unua fojo, titanio estis uzita anstataŭe de aluminio por presi veturilkomponentojn, kiuj alportis siajn defiojn. La alta forto de titanio estis la ĉefa kialo, kial ĉi tiu materialo ne estis uzata, kio devigis la feriejon al alt-efikeca presilo.Ĉi tiu speciala 3D-presilo, situanta sur la Laser Zentrum Nord, kiu estis la plej granda en la mondo kapabla pritrakti titanion komence de la projekto, estas ekipita per kvar 400W laseroj.
Ĉiu pinĉilo bezonas 45 horojn por presi.
Dum ĉi tiu procezo, titana pulvoro estas deponita tavolo post tavolo, kie la kvar laseroj fandas la pulvoron en la antaŭfiksitan formon. La materialo malvarmiĝas preskaŭ tuj, kaj la krampo komencas formiĝi.
Entute proksimume 2213 tavoloj estas bezonataj ĝis la peco estas kompleta.
Post kiam la lasta tavolo estas deponita, la troa materialo estas forigita el la presa ĉambro, purigita kaj konservita por reuzo. La bremskalibrilo, jam kompleta, restas en la kamero, subtenata de subteno, kiu permesas al ĝi konservi sian formon. Subteno, kiu estas forigita post kiam la komponanto ricevas varman traktadon (kiu atingas 700 ºC) por stabiligi ĝin kaj garantii la deziratan reziston.
La surfaco estas finita per kombinaĵo de mekanikaj, fizikaj kaj kemiaj procezoj, kiuj ankaŭ kontribuas al plibonigo de ĝia lacecforto. Necesas pli ol 11 horoj por optimumigi la konturojn de funkciaj surfacoj, kiel piŝtaj kontaktoj, uzante kvin-aksan maŝinan centron.
Bugatti, grupgvidanto en 3D presado
Kun ĉi tio, Bugatti prenas la gvidon en la Volkswagen-Grupo ne nur laŭ 3D-presa teknologio, sed ankaŭ laŭ altteknologiaj aplikoj. Ia milionula laboratorio kaj tre, tre potenca...
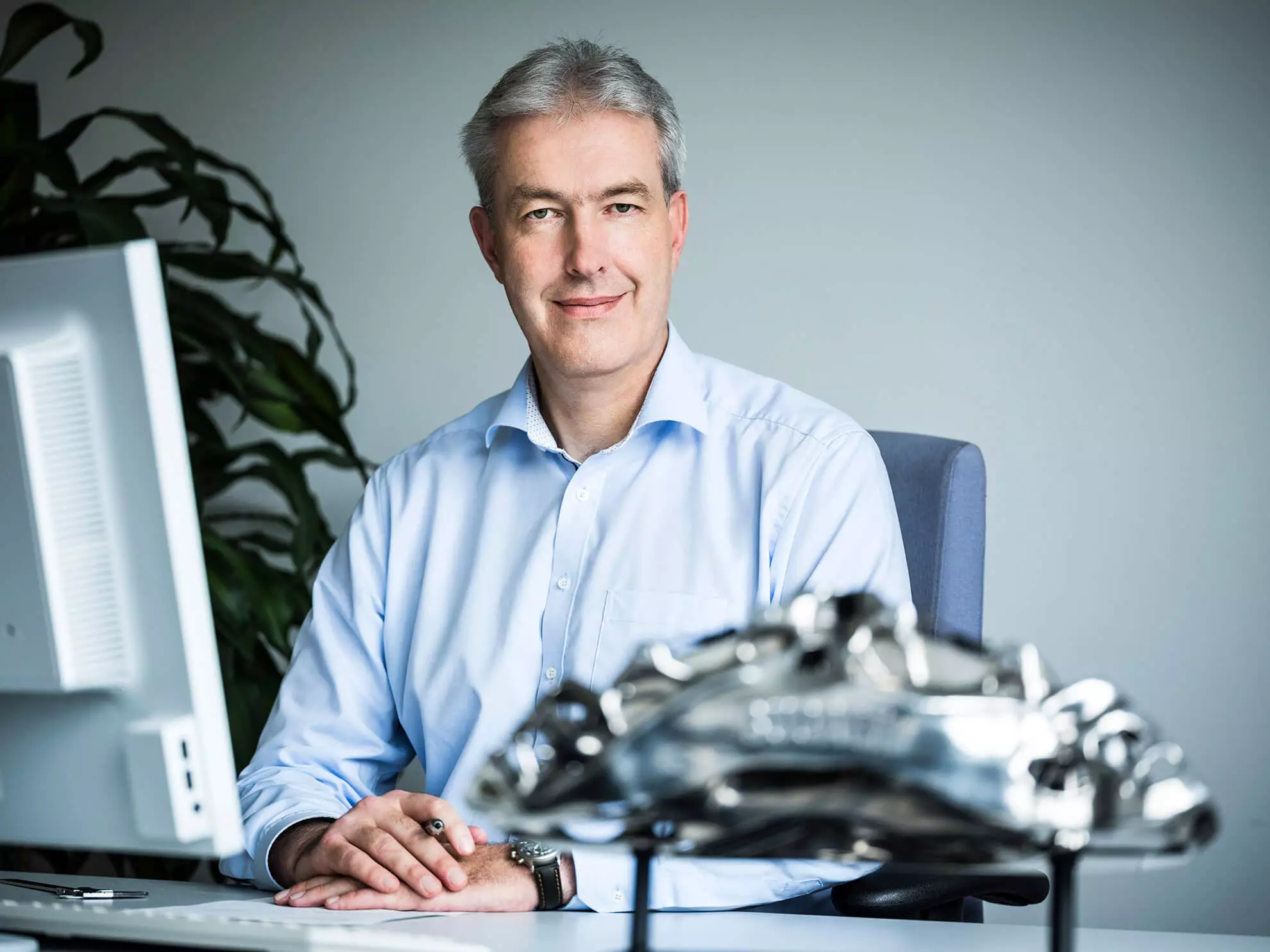
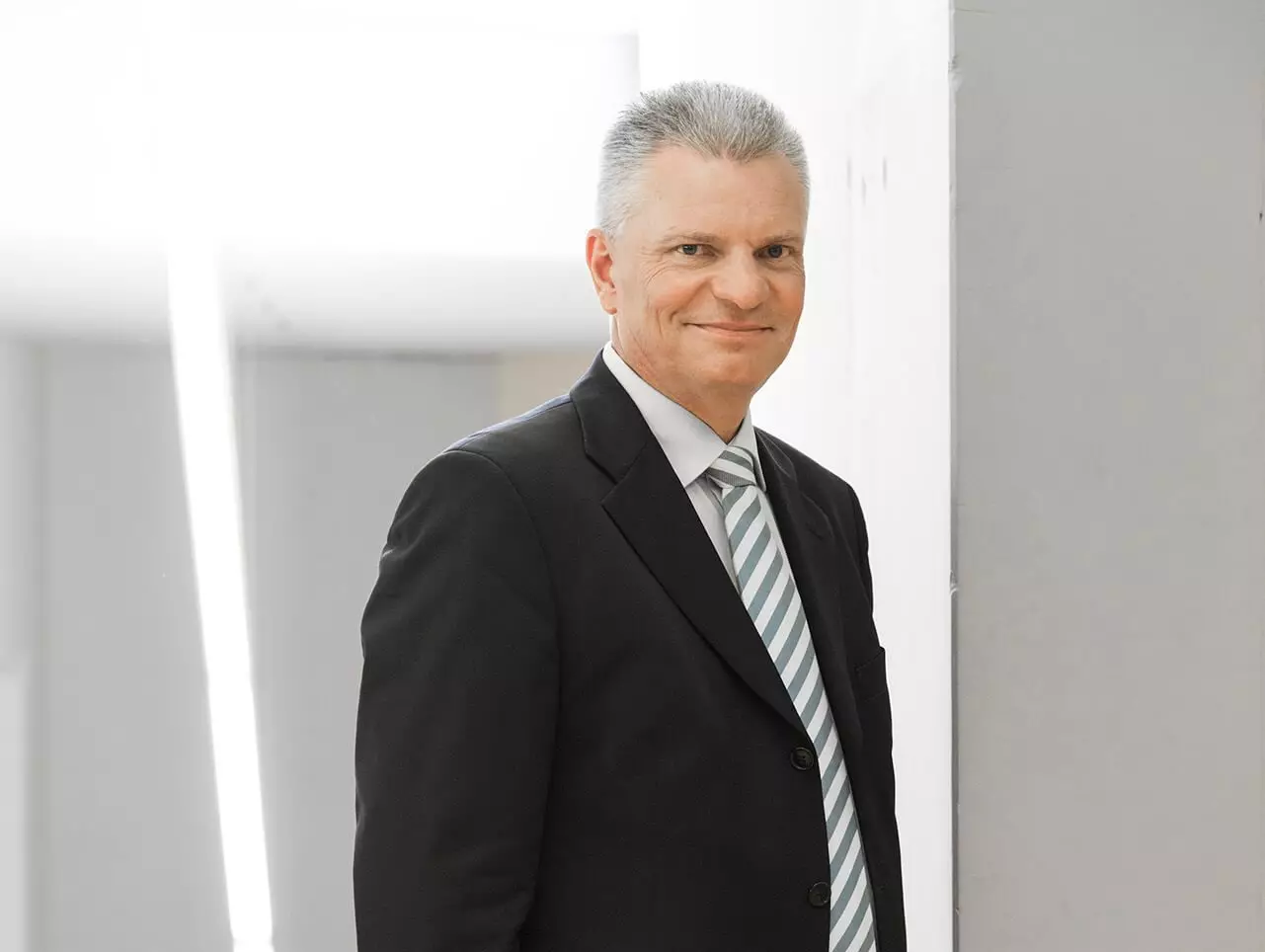