DE bugatti chiron is een machine van superlatieven - ook al werd hij op de een of andere manier ter ere van hem verwond door een rivaal van Zweedse afkomst ... - en heeft zojuist weer een superlatief aan gewicht gewonnen, met de toevoeging van nieuwe titanium remklauwen, die later in dit model zouden moeten worden geïntroduceerd in het jaar.
Zoals u weet, de Bugatti Chiron was al de "eigenaar" van de grootste remklauwen in de auto-industrie. Deze remklauwen zijn gesmeed uit een zeer sterk blok van aluminiumlegering met acht titanium zuigers voor en zes zuigers achter. Dusver…
sterker en lichter
Bugatti heeft nu een nieuwe stap voorwaarts gezet door titanium remklauwen te ontwikkelen - nog steeds de grootste in de branche - die nu niet alleen de grootste functionele component in titanium geproduceerd door middel van 3D-printen, aangezien het de eerste remklauw is die met deze methode wordt geproduceerd.
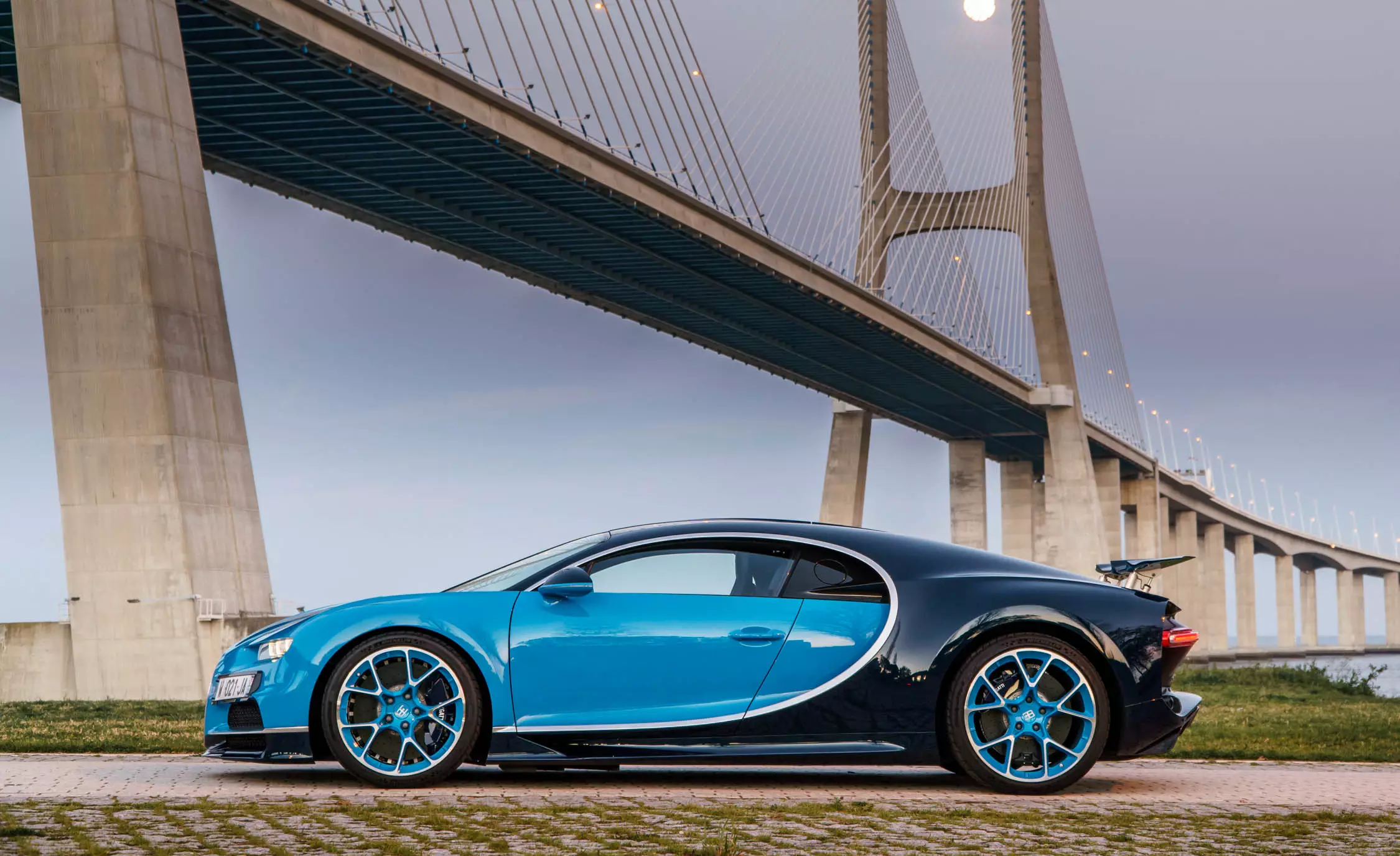
Het nieuwe pincet gebruikt als materiaal een titaniumlegering - Ti6AI4V van zijn naam -, die voornamelijk door de lucht- en ruimtevaartindustrie wordt gebruikt in onderdelen die onderhevig zijn aan enorme stress, en biedt een prestatie die veel beter is dan die van aluminium. De treksterkte is natuurlijk extreem hoog: 1250 N/mm2 , wat neerkomt op een uitgeoefende kracht van iets meer dan 125 kg per vierkante millimeter zonder dat deze titaniumlegering breekt.
De nieuwe remklauw is 41 cm lang, 21 cm breed en 13,6 cm hoog en heeft, naast zijn superieure sterkte, het grote voordeel dat het gewicht aanzienlijk wordt verminderd, waardoor de altijd belangrijke onafgeveerde massa's worden aangetast. Weegt slechts 2,9 kg tegen 4,9 kg van hetzelfde aluminium onderdeel, wat neerkomt op een vermindering van 40%.
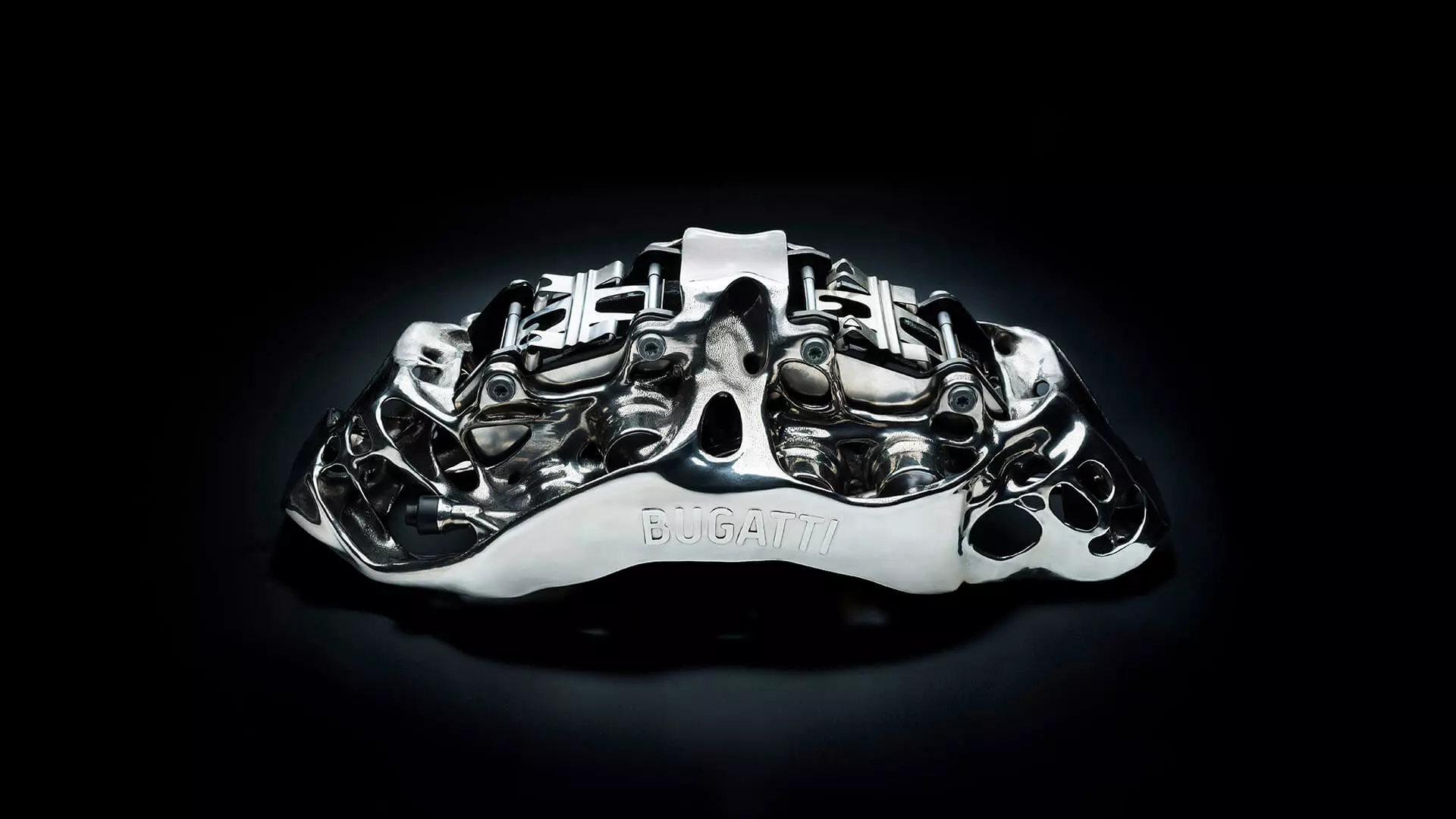
additieve fabricage
Deze nieuwe titanium remklauwen zijn het resultaat van een samenwerking tussen de Bugatti Development Department en Laser Zentrum Nord. Voor het eerst werd titanium gebruikt in plaats van aluminium om voertuigcomponenten te printen, wat de nodige uitdagingen met zich meebracht. De hoge sterkte van titanium is de belangrijkste reden geweest waarom dit materiaal niet is gebruikt, waardoor de toevlucht tot een krachtige printer is genoodzaakt.Deze speciale 3D-printer, gelegen op het Laser Zentrum Nord, dat aan het begin van het project de grootste ter wereld was die titanium kon verwerken, is uitgerust met vier 400W-lasers.
Elke pincet heeft 45 uur nodig om af te drukken.
Tijdens dit proces wordt titaniumpoeder laag voor laag afgezet, waarbij de vier lasers het poeder in de vooraf bepaalde vorm smelten. Het materiaal koelt vrijwel direct af en de klem begint vorm te krijgen.
In totaal zijn er ongeveer 2213 lagen nodig totdat het stuk compleet is.
Nadat de laatste laag is aangebracht, wordt het overtollige materiaal uit de drukkamer verwijderd, gereinigd en geconserveerd voor hergebruik. De remklauw, die al compleet is, blijft in de kamer, ondersteund door een steun, waardoor deze zijn vorm behoudt. Ondersteuning die wordt verwijderd nadat het onderdeel een warmtebehandeling heeft ondergaan (tot 700 ºC) om het te stabiliseren en de gewenste weerstand te garanderen.
Het oppervlak wordt afgewerkt door een combinatie van mechanische, fysische en chemische processen, die ook bijdragen aan het verbeteren van de vermoeiingssterkte. Het duurt meer dan 11 uur om de contouren van functionele oppervlakken, zoals zuigercontacten, te optimaliseren met behulp van een vijfassig bewerkingscentrum.
Bugatti, groepsleider in 3D-printen
Hiermee neemt Bugatti het voortouw in de Volkswagen Groep, niet alleen op het gebied van 3D-printtechnologie, maar ook op het gebied van hightech toepassingen. Een soort miljonairslaboratorium en zeer, zeer krachtig...
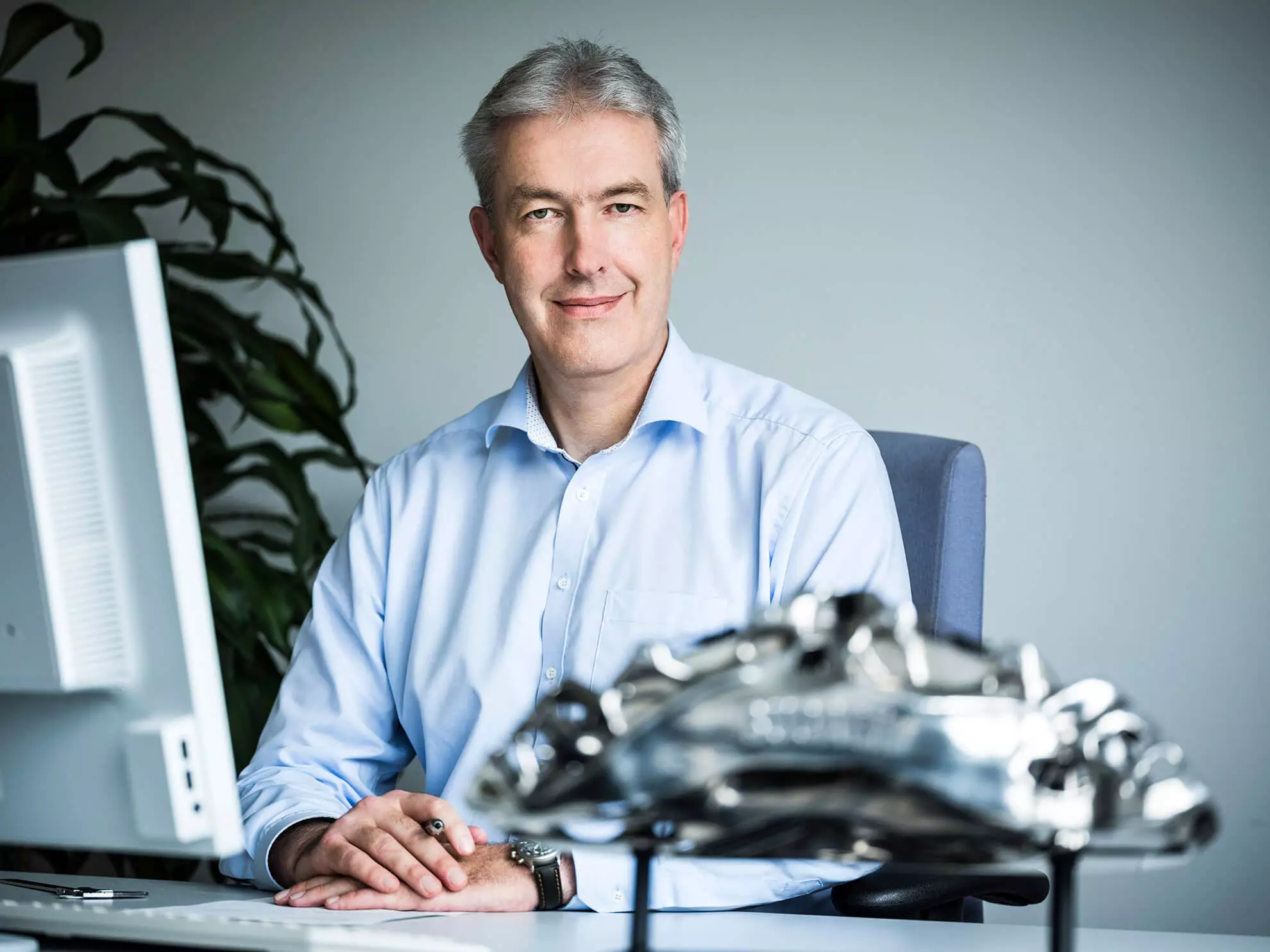
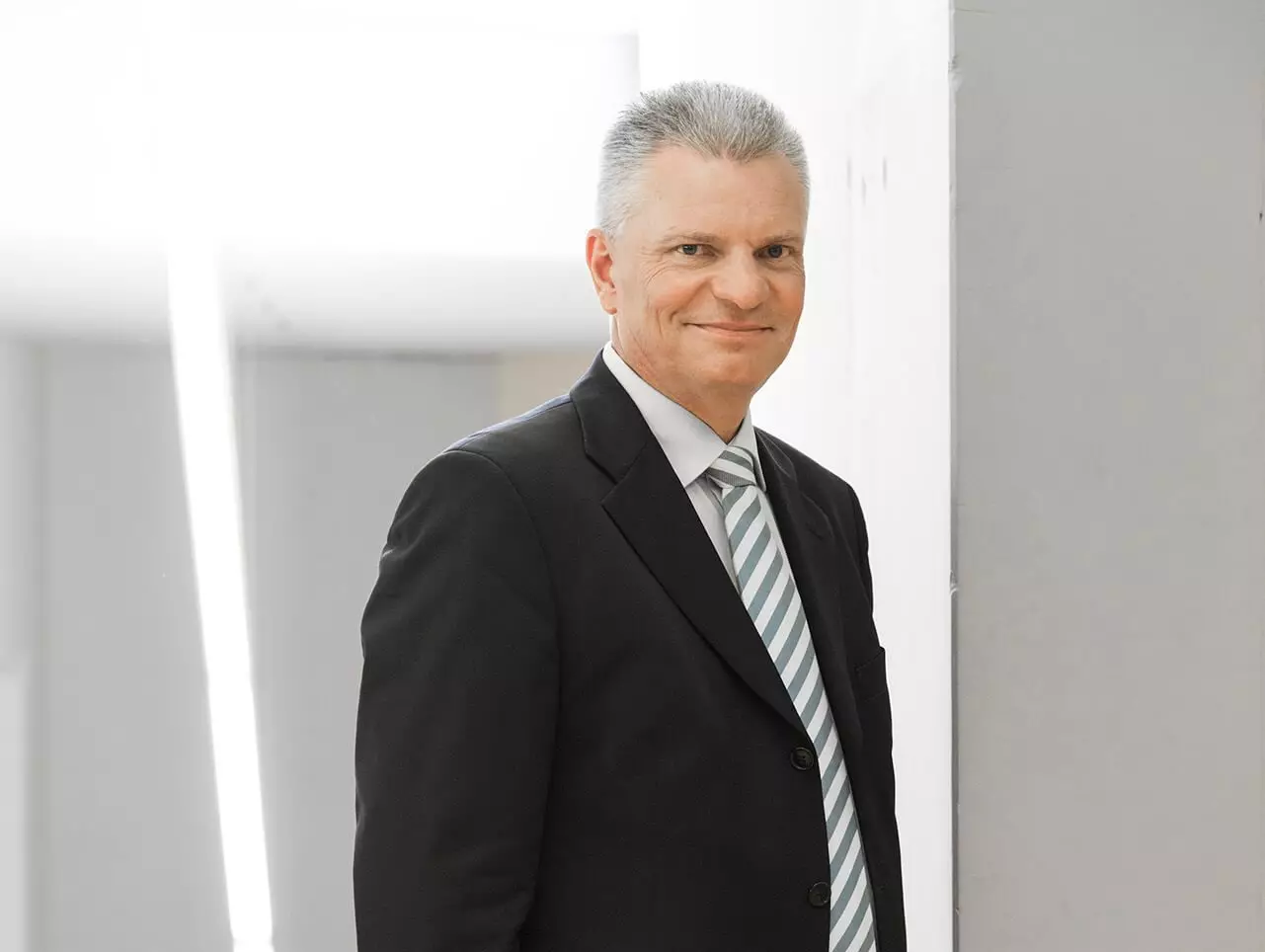