THE bugatti chiron superlatiboen makina bat da —nahiz eta bere omenez suediar jatorriko arerio batek nolabait zauritu zuen...—, eta beste pisu superlatibo bat irabazi berri du, titaniozko balazta-pintza berriak gehituta, gero modelo honetan sartu beharko liratekeenak. urtean.
Dakizuenez, Bugatti Chiron automobilgintzako balazta-pinten handienen "jabea" zen jada. Pintza hauek erresistentzia handiko aluminiozko aleazio bloke batetik forjatu ziren, aurrealdean titaniozko zortzi pistoirekin eta atzeko aldean sei pistoirekin. Orain arte…
indartsuagoa eta arinagoa
Bugatti-k beste urrats bat eman du orain, titaniozko balazta-pintzak garatuz —oraindik industriako handienak—, orain ez direnak bakarrik. 3D inprimaketaren bidez ekoizten den titanioaren osagai funtzional handiena, metodo honen bidez ekoizten den lehen balazta-pintza baita.
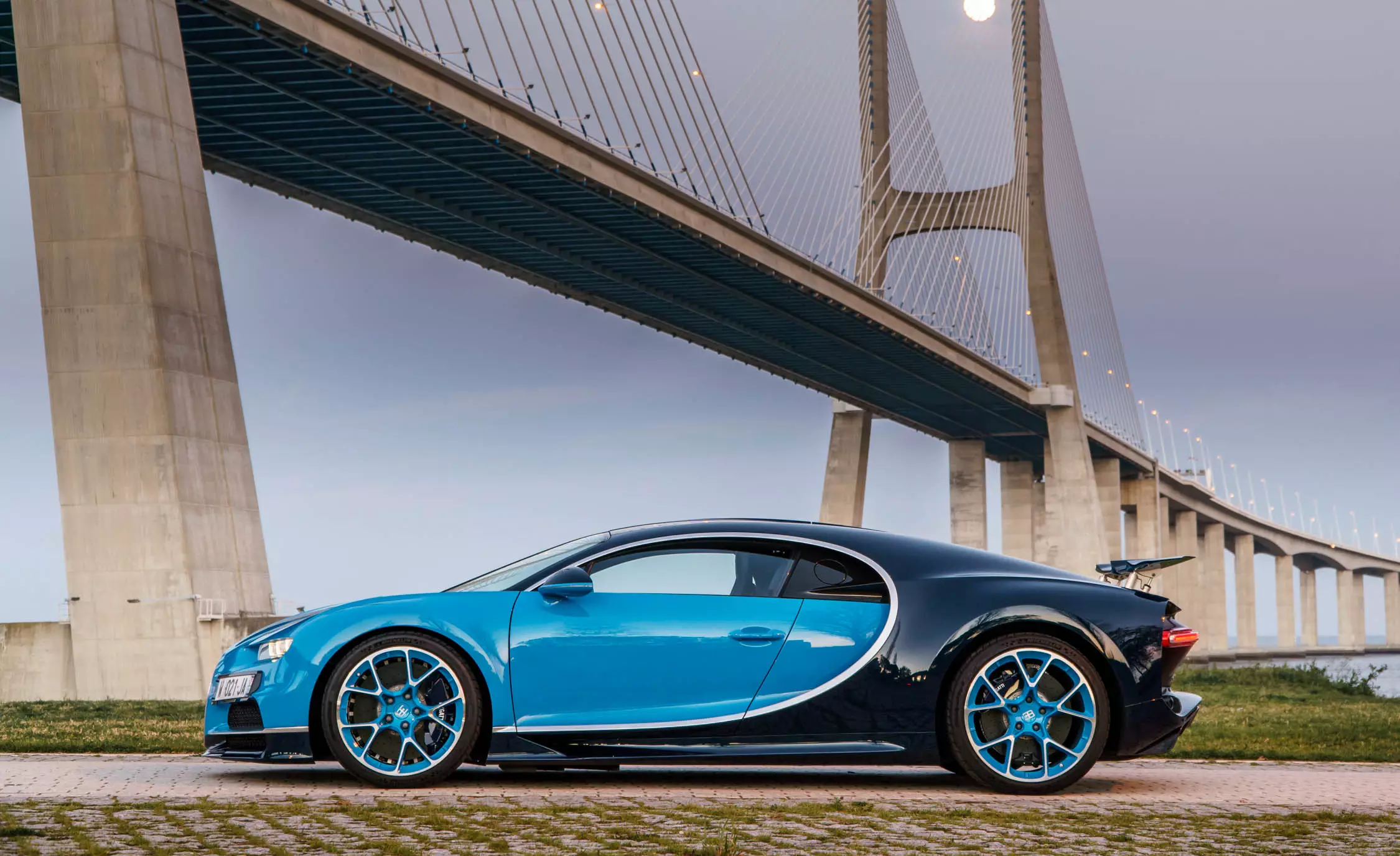
Pintza berriek material gisa titaniozko aleazio bat erabiltzen dute —Ti6AI4V bere izenetik—, industria aeroespazialak tentsio izugarria jasaten duten osagaietan erabiltzen duena batez ere, aluminioaren errendimendu handiagoa eskaintzen duena. Tentsio-erresistentzia, noski, oso handia da: 1250 N/mm2 , hau da, milimetro karratuko 125 kg pasatxoko indarra aplikatuko da titanio-aleazio hori hautsi gabe.
Balazta-pintza berriak 41 cm-ko luzera, 21 cm-ko zabalera eta 13,6 cm-ko altuera ditu eta, bere sendotasun handiagoaz gain, pisua nabarmen murrizteko abantaila handia du, beti garrantzitsuak ez diren udatu gabeko masei eraginez. 2,9 kg baino ez ditu pisatzen aluminiozko pieza bereko 4,9 kg-ren aurka, %40ko murrizketa dakar.
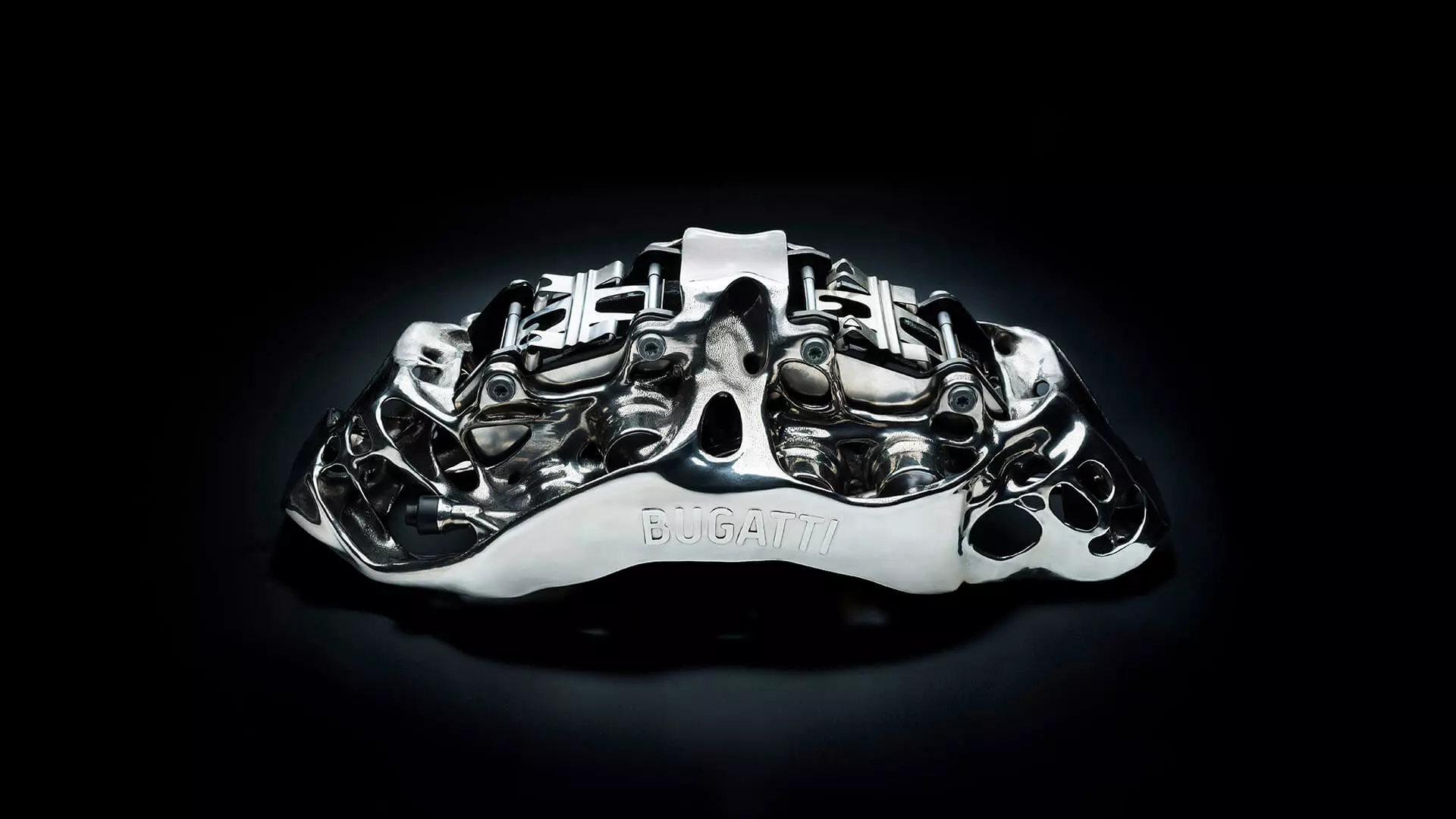
fabrikazio gehigarria
Titaniozko balazta-pintza berri hauek Bugatti Garapen Sailaren eta Laser Zentrum Norden arteko lankidetzaren emaitza dira. Lehenengo aldiz, aluminioaren ordez titanioa erabili zen ibilgailuen osagaiak inprimatzeko, eta horrek bere erronkak ekarri zituen. Titanioaren erresistentzia handia izan da material hori ez erabiltzeko arrazoi nagusia, eta horrek errendimendu handiko inprimagailu batera behartu zuen.Laser Zentrum Nord-en kokatutako 3D inprimagailu berezi hau, proiektuaren hasieran titanioa maneiatzeko gai zen munduko handiena izan zena, 400W-ko lau laserrez hornituta dago.
Pintza bakoitzak 45 ordu behar ditu inprimatzeko.
Prozesu horretan, titanio-hautsa geruzaz geruza jartzen da, eta lau laserek hautsa aurrez zehaztutako forman urtzen dute. Materiala ia berehala hozten da, eta besarkada forma hartzen hasten da.
Guztira 2213 geruza inguru behar dira pieza osatu arte.
Azken geruza metatu ondoren, soberan dagoen materiala inprimaketa-ganberatik kendu, garbitu eta berrerabiltzeko kontserbatzen da. Balazta-pintza, dagoeneko osatua, ganbaran geratzen da, euskarri batek eusten diona, eta horri esker bere forma gorde dadin. Osagaiak tratamendu termiko bat jaso ondoren (700 ºC-ra iristen dena) kentzen den euskarria egonkortzeko eta nahi den erresistentzia bermatzeko.
Gainazala prozesu mekaniko, fisiko eta kimikoen konbinazio baten bidez amaitzen da, eta neke erresistentzia hobetzen laguntzen dute. 11 ordu baino gehiago behar dira gainazal funtzionalen ingerada optimizatzeko, hala nola pistoi-kontaktuak, bost ardatzeko mekanizazio-zentro bat erabiliz.
Bugatti, 3D inprimaketaren taldeko liderra
Honekin, Bugattik Volkswagen Taldeko lidergoa hartzen du 3D inprimatzeko teknologiari dagokionez ez ezik, goi-teknologiako aplikazioei dagokienez ere. Laborategi milioidun moduko bat eta oso-oso indartsua...
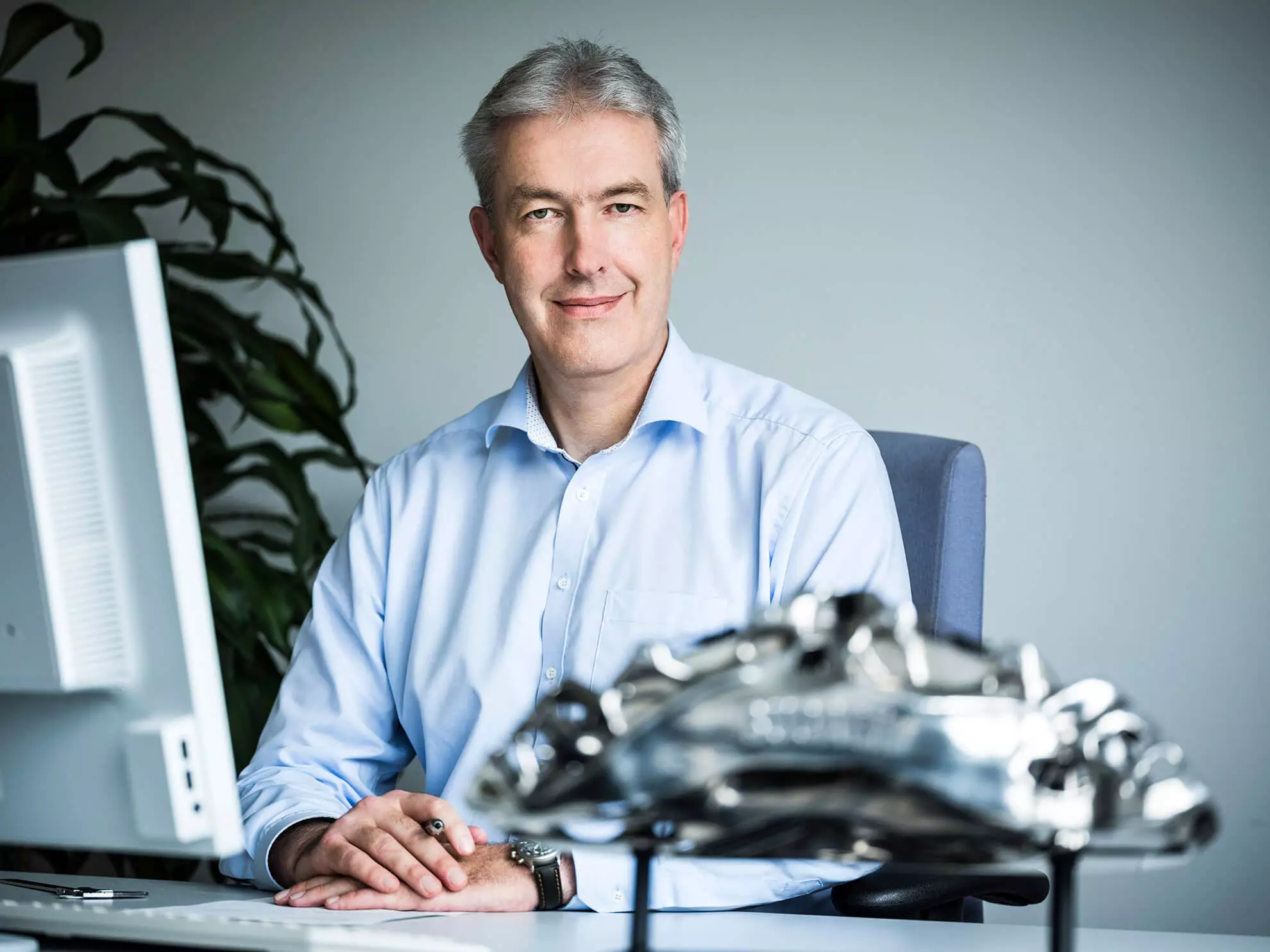
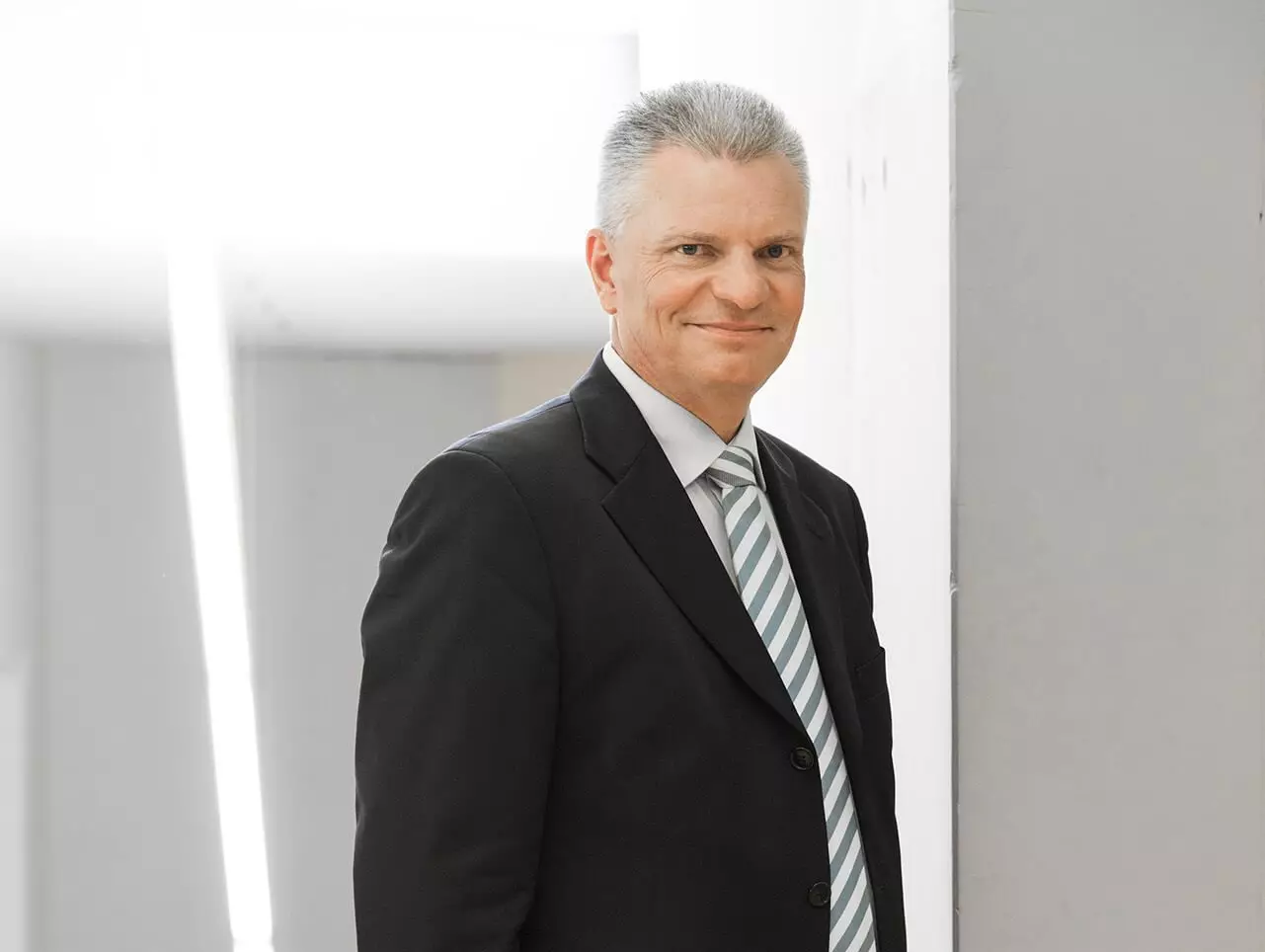