TEN bugatti chiron to maszyna superlatyw — mimo że została niejako zraniona na jej cześć przez rywala szwedzkiego pochodzenia… — i właśnie zyskała kolejny superlatyw wagi, dodając nowe tytanowe zaciski hamulcowe, które w tym modelu powinny być wprowadzone później w roku.
Jak wiesz, Bugatti Chiron był już „właścicielem” największych zacisków hamulcowych w branży motoryzacyjnej. Zaciski te zostały wykute z bloku ze stopu aluminium o wysokiej wytrzymałości z ośmioma tytanowymi tłokami z przodu i sześcioma z tyłu. Dotychczas…
mocniejszy i lżejszy
Bugatti zrobiło kolejny krok naprzód, opracowując tytanowe zaciski hamulcowe – wciąż największe w branży – które są teraz nie tylko największy funkcjonalny składnik tytanu wytwarzany w druku 3D, ponieważ jest to pierwszy zacisk hamulcowy wyprodukowany tą metodą.
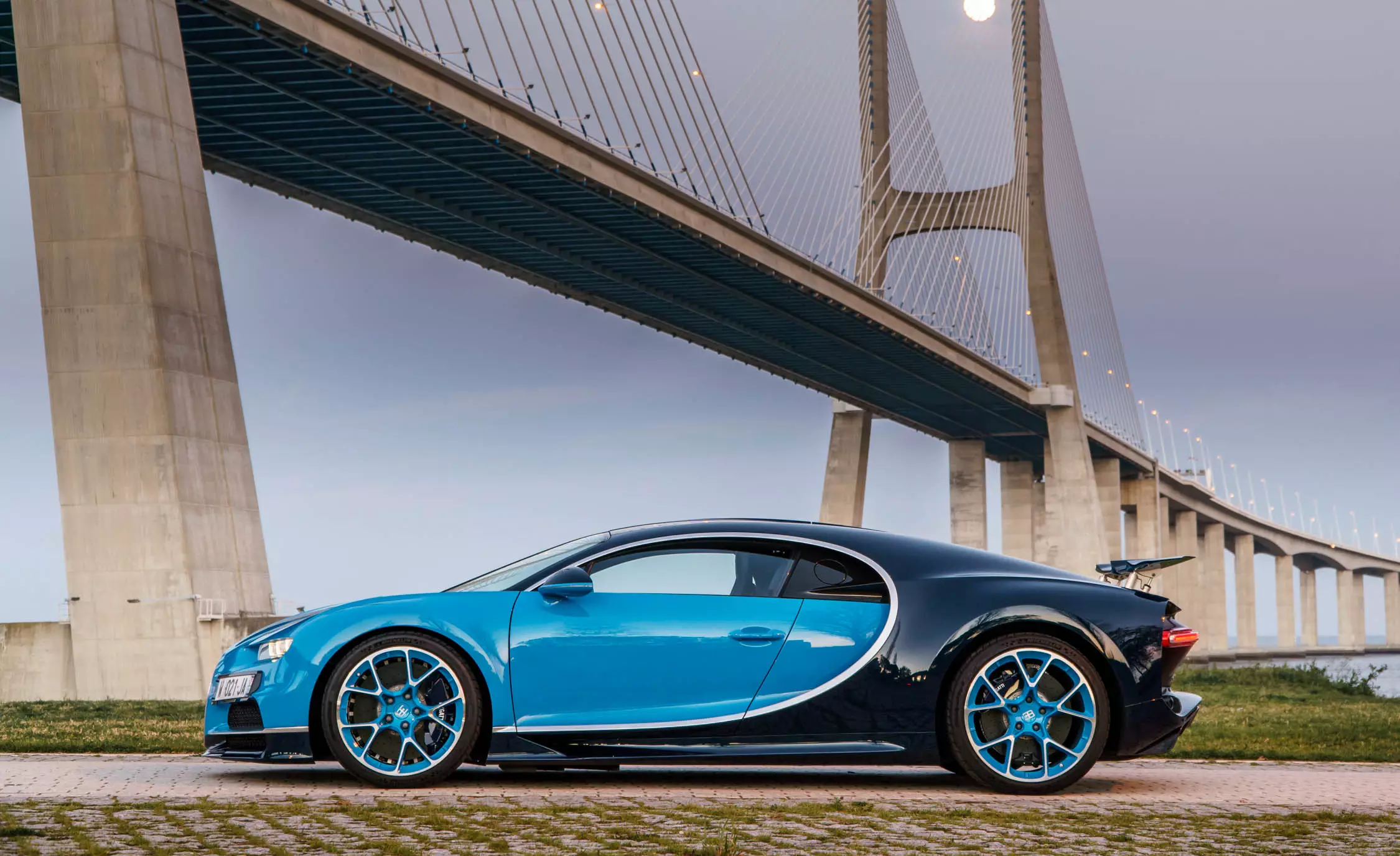
Nowe pęsety wykorzystują jako materiał stop tytanu — Ti6AI4V od jego nazwy — używany głównie przez przemysł lotniczy w komponentach poddawanych ogromnym obciążeniom, oferując znacznie lepsze parametry niż aluminium. Wytrzymałość na rozciąganie jest oczywiście niezwykle wysoka: 1250 N/mm2 , co oznacza przyłożoną siłę nieco ponad 125 kg na milimetr kwadratowy bez pękania stopu tytanu.
Nowy zacisk hamulcowy ma 41 cm długości, 21 cm szerokości i 13,6 cm wysokości, a oprócz doskonałej wytrzymałości ma tę wielką zaletę, że znacznie zmniejsza wagę, co ma wpływ na zawsze ważne masy nieresorowane. Waży tylko 2,9 kg w stosunku do 4,9 kg tej samej części aluminiowej, co odpowiada 40% redukcji.
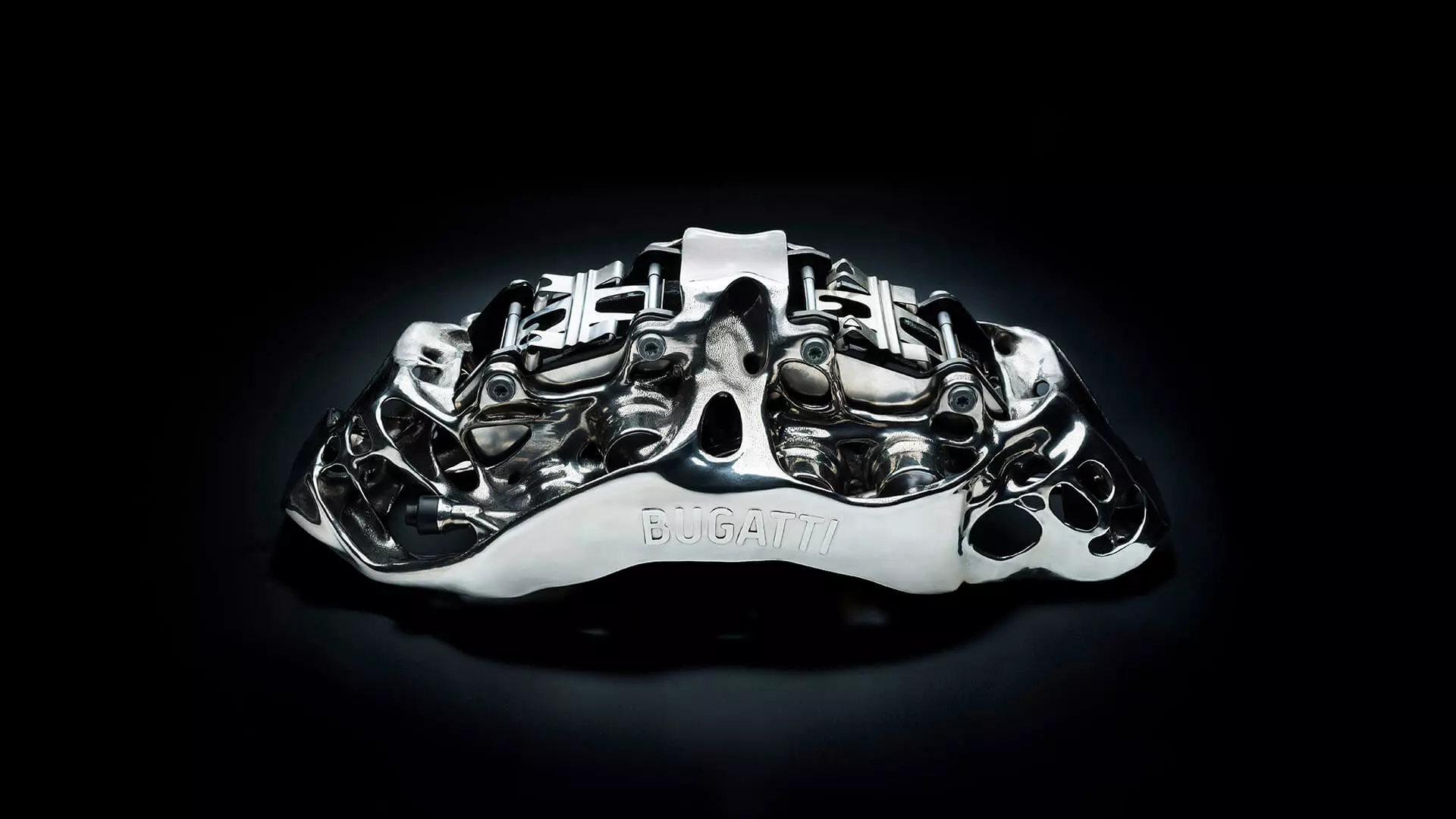
produkcja dodatkowa
Te nowe tytanowe zaciski hamulcowe są wynikiem współpracy pomiędzy Działem Rozwoju Bugatti i Laser Zentrum Nord. Po raz pierwszy do drukowania elementów pojazdów zamiast aluminium zastosowano tytan, co wiązało się z wyzwaniami. Wysoka wytrzymałość tytanu była głównym powodem, dla którego nie zastosowano tego materiału, co wymusiło odwołanie się do wysokowydajnej drukarki.Ta specjalna drukarka 3D, znajdująca się na Laser Zentrum Nord, który na początku projektu był największą na świecie zdolną do obsługi tytanu, jest wyposażona w cztery lasery o mocy 400W.
Wydrukowanie każdej pęsety zajmuje 45 godzin.
Podczas tego procesu proszek tytanowy jest nakładany warstwa po warstwie, a cztery lasery topią proszek w ustalonym kształcie. Materiał stygnie niemal natychmiast, a zacisk zaczyna nabierać kształtu.
W sumie potrzeba około 2213 warstw, aż kawałek będzie gotowy.
Po nałożeniu ostatniej warstwy nadmiar materiału jest usuwany z komory druku, czyszczony i konserwowany do ponownego użycia. Zacisk hamulcowy, już kompletny, pozostaje w komorze podpartej wspornikiem, który pozwala zachować jego kształt. Nośnik, który jest usuwany po obróbce cieplnej elementu (do 700 ºC) w celu jego stabilizacji i zagwarantowania pożądanej odporności.
Powierzchnia wykańczana jest poprzez połączenie procesów mechanicznych, fizycznych i chemicznych, które również przyczyniają się do poprawy jej wytrzymałości zmęczeniowej. Optymalizacja konturów powierzchni funkcjonalnych, takich jak styki tłoków, za pomocą pięcioosiowego centrum obróbczego zajmuje ponad 11 godzin.
Bugatti, lider grupy druku 3D
Dzięki temu Bugatti jest liderem w Grupie Volkswagen nie tylko pod względem technologii druku 3D, ale także pod względem zastosowań high-tech. Coś w rodzaju laboratorium milionera i bardzo, bardzo potężnego...
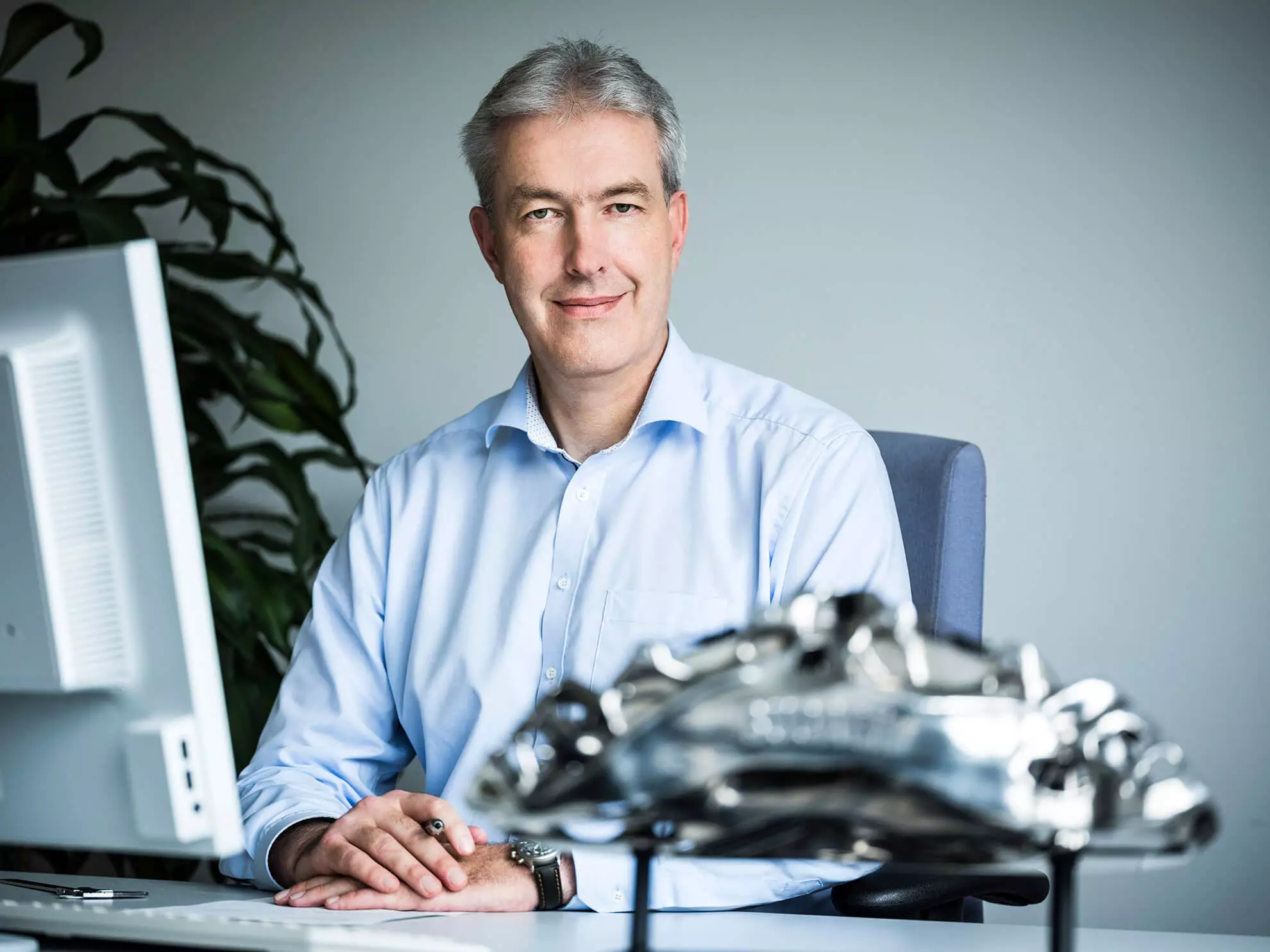
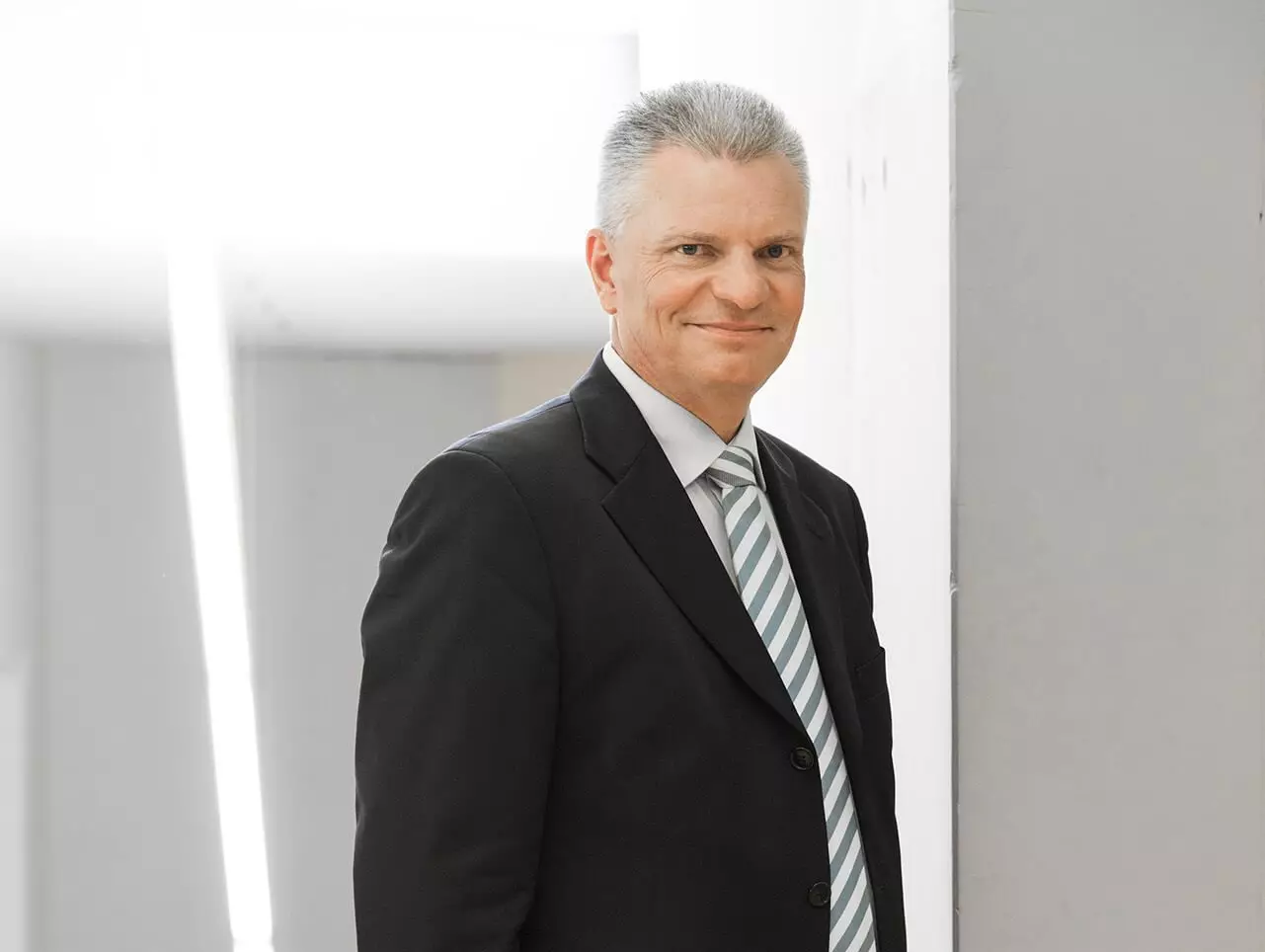